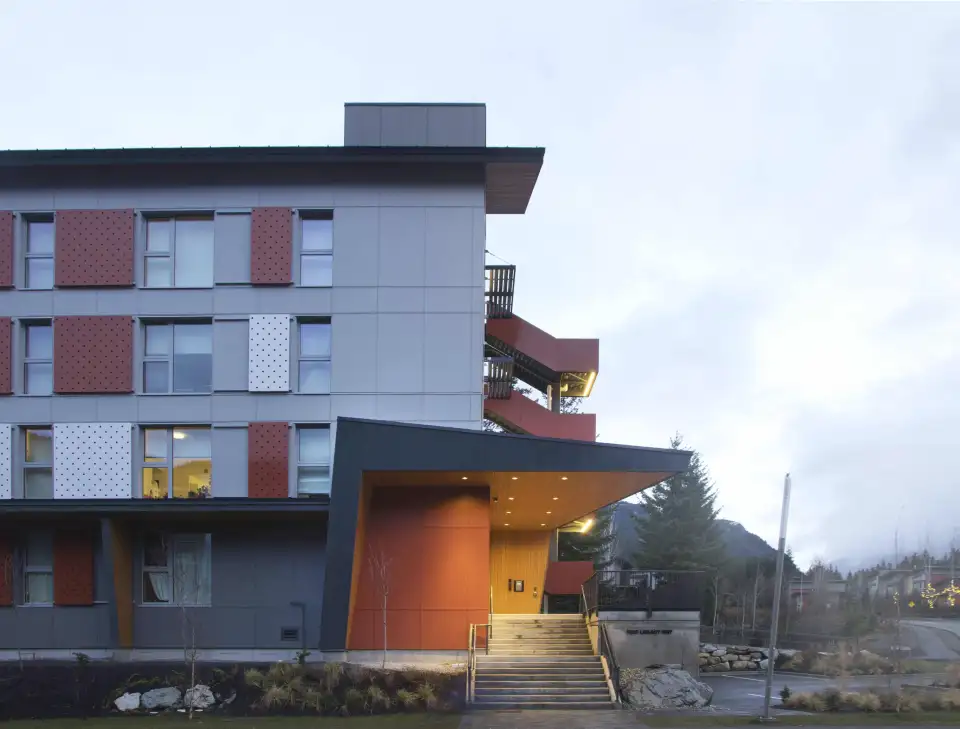
The Whistler resort area in British Columbia has earned a well-deserved reputation as an outstanding ski area, attracting two million visitors each year. Its popularity, though, has led to a housing affordability crisis for the resort’s employees. Last November that crisis eased somewhat with the opening of a four-story apartment building developed by the Whistler Housing Authority (WHA). The 24-unit rental property, which has been certified as meeting the Passive House standard, has a mix of studios and one- and two-bedroom apartments, providing housing for roughly 50 employees. The building includes an underground garage, a shared laundry, an elevator, and in-suite storage for bicycles.
This Passive House project posed many challenges, says Duane Siegrist, principal architect with Integra Architecture, yet it also had one strong advantage. “The clients were our champion in this case,” Siegrist says. In particular, Marla Zucht, WHA’s general manager, ensured that the authority’s commitment to achieving Passive House was unwavering. She helped guide the team selection process, including hiring a construction manager whose expertise and local knowledge contributed heavily to the project’s success.
Prime among the challenges was Whistler’s alpine climate. The area’s many months of snow and rain translate into a compressed build season. Another pitfall was the local shortage of skilled trades. In addition, the design had to be frugal, given WHA’s strict budget, while still providing the 24 units of housing. “We had to find innovative solutions,” Siegrist notes.
Fortunately, one solution—prefabrication—helped WHA to address many of these challenges. The walls, floors, and roof panels were all prefabricated off-site, sharply cutting on-site labor time. The use of these panels allowed for the efficient enclosure of the load-bearing structures despite the temperamental and often harsh climate, thus avoiding potential seasonal delays.
In addition to these efficiency benefits, the panels have environmental advantages as well. They are constructed of low-embodied-energy materials, with cellulose as the main insulator. The approximate effective R-values were R-45 for the walls, R-98 for the roof, and R-71 for the floors. “It went together really well, and the credit goes to the prefabrication,” says Siegrist, adding, "The final airtightness testing was tighter than we expected at 0.15 ACH50, leading to PHPP results of 13 kWh/m2 for the heating demand, and a PER (primary energy renewable) factor of 62 kWh/m2, which are very strong performance numbers."
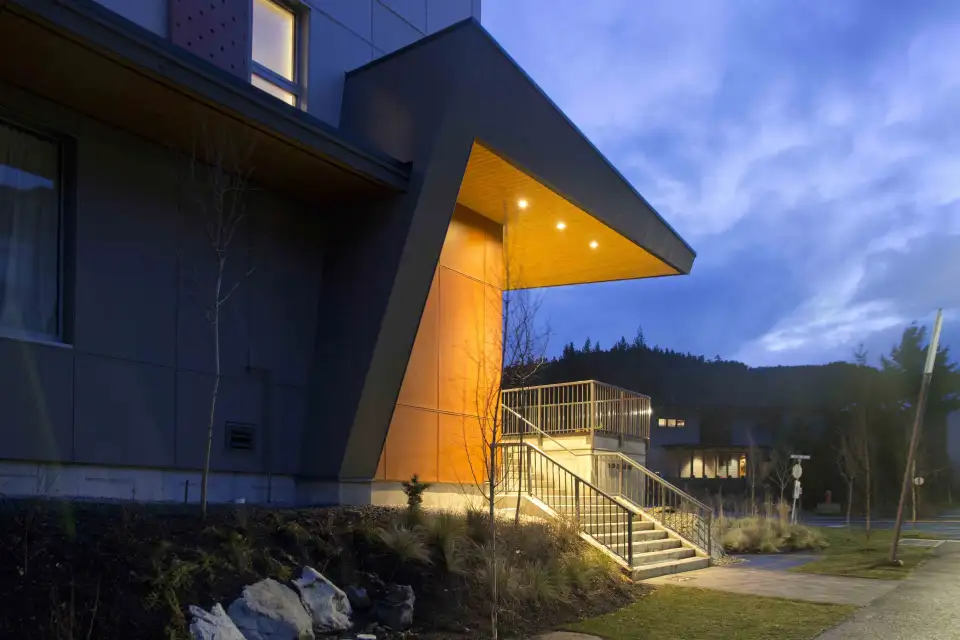
Long before construction began, Siegrist wrestled with designing the building to accommodate the authority’s program goals on a tight site. To make all of the bedroom types for 24 units fit within the allocated floor area, the building’s exit staircase was moved out of the envelope. A dynamic shaped canopy entrance serves as a marker for the public and residents. Placing the exterior stairs so that they overlook the plaza affords ample space to sit, soak up some sun, and socialize. Anticipating the needs of the generally athletic renters who work in the resort area, Siegrist provided space for bike storage in each unit. “We could have provided bike storage below grade in the garage, but for many of these renters their bicycles are their most important assets and their only source of transportation,” says Siegrist, “and losing one would be a huge deal.” The units’ entry doors are sized slightly larger than is typical to allow for easy bike access, and the corridors and elevators were designed with durability in mind.
From a Passive House perspective, the site also posed challenges. Instead of facing south—optimal for maximizing solar exposure in winter and controlling it in summer—the building fits on the site in such a way that three façades get direct solar exposure. Early modeling showed that the building would overheat in summer unless shading was addressed. “We had to specify horizontal sunshades not on the south alone but on all three sides,” Siegrist says. He adds that this kind of detailing is costly and tricky to implement but was absolutely necessary for occupant comfort and for meeting the requirements of the Passive House standard. At first the design team had considered movable screens to shade the windows, but the team eventually opted for a fixed solution that did not require the occupants’ participation or ongoing maintenance by the client, and also avoided potential issues related to ice accumulation.
A centralized ERV and integrated variable refrigerant flow heat pump system supplies constant ventilation, along with post-heating and cooling. Control dampers allow for individualized heating and cooling in each suite. The centralized system provided many advantages, including fitting most of the duct runs in the corridor spaces. Modeling determined that the supplemental space heating load could be met with a cost-effective electric baseboard system.
Although new buildings in Whistler are required to connect requires that new buildings connect to the district energy system for water heating, that system was at odds with the Passive House efficiency requirements. This hurdle was overcome through further study that led to the building’s domestic hot water being provided by an electric boiler.
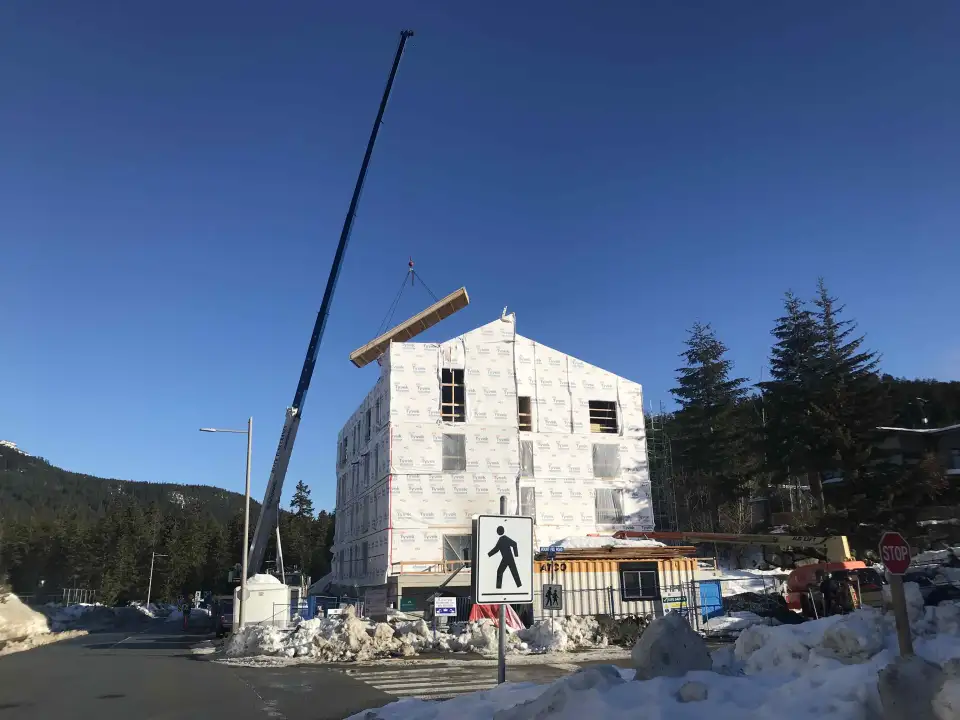
The tenants began moving in last November. All of the feedback that Integra Architecture has received has been very positive. “The clients have been really happy and, I am sure, relieved that the team's plan worked. They were very supportive when it became complex,” says Siegrist. "Working on a building type that is new to the industry requires strong leadership and teamwork and good communication skills to be successful. The clients still say how proud they are of this completed innovative housing project." New housing that is designed specifically for the resort’s typical employee and that delivers Passive House levels of comfort is a huge bonus in a tight housing market.