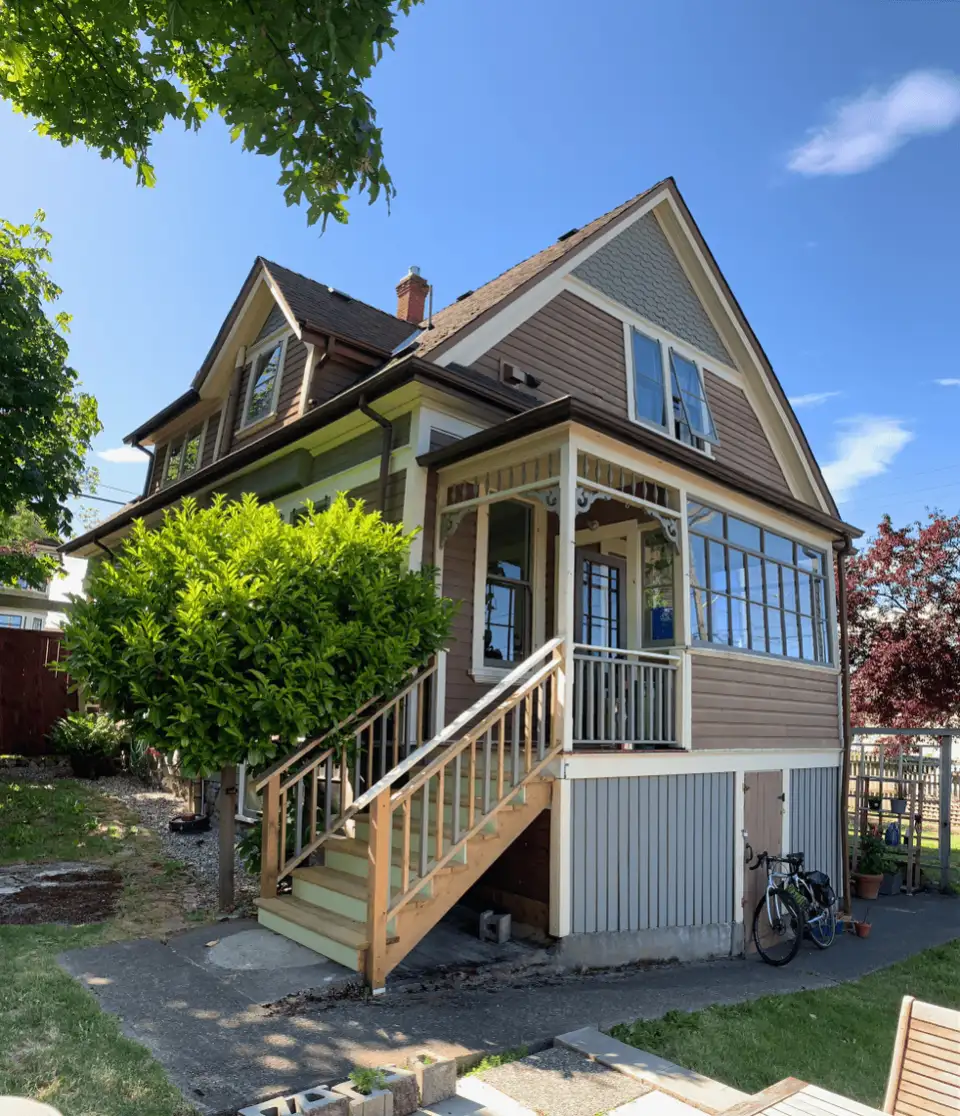
When it comes to combatting climate change, the high-performance building industry has made great gains by focusing on reducing operational carbon emissions in buildings, resulting in new homes that use far less energy than existing ones. However, focusing solely on operational carbon emissions is short-sighted and misses the whole picture. We should be asking additional questions: what is the impact of embodied carbon, how does it relate to operational carbon, and how should we consider their relative importance? Considering these questions helps our architecture firm better serve our clients, especially those who are choosing between renovating their existing homes and building new high-performance homes, and it helps drives best practices within the industry.
Many in the industry have strong opinions about retrofits, and we often hear the phrase, “The greenest house is the one that’s already built.” Is this the case? To help answer this question, Waymark Architecture and Energy Code Solutions worked together to compare two real-world projects, together with a number of additional hypothetical scenarios. Our goal is to contribute to the conversation about measuring both operational and embodied carbon emissions in buildings and to advocate for best practices.
Two of Waymark Architecture’s current projects made ideal candidates for this analysis. The first is a registered heritage house, for which we are designing a renovation that includes energy efficiency upgrades. The second is a new build, located a block away, which will be certified to the international Passive House standard and uses commonly available low-embodied-carbon materials. Both single-family homes are located in Victoria, BC, in climate zone 4 (CZ4). In addition to these two real-world examples, we included four hypothetical scenarios and looked at the data across a broader range of climate zones.
Our analysis indicates that the greenest house may not be the one that is already built. Instead, a new build that uses low-embodied carbon materials to achieve an operational standard that may not be practical for a retrofit will perform better in the long run than an existing single-family house that has been updated to improve performance. While the best solution will always depend on the circumstances, materials do matter, and operational emissions matter more, especially considering the longer-term trajectory of the scenarios we have analyzed.
The Scenarios
Scenario 1 - Retrofit
This house is in Victoria, BC. Due to its heritage status, it has some significant restrictions on what can be done. We have proposed a triage approach where we address the more poorly performing aspects of the house within the boundaries of the heritage status and budget constraints. This means improving airtightness, updating the attic insulation, and adding basement insulation and an air source heat pump. No drywall demolition was considered in this approach, nor was a heat recovery ventilator (HRV) added as this would have required significant drywall demolition. If we had added an HRV, the embodied carbon (EC) of additional drywall would significantly rise with a minimal pay-off on energy savings in CZ4. Wood-framed double pane windows (the lowest EC replacement) have been proposed, as windows constituted the biggest heat loss.
Scenario 2 – Low-embodied-carbon Passive House (LEC PH)
The Sugar Cube house is also in Victoria, BC. (For more information on the Sugar Cube house, see “The Sugar Cube House: How Prefab and Passive House Can Accelerate Infill Housing” in this issue.)
Scenario 3 (hypothetical) – High-embodied-carbon Passive House (HEC PH)
For this case, we used a Passive House of the same shape and size as the Sugar Cube house, but instead modeled it as built with high-embodied-carbon materials.
Scenario 4 (hypothetical) – Base with air source heat pump
For this one, we left the heritage house as is, except we replaced the current gas heating with an air source heat pump.
Scenario 5 (hypothetical) – Base with baseboard
Again, we left the heritage house as is, except we replaced the current gas heating with baseboard heating.
Scenario 6 (hypothetical) – Base with gas furnace
Here we left the heritage house as is, including keeping its current gas heating.
In addition to analyzing these scenarios in CZ4, we also analyzed their performances in CZ6 and CZ8 to see how similar choices would play out in colder climates. The thickness of insulation, sizes of mechanical systems, and other factors were adjusted to suit.
Methodology
For our analysis to be the most useful, we employed a consistent methodology across the six scenarios. Access to all data and calculations is available in the footnote. Table 1 outlines the tools and parameters used.
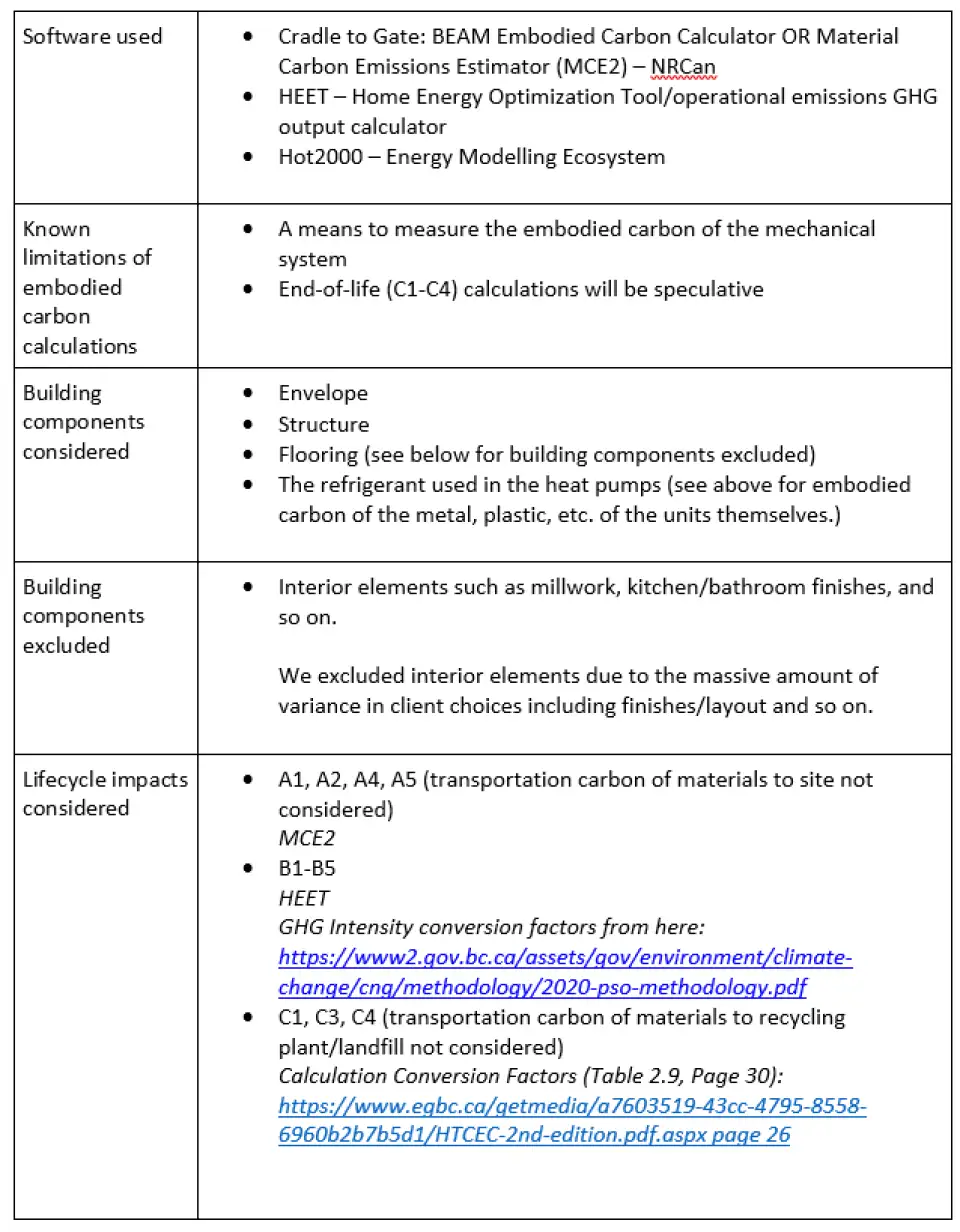
With the tools and parameters defined, Energy Code Solutions conducted the following steps.
1. Model each individual case in each CZ in Hot2000.
2. Import the geometry from each case into MCE2 calculator.
3. Assign assemblies to each case in MCE2 calculator to establish A1-A4 for each case.
4. Create CSA-F280-12 heat loss calculations for each heat pump case in each CZ to size the mechanical systems properly. (Note: CSA-F280-12 calculations not required for other cases as heat pumps are Type 2 heating systems. Type 1 systems (furnace and baseboards) have a calculated capacity assigned to them.)
5. Use CIBSE heat pump calculator to establish EC of the heat pumps.
6. Use CIBSE calculator to estimate EC of HRVs in PHs.
7. Use HEET to extract yearly operational carbon from each H2K file.
8. Use MCE2 calculator to establish quantities (volume) of material for C1-C4 of base case.
9. Estimate weights of materials via research docs. (MCE2 calculator outputs volumes and is closed source on its EC conversion factors. The volume of material was then multiplied by a kg/m3 conversion factor, and then multiplied by the C1-C4 conversion factors from the 2022 engineering report from the Institution of Structural Engineers.)
10. Use the engineering report and its C1-C4 conversion factors to establish EC of demolition.
11. Estimate the percentage of materials recycled, incinerated, and disposed based on experience as a PH project manager.
12. Estimate the percentage of materials reused based on City of Victoria Deconstruction Bylaw requirement.
13. Start plots at the sum of (A1 to A4) + (C1 to C4) of each case (bar graphs labeled Invested Carbon quantifies these); operational carbon is then applied over time with properly sized mechanical jumps every 25 years for replacement taken from the CIBSE calculators.
Results
Our analysis shows that the first priority should be to reduce operational emissions. This finding is not surprising and reflects the long-standing focus of the high-performance building industry. A very close second priority should be to choose responsible materials. A high-embodied-carbon house, even one built to the Passive House standard, is never the right choice. In CZ4, it takes 50 years for the low operational carbon to make up for the embodied carbon and about 63 years for it to surpass the retrofit scenario (see Figure 1). The colder the climate zone, the shorter the payoff. In CZ6, the payoff for the high-embodied-carbon house is 27 years and 17 years in CZ8 (see Figures 2 and 3), respectively. In comparison, the low-embodied-carbon house has a payoff of 16 years for CZ6 and 9 years for CZ8.
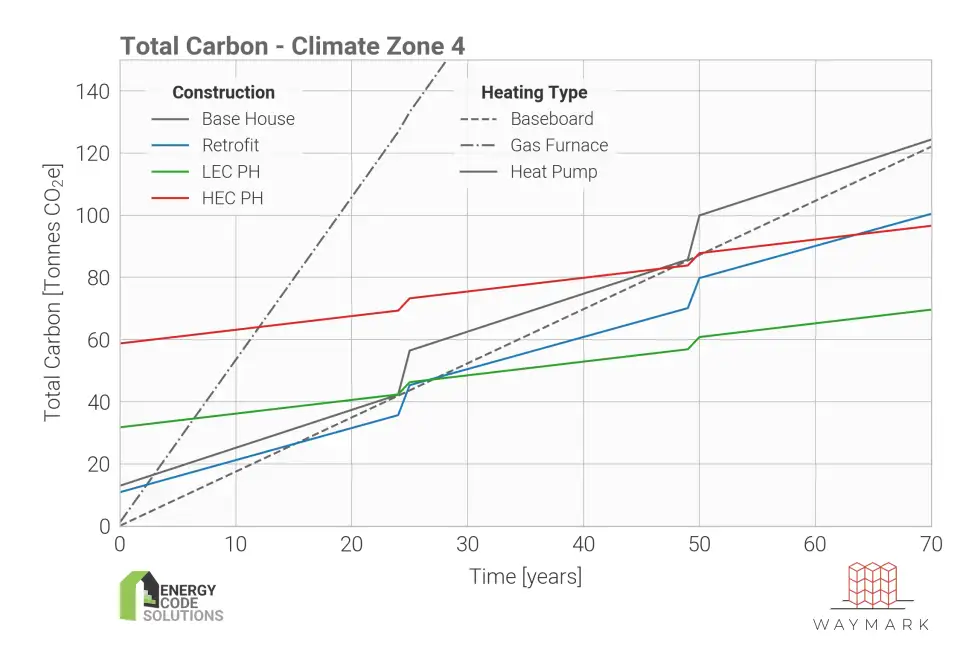
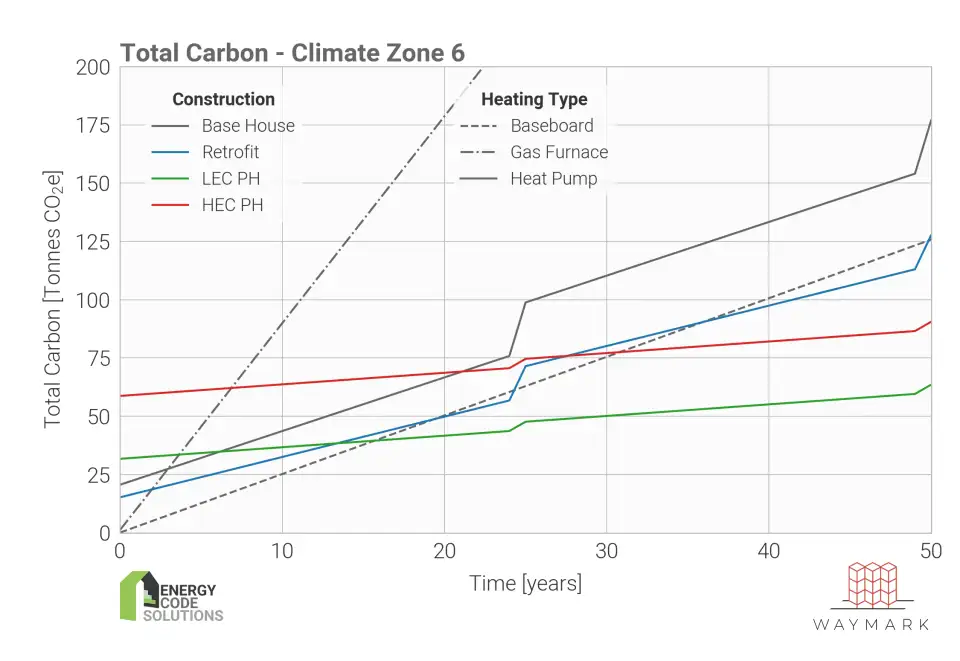
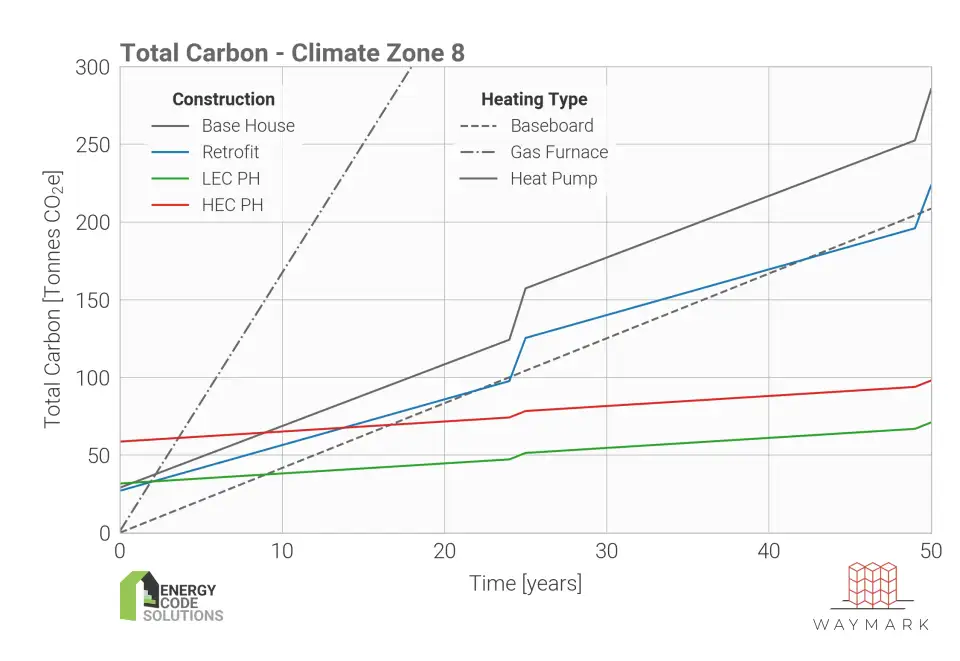
The most consequential impact of failing to prioritize the reduction of operational emissions first is that heat pumps necessarily end up being larger. We are assuming that heat pumps will be the standard, as even in colder climates dangerous heat events will become the norm, necessitating the cooling a heat pump will provide. A larger heat pump means more refrigerants, which have extremely high global warming potential and, as such, are a considerable portion of the embodied emissions in all scenarios (indicated as A1-A4 Mechanical in Figures 4, 5, and 6). The larger heat pump is the entirety of embodied emissions for the scenario where the only upgrade is fuel switching. The difference between Scenario 2 (LEC PH) and Scenario 4 (Base with air source heat pump) best shows this. A larger heat pump is needed in Scenario 4, and the embodied greenhouse gases are higher as a result. In Scenario 2, the upgrades that improve efficiency allow for a smaller heat pump and have less of a greenhouse gas impact than the larger heat pump in Scenario 4.
The impact of refrigerants consistently points towards the importance of having smaller loads on heat pumps so that you can have smaller units—a win for high-performance construction in every case. In other words, failing to reduce operating emissions necessitates higher embodied emissions from the mechanical systems.
In CZ4, the EC of the heat pump is nearly the same as all the building components of the low-embodied-carbon Passive House. This only worsens as we move to colder climate zones where the Passive House’s heat pump sizing remains the same as we have a much more efficient envelope. However, the existing homes drastically increase the heating load as their envelopes are much less efficient, skyrocketing the required heating system sizing and thereby massively increasing refrigerant usage. Changing fuels to electricity is only environmentally friendly if the heating load is reduced first; otherwise, we run the risk of greenwashing. In CZ6, the EC of the heat pump is 20.6 tonnes, whereas the EC of the low-embodied carbon Passive House is still 13.4 tonnes.
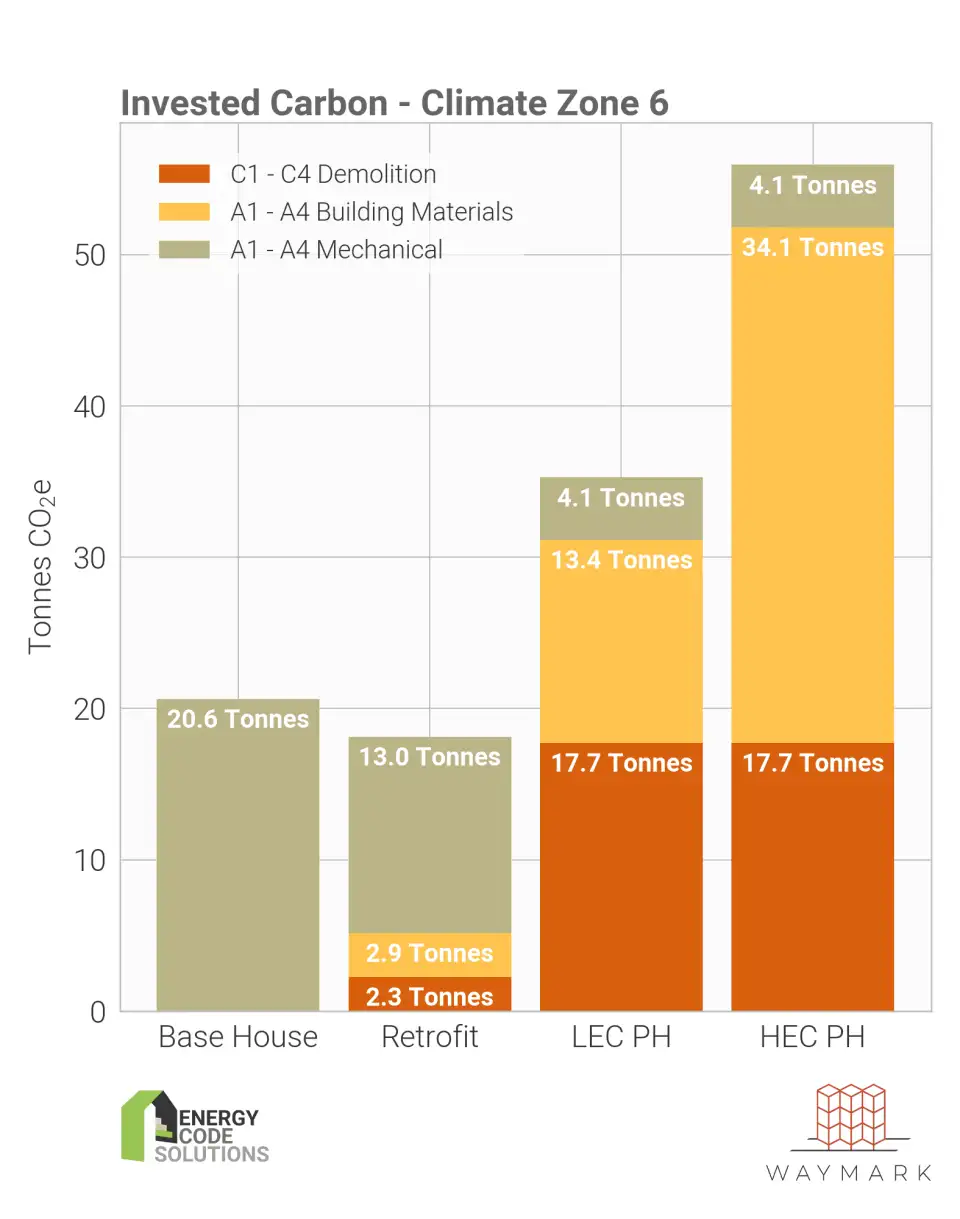
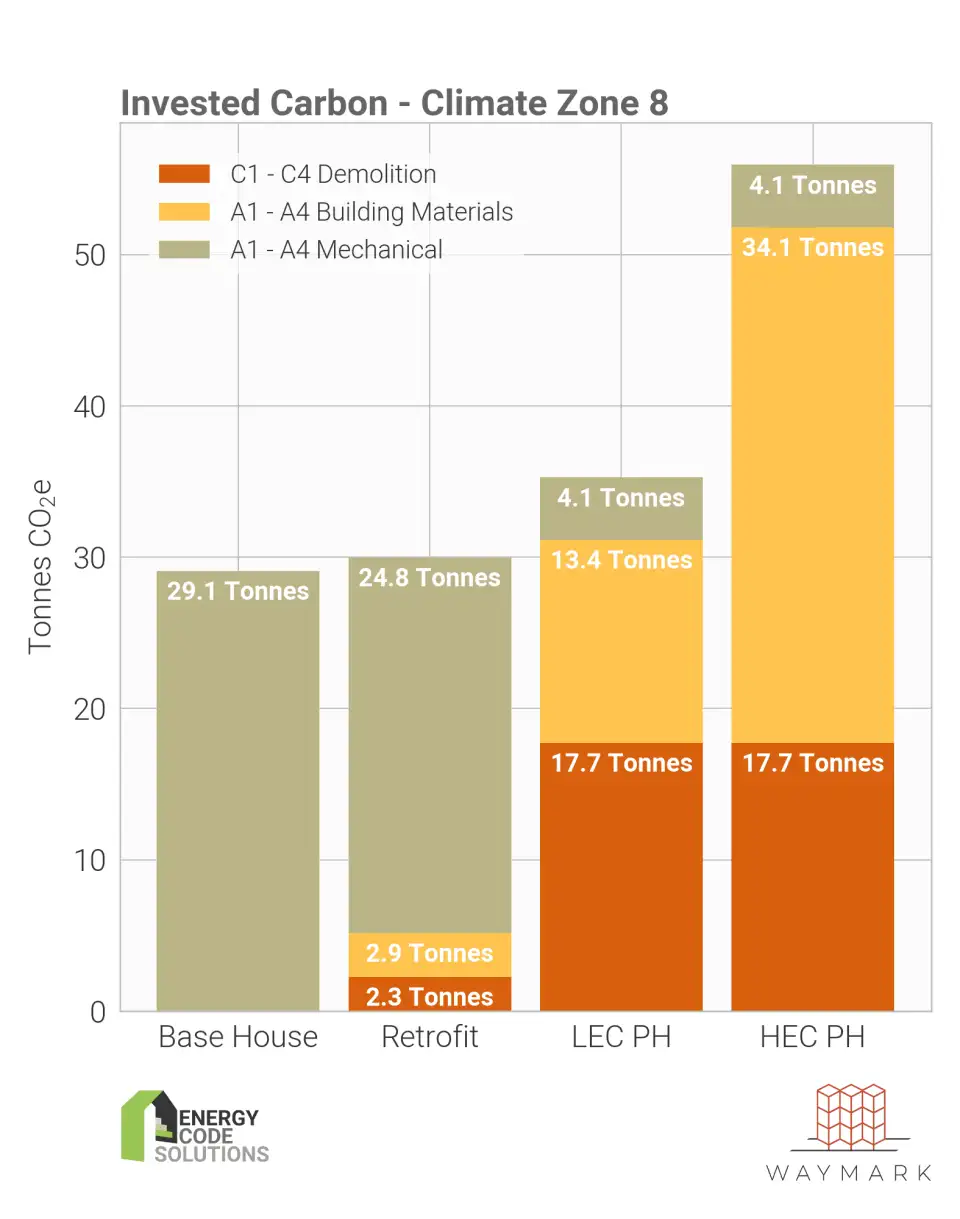
Not included in the analysis is the consideration of CO2 heat pumps, which are new to the market and drastically reduce the carbon impact of mechanical systems. However, these heat pumps require a relatively high-performing house as their output capacity is limited. For this analysis, we assumed identical refrigerants for each case, only changing the capacity of each heat pump. All heat pumps were sized with a CSA-F280-12 calculation.
Moving on to the non-mechanical building materials, a detailed embodied carbon analysis shows that the most significant impact in Scenario 2 (LEC PH) stems from the concrete and windows, highlighting the importance of responsible overall design and of material choices. This result clearly points to the importance of a design that only uses as much concrete as necessary. For example, Waymark Architecture made key design choices for the Sugar Cube house that included using concrete only where needed and eliminating the need for slab or foundation foams by placing the Passive House envelope above grade.
There are places where the use of concrete and high embodied carbon foams are the only practical solutions. However, these situations can be drastically reduced or eliminated with early design decisions, such as massing and locating the thermal envelope of the building. If we don't make these adjustments, there is a real potential for the reduced operational emissions to never make up for the carbon that has been invested upfront.
Another takeaway is that timelines matter; the right decision from a GHG-only point of view depends on whether you are looking at 2030 targets, 2050 targets, or some other timeframe. The conversion factors we used are the same as how the province of British Columbia will be evaluating its greenhouse gas intensity (GHGI) targets. They will also be adopted by the city of Victoria in 2025. Interestingly, many scenarios converge after around 25 years in CZ4 with approximately the same total GHGs, although from very different sources. After that time, the better the envelope, the fewer GHGs, except for the high-embodied-carbon Passive House.
The colder the climate zone, the more operational emissions matter. In CZ8, operational carbon tends to be more impactful than embodied carbon until roughly 25 years out, and the low-embodied-carbon Passive House outperforms all the other options in less than a decade. Looking only through a GHG lens and considering primarily the goal of reaching net zero by 2050, the low-embodied-carbon Passive House surpasses the other scenarios by a small margin. This margin only increases over time, which leads us to the conclusion that the greenest house is not the one already built.
In coming to this conclusion, the time value of GHG emissions becomes an important part of the conversation. To mitigate the most catastrophic effects of climate change, we need to get to net zero as quickly as possible. To do this, some argue that we need to avoid the embodied carbon emissions of new buildings. However, this is short-sighted, because we need to also factor in the long-term trajectory that our actions today will determine. Our position is that we need to do both—lower embodied carbon emissions in a responsible way and lower operational emissions.
The building industry also has a unique opportunity compared to other industries. By reducing operational energy use, we can free up energy capacity for use in other industries where such deep reductions in energy demand are harder to achieve. For example, transportation will need additional grid capacity as vehicle fleets electrify. Consequently, transforming our industry is a crucial step in the larger strategy to decarbonize our economy, and provides the other benefits of efficient buildings, like better comfort and air quality.
Limitations of this analysis
This analysis is limited to single-family wood-frame houses. We expect different results for other building types. The scenarios we analyzed are also all looking at like-for-like replacement when it comes to land use; they do not consider scenarios where a higher density building could replace a single-family house. Land use patterns are extremely significant for car use and transportation, and other city-wide considerations. In our opinion, the conclusions we come to with like-for-like replacements mean we should not be precious about keeping existing single-family housing stock, and there will only be more reasons to replace them in cases where higher density land use is appropriate.
The various tools available for embodied carbon calculations tend to give quite different results. This, of course, leads to a distrust of the data. For this analysis, we have kept consistent how the different scenarios are measured. We believe that if the method is consistent, the comparison between scenarios will be valid, even if there is doubt about the final numbers.
One assumption we have made is that the grid-supplied electricity will have a consistent GHG profile. This is not an assumption that will hold, but it is reasonable to assume it will keep longer in BC than in other places.
Conclusion
In summary, the biggest takeaways from our analyses are:
There is a real need for advancements in and eventual standardization of the measurement of embodied carbon.
There is no clearly better answer between a careful retrofit and a new build, low-embodied-carbon Passive House in CZ4 when measured over a 25-year period.
Beyond 25 years, there is a clear benefit to the newly built, low-embodied-carbon Passive House.
In climate zones colder than CZ4, there is a clear benefit to the newly built, low-embodied-carbon Passive House.
High-embodied-carbon building materials should always be minimized as much as possible or avoided completely.
Refrigerants have a huge impact on global warming potential, and better efficiency means less refrigerant.
Calculating the overall carbon impact of buildings is critical to effectively addressing climate change. These calculations provide a springboard for action. Building professionals have significant influence over design and material choices. The Passive House standard can be part of the climate solution, but not without a holistic look at the total carbon of buildings. We don’t need to sacrifice operational emissions for embodied carbon emissions in new builds, as illustrated by the Sugar Cube house. Policymakers can prioritize carbon in the development of standards, while municipal policymakers can deprioritize saving existing single-family housing stock for environmental reasons. We, as members of the high-performance building community, can continue the conversation about measuring the overall carbon impact of buildings and advocate for best practices.
Top photo courtesy of Will King.
*Energy Code Solutions has provided all access to the data here: https://zenodo.org/record/7021184#.Ywf_-OzMLYU