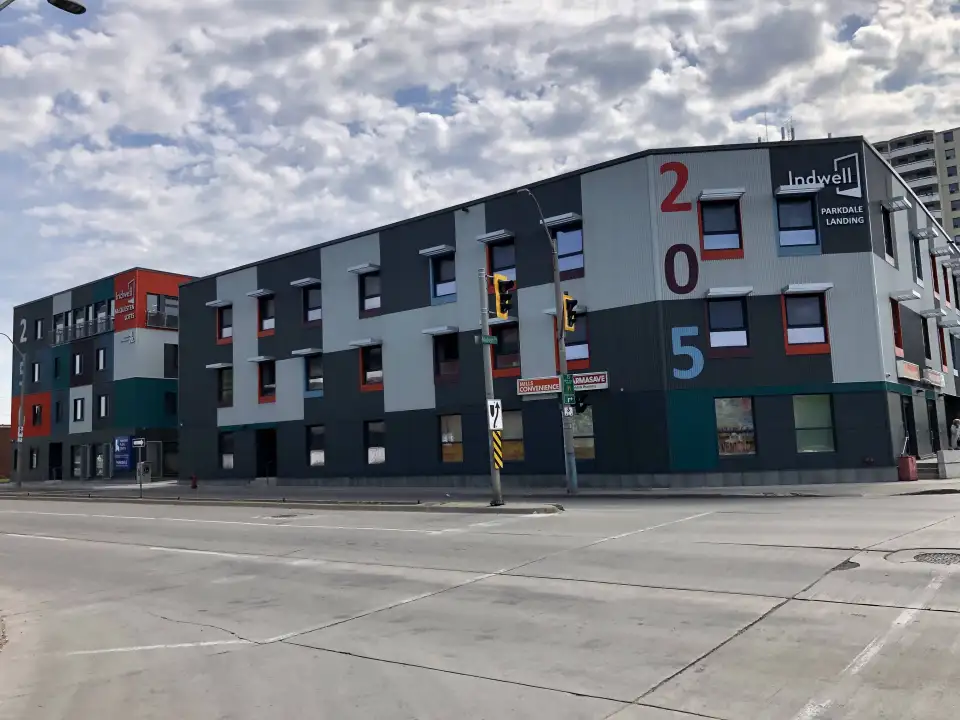
Indwell, a Christian charity that creates affordable housing communities for people seeking health, wellness, and belonging, bought a deteriorating building in East Hamilton with the goal of creating affordable apartments with support services and a community hub. The site was first developed in the 1880s and included retail, a tavern, a banquet hall, and rooming house additions over the past 100-plus years. The finished project transformed the building into 57 studio apartments, including eight barrier-free units. The ground floor includes a community restaurant and food-service training facility, two retail storefronts, and offices for Indwell staff.
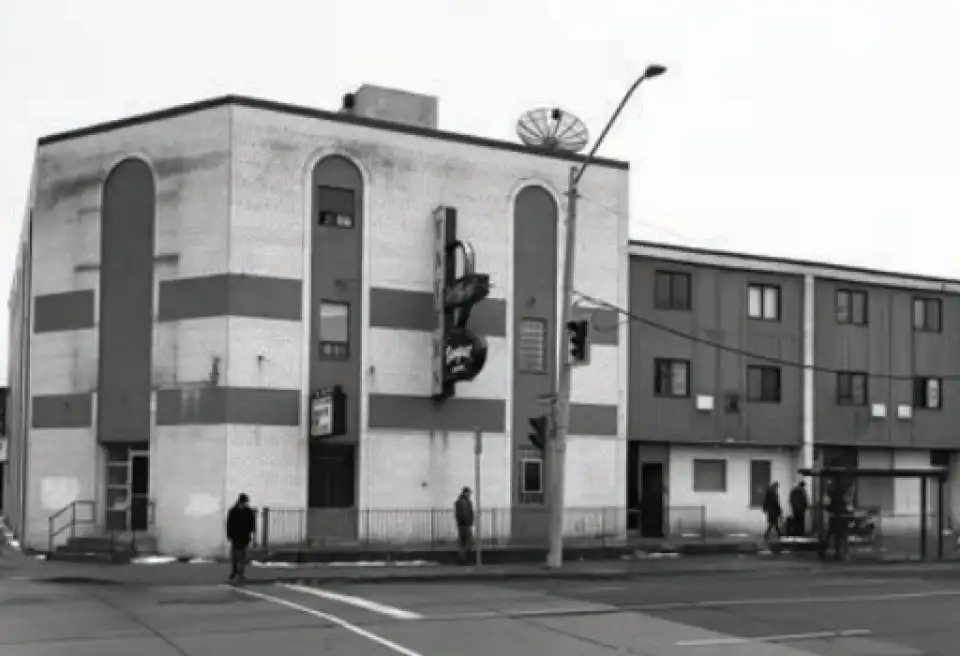
The renovation retained roughly 60% of the original building, while the remainder was rebuilt due to poor structural conditions. “We went through many different scenarios for the building envelope, but all included keeping the majority of the masonry structure,” says Emma Cubitt, a principal with Invizij Architects. “We needed to enlarge and standardize the window openings, which we did at the outset. Keeping the masonry walls and insulating on the outside allowed us to minimize the thermal bridging, unify the façade elements, and retain the maximum interior space for apartments.” The building’s HVAC was also designed to provide all the heating and cooling to the apartments through the building’s two rooftop heat recovery units, along with supplemental electrical heating that will likely not be needed.
The building was less than 12 inches from the property line, so the exterior insulation options called for close consideration. The team found a locally manufactured spray foam with a very low global warming potential (GWP) of 1, and an R-value of 6.6 per inch. The existing masonry façades were topped by a sheet-type air-vapour membrane to ensure continuous airtightness; the spray foam is being relied on solely for its insulative value. Fibreglass clips were used to minimize thermal bridging and attach the new corrugated metal cladding.
Subslab insulation under the existing foundation was not feasible, but 10 cm of XPS board was installed outside the existing foundation walls to 0.6 metres below grade. This was overlapped internally with spray foam up to the basement ceiling. Where there was new construction, 20 cm of XPS was installed under-slab and up the foundation walls to complete the thermal envelope.
Renovating buildings to the EnerPHit Passive House standard is challenging enough, but this project was even more complex due to the building’s programmatic uses. Though the design criteria on usage are feasible, the primary energy targets may prove difficult to achieve, due to a combination of the high ventilation rates for commercial gas appliances in the restaurant and the electrical loads for the walk-in refrigeration and the retail activities of the convenience store and pharmacy.
Schilthuis Construction was committed to the project’s success from the outset, despite this being the firm’s first Passive House build. “We knew that we were learning together with the design team, owner, and trades, so we took our time and didn’t rush any Passive House-related critical stages,” says Beth Schilthuis, project manager. “We’re very happy with the results, especially the airtightness we achieved of 0.3 ACH50.”
The Passive House features were immediately apparent to tenants who moved in in September 2018. The constant suite ventilation means high air quality, and the triple-pane certified Passive House windows make the building very quiet. Despite a very cold first winter, tenants didn’t need to use their in-suite electric heating, relying solely on the high-performance ventilation system and other solar and internal heat gains. This Passive House approach is maximizing tenants’ comfort, energy efficiency, and cost savings, creating long-term benefits for everyone involved.
This case study was originally published in Passive House Buildings book, Passive House Buildings in Canada: Transforming How We Build.