Edie Dillman is CEO and co-founder of B.Public Prefab – a component-based high-performance building company that prioritizes energy reduction and housing creation. As co-founder of a decidedly disruptive company, she is committed to systems change and the rapid adoption of solutions for the natural and the built environment. Jonah Stanford founded the design firm NEEDBASED Inc and is CTO and Co-founder of B.PUBLIC Prefab. Jonah joined the first generation of Passivhaus Consultants trained in North America in 2009. Jonah's work typically targets site-net-zero-energy and incorporates his enthusiasm for building science and material science applications. Charlotte Lagarde, is COO & Co-founder of B.Public. After 25 years in advocacy work, Charlotte brings her passion for systems change to B.PUBLIC to address climate and housing issues and returns to her first love of architecture and the built environment. Prior to B.Public, as the executive director of the Swell Foundation, a non-profit corporation she founded in 1998, she produced over 20 films and raised millions of dollars. JD Scott is Lead Architect at B.Public and an emerging leader with nearly a decade of experience in the movement to tackle climate change and the affordable housing crisis. JD has also worked in architectural practice at multiple scales, from single-family homes to complex multi-family developments.
View the full transcript for the video here:
Edie:
Lovely intro. Great to be here. We're really excited to share a little bit about what we're doing and really fun to use a live case study tonight, to walk you through what B.Public has developed and how we approach Passive House, as well as Prefab. We're going to walk through, I'm going to intro first, JD Scott who's the lead architect. Charlotte Lagarde was actually the project manager on this, and she's going to jump in at the Q and A as well. And Jonah is both CTO and architect. I think some of you know Jonah, he's wearing a really excellent B.Public t-shirt. Here quickly going to make my B.Public t-shirt.
JD:
It's actually all I wear. I'm just so appreciative of having a uniform.
Edie:
There we go. So we're just really delighted to share this and excited for the Q and A. It's always great to have a conversation about this, and we'd love to jump in. So JD, you can take it away and share screen.
JD:
Great.
Edie:
Looks great.
JD:
Well, everyone can see. All right. I'll just pause it here for a second. We have this lovely Gif that scrolls through, so we can all get mesmerized by this for a second. Thanks for the introduction, Edie. Just to give you some context on the project and the background. This is a rebuild from the CZU fire, which was a major wildfire event back in 2020 in Northern California and Santa Cruz county was really the hardest hit in that event losing nearly a thousand single family homes in the fire.
JD:
And so our client had lost their home in the event and were really excited to return and rebuild, but this was a really traumatic event for this community. And that's something that we all experienced when we were on the ground there in September. Santa Cruz county has really rigorous pre-clearance requirements for these rebuilds. And so on the front end, our client really had to do a lot of work to even be eligible to do this. This is an image of the site, in the aftermath of the fire. So you'll notice some debris has been cleared and they've scraped and started excavation process. And you can see the erosion controls in place on this project. [crosstalk 00:03:13]
JD:
Jonah's going to give kind of an overview of the B.Public's system and it's attributes, too.
Jonah:
Thanks, JD. And JDs been so much fun to work with, and just sort a note quickly. So this project, these clients approached B.Public in February and we installed, about a month and a half ago. And so just JD's response role for onboarding those clients, finalizing the design process and then getting those CDs with offsite construction, through permitting so forth. Thanks, total shoutout his abilities there. So, it was a really good case study for the B.Public components, because it really had a little of everything. It's a little bit of two stories. It's a lot of seismic, it's a little bit of insulated slab. And so it really did test some of the resiliency within the design of the offsite standardized components in a lot of ways. And then also just being in a C3 coastal climate range also.
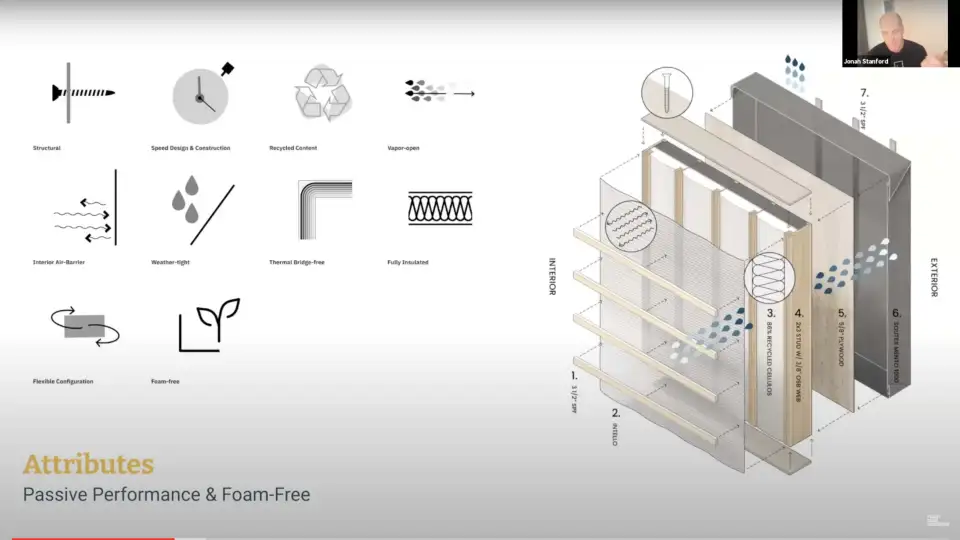
Jonah:
So, all the components are designed with best practices that we've learned over the last decade around Passive House, right? Insulate as far as you can go until there's a reduced return to it, but really your greatest long term gains come from good building science of eliminating your thermal bridges and in ensuring your air tightness is going to be on target and so forth. And so, the B.Public components, I think maybe most people are familiar with them here, so they are primarily carbon sequestering. They are thermally bridge free, even if they're all their connections. And so it was really great to see JD take on this project with the components and see how they did from a structural and a seismic perspective. Cause really our focus has been, see if we can take those best practices in generate something that was really resilient in terms of its climate, its seismic or structural loads that are always defined per project and see if it would work within these really diverse situations. So it was a really great project in that way.
Jonah:
And I'll just give it back to JD for process there. And we'll have lots of time afterwards for questions to get into more technical, if people want.
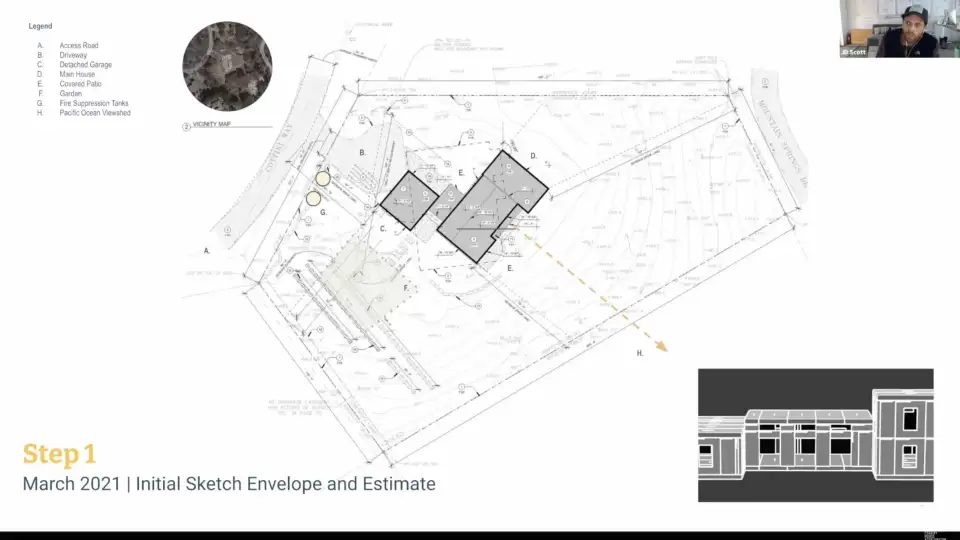
JD:
Absolutely. So yeah, moving kind of more into the design process. B.Public, the way we structure our project phases is we start with a site evaluation, site sketch phase, and we also provide a preliminary 3D model at that phase using the components that Jonah just outlined. And it's really just to give our clients that first vision of what could be done on a site. And so in this case, we're showing that dash line where the original building was and then locating the new house on the site. Particularly important now for these rebuild projects is having a pretty beefy fire suppression system. So you'll notice the tanks that we've located on the site plan. And we also look at other site elements they might want to incorporate like a garden or things like that.
JD:
And this project was oriented for a PV array, but it's also on this really wonderful access with a view towards the Pacific Ocean that you can see on clear days when you're out there. And the second half of this phase is, like I said, is generating this component model. And this is all using our standard panel components, which we have in SketchUp. They're available for download for free. So anyone on this call could download these and experiment with, but it's a really intuitive way to design and to create a thermal envelope really quickly. This newest generation of SketchUp components are true to life. They have all the information that our shop drawings would have for the panels.
JD:
So you can see all the structural framing and the interior and exterior furring strips are on these. So it gives the client a ton of detailed information up front that in a normal architectural process, you wouldn't encounter this until DD, sometimes later. And accompanying this, we give the client a detailed panel estimate. And so this gives them options up front. If they want to look into financing or talk with a builder they have a lot of leverage coming out of this first phase, just from this panel model. Jonah, I don't know if you had anything to add on this.
Jonah:
No, I think we can probably go onto the other site, but during that first site plan design, and then the model building happens really side by side so that the client has a good estimate for that total thermal envelope construction cost. And one thing that JD and I pay attention to is that once you've got your performance nailed down and the cost of it, then it's around 35% of your total construction costs where the remainder is really a tool in terms of finishes and amenities that a project can undulate its budget too. So it's really nice to have that level of cost estimate for the thermal envelope at this point.
JD:
And kind of moving into our next phase, we get more into the kind of architectural expression of the project. In this case, we're giving the client different fire resistant, finish options. That being said, we really try to leave these decisions to the client and builder because our primary focus is really on the system performance and those critical items like the penalized assembly, windows and doors, the ventilation system, ERV system. And so in our builder set construction documents, we developed those critical items in an extremely rigorous detailed way. But we let the fun decision making fall onto the client and builder. So again, that opens up some more flexibility for our clients.
Jonah:
Yeah. This is all done on an iPad.
JD:
Yeah.
Jonah:
So this combination of the aesthetic being defined on an iPad and traced, really light, and then the other, the 3D modeling, before it goes to a BIM or construction documents. So you have really accurate Passive House detailing, building science, thermally bridge understanding, and a fun sketch of what it's going to look like on the outside. And it's kind of cool that it really works from both sides. And then the next step is where that BIM comes together for coordination.
JD:
Yeah. Which again is flipped from the normal architectural process where these types of drawings would be extremely developed. And then all the system stuff would be complete question mark. And so then we move into developing the construction set. One of the ways that we're really streamlining this is by developing a standard library of our details. So our panel connection details, and also site built details. And these are kind of vetted ahead of time. And we're able to run them by the engineer of record and develop them on a project by project basis. And at the same time, we're thinking ahead towards the actual panel install. So this image on the right, it was included in the construction documents set as an aid to our install crew, when they were on the ground installing the project.
JD:
The other main thing we're tackling with our construction sets is, we're hopeful as a company that a Prefab is going to become the norm in terms of construction. And with that it becomes really important to understand and delineate scope of work. And so at the beginning of all of our construction sets, now we have this project navigation page, that drawing on the right. That kind of establishes what the different scopes are, and really serves as a communication tool to the builder indicating what needs to be done before the panels arrive, what scope B.Public is providing, and then everything that would come after that. And I think it helps more and more as we're partnering with other architects where we're not the architect of record. It helps communicate to them how that scope is divided up and what those responsibilities are.
Jonah:
Yeah. And for those of you that are lucky enough to work on full modular project or multiple family projects, then this becomes less critical in a way, because if the coordination is happening all within house. But where B.Public is really working on trying to serve smaller projects or more rural projects that are not having the level of access to full modular and a larger of a scale project where the whole project is being pre-fabricated. So, working on ways how we can clearly integrate with local architects and builders in that way and serve smaller projects just as efficiently as the larger or multiple family or larger projects or utilizing offsite construction.
JD:
Yeah. And once the building permit is issued, we can start with power,
Jonah:
Maybe a little bit before the permit.
JD:
Right, right. Ideally we could start with panel fabrication. So these are some images of the panels being constructed in this shot.
Jonah:
JD, I do want to jump in here really quickly.
JD:
Sure, sure.
Jonah:
With that, so we did actually components were being manufactured. And at the last minute through permitting, one of the consultants for the plan reviewers was like, no, you need independent testing on everything. And so, just talking about the process it's one thing that we really learned is it's very important for us to engage with that jurisdiction very early on and everybody to be on board. And once they understood it, then it was totally fine and we were good to go, but there was some funny moments.
JD:
Yeah, that's a good point. But yeah, these are just images from the shop. I think what's great about the system is that it's constructed very intuitively, it uses pretty standard tools that all of us are familiar with. So it's not reliant on automation or anything like that. And yeah. And it's built obviously in a really controlled environment. So this is what it looks like as the panels are being fabricated and before they're trucked out to the job site. I don't know if you had anything to add on this one, Jonah or Edie or Charlotte.
Jonah:
No, I think Deann collective carpentry would probably laugh. I'd say it was in a super controlled environment.
JD:
Yeah. Once the panels are complete, they're brought to the job site, these are just some images from the first couple days of this install. I think in total, the panel install was less than a week. And then plus some extra days for air ceiling and the taping of seams and things like that. And this video shows some of that. I think another Hallmark of the system is that the install crew is pretty small. I think this was done with a crew of four or five and a crane and that's it. And yeah, I think for all of us, it was really exciting to see the system tested and implemented this way, and this quickly. I don't know if you all had other thoughts on the install.
Jonah:
No. We might see another picture of it, but one of the hallmarks of the B.Public assemblies, the organization or sequencing of loading and unloading the panels. And I actually wasn't there at the very beginning of this project, but came in after the walls were all set and so forth, but just being able to have all your components stacked in one place, and all of your roofs that are identical and they're not 100% project specific, it can just really ease this portion for mobilization and offloading.
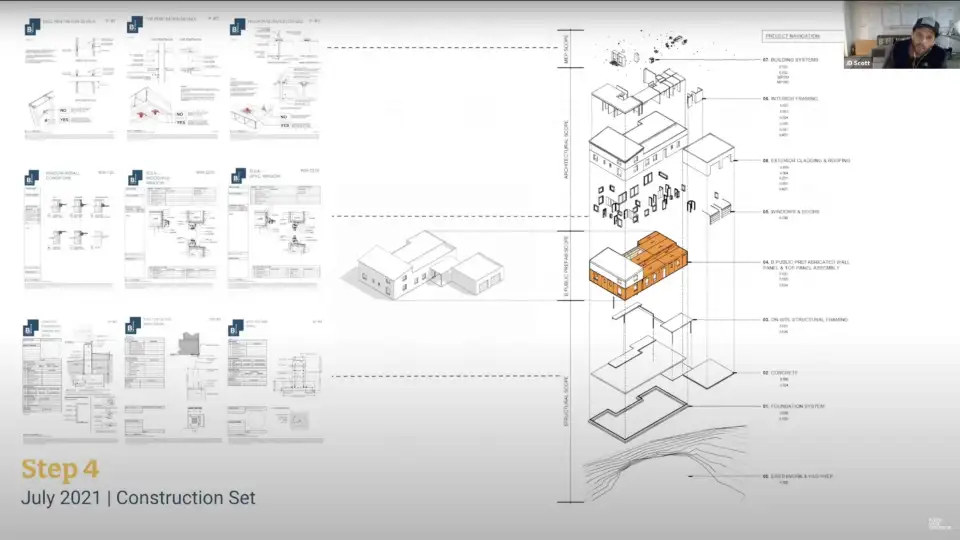
JD:
Yeah. Just some images of the interior. I think we definitely used the installs as an opportunity for community building. So we really encouraged during this project for neighbors and just passers-by to hang out on the job site. And there was just a lot of excitement I think, around someone rebuilding, first of all, but also someone really rebuilding with such an innovative system. And I think the speed of it really just inspired people in that neighborhood. And we also use it for educational purposes. And so this is a image of a larger group of architects, designers on site, who toured the project. I can't remember the total number of people we had who came out to see it, but it's a great opportunity for people to see the system, to see the different connections and even for clients and people who aren't as interested in the technical side, they get to see really early on, I think how the spaces are shaping up and how it feels to be in some of the spaces. So, yeah. Each build is a really good opportunity for that.
Jonah:
Yeah. I think there was probably at least 150 people through this in the four days that I was there. That picture in the lower left is, like you saw in the sketch up video of the components being sort of dragged in place. And then it's really onsite that you're actually able to see those same components with the install crew craning them over and placing them. And it's amazingly similar to the sketch up drag and drop. But you can actually get a really physical understanding of how to create the rough openings using the different filler panels. And it just gives a lot more intuitive understanding of it when designers are then doing it from a digital side or a design side.
JD:
Yeah. And I think just another quick video from one of the open houses we had on the project. But yeah, it just generated. I feel like I've talked to dozens of people when I was out there and it generated a lot of interest and excitement. And I think that's it. Feel free if other B.Public folks to chime in if we need to backtrack or if you wanted to add to that. But I think that's it.