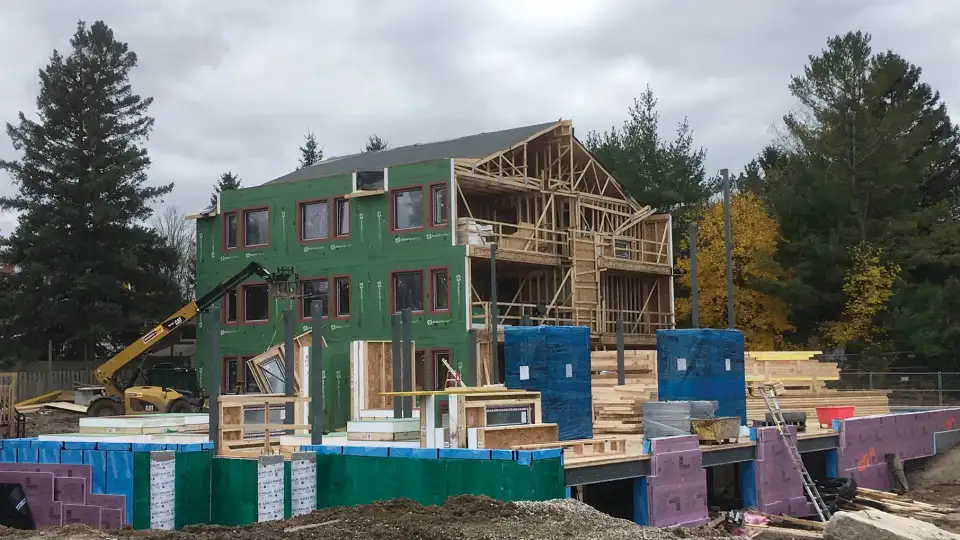
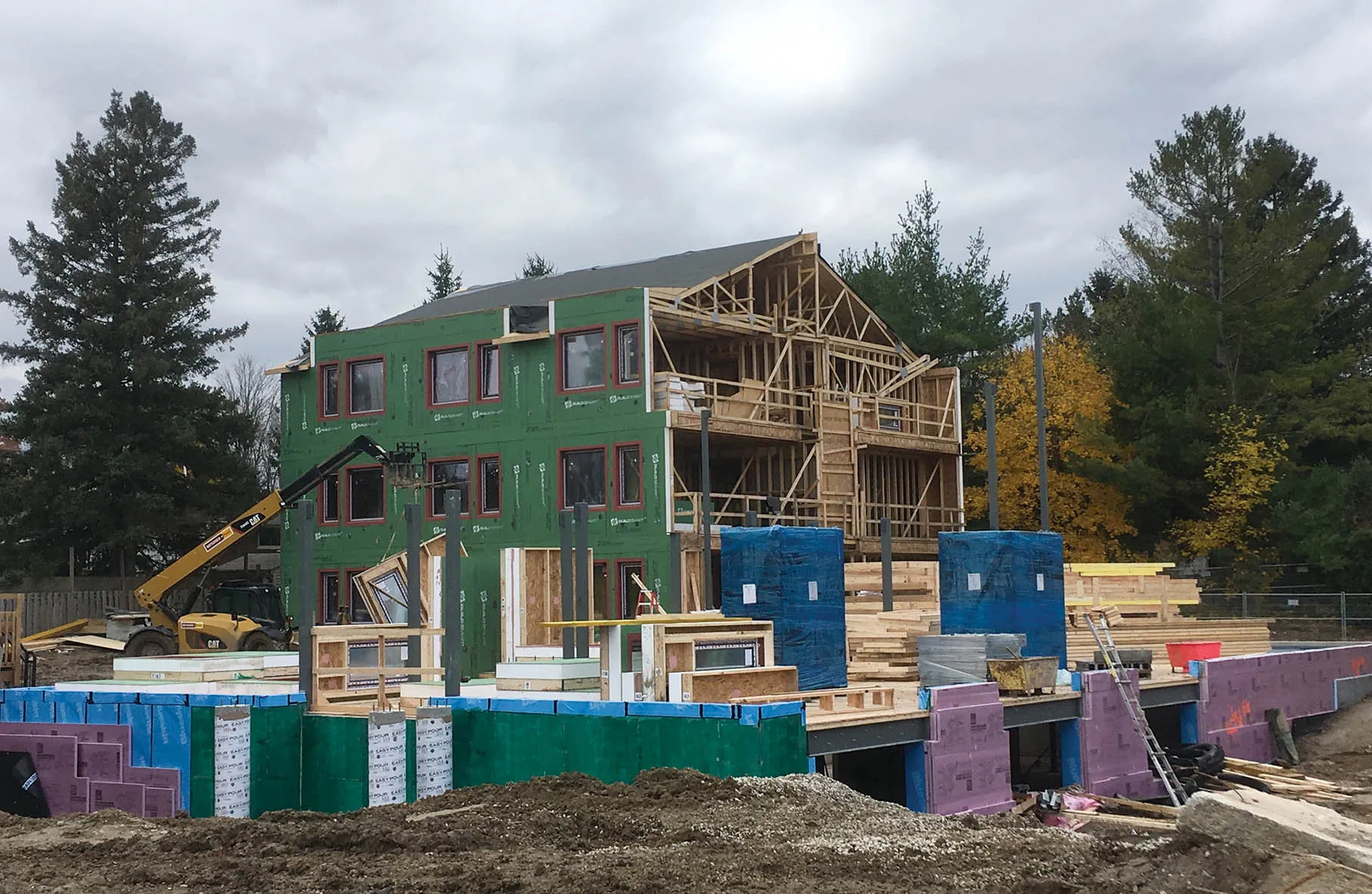
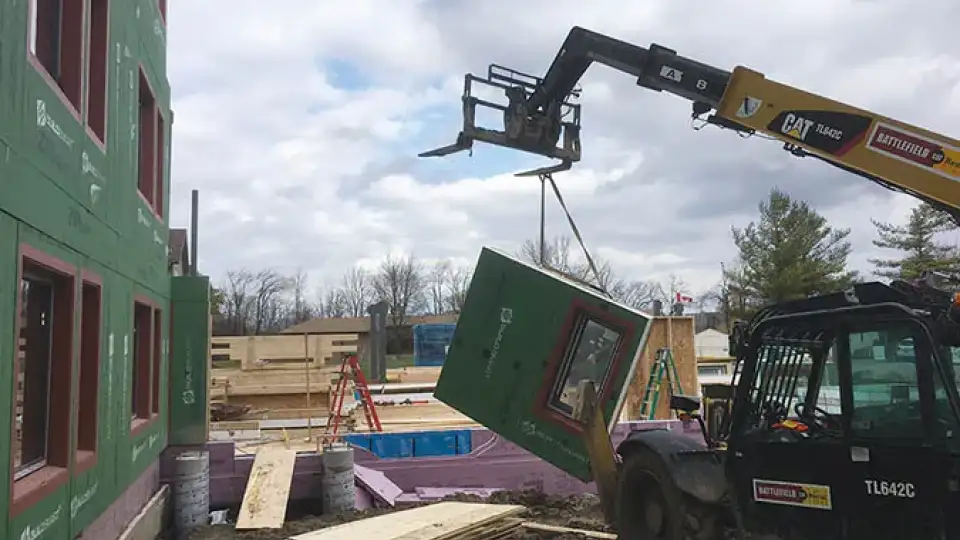
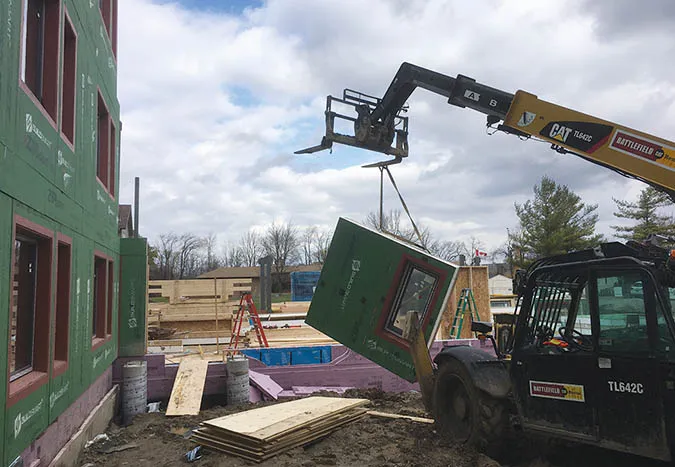
Metrics
Heating demand |
Cooling and dehumidification demand |
Primary energy |
Air leakage |
14 kWh/m²a |
1 kWh/m²a |
120 kWh/m²a |
0.6 ACH₅₀ (design) |
Providing people with safe, comfortable, and affordable housing is the primary mission of Indwell, a Christian charity that has committed to incorporating Passive House principles into its developments. As the owner of an outdated group home in Woodstock, Indwell seized the opportunity to redevelop the site, creating a new 2,434-m2 housing complex with 34 apartments and a community hub that will be shared with other nearby tenants. All tenants will have access to a meal plan and other supports to maximize their ability to remain in stable housing.
Common spaces in the complex include a large community kitchen, a dining area, a laundry room, a lounge, meeting rooms, storage space, and offices for Indwell staff. Each apartment has a bedroom, washroom, kitchenette, and living area in an efficiently designed, roughly 34-m2 space. Most units will be single occupancy.
The design team, led by Invizij Architects, opted for a prefabricated wall system built off-site in Kansas that would deliver the required performance and shorten construction time. The walls are designed to achieve an effective R-value of 49, including 14 cm of mineral wool batts between the studs with an additional 19 cm of EPS on the exterior. Triple-glazed PHI-certified windows were preinstalled and air sealed off-site.
“We have one of the most challenging climates, because it is heating dominated but we also have stringent cooling requirements,” says Greg Leskien of Zon Engineering, who consulted on the project. Low-solar-heat-gain glazing units will help to balance these demands. Operable windows with insect screens that will be added on-site will aid in reducing the cooling demand when the weather is favourable. Large evergreen trees on the south and west sides of the complex should help reduce solar gains in summer.
Continuous ventilation is being supplied to each apartment by a centralized system composed of three commercial-size ERVs. A fourth ERV will bring fresh air to the kitchen and common areas.
Heating and cooling will be provided by a variable refrigerant flow (VRF) heat pump system. This system’s condenser units are housed in an unconditioned mechanical room located in the basement, outside the thermal envelope, so that these units will extract or reject heat from or to the outside air that moves through this room when conditions are favourable. When outdoor temperatures drop, and the VRF systems lose efficiency and capacity, outdoor dampers to the room close, and heat is extracted from the ground through the slab and walls. If the temperature in the room continues to drop, additional heat is added by a natural-gas furnace.
To allow for the use of just one wall-mounted VRF fan coil to deliver the conditioned air in each unit, the architectural team redesigned the apartments’ bedroom walls and doors so that they stop short of the ceiling and air can circulate freely. Attractive sliding barn-style doors screen the bedroom from the rest of the unit.
Great efforts were made to reduce the energy used by appliances and other equipment. The common kitchen will have highly efficient residential-style electric ranges, and a commercial-grade dishwasher, freezers, and walk-in coolers. Direct-vent range hoods are interlocked with the kitchen’s ERV to increase the supply airflow to automatically deliver balanced makeup air whenever an exhaust hood is operating. An efficient hybrid elevator and lift was selected to further reduce energy use.
A 58-kWac PV system will help offset most of the electricity used annually.