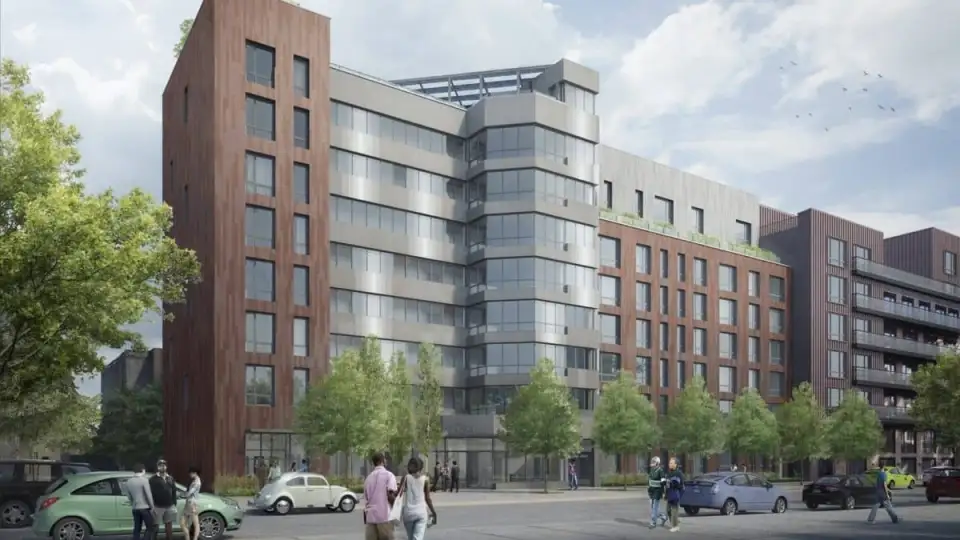
Magnusson Architecture and Planning (MAP) operates at the nexus of affordability and sustainability. For over three decades we’ve worked with nonprofit organizations, municipalities, and for-profit developers to design housing and neighborhood revitalization projects with a focus on affordable, supportive, senior, and workforce housing. The affordable- housing industry has, in many respects, led the way on sustainable residential development in the New York area for years, and now on Passive House adoption, too. This is due in large part to local and state funding agencies that have adopted sustainability standards as a requirement for public subsidies. Operational costs are key, too; as affordable developers are more likely to own properties for an extended period of time, they often consider investing a little bit more in strategies to make them more durable and efficient. We at MAP are very aligned with these efforts.
While we are always addressing a host of factors in our work—unique building typologies, new regulatory requirements, cost considerations for publicly subsidized developments—making progress toward a carbon-neutral architecture has consistently been a high priority for our firm. To gain insights into exactly how we are doing, we recently charted our new construction projects over the past ten years. During that time we have dealt with a wide variety of potential certifications and standards, including LEED, PHI, PHIUS, Enterprise Green Communities, Energy Star, and NYSERDA. This mix of standards complicates the comparison process. In order to provide a comparable metric of our projects’ operational energy performance, we decided to focus on energy use intensity (EUI) and corresponding conversions to kgCO2/sf (see Figure 1).
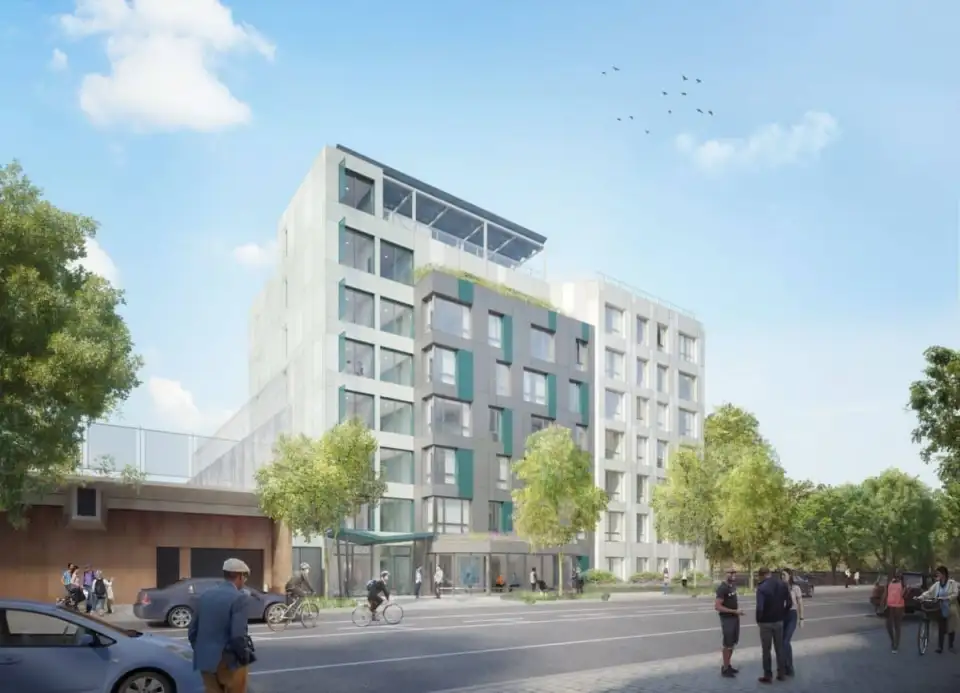
The yellow line is the mean energy use of our projects, and the solid top line is baseline code for a typical multifamily building in NYC. We show the modeled energy performance of buildings as source EUI, instead of showing it as X% better than this or that code, which is how it is typically shown in sustainability certifications. We have tracked source energy without renewable-energy generation, so we can understand exactly how the rest of the building systems are performing. And, because our New York State grid is expected to vastly improve, we have included the data as site EUI for two of our recent projects, Rheingold and DeKalb. Rheingold Senior Housing is a 94-unit affordable senior housing development, and DeKalb Commons is an 82-unit affordable multifamily project.
These calculations were provided by Bright Power, using a database of baseline models. One can see the implications of the stretch code as well, and just how fast things are moving. Until our codes can provide the structure and regulations necessary to implement a successful low- energy building (built almost certainly with Passive House principles), we will need to rely on certifications such as Passive House to reach low EUIs. Fortunately, our NYC energy code is expected to become performance based by 2025 per local law 32, which will allow for clarity, flexibility, and a focus on the end goal.
Making this chart revealed several important points:
While accreditation systems are quite useful, they don’t help us compare energy performance across projects. Even comparing within the same system can present challenges when standards change over the years.
When calculating EUI per square foot (SF), what you count as “SF” matters. (For example, PHI uses treated floor area instead of gross square feet as we have done here.)
The density of a building matters. For example, a building with lots of studios will have more refrigerators and stoves per square foot than one with more three-bedroom units. In part because of this, we are also planning to convert this source EUI chart in the near future into energy use intensity per person housed (which is how PHIUS sets its energy use criteria).
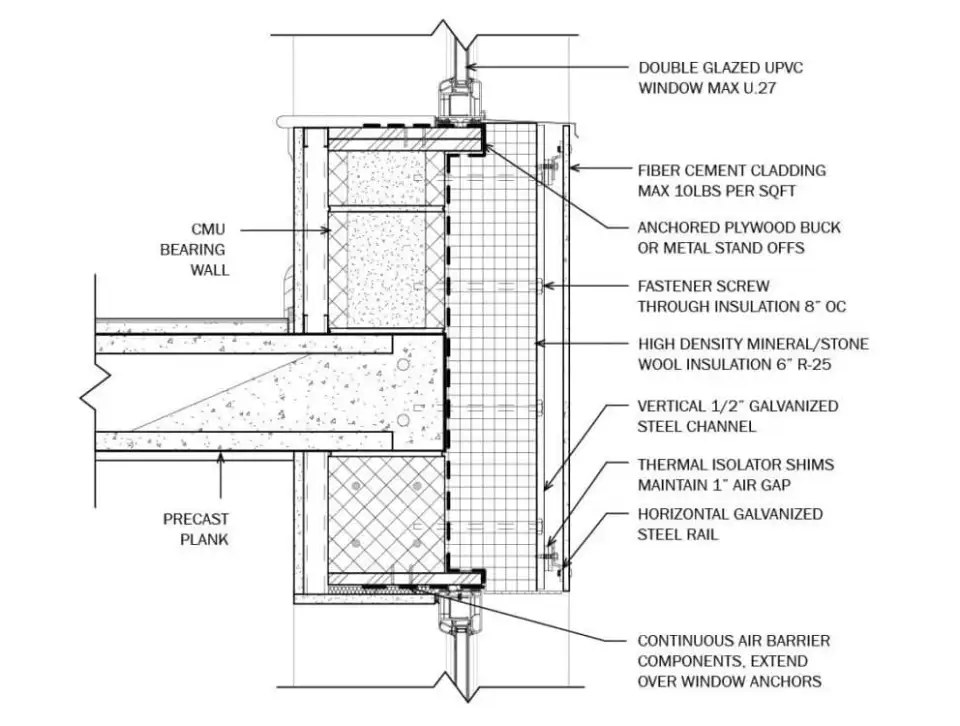
The last point is critical and highlights an important lesson learned from Rheingold and DeKalb: Both are designed to PHIUS 2015 standards, but only DeKalb will be able to certify. (The PHIUS certification is often used by this multifamily affordable typology in our region, because typically double-pane windows will meet the energy, comfort, and hygrothermal criteria, whereas PHI in our climate often requires triple-pane.)
The discrepancy arises from the studio apartment density of senior housing, which translates to high miscellaneous electric loads per building occupant. While all other PHIUS energy metrics have been met, Rheingold’s source energy per person exceeds PHIUS thresholds. To meet this requirement, the building would have needed appliances and systems with efficiencies beyond what is commercially available and/or a PV system covering far more roof area than what is physically available or allowed per zoning. Short of these interventions, a cleaner electric grid would have single-handedly brought the metrics within range of certification. While New York State has proactive goals to do just that, as it stands, and despite all the other benchmarks it hits, Rheingold cannot be certified through PHIUS.
Nonetheless, the project team decided to move forward with a building fully optimized to Passive-House-level performance, facilitated by energy modeling in WUFI Passive, complete with a superinsulated envelope with thermal-bridge-free detailing, airtight specification and details, Passive-House-level efficient mechanical systems and appliances, and a balanced ERV system supplying the ventilation. Rheingold was selected as a NYSERDA Buildings of Excellence Award winner, a competition that recognizes the design, construction, and operation of very low or zero carbon-emitting multifamily buildings. With construction oversight and quality control measures in place as if the project were seeking certification, it will perform like a Passive House with a site EUI of 28.03 and source EUI of 60.4 kBtu per square foot per year (/ft2/yr) (exclusive of renewable generation). It is expected to be ready for occupancy in fall 2022.
This is very much in line with our DeKalb Commons development, a multisite project at which energy savings is expected to be roughly 30% to 40% compared to NYC ECC2016 code-built buildings. It has a site EUI of 18.3 and a source EUI of 52.7 kBtu/ft2/yr (exclusive of renewable generation), and is expected to be completed by spring 2023. The design for the two structures maximized the area feasible to provide solar, and they will feature 40-kW and 50-kW systems on the north and south buildings respectively. No fossil fuels will be used on-site. Instead, these all-electric buildings will have electric stoves and laundry equipment and will incorporate air source heat pump domestic hot water (DHW) production, with roof-mounted condensing units. The systems will include storage tanks in the cellar to help ensure that the heat pumps can meet the DHW demand of the building, while also promoting off-peak DHW production. The insulated storage tanks are located in the cellar to reduce the need for structural reinforcement at the roof in these block-and-plank buildings. The piping between the condensing units and storage tanks will be insulated above code levels to ensure that losses will be negligible.
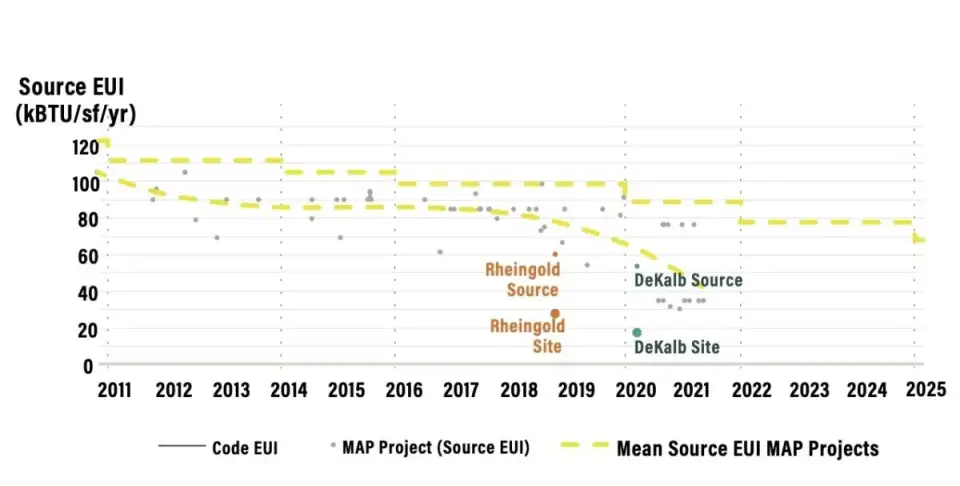
While the efforts of our industry to adopt Passive House technologies—including ERVs and heat pumps—have helped to make them more available in our market, and therefore more affordable, there is still a cost differential associated with constructing a Passive House. At DeKalb, the cost premium is expected to be from 2% to 8%—a premium that translates to energy savings of about $72K annually, shared between residents and ownership.
Many strategies have been employed to simplify construction and limit development costs. The layout of the variable refrigerant flow (VRF) system was optimized to reduce refrigerant runs, which controls that expense. The design also relies on a single cladding system with minimal protrusions into the envelope. The mineral wool insulation is dense enough to support the relatively lightweight cladding with only subframing directly behind the cladding and screws alone penetrating the insulation. This approach saves significant material and expense, compared to the initial option of using thermally broken subframing with a fiber-reinforced polymer girt. Streamlining the façade saved the project an estimated $5 per square foot in material costs alone.
At MAP, when we conduct a construction cost comparison, a baseline of code minimum would not usually be appropriate. When we consider Passive House costs, we compare them against the sustainability options that affordable housing would otherwise pursue. Rheingold is a perfect example. It was originally priced to meet a different, slightly less efficient standard, but we found that the incremental cost to step up to Passive House was less than 1%. The baseline was NYSERDA NCP Tier II with a minimum energy target of 25% above current code (or source EUI of approximately 74 kBtu/ft2/yr), employing ERVs and heat pumps. With this minimal construction cost increase, the project will now perform 44% above code with a source EUI of 60.4 kBtu/ft2/yr and save $47K in energy cost yearly. To get this Passive House cost construction differential, we priced the project with four contractors and gave them a detailed Passive House alternate to bid on.
Achieving a high-performance standard for operational energy is only one piece of the truly sustainable housing puzzle, however. In recent years MAP has also been investigating methods for calculating and reducing embodied carbon in our projects. As has been widely discussed in the last few years, embodied carbon represents a large portion of a project’s short-term impact on the greenhouse gas balance. Considering that we have a limited budget of greenhouse gases to emit in the next ten years, rapid innovation is required. In searching out lower-embodied-energy products, we have found certain ones easily accessible in our region, while others are more difficult to obtain. Environmentally preferable subslab insulation—expanded foam glass—is becoming more readily available here. This product, which is made of 100% recycled glass and comes in a simple-to-install gravel format, can serve as both an insulation and a drainage layer. (The “foam” in its name refers to the process by which it is created, not to be confused with the petroleum products.) However, New York City currently has few concrete/masonry suppliers who carry low-emitting products. We are steadfastly optimistic and excited about further innovations in biogenic materials, modular construction, and circular products. And we look forward to new opportunities to combine them with near net zero operational energy performance!
—Sara A. Bayer is MAP’s associate principal and director of sustainability, and Matt Scheer is MAP’s director of communications.