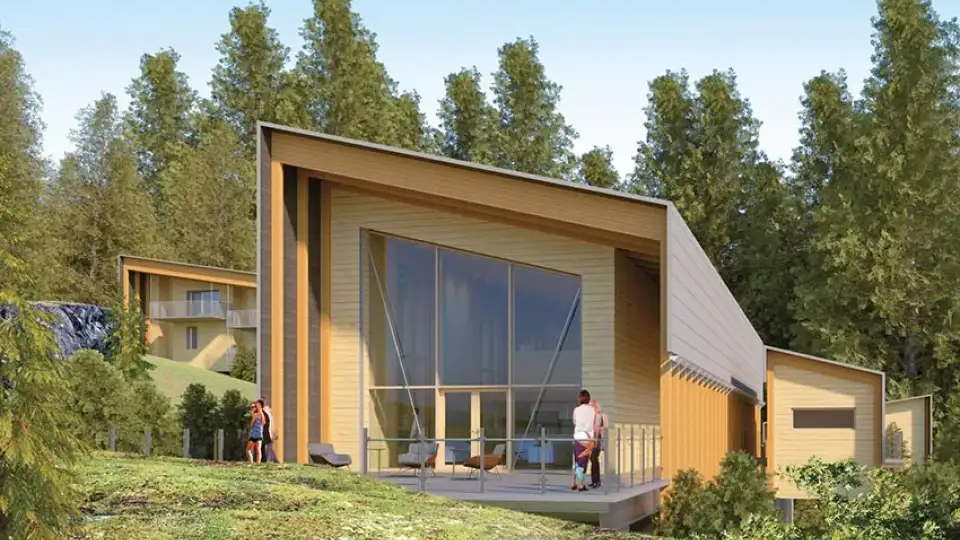
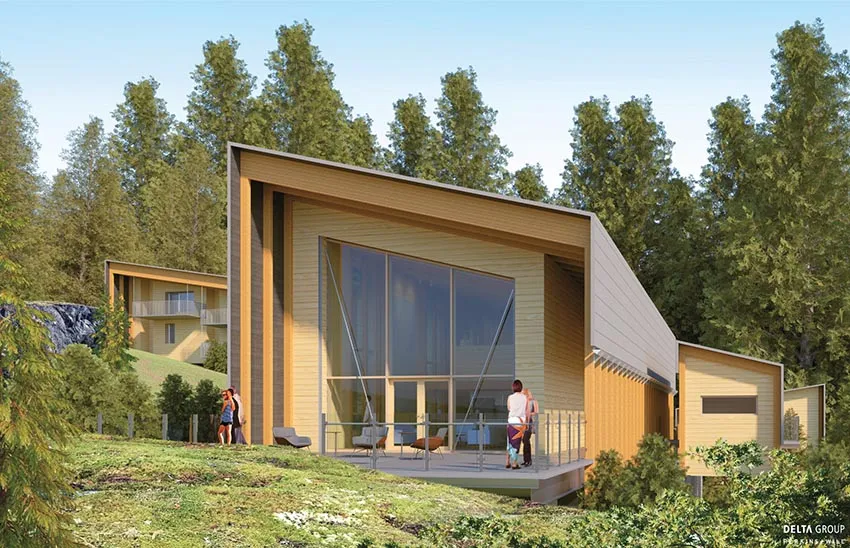
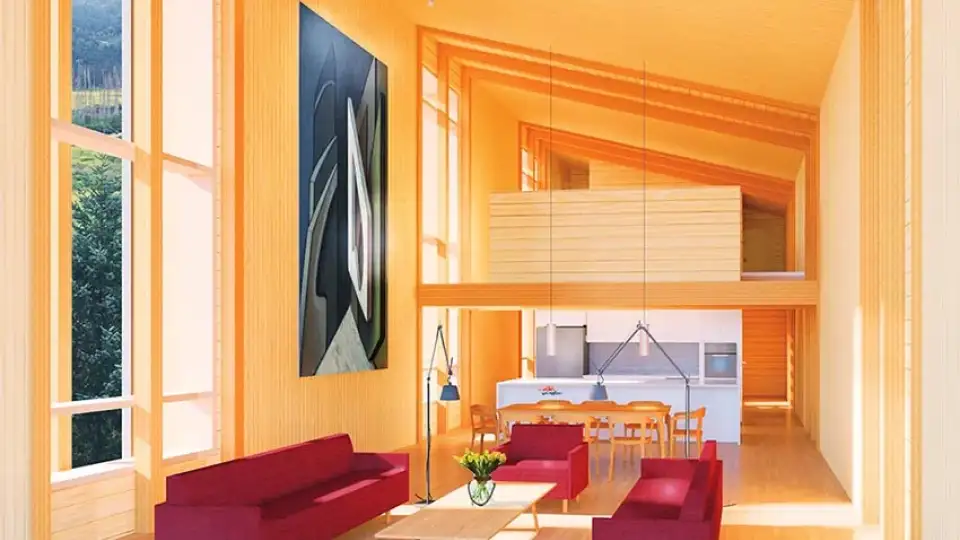
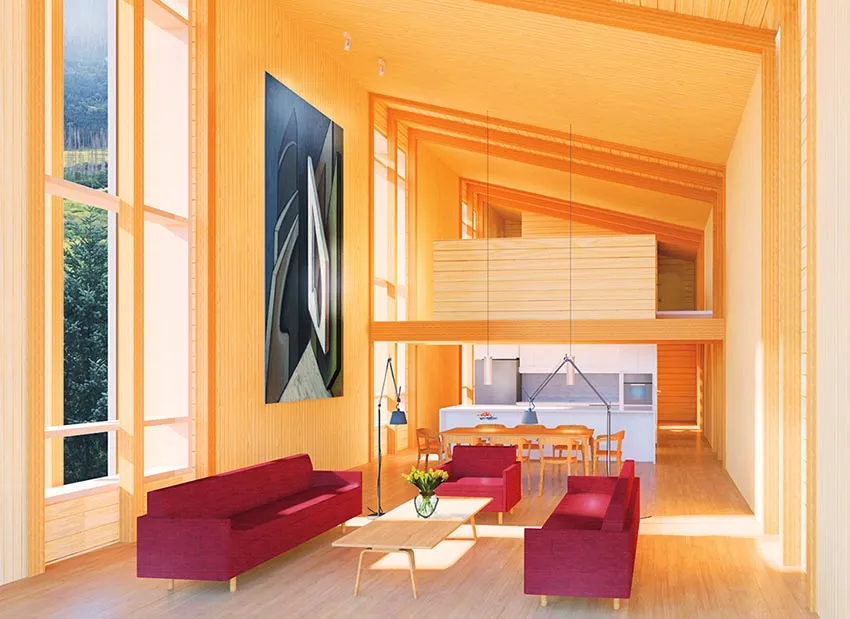
Soo Valley, British Columbia
The Soo Valley Prefabricated Housing project began with a vision to accelerate the availability of low-carbon housing and was intended for a remote site within the traditional territories of the Lil’wat and Squamish Nations, yet not far from the ski resort of Whistler.
The project’s brief was to create an off-grid custom prefabricated house that could then be spun off as a prototype for a smaller townhouse design for use as workforce and ski resort housing.
For this location’s high mountain climate, where temperatures can drop to –25°C , pursuing Passive House helps to achieve the goal of energy self-sufficiency for this house. The project will offer exceptional comfort, resilience, and integration within the local ecological systems—all highly desirable attributes of a prototype for a much larger community.
The site for the prototype house proved challenging due to its prime views to the northeast, setting up a battle between views and warmth. Overhangs are being used to block the sun on the south side, while deep reveals or fins are used to block solar gain through the east- and west-facing glazing.
Opting for constructing with prefabricated components offers obvious benefits for a house in this snowy climate, allowing manufacturing during winter. In addition, prefabrication dramatically reduces construction waste and site disturbance.
For this project, there were a few challenges that affected the specifications. This house is being designed for intermittent occupancy, so there will be fewer internal loads than would be the case in a fully occupied residence, necessitating a thicker building envelope. An added challenge was meeting the project’s desired aesthetic of exposed glulam beams and wood structure. Optimal collaboration was required between all teams to properly conceal the electrical wiring within the wood structure.
The prototype was designed with a suspended floor over a crawl space to minimize disturbance of the ground. While yielding aesthetic and environmental benefits, this approach can also result in colder floors, which here are mitigated by a low-mass radiant floor that is geothermally fed. The low-mass radiant floor is faster to react than concrete, and thus suited to houses with intermittent occupancy.
Geo-exchange heat pumps will be supplying the hot water, thus avoiding the overproduction of hot water in the summer. By taking advantage of moderate ambient ground temperatures of 10°C , the geo-exchange loop also provides preheating and precooling of the high-efficiency ERVs.
The PV panels are inclined at a steep angle to shed snow. Additional renewable energy is provided by a wind turbine. Backup is provided through battery storage and hydrogen fuel cells. The fuel cells were chosen to meet responsiveness needs when large groups arrive for a visit. With the completion of this pilot project, Integral Group will be instrumental in pushing for increased scale in the production of Passive House residential construction.
Service Provider(s)
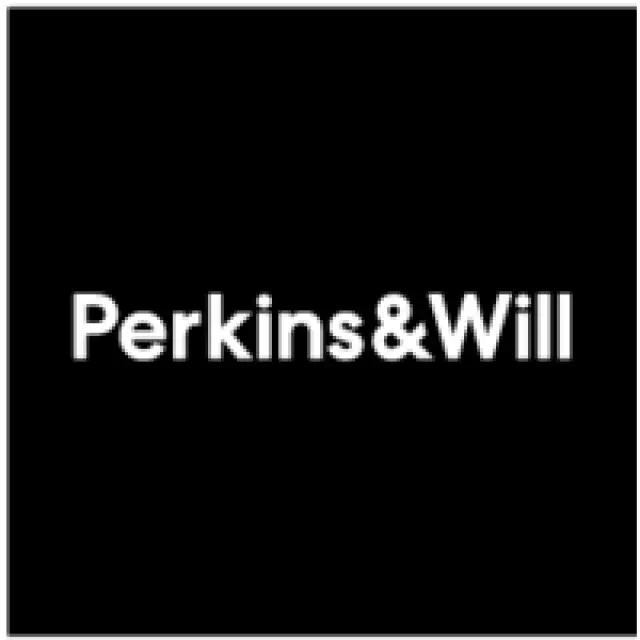
Perkins&Will
Service, Services: Architect
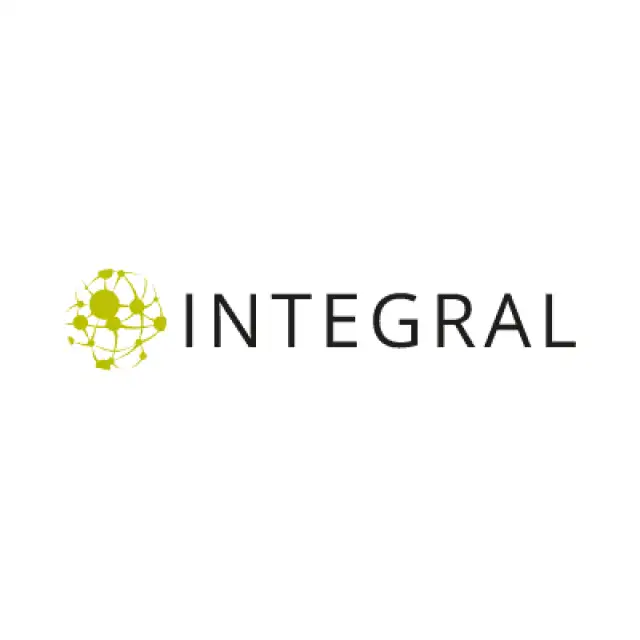
Integral Group
Service, Services: Consulting, Services: Engineering, Services: Architect
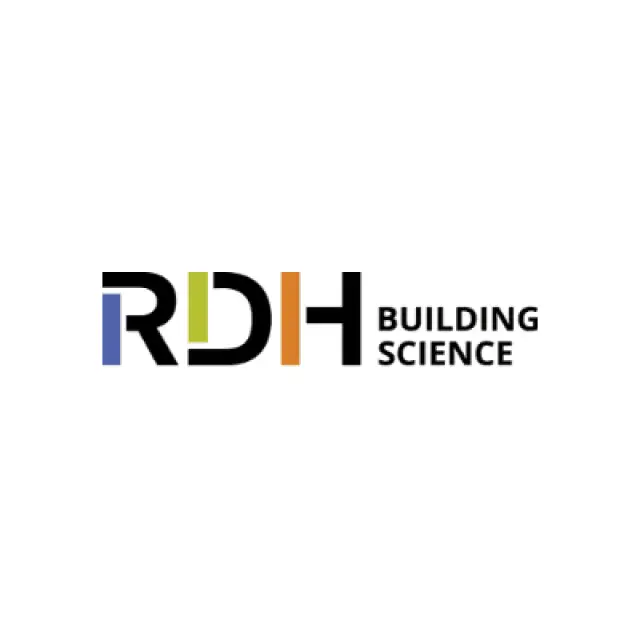
RDH Building Science
Service, Services: Consulting, Phius
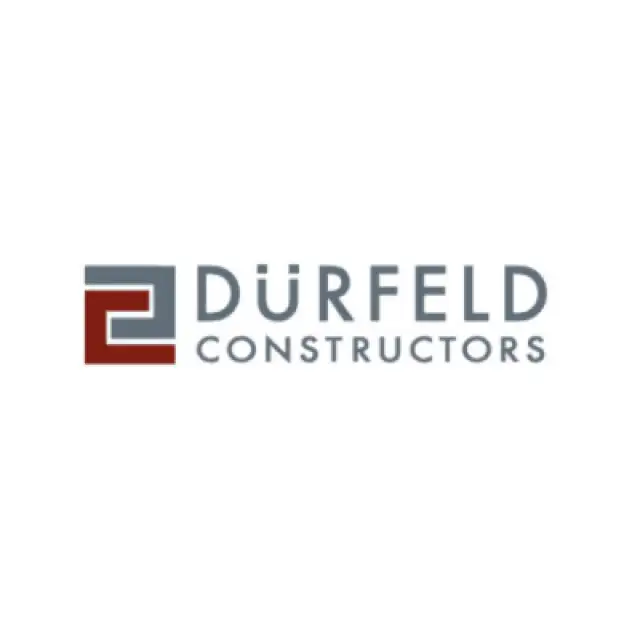
Durfeld Constructors
Service, Services: Contracting
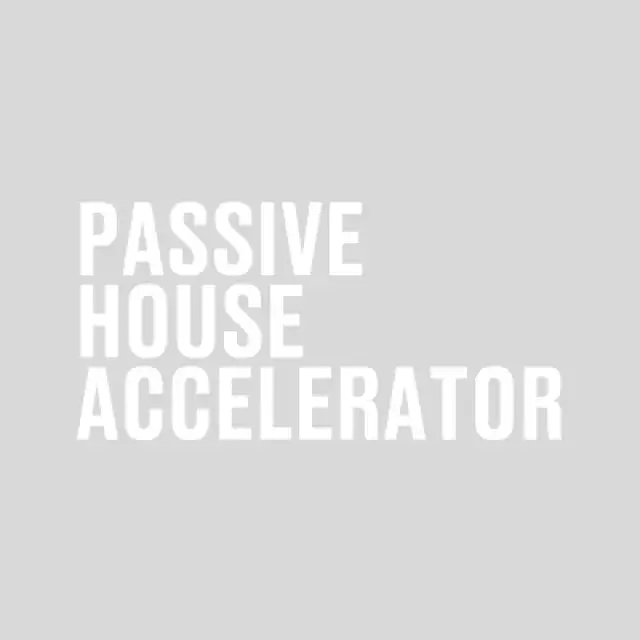
Delta Land Development
Service, Services: Developer