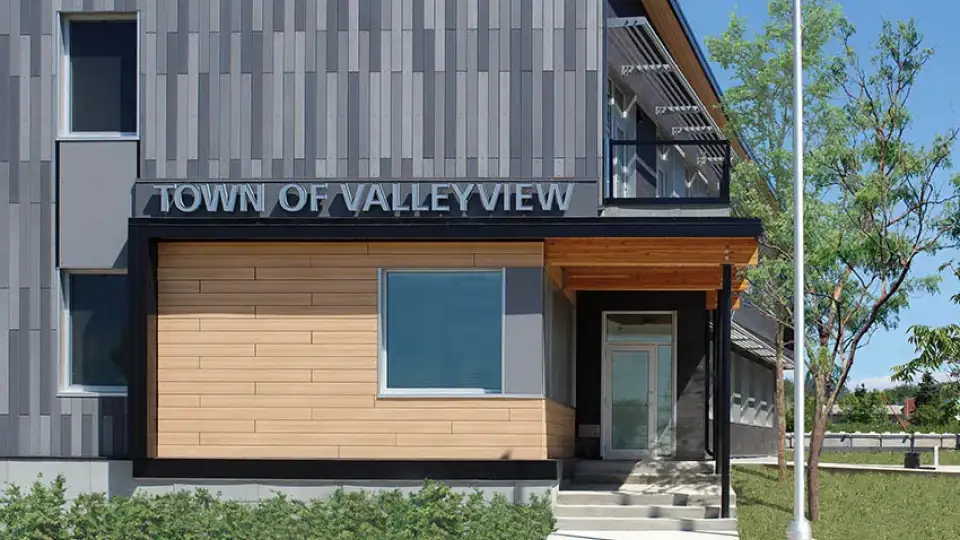
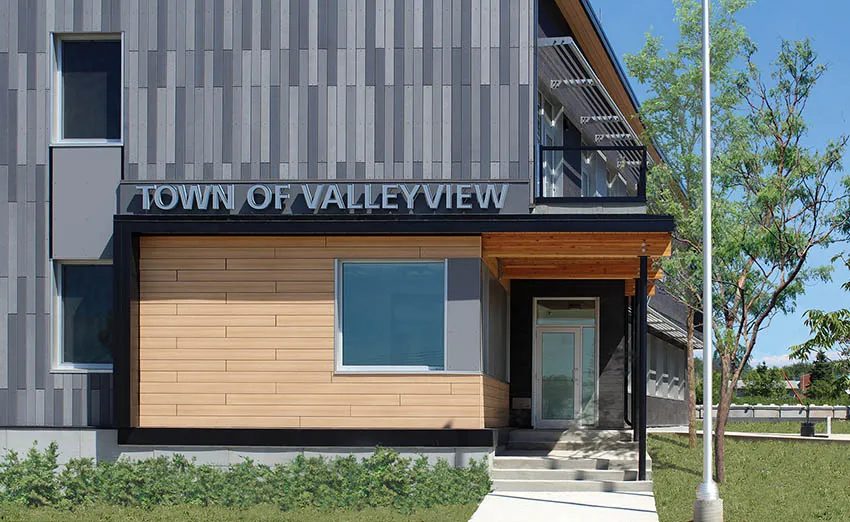
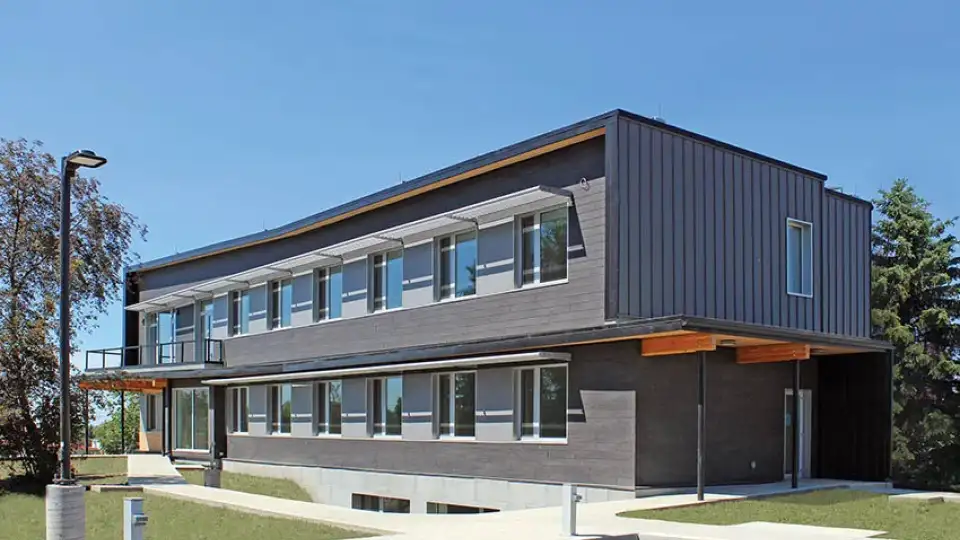
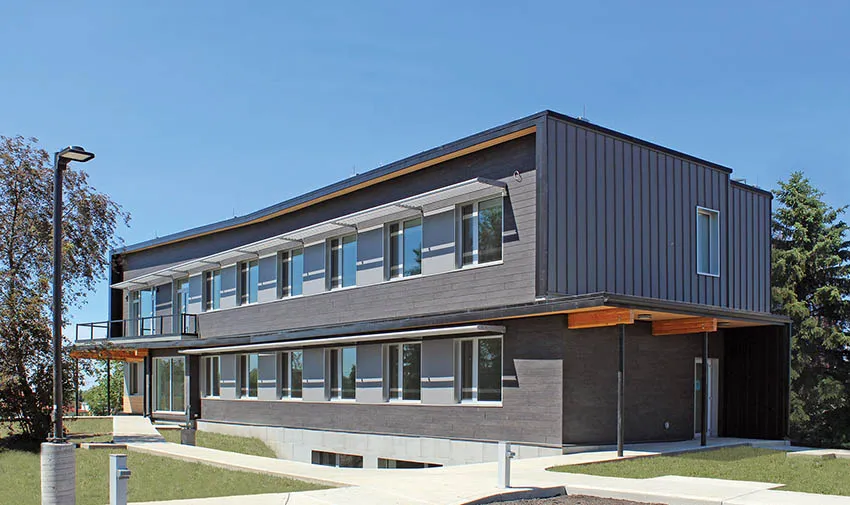
Metrics
Heating demand |
Cooling and dehumidification demand |
Primary Energy Renewable (PER) |
Air leakage |
12.9 kWh/m²a |
0.1 kWh/m²a |
46.8 kWh/m²a |
0.42 ACH₅₀ |
Valleyview, Alberta
Completed in the summer of 2018, Alberta’s Valleyview Town Hall is the result of extensive collaboration among the municipality, the contractor, and a skilled team of designers and consultants, including Scott Builders and Flechas Architecture. These parties worked together to achieve Passive House Plus certification for a commercial building in a northern climate—a first in many respects.
The town of Valleyview experiences long, cold winters and short, mild summers, with temperatures ranging from –20°C to 22°C. When the original town hall was approaching the end of its life, running it became too expensive in these harsh environmental conditions. After considering all options, the town council decided to build a new structure that would bring down operation and maintenance costs and reduce greenhouse gas (GHG) emissions.
Marty Paradine, Valleyview’s town manager during the procurement process, had participated in the development of the city of Fort St. John’s Passive House, an award-winning demonstration project in northern British Columbia. Learning from that experience, the council opted to have the new town hall meet the Passive House standard.
The Valleyview Town Hall design emphasizes flexibility, functionality, accessibility, comfort, and sustainability. The main entrance offers a welcoming presence, framed by a human-scaled canopy with a raised roofline. The main exterior finish of the building is high-pressure compact laminate siding on the visible south and east elevations and prefinished metal siding on the north elevation.
With the main entrance located on the west side of the lot, the rectangular massing extends eastward and exposes the long side of the building to the south, where all high-traffic working areas are located, maximizing the benefits of natural light in the workplace and providing views of the green area south of the building.
This orientation and simple layout optimize sun exposure in the winter but can create challenges in the warmest days of summer. Having specified Passive House-certified windows with a G-value of 0.57 to control heat loss, the design team—which also included Kobayashi + Zedda Architects Ltd., ReNu Building Science, and Williams Engineering—specified Passive House-certified windows and 91.4-cm fixed solar shades to control summertime heat gains.
The structure is encased in a 235-mm full-perimeter blanket of insulation and 140 mm of insulation within the cavity walls for a total R-value of 58. The ventilation system includes a mix of outdoor variable refrigerant flow systems for cooling and heating and a high-efficiency ERV.
This high-performance structure and high-efficiency mechanical equipment allowed for 28 kW of solar panels to meet the building’s total energy needs. The system is expected to generate almost 27,000 kWh per year, maximizing operational savings and reducing GHG emissions by 17 tonnes per year.