
For more than 40 years, two concrete high-rise towers in North Vancouver owned by Affordable Housing have been providing high-quality affordable housing, but decades of use have led to the need for a serious overhaul. Just from a mechanical perspective, the boilers were original equipment, as were the ventilation units, most of which are failing. Affordable Housing hired Impact Engineering, then known as HiH Energy, to update and optimize the mechanical systems.
Both towers feature a mix of commercial and residential spaces. The south tower has a ground-floor commercial space and 15 residential stories with 122 units. The north tower’s commercial podium takes up 2 stories; its additional 10 stories contain 90 dwelling units. Most of the suites in this social-housing complex are single occupancy, and the population tends to be older.
When Ben Mills, principal and founder of Impact Engineering, heard that Affordable Housing was simultaneously exploring envelope measures, he got excited. If he could bring the teams together, they could work with each other and develop a more substantial and comprehensive building overhaul. “I pitched an EnerPHit feasibility study,” says Mills, whose proposal was ultimately accepted. “It was a deep lesson in truly collaborating, which turned an unambitious project into a great one.”
The feasibility study has turned into a full-fledged plan to proceed with a renovation that is targeting EnerPHit-level energy criteria for the residential portions of the buildings. Both buildings’ mechanical systems will be fully decarbonized, and the building envelopes will undergo major retrofits, bumping up the walls’ effective R-value substantially.
Mills says the project may not quite meet all the EnerPHit targets because of the challenges of renovating a mixed-use building. “In order to make the air-sealing target, we would have to add doors and air-sealing details in the commercial spaces that wouldn’t make practical sense,” Mills explains. “What we will achieve is a high-performing resilient envelope, a decarbonized building, and reduced operating costs.”
The projected cost for all of these achievements was shockingly reasonable, according to Mills. As part of the feasibility study, his firm collaborated with a cost consultant to estimate the cost of replacing like for like and then compared that to implementing the mechanical and electrical portion of the EnerPHit proposal. “The delta between like for like and Passive House was a 25% uptick, which was mind blowing,” says Mills. The EnerPHit building will be far superior in terms of durability, reduced liability, occupant comfort, and resilience. For the first time the mechanical system will be able to actively cool the suites—a safeguard against future potential heat waves. “Financially, this project makes a really strong case for fully decarbonized buildings,” Mills points out
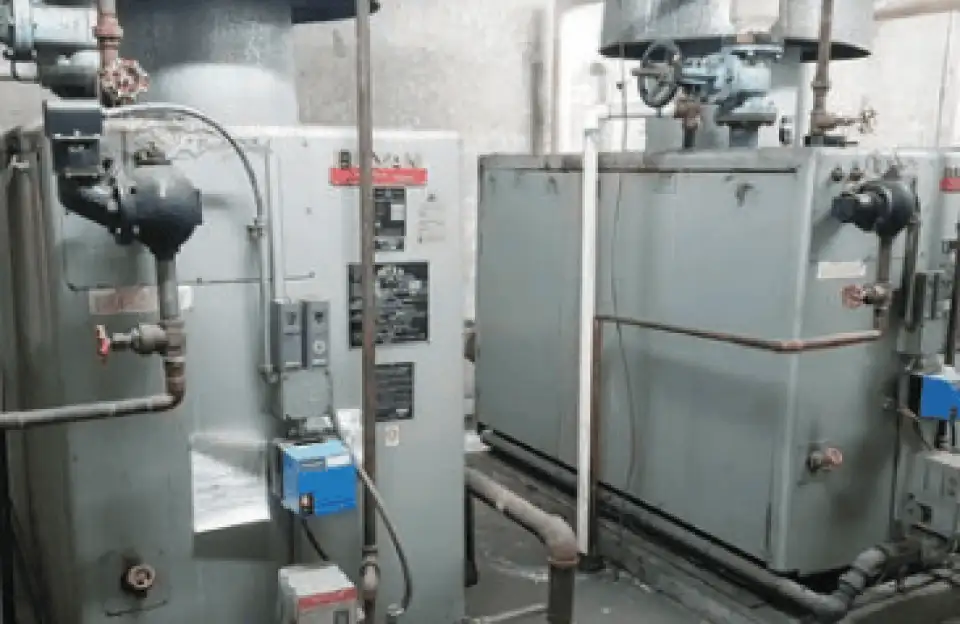
.

Having moved from feasibility study to schematic design at press time, the project is slated to proceed through detailed design in the first half of 2020, with the construction start planned for fall 2020. The retrofit strategy is to work on a floor-by-floor basis, with Affordable Housing keeping enough vacancies in the building that the residents from one floor can be temporarily moved to another floor to accommodate the construction work.
The HVAC equipment will consist of Passive Housequality rooftop HRV units with a heat pump to supply some heating and cooling, along with supplemental electric baseboard heating. Each suite will incorporate up to two small baseboards with hard-wired wall-mounted thermostats. Domestic hot water will be provided by heat pump water heaters on each floor, thus shortening hot water runs and creating some water heating redundancy as compared to a centralized system, which when it needs servicing interrupts the hot water supply for the whole building. As an additional benefit, the heat pump hot water tanks on each floor will provide cooling to common corridors. The all-electric mechanical system will reduce the buildings’ carbon emissions by approximately 450 tons annually, with 9,000 tons of carbon reduced over 20 years of system life for the towers’ residential portions, according to Mills
All envelope upgrades are focusing on exterior solutions to minimize disturbances to the building residents. The proposed envelope refurbishment will start with the removal of the existing stucco walls and the installation of a new exterior sheathing over the existing insulated steel stud wall and the existing concrete walls. The renovated wall assemblies will include a new air barrier membrane, 6 inches of exterior insulation, thermal clips, an aluminum rail, and composite metal cladding panels. Additional membrane detailing will be required around the new mechanical unit curbs, around the parapets, and at the doorsills. The glazing, including the patio doors, will most likely be replaced with thermally broken aluminum-framed high-performance windows. A solar heat gain coefficient of 0.3 will be specified to reduce overheating risks. The airtightness target post renovation has been set at 1.0 ACH50 for the residential portions, in keeping with EnerPHit performance specifications.
Impact Engineering points out that the vast majority of rental buildings in Canada—76% according to a recent study—are of similar vintage to these twin towers. How these buildings get renovated can translate into modest greenhouse gas reductions or a more ambitious transition to existing buildings attaining near zero emissions—and Impact Engineering is doing what it can to make that latter goal a reality