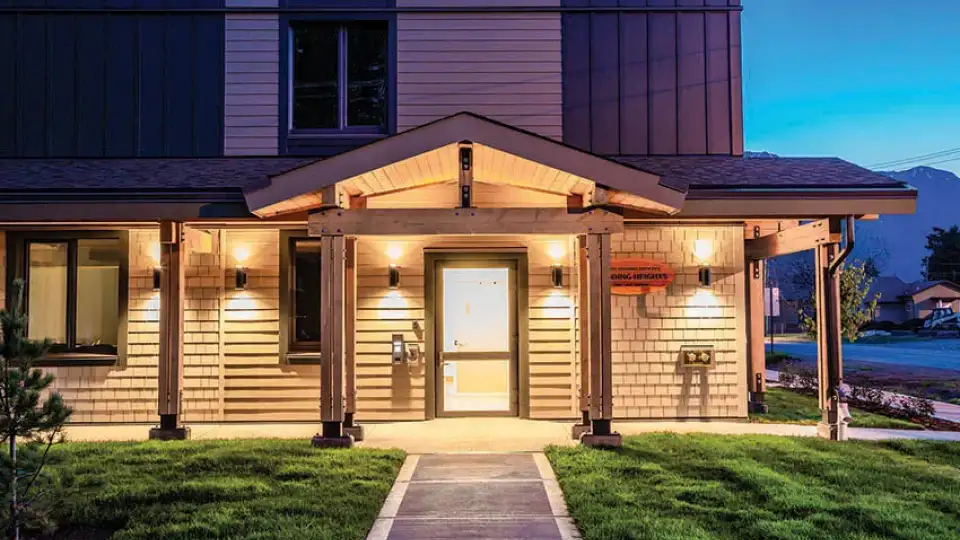
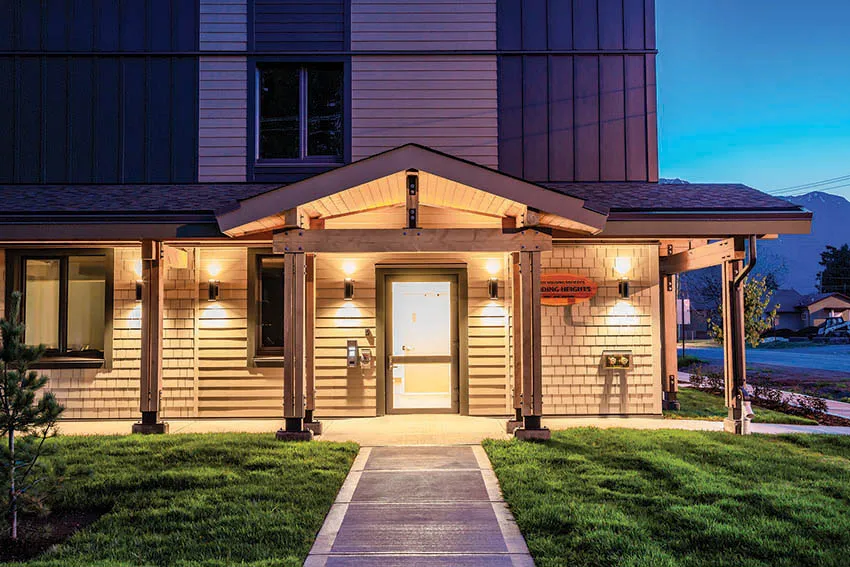
Completed in the summer of 2018, Harding Heights is a 19-unit residential building for seniors and adults with learning difficulties. This three-storey development features a mix of studio and one-bed suites with shared common and program spaces on the ground floor. Harding Heights is BC Housing’s first Certified Passive House development.
The agency is looking to Harding Heights as a model of an efficient, cost-effective Passive House building that can serve as a template for its future residential developments throughout the province.
This project was designed in a contemporary style and with a language that aimed to fit within the town of Smithers’s Alpine theme. The building utilizes a simple and efficient rectangular plan and features dominant roof forms and large overhangs. It is clad with a simple palette of durable cementitious materials that embrace both the visual and the climatic context. Large tilt-and-turn windows are featured on the south elevation to utilize solar gains, while smaller windows were placed on the north, east, and west façades to balance solar-energy gains and losses.
Located in PHPP’s climate zone 2 (cold), the building envelope is highly insulated on all sides. An internally insulated raft slab with 30.5 cm of EPS insulation achieves an R-value of 50. The above-grade wood-framed sandwiched double-wall assembly includes a 2 x 6 batt- insulated exterior structural wall, 15 cm of rigid EPS insulation in the centre, and a 2 x 4 batt-insulated service wall to the interior, together delivering an R-value of 56. The R-86 roof assembly relies on 61 cm of blown cellulose. Cornerstone Architecture specified overinsulation of the triple-glazed window frames and exterior solar shades to control solar gain in the warmer seasons.
Six highly efficient HRVs with up to 93% efficiency are arranged with two units serving each floor, providing 24/7 ventilation with a boost option for the common areas and suites. The air delivery in the suites utilizes a cascade ventilation strategy, supplying fresh air to the living rooms and bedrooms and extracting exhaust air from the washrooms, kitchens, and bathrooms.
Simple maintenance-free user-controlled electrical baseboards provide the in-suite heating. CO2-based heat pumps provide the primary source of hot water with traditional electrical tanks as backup.
The design team and the client required the general contractor to participate in the Passive House Trades Training program to ensure familiarity with the Passive House standard and understand the methodologies behind the wall and envelope construction and the window install strategy.
At the commissioning stage, an airtightness test of 0.44 ACH50 was achieved, approximately 30% better than the air infiltration rate permitted by the Passive House standard. The building will be highly monitored over at least its first two years of operation to assess its energy use and indoor air quality. The building’s latest monitoring data indicate a projected yearly average total energy use intensity of 50 kWh/m2/yr. The project received its Passive House certification in November 2018.