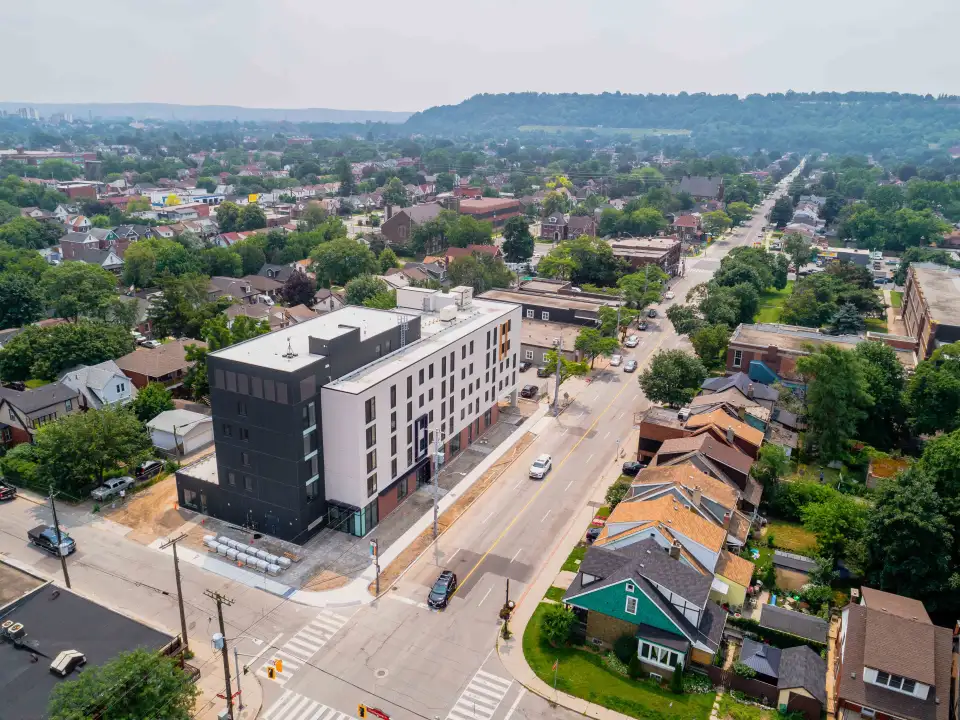
The Putman Family YWCA housing in Hamilton, Ontario opened its doors this fall to its first affordable housing development designed for women and their children. The Putman Family YWCA offers 50 units of permanent affordable passive housing, 15 of which are reserved for women living with a developmental disability. Priority for all units was given to women from marginalized communities, including those who are Indigenous or who have experienced domestic violence or homelessness.
The Putman’s five stories of affordable housing—a mix of one-, two-, and three-bedroom units—sit atop a podium level that houses a community center, offices, reception, bike storage, and a garbage room. On a penthouse level, there are two offices, a laundry room, a mechanical room, and an amenity space. YWCA Hamilton set the Passive House goal for the housing in part so that the residents would be able to focus on their well-being, health, and education rather than coping with poor or substandard living conditions. By offering comfortable and resilient permanent housing, and pairing that with employment support and leadership development services, the YWCA Hamilton hopes to help women get the tools they need to graduate from the system. With the project’s expected reduction in energy usage of more than 80%, it's estimated that the YWCA Hamilton will recoup the incremental cost of Passive House in just two years.

Kearns Mancini Architects (KMAI) was chosen to lead the project’s design. Deborah Byrne, KMAI’s chief operating officer and director of Passive House design, headed up what turned out to be an all-women led design team that included Alice Gibson as project architect; Irene Rivera, an architectural designer; Natalie Krakovsky, architect; and Kelly Fisher, a Passive House consultant who helped develop the certifiable Passive House design. Byrne points out the congruities between the YWCA Hamilton’s objectives and Passive House performance targets: supplying housing that is beyond par and, in fact, is the highest quality housing available. Indeed, for the YWCA Hamilton, social equity concerns were as important as energy efficiency in shaping this project.
With an eye on affordability and performance, the client opted for a concrete structure for the six-story building. At that time, building codes for using wood framing in large buildings were in flux, and, as a low-income housing provider, YWCA Hamilton did not have the time or money to push for alternative compliance pathways. Indeed, KMAI’s design team relied heavily on traditional construction approaches and products—specifying locally manufactured materials such as the ERVs and an innovative wall assembly—to guarantee the project’s ultimately successful conclusion. Byrne adds, “Rick Sealey, KMAI principal and the contract administrator for the project, made the design come to life on site, ensuring the building effectively met the design standard.”
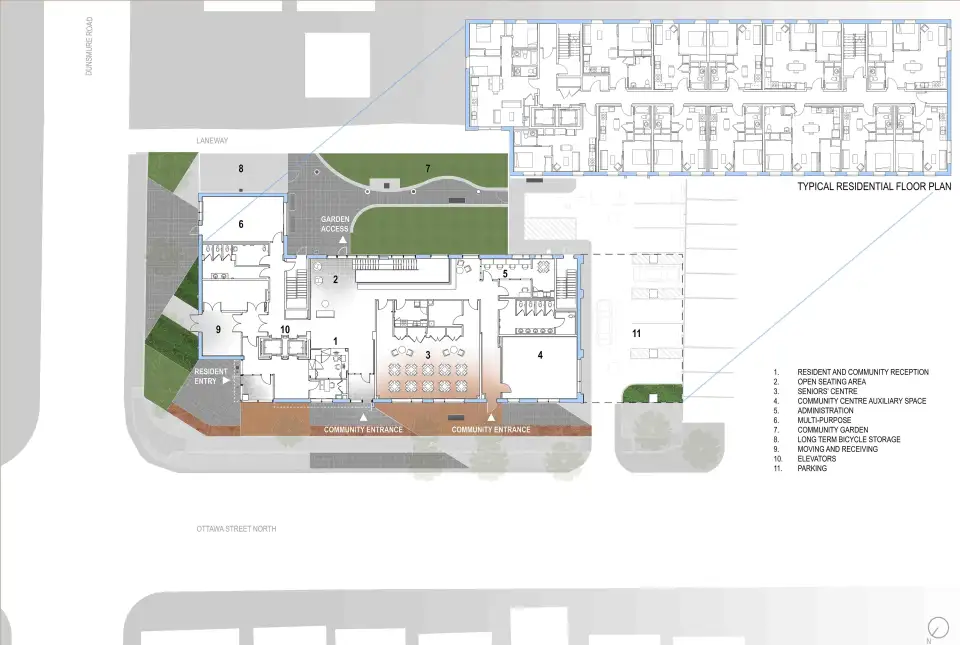
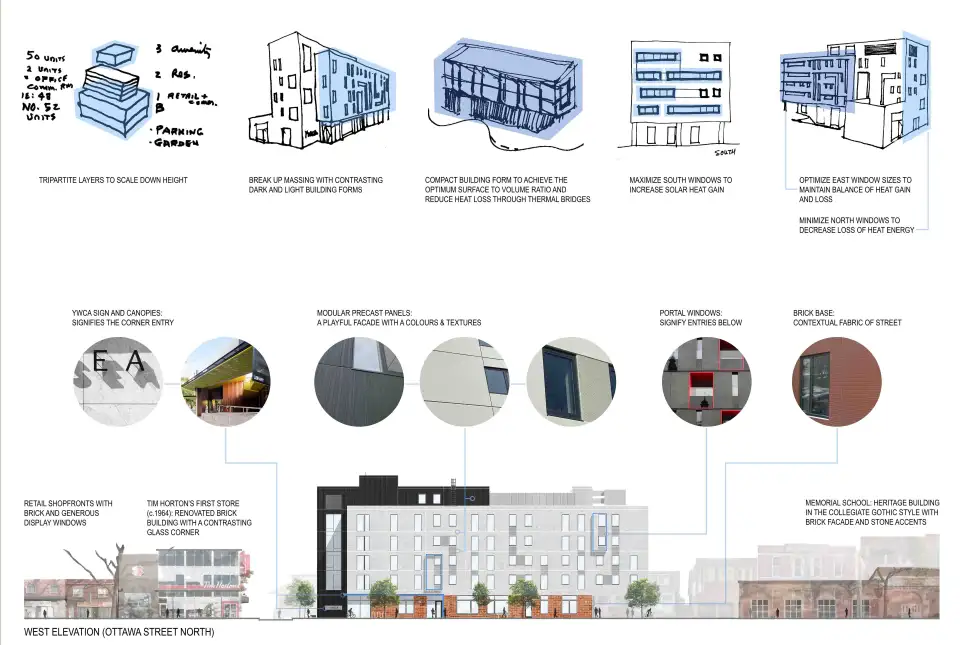
To economically meet the building’s insulation and airtightness specifications, KMAI worked with a local manufacturer, Hamilton-based Coreslab Structures, to jointly develop an entirely new wall assembly consisting of a precast concrete sandwich panel. Kooltherm, the phenolic insulation included in the sandwich board, is made with a blowing agent that has a low global warming potential (GWP). While these materials are not ideal from an embodied carbon perspective, a precast system reduces the carbon emissions associated with travel to and from the site and on site during the lengthy construction process. “Without the precast system, the construction would have been far more labor, equipment, and material intensive—think massive concrete pumps and concrete trucks idling on site all day every day for months and months,” says Byrne, adding that the building’s embodied carbon is lower than it would have been with a traditional cast-in-place system.
Coreslab Structures worked closely with the design team to ensure its product would meet the high-performance envelope specifications. The precast system was a big advantage in terms of meeting the project’s airtightness target, says Rivera, and still during the design phase the team encountered the usual difficulties in detailing the junctions. “The junctions between the precast envelope and other structural elements in the building, like the basement and foundation wall, proved to be particularly challenging,” she notes. “We had to maintain the continuous insulation and airtight layer from the precast sandwich panels to the cast-in-place concrete basement wall, without compromising the structural stability of the building. The solution was to have a piece of expensive structural insulation that connected the two assemblies. The junction was taped from the inside, above and below the ground floor slab, to maintain the envelope’s airtightness.”
Meeting PHI’s primary energy target was another challenge, Rivera notes. “A single mother with five kids needs a bathtub from a safety point of view,” Rivera points out, so the hot water needs for the building—especially the peak demand—were relatively large, making a gas-fired boiler the only reasonable equipment at the time the building was designed, as well as the only practical means of staying under the primary energy limit. The YWCA Hamilton, because it is a multifamily building with high occupancy, met the criteria for using PHI’s Primary Energy Relaxation tool, which is why this project’s primary energy exceeds the typical annual target of 120 kWh/m2.
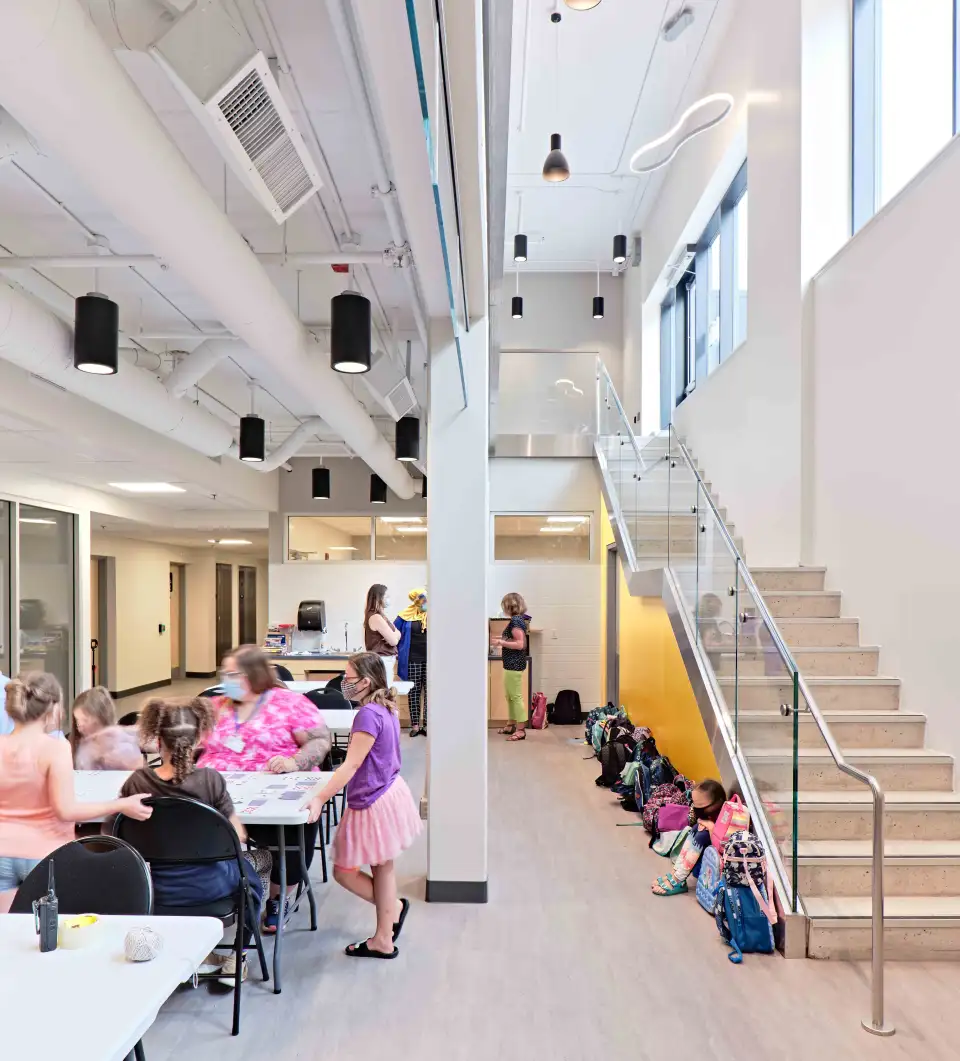
Integral Group was tasked with the mechanical and electrical engineering for the project. Hamilton has a cool temperate climate with hot summers, and the team decided to use centralized air source heat pump (ASHP) fan coil units and direct ventilation from two locally manufactured ERV units to address ventilation and conditioning needs. Assuming the building is occupied as designed, the team expects the fan coil to only be needed during more extreme winter and summer conditions.
Despite the project’s challenges, the almost all-woman team achieved Passive House certifiable status for the entire building; it is awaiting certification from PHI. Design had begun in March of 2018, with permits issued by July 2018. Construction of the precast system had started in March 2020, and then been slowed by Covid. Still, by September 2021 the first cohort of women-led families started moving into their new homes at the Putman Family YWCA. All 50 residences are expected to be fully occupied by January 2022. The building’s Passive House features—its comfort, climate resiliency, low energy costs—will aid in fostering social equality for the occupants and giving them the needed security to move forward with their lives.
Heat demand |
Heat load |
Cool demand |
Cool load |
PER |
PE |
---|---|---|---|---|---|
10.7 kW/m2 |
9.8 kW/m2 |
7.6 kW/m2 |
9.4 w/m2 |
93.1 kW/m2 |
135.6 kW/m2 |