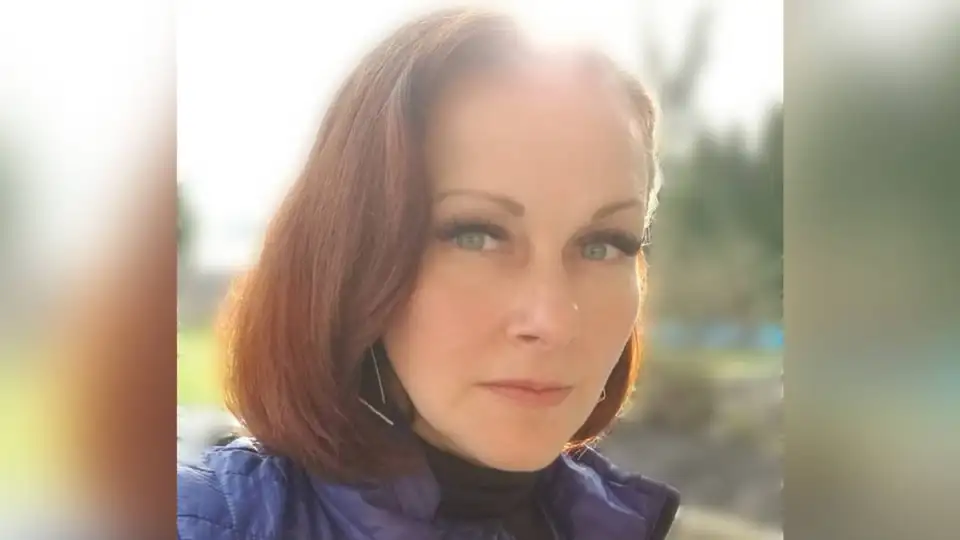
For a decade, Prudence Ferreira has been setting the bar for Passive House building science praxis and education in North America, playing roles as an early board President of Passive House California, managing partner with PassivScience, leader of the PHIUS board, founding member of the PHIUS Technical Committee, PHIUS Certified Trainer (600 Passive House Consultants trained to-date), and now the Passive House lead at building engineering powerhouse Morrison Hershfield responsible for overseeing major PHI- and PHIUS-certified projects in the US and Canada. In this wide-ranging interview, Prudence describes her approach to lean project management, leading from the heart, high rise Passive House experiences, and her effort to organize an open source Passive House details library.
Zack Semke: You have been a leader in the Passive House movement and Passive House practice that I’ve admired since we first met in Innsbruck back in 2011. I know you’ve had a lot of different roles since then. Can you start by describing your new role at Morrison Hershfield and what your work entails?
Prudence: My title is Passive House Practice Lead. Prior to my arriving at Morrison Hershfield the company already had a history of innovating and pushing the envelope—literally—with high-performance buildings. They are excellent building envelope consultants, and work with a lot of complex, large-scale buildings. Because they’re so respected and skilled, they also end up doing a lot of policy work. They were instrumental in helping develop the BC [British Columbia] Step Code. So, although Passive House is a discreet, sort of branded approach to sound building science, Morrison Hershfield is not at all new to the high-performance building world.
As the Passive House Practice Lead, my role is to develop our team’s understanding of the specifics of Passive House, not only the criteria and the approach, but all of the ins and outs of what it takes to get a project from conceptual design all the way through certification. My work consists equally of training my team internally and working with project teams around North America. Morrison Hershfield has 22 offices. About half of them are in Canada and half are in the United States. We span a lot of different climate zones, a lot of different markets and building practices. Developing centralized resources, training modules, process documents…all of that kind of stuff has been a large part of what I’m doing in startup mode.
I’m also helping folks like the City of Vancouver. I’m working on a couple of studies with them—one on Passive House, one on embodied carbon reduction. I’m starting to finally get into the policy work that I’ve been wanting to do for a while. I’m really happy to be here because I feel like it really allows me to expand my impact.
Zack: That’s exciting. You mentioned that you have 19 projects going on earlier?
Prudence: I’m probably juggling about 20 between old Passive science projects and projects that are happening within Morrison Hershfield.
Zack: How are you managing that? Are there any secrets to making that possible?
Prudence: Yes. Wake up at four in the morning. I’m serious.
Zack: Man, that’s a good start.
Prudence: Before I do any work, meditating, and starting the day with open mind, good intentions, positivity, clarity. From there, it’s all about being lean. Yup. It really is. When I was working with the PassivScience team, a large part of our product delivery approach was being lean. That means creating what’s called “standard work”—things that you do again and again—and actually purposely taking extra time when you develop standard documents and process flows to really think it through. You know you’re not just going to use this document once and then on the next project reinvent it again. Instead, you’re creating a resource for yourself so you can work smarter and have a process of continual improvement on every single project. So, really, that’s the backbone of everything that I do with my team and with my own projects. It’s having as much standardization as possible so it’s always there to go to as a resource. Those documents are living so that they can be continually approved.
Ultimately, it’s about teaching people to fish, right? Because there’s no way I could manage all of this on my own. I think this is about the maximum. But it’s at the point now that I have team members in the East that are taking projects and running with them, and I’m doing quality assurance and being a resource for the tricky stuff. There are enough standardized startup meeting agendas, checklists, and quality assurance documents that people can just follow through and know they’ve got it covered.
Right now, between PHI and PHIUS, there are so many different documents. I mean, PHIUS consolidated their Passive House certification guide and their quality assurance protocols into one big document in this version 2 update, which is great, but it’s all text. It’s all in narrative format with external links. It took a long time, but I was able to condense everything down for both PHI and for PHIUS. It’s short, it’s sweet; there are checklists, there are links to where you need to go. All of the extra putzing around has been eliminated, and that really helps things flow more smoothly.
That’s part of that critical path approach that I was describing to you, where’s it’s like, “Okay, what is the most efficient, direct method to get through projects where there’s a million things happening at once.” On every project, it’s always the same. There’s always a million things happening at once. So, really, the key for Passive House folks is to understand, number one, that we’re all here for a reason. We’ve all been drawn to Passive House for often a very passionate reason. It may not all be intellectual. I think a lot of us are in it with heart, right? You’re in it with heart.
Zack: Yeah. Absolutely.
Prudence: And a lot of us, you know, we care about our communities; we care about the planet; we care about our families. And so, when I talk about a critical path and a through line for dealing with complexity, that’s almost the very first thing, and the critical path is, “Okay. Are you coming from your heart?” And if you’re coming from your heart, how do you want to create an environment working with people? And being drawn to Passive House because we care, if we can keep a focus on that caring and use that to create collaborative practices where we’re leading, but we’re not leading with ego, we don’t need to; we have the laws of nature behind us, right? I mean, that’s what Passive House is; it’s like, “Hey, here’s physics. Here’s how it works. It’s the laws of nature. That’s how energy flows.”
So, we don’t have to lead with ego—but we can, if we Passive House people accept, that we’re here for a reason; we’re here to lead; we’re going to lead with heart, we’re going to lead without ego; we’re going to share—then that critical path, becomes, “Okay, how can we eliminate waste? How can we create a positive, collaborative environment where everyone gets to take part, everyone feels good, we’re all learning, we’re all having continual improvement, and it’s fun, then that’s it! That’s the critical path. And then everyone gets excited about it, innovation comes, creativity comes, and then we really start transforming the industry.
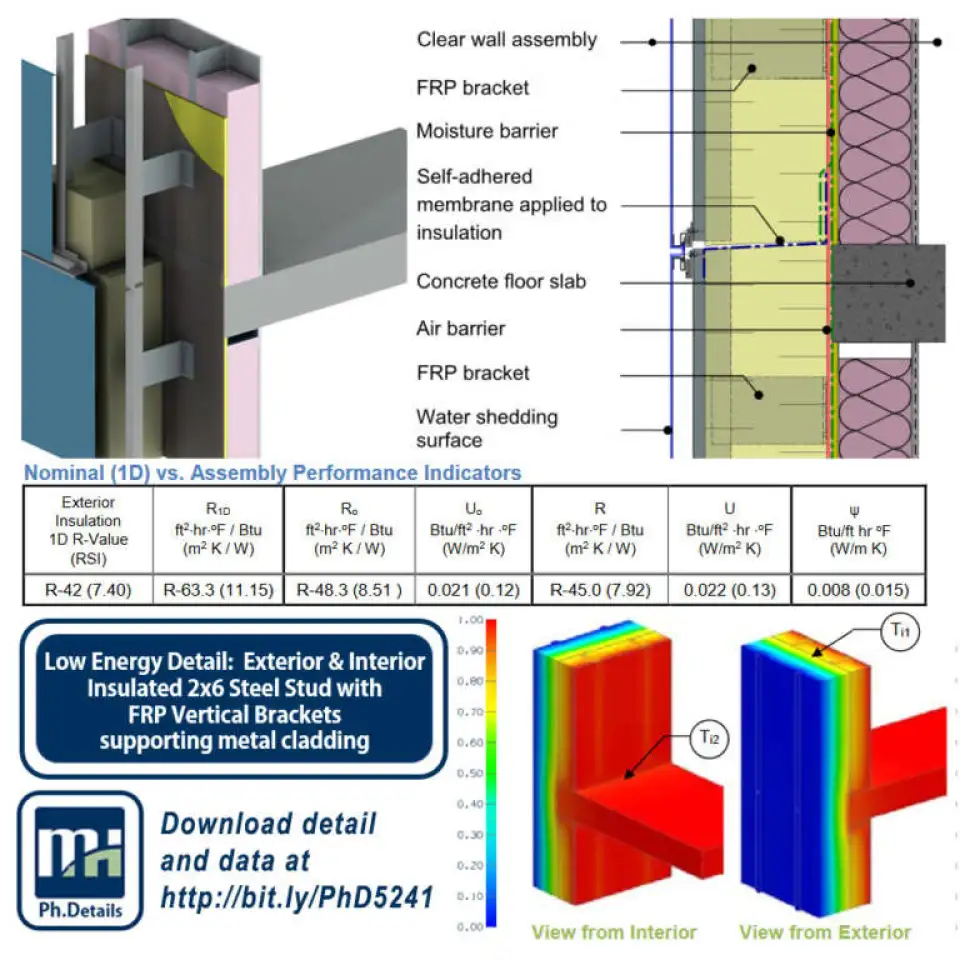
Zack: I definitely feel that we’re kindred spirits in terms of what is motivating our participation in Passive House. We reconnected recently because of outreach that you’ve been doing around your Passive House Details group on LinkedIn, and this idea of the spirit of collaboration and sharing how the laws of nature should impact how we construct buildings. Could you talk a little bit about that effort with the Passive House Details group and what Morrison Hershfield is up to around sharing details with the world?
Prudence: One of the most challenging parts of successfully designing high-performance buildings is overcoming the attitude of, “This is the way we do things.” I think sometimes there’s comfort for designers, for architects and engineers, and a feeling of groundedness in that idea of “This is the way that we do things,” or “We know what we’re doing—we’ve got it covered.” But oftentimes, and especially as we move into these larger-scale, more complex buildings—whether they be a seven-story tall multifamily building or a 30-story tall office tower—the architects and the designers that are typically involved with these kinds of developments, they’re very skilled. They’re used to handling a lot of complexity and they’re used to working with very high caliber teams. However, they don’t necessarily know about Passive House. And when it comes to detailing, that’s usually something that’s happening too late in the design development process.
One of the things that happens when you’re dealing with developments at this scale is that the timelines are condensed. If you’re affordable, oftentimes there’s a funding cycle. If it’s market rate, there’s a developer sitting behind it all that’s funding the effort, and every single day is money. Any delays or any significant extensions of that construction timeline is impacting their bottom line in a very serious way.
What often happens is that you’ll be going through design, and there will be a point in design-development where the project starts being bid. Pricing starts being done when not everything is even developed. All the small details that need to be covered with Passive House—every single element, be it electrical, mechanical, or water penetration, everything that’s going to happen on these large-scale buildings—they’re not designed yet. That doesn’t happen until shop drawings and the project is already being bid. So what happens, from a big picture perspective, is you’re dealing with “building the plane in flight” syndrome. The plane is taking off, it’s flying, construction is starting, and not everything has even been designed yet. The architects—my heart goes out to them—they’re just caught in the middle of this process trying to get things done, but they don’t have enough time.
Morrison Hershfield is very good at being an ally for architects and for design teams in general when it comes to the envelope—helping from very early design to get the team thinking about these things, suggesting practical solutions that actually work. And because of the work that Morrison Hershfield has done over the years in this role, they have received funding to develop the building energy thermal bridging guide, a fantastic resource. It has details in it from all walks of life, if you will—both low-performance and high-performance.
In recent years, Canada has begun to dedicate itself to low carbon emissions buildings—they stuck with the Paris Accord when the US bailed. British Columbia as a province has a very aggressive Step Code and a very aggressive plan towards carbon emission reduction. So, the inclusion of high-performance energy details in the building energy thermal bridging guide has created a resource for Passive House buildings.
Now we all know that, when it comes to Passive House, there’s no prescriptive detailing. We all know that the idea is to eliminate thermal bridging and to design as simply as we can, but high-performance details that work for Passive House buildings will also work for zero-carbon emissions buildings. When we’re talking operational energy, they’ll work for any kind of high-performance building. So, when we started the Passive House Details group on LinkedIn, it was more to open up this resource to folks in the Passive House community who maybe did not know that it existed. Moreover, apart from sharing resources that have already been created and data that has already been created, we wanted to invite people in the Passive House community to form a brain trust around detailing because there’s no reason we need to keep reinventing the wheel again and again and again.
We want to increase knowledge about what constitutes thermally efficient detailing and what some of the best practices are. You know, there are some MacGyver approaches out there for sure, and some of them are great. We want to share information regarding what works, what doesn’t work, from multiple perspectives—not just the architect’s perspective, but also from the contractor’s perspective, and from a developer’s perspective in terms of cost. The more we share, the quicker our entire community of Passive House practitioners is going to be able to get up to speed and it will allow for the practical implementation of these more complex, larger-scale buildings that are not wood anymore—these are concrete and steel structures for the most part, with steel studs and exteriors; they’re non-combustible buildings. It’s a different animal. Not to say that we can’t do large-scale buildings out of mass timber and CLT (cross laminated timber). That’s happening, that’s coming. The codes are allowing for it more and more. I think in some places we’re up 12 or even 18 stories. Even with those, even as those buildings come online, sharing details around what works, what doesn’t work, do you insulate internally, do you insulate externally. We’re going to be sharing some of those details on the details group pretty soon.
That’s the idea. It’s to create a brain trust so all of the boats can rise at the same time—or all of our brains can recalibrate.
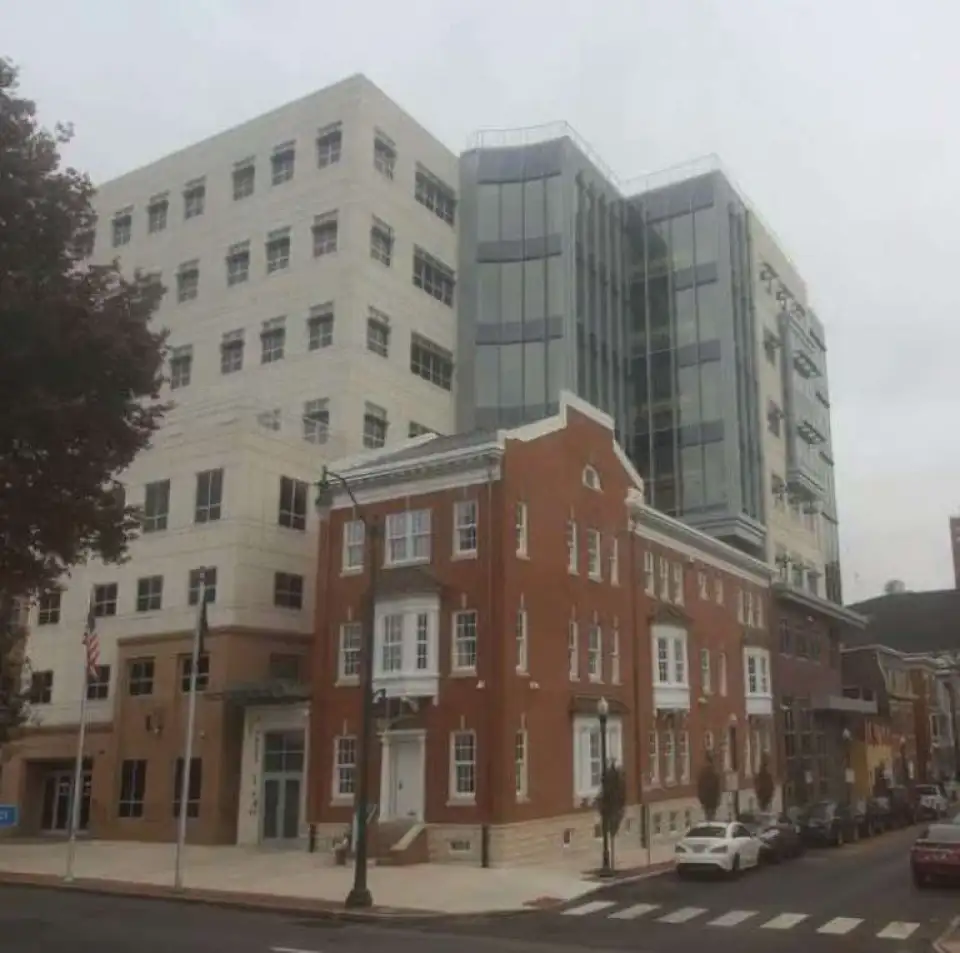
Zack: One of the things that you mentioned in the email to me was the Pennsylvania Housing Finance Agency’s headquarters building is nearly done.
Prudence: Yeah. We have a close out call tomorrow.
Zack: And this is in Harrisburg, Pennsylvania, right?
Prudence: Yes.
Zack: Could you say a little about why, first, it’s significant that PHFA is doing this building, and, secondly, what’s special about the building itself?
Prudence: Pennsylvania was the first state to incentivize Passive House for low income housing tax credits (LIHTCs). [Learn more about PHFA’s Passive House-friendly policy regarding LIHTCs here.] When they opened that program, they were equally interested in any Passive House approach—the PHI approach, the PHIUS approach…it didn’t matter. What happened pretty quickly is that they started getting more technical expertise as their staff reviewed these projects that were applying for funding, and at some point they realized, “You know, we have this project on the drawing board for our headquarters, and it’s already fairly far along. Why should we not do Passive House? Let’s look at the feasibility of actually accomplishing Passive House.” And it’s comprised of both an addition of a new, seven-story curtain wall tower—two facades are curtain wall—and a full Passive House retrofit of an historic brick building.
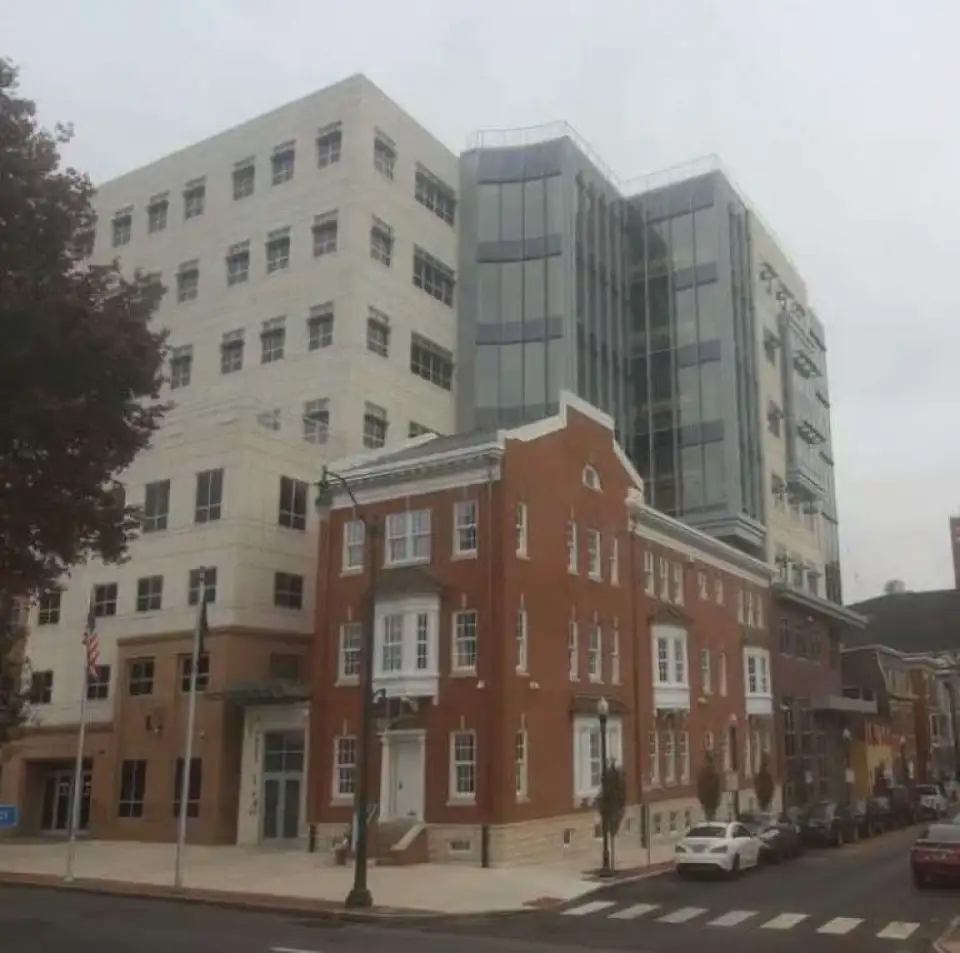
Those two buildings are attached. They’re attached to a larger, existing office that PHFA is using, so there was complexity there. But the significance of them wanting to walk the walk can’t be overstated. It really needs to be celebrated. They committed themselves to going through that process rather late in the game. This is definitely a project where we had the syndrome of building the plane in flight, and there have been a lot of somewhat painful lessons learned on that one on all sides.
The building does does have a lot of glazing. It’s a curtain wall system on two facades and on the front facade or street-facing façade it’s an insulated metal panel with some punched windows and some storefront-style glazing down below. One of the things we struggled with early on was how to keep the building from overheating. The solution that we came to was electrochromic glazing. It’s the first high rise—seven stories qualifies, apparently—Passive House building in North America that is using curtain wall and also electrochromic glazing.
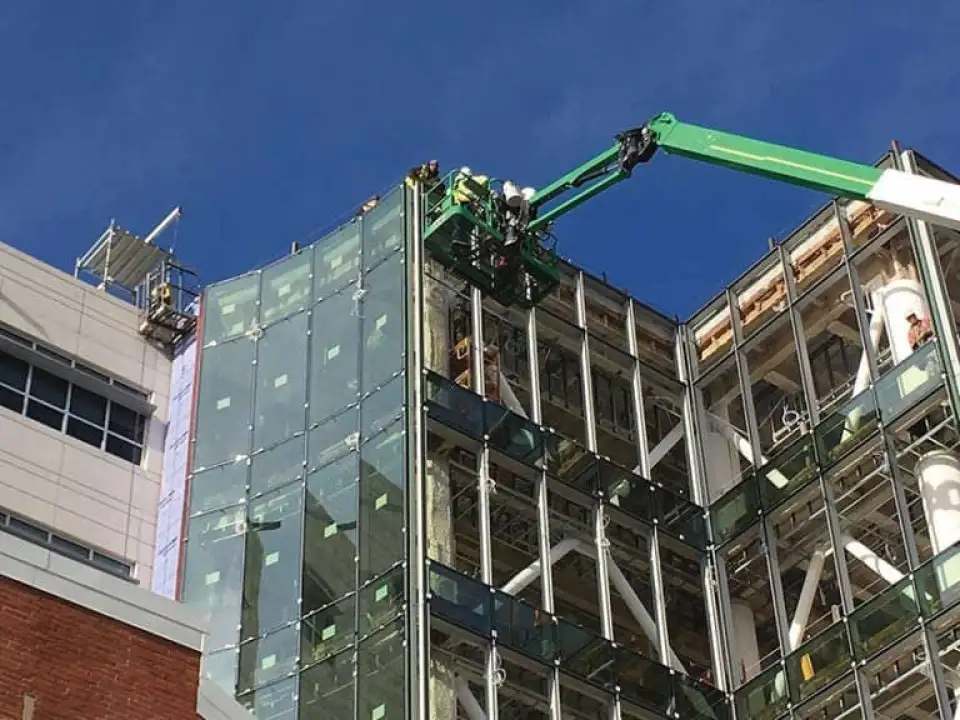
I’m very excited as folks are getting settled in there and the building is operational to get feedback from PHFA on how things are going and how they’re loving the building. The detailing, the coordination, the field verification…there are so many lessons learned in all of those that we’ll carry forward into much of the work that I’m doing now with Morrison Hershfield. I’m super honored to have been part of that project.
Zack: I’ve had my eye on it for a while just because I’m aware of and excited about the affordable housing policy around low-income housing tax credits for Passive House and the impact it’s had in Pennsylvania. It’s really exciting to see PFHA walk the talk, so that’s great. Speaking of firsts and of high rises, I think you have a big building in Vancouver you’re working on, right?
Prudence: Well, again, it barely clears the definition of high rise because it’s seven stories. It’s actually a building that’s owned by the City of Vancouver and their tenant is Artscape. The ground floor will be gallery space and the upper levels are all art production spaces. It’s unique because we don’t know who the individual artists will be that are inhabiting the space and will be working there and exactly what kinds of processes they will be bringing in their art production. So, figuring out how to model that was a little challenging. We worked with PHI to agree on a path forward that made sense and that was as accurate as we could make it, and then agreed with the City of Vancouver on a general policy for Passive House projects that are going to be doing tenant improvements. There are more that are going to be coming for sure.
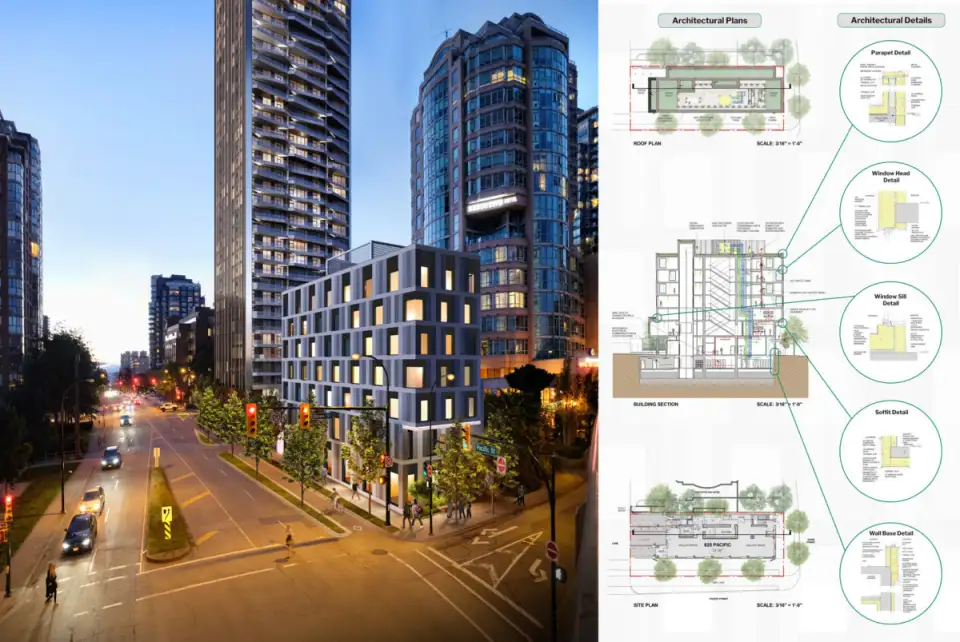
The walls system is innovative. It’s non-combustible. I posted some mockups that are almost what we’re doing on Instagram a few weeks ago, and, as the project moves forward, I definitely will be documenting and posting. It’s essentially a concrete structure, steel frame, steel stud wall with exterior mineral insulation and thermal clips. Rather than vertically spaced thermal clips, we’re doing horizontally spaced because you can get much wider spacing. You can do 48-inch on center instead of 16-inch on center, which has big implications for labor savings and labor time if we’re talking about exterior access and pump jacks or scaffolding or swing stages.
The interesting thing is, looking in the thermal clip world—and there’s plenty of them out there by now—is some of them may have lesser thermal performance when you look at the clip in a vacuum. But then when you actually look at how it’s applied and how the spacing works, horizontally spaced clips 48 inches on center, although the individual clips may have worse thermal performance than a vertical clip system, you have a lot less of them, and so the overall thermal performance ends up being better.
Zack: Interesting. That makes sense.
Prudence: Also, we’re using a heat pump water heater in that one. There will be definitely some other interesting details coming out of it. I’m really looking forward to the process. It’s really the first time I’m getting to be in the trenches and in the same place, in the same town, with a project team on one of these larger scale nonresidential projects. I’m really enjoying getting to work with Leadcore, who’s our construction manager, and looking at their quality assurance process and talking about ways we can streamline it on not only this project but future projects. Already, although we’re just in the ground now—construction is just starting—there’s already a lot of lessons learned that we’re sharing with the community.
We actually have a low carb—low carbon—lunch coming up this Friday where we’re going to be talking about just that, and, really, some of the revelations that have come out of it so far are the huge benefits of having coordination meetings that might not ordinarily happen. Obviously, Passive House preconstruction kickoff is really important to get everyone on the same page about what’s going to happen during construction and how its different and what needs to be kept track of and verified at what stages. But when it comes to things like coordinating shop drawings and reviewing shop drawings, we’re coming up with some pretty innovative and streamlined approaches that everyone is really having fun with. The whole tenor of the team, at least as far as I can tell, has actually changed to being much more collaborative and fun. People are just picking up the phone and sharing ideas. It’s just really starting to bubble in an organic way that I’m enjoying. We’re finding ways to be super efficient, so it’s great!
Zack: That’s awesome. Well, we’ve covered a lot of ground here. Is there anything else that you want to add here?
Prudence: I think just going back to what I was talking about before and remembering why we’re all doing this and bringing that to the office, the conference room, the construction site, every day. We are leaders. We are doing something new. Sometimes we may get arrows in the back, but, you know, we need to just remember to keep our hearts in it and to try to spread that feeling, that awareness, amongst everyone. That’s definitely what keeps me going.
Zack: Absolutely. Right on. Thank you.
Prudence: You’re welcome!