In 2018 the University of Northern British Columbia (UNBC) opened the doors of its Wood Innovation Research Lab, a pioneer in Passive House academic buildings in Canada. This lab and classroom space has been used by UNBC faculty and students for research and testing related to wood construction and Passive House buildings. In August 2023 the building next door exploded, and the resulting fireball eventually spread to the lab. UNBC Director of Facilities Management and Capital Planning David Claus talked about the disaster and the recovery process at the 2024 Passive House Canada conference in Victoria, B.C.
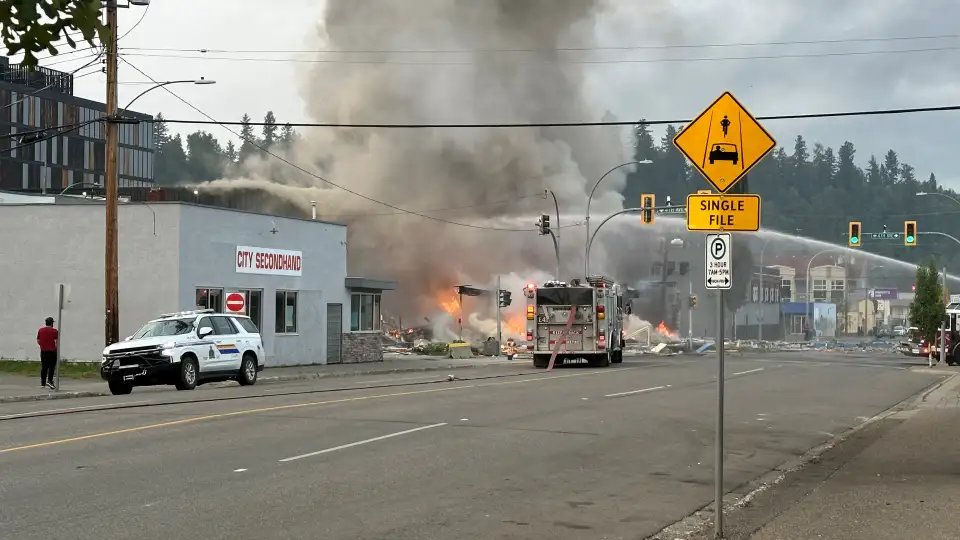
Resiliency in the Face of Disasters
Mary James sat down with him after his talk. The interview has been edited. The entire interview is available as a podcast.
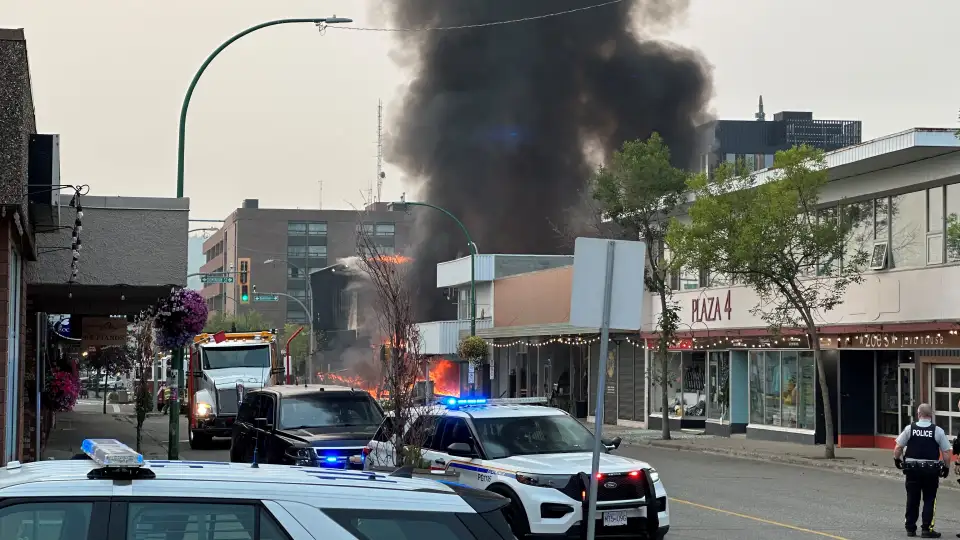
Mary James (MJ): Can you please tell us a little about your work at UNBC?
David Claus (DC): I look after buildings, and I also help plan new buildings. I'm a mechanical engineer by background, but I've been involved in a couple of Passive House certified builds, so I get involved on the design side as well. I'm based out of Prince George, B.C., and I've been there about 14 years.
MJ: You just gave a really interesting talk about a benefit of high-performance buildings that fortunately isn’t needed too often—resilience in the face of disaster. Can you fill us in on what happened to the Wood Innovation Research Lab when the building next door, which did not belong to UNBC, exploded and burst into flames due to a gas leak?
DC: We talk about high-performance buildings, and how they're comfortable to live in and they use less energy and do all this amazing stuff for the planet, but one of the other byproducts is that they're actually more resilient in the face of disasters. Now hopefully all of our buildings don't experience what this building went through, but the way that the high-performance building reacted to that made it easier for us to put everything back together and get it operational again.
As a little bit of background, it was essentially one wall that really faced the brunt of the fire, although there was also water damage that occurred as a result of fighting the fire. The building is basically a square, viewed in plan. It's three stories tall in overall height, because of the kind of structural research that we do inside the building, and it's mass timber. It has large glulam posts and columns that hold it all up.
When the building next door exploded, there was a shockwave that came through, and it caused the whole building to shake. In fact, it flexed over and then sprang back, and that's really a function of the mass timber construction. If that had been a concrete building or a cinder block building, it would've cracked and not come back.
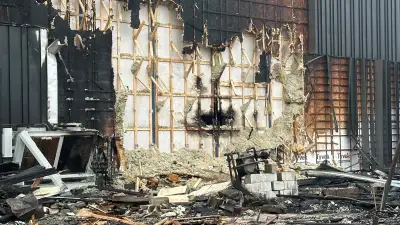
So, there’s the mass timber frame for the structure, and then as you work your way out, there’s an OSB sheathing layer and then about a 22-inch deep open-frame wood truss. Those trusses are filled with mineral fiber insulation, and then there’s another layer of OSB, a Tyvek rain screen, and metal cladding.
The metal cladding protected us from the fire, but eventually that cladding got hot and that caught the Tyvek behind it on fire. So now we have fire burning in our rain screen cavity. Eventually that fire burned through the OSB and started trying to light the trusses on fire. But trusses that are encased in mineral fiber insulation don't really burn that well, which was good.
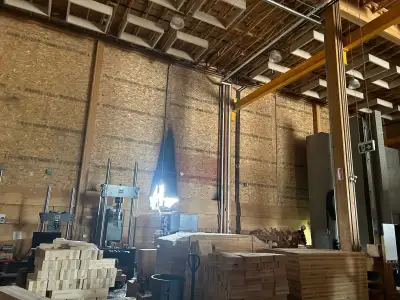
Meanwhile, as this is all happening, the firefighters are trying to put the fire out by spraying water on the outside, but that metal cladding did a really good job of keeping the water out, which meant that the fire could keep burning for some time.
Finally, though, the cladding came off. The fasteners that held it in, the wood that they're embedded into, burned out too much. The fire department also figured out that they could use their water as a jet to blast the cladding off, which was helpful, because then the water could get in and actually start putting the fire out.
There were also projectiles that came from the building next door that damaged the exterior cladding, which allowed the fire to burn right through the wall in an area about the size of a dinner tray. When the fire burned through, we got flames inside the building and then the sprinkler system, the fire suppression system inside the building, did its job.
The one sprinkler opened up, dumped a whole bunch of water on that part of the fire, and put it out pretty much immediately, which was good. We didn't have a lot of fire damage inside the building, but nobody could turn that sprinkler off (because no one was allowed in the building). That sprinkler kept going for hours and dumped several inches of water through the whole building.
The building had to deal with the impact of the explosion, which in some ways functions kind of like an earthquake, the fire from the outside, and the flood from the sprinkler system. So, lots of disasters all at once. Then we spent the next 10 months or so putting the building back.
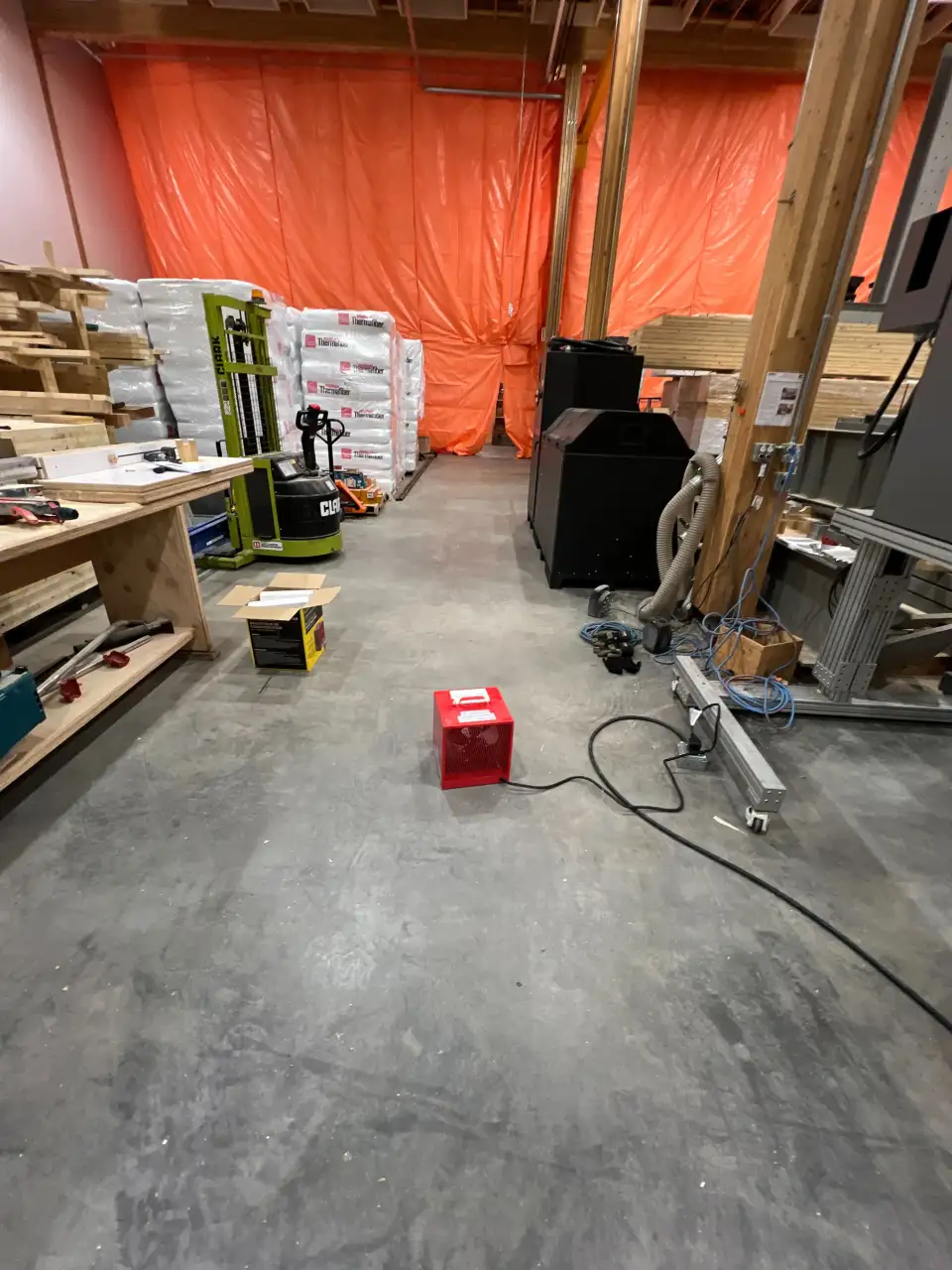
MJ: There is a happy ending to the story.
DC: There is, yes. The building at that point was only about five years old, so we decided to bring back the original team—the architectural team, the contractor that had originally built it, a lot of the same suppliers, some of the same tradespeople even. And, we said, we’ve got to build it exactly the way we built it the first time.
Initially there was some nervousness about how to bring back a Passive House and a high-performance building. Can you even fix it? Of course, you can. We just did it. We took it apart piece by piece and put it back together the way we built it the first time. The building thankfully is up and running now.
The great news was it was a panelized construction, which in some ways simplified the rebuilding process. We had the wood timber frame structure, and then these panels, which had been prefabricated off site, were screwed onto the outside of it.
So, after the fire we were able to take off eight panels that had been damaged and replace them with eight new panels. We joined up all the air barriers, added new insulation, and now the building's back to its original performance or very close to it.
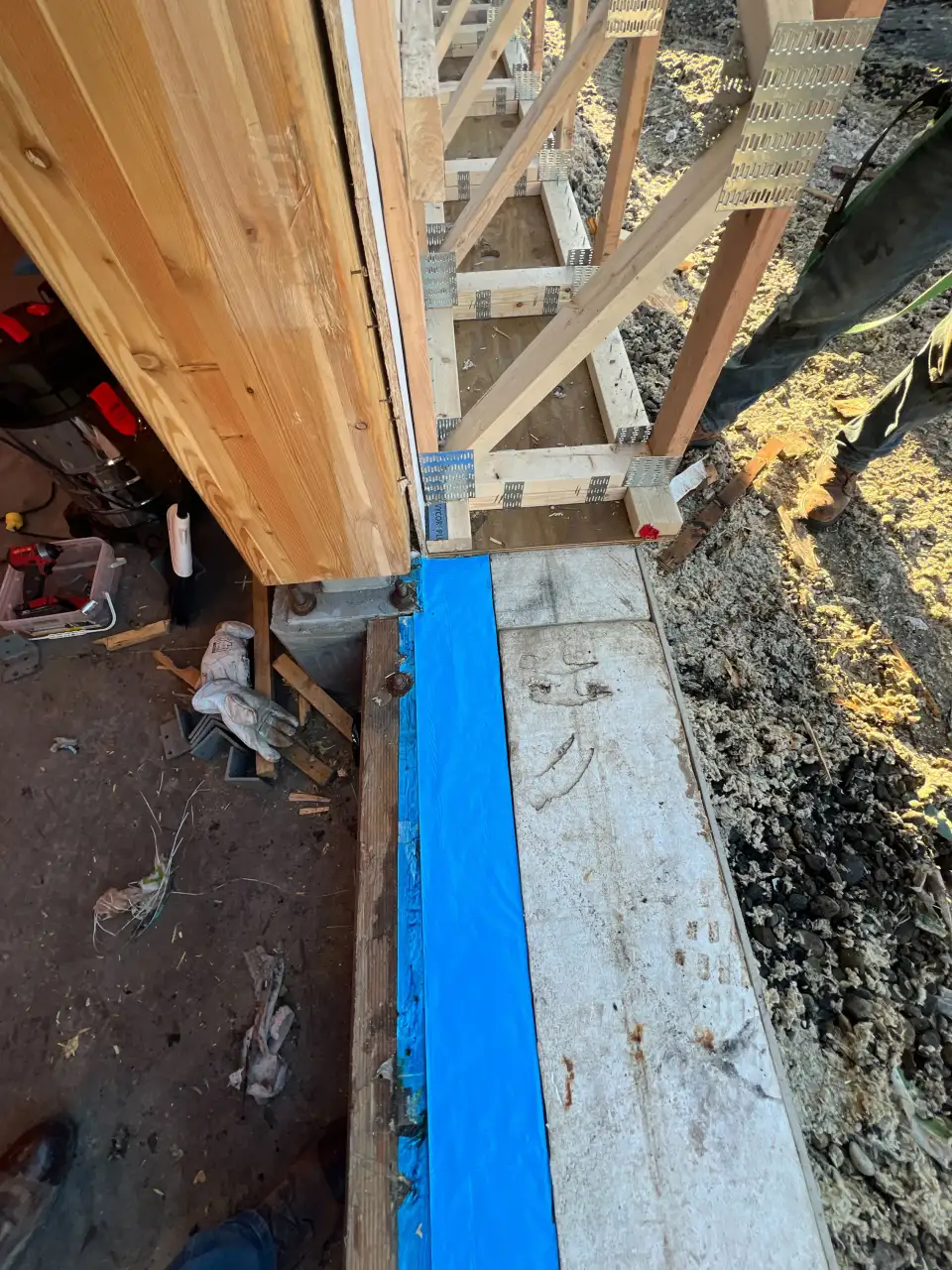
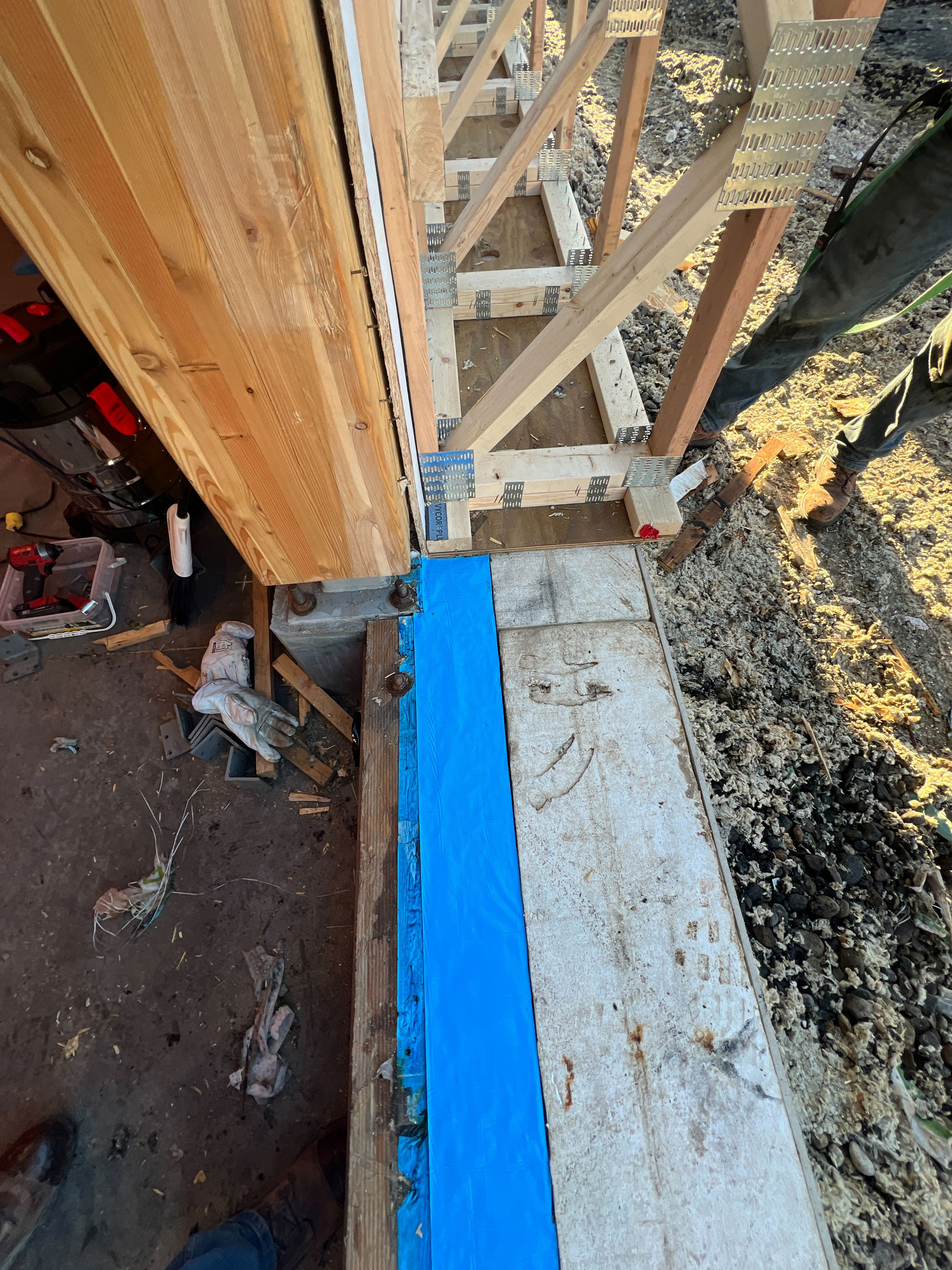
The mass timber column's detail at the foundation/wall transition and cross section of the open web truss that will hold the insulation.
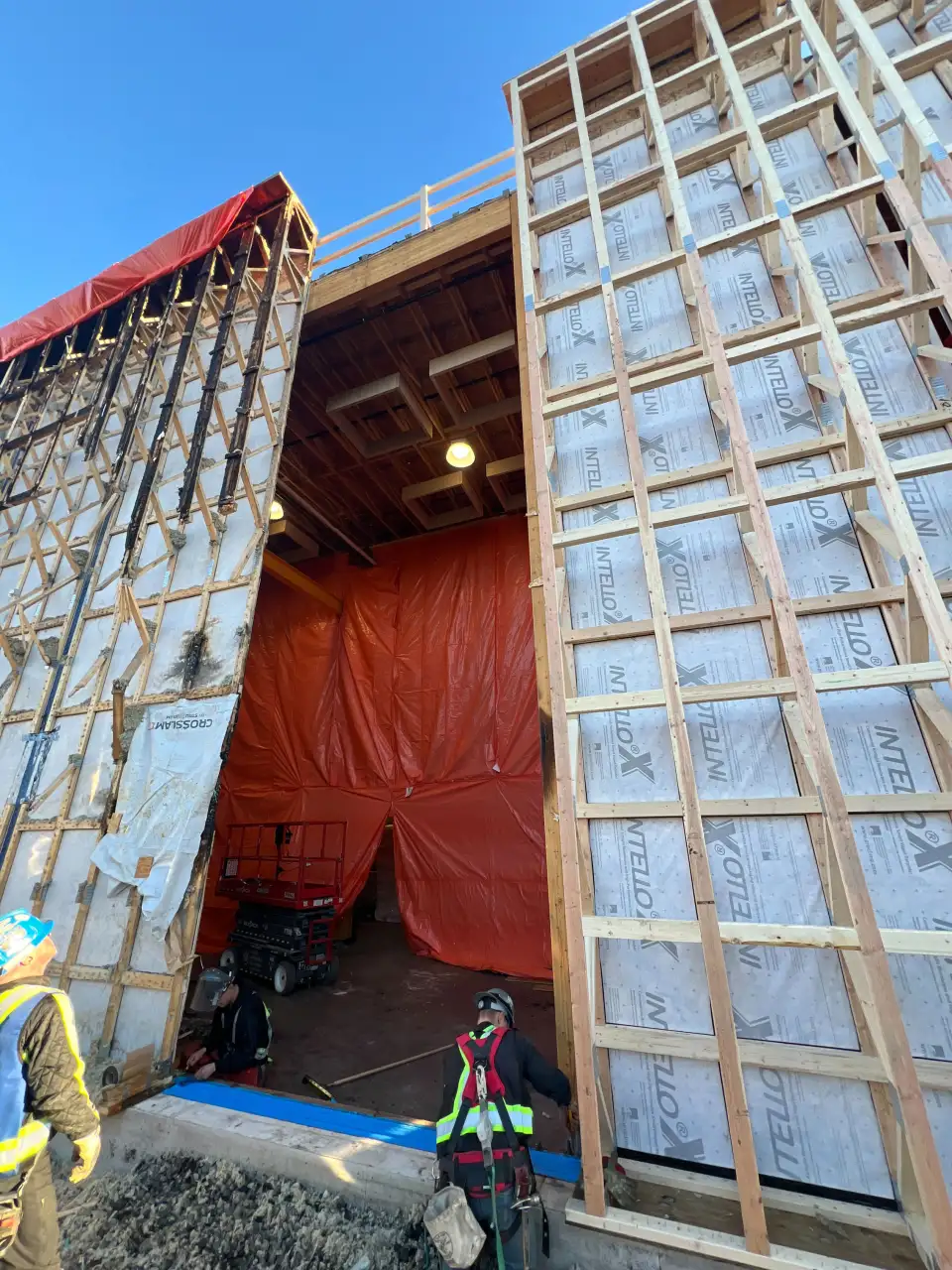
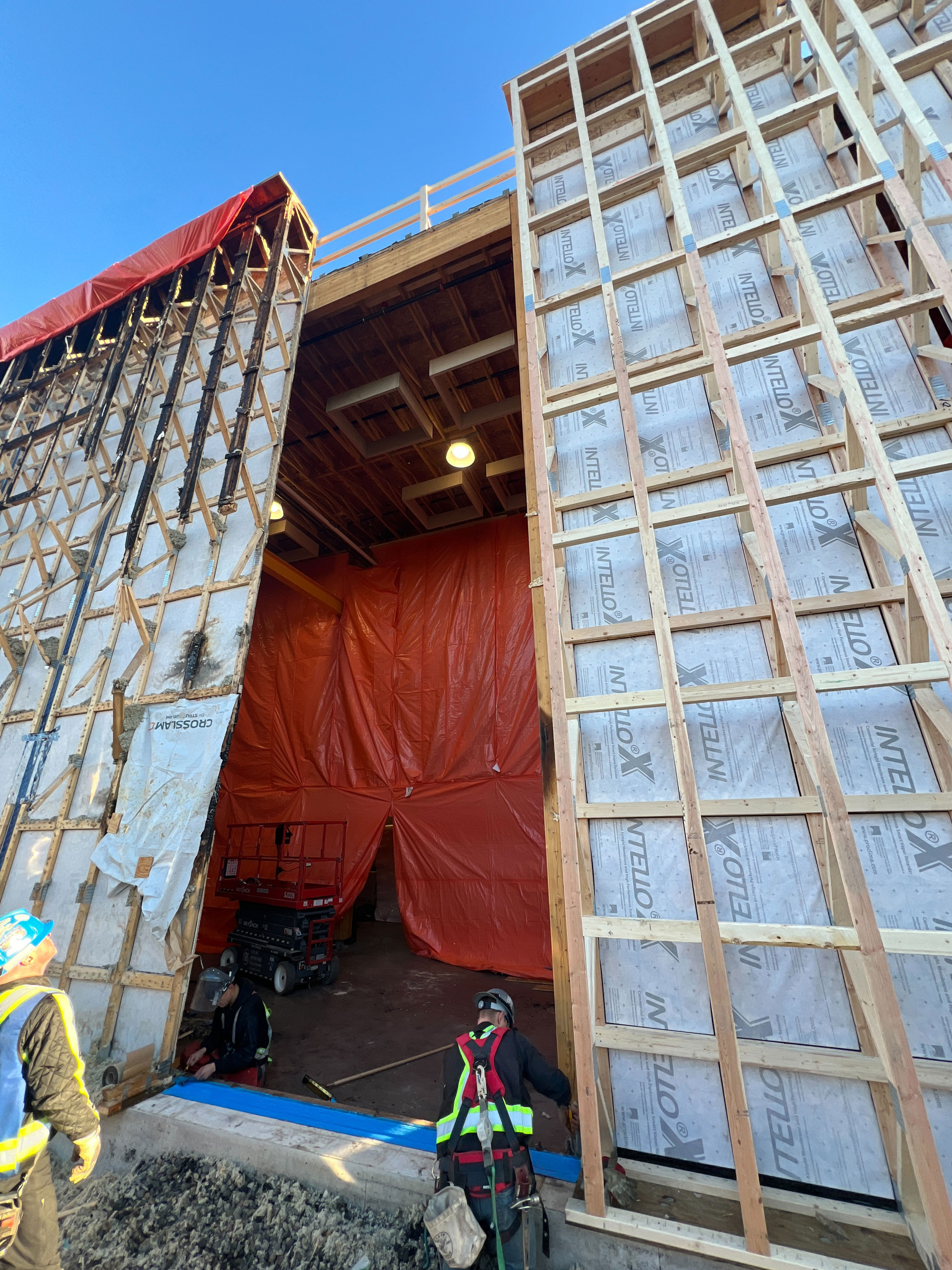
The damaged wall on the left, new panel on the right, and preparation for bringing in another panel to bridge the gap.
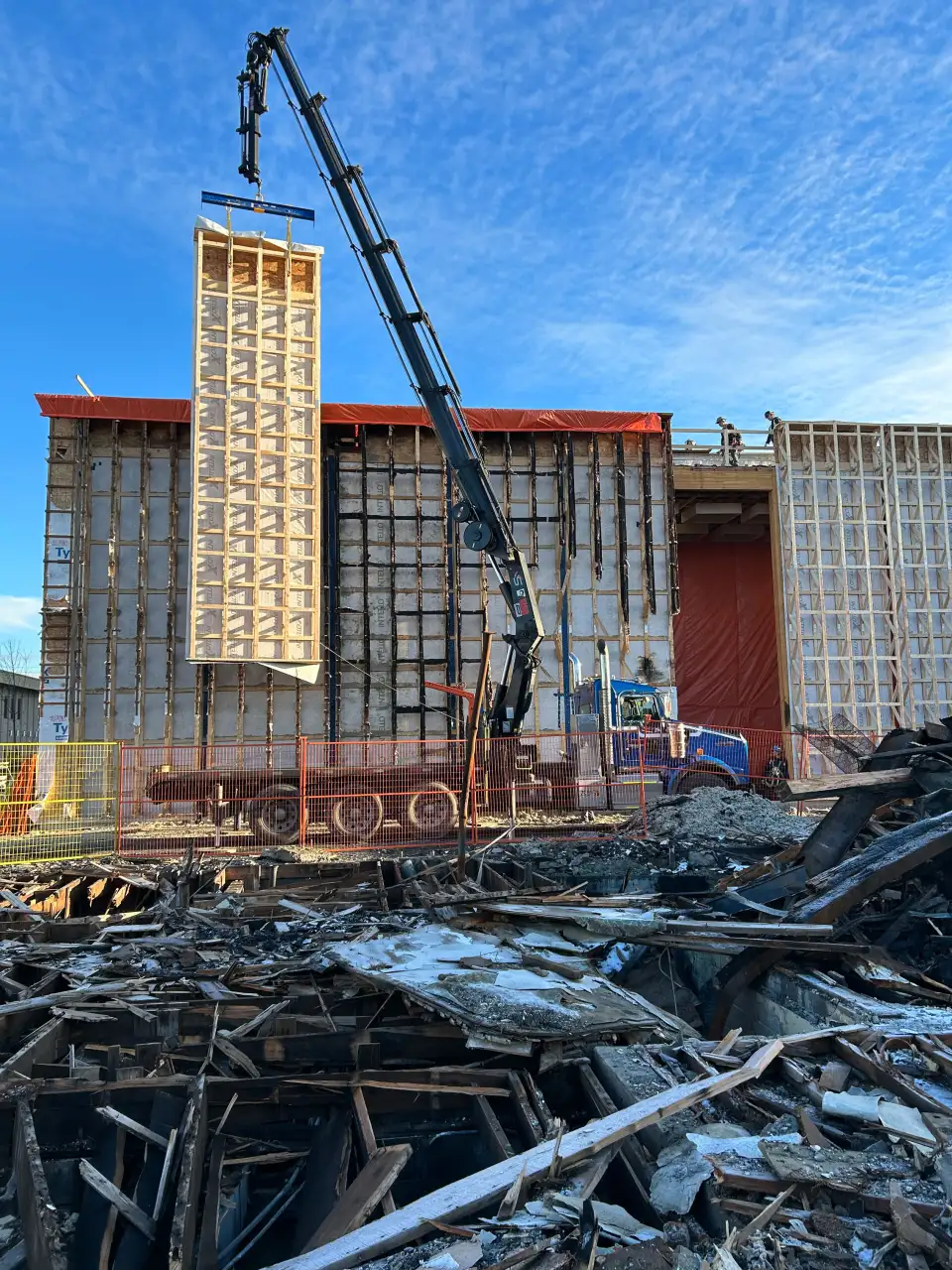
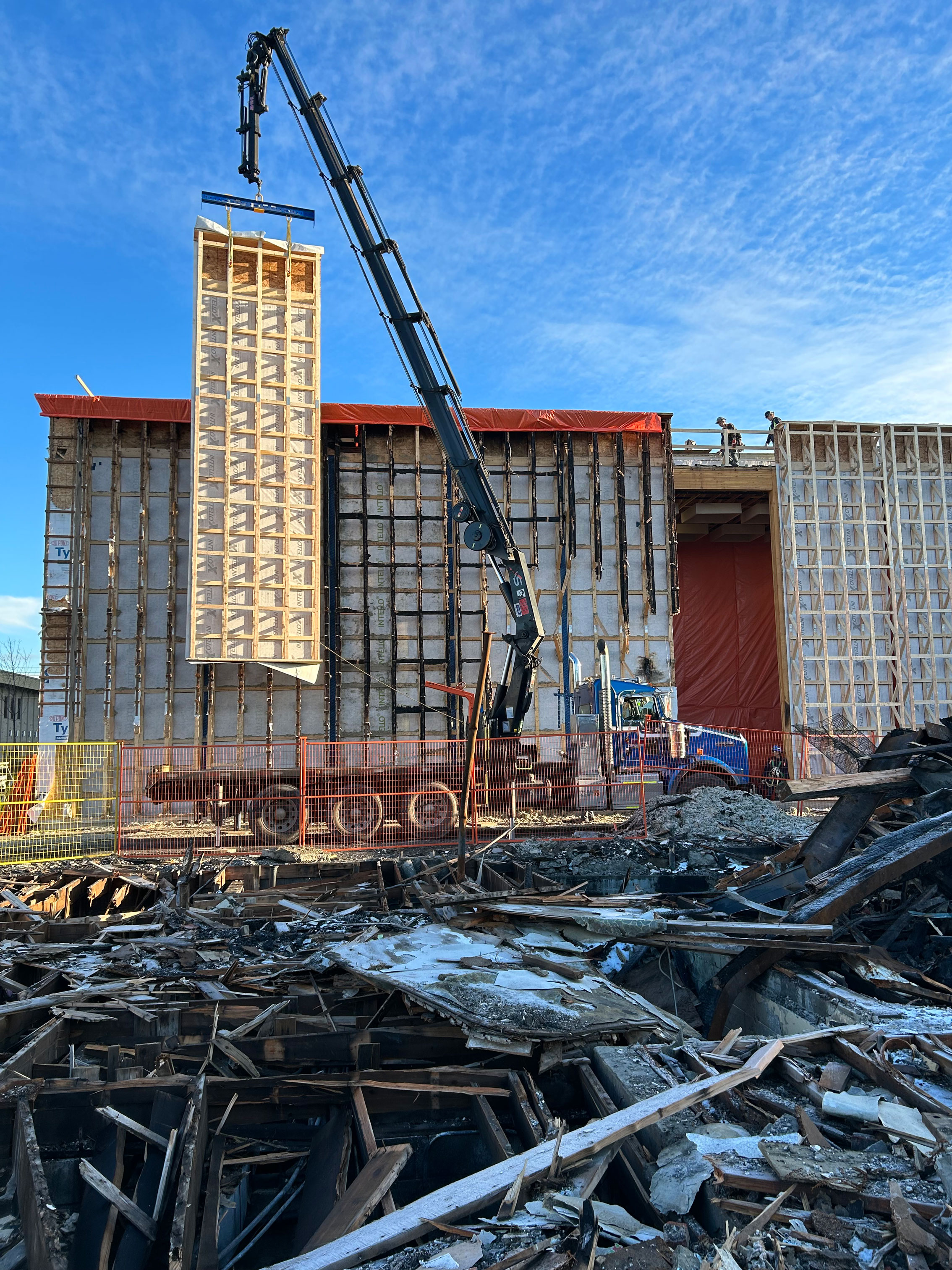
Lifting a new prefabricated wall panel into place. The damaged panels are behind, which were replaced one at a time. Note that the interior air/vapor membrane (Intello) in the damaged trusses is still intact – this is because of the mineral fiber insulation. The debris in the foreground is the building that exploded.
MJ: Your choice of insulation—mineral wool—had some advantages too, yes?
DC: Absolutely. During the original construction, they made the choice to use mineral fiber, and it turned out very well for us. Mineral fiber doesn't burn, so it continued to insulate the building. We didn't even melt the interior air and vapor barrier that was on the inside of that insulation, except for where the fire burned right through. But everywhere else it was fine. So, the mineral fiber kept the building from having too much damage from the heat.
But, firefighting efforts put tons of water into that wall assembly in a couple of different locations, and particularly in one wall that wasn't damaged. The fire department thought that the fire may have gotten that far, so they put a hose into a hole at the top of that wall and dumped water into there for hours.
Months later, when our building envelope specialist was checking over the building, he was quite concerned that we would have water damage, and particularly mold, and structural damage to the wooden members inside that wall, because of all the water that was dumped into it. When he opened it up, we didn't find any of that.
What we found was the wood inside that wall was drier than some of the wood inside the building. The reason for that is that the mineral fiber drains water really, really well. It won't absorb any itself. The wall assembly, as it was designed, has a breathable membrane on the inside and a breathable membrane on the outside, and that whole wall is designed to dry itself out under normal operating conditions. It did that. It did that, exactly. It worked.
MJ: At the end of your talk you mentioned this building was a certified Passive House building, and that the certification process provides a check to make sure we are building it right.
DC: Absolutely. As far as I can, all the buildings that I'm involved in have been certified. It's a check on the overall design that all the components work together the way they're supposed to. If you get a good certifier, it's not a lot of money, but it's money well spent.
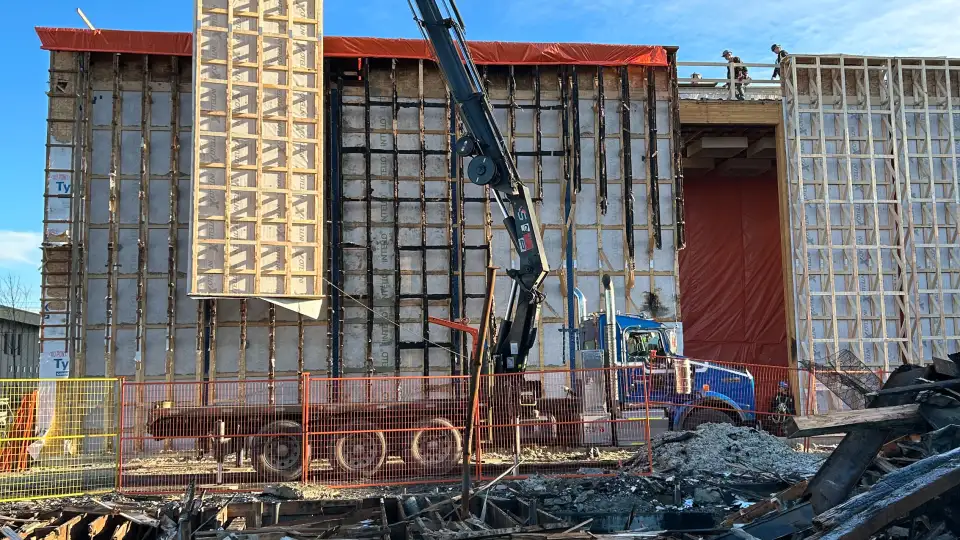
UNBC also produced a video about the reconstruction, and launched it this week. You can view it here: