In this special installment of the Global Passive House Showcase, Passive House Accelerator founder and Baxt Ingui Principal Michael Ingui and John Mitchell from Bldgtyp joined us on November 10th to talk through one of Michael's favorite projects. The Willow Heights Passive House retrofit is a rowhome located in a landmark district in Brooklyn. Michael and John will geek out on the Passive House details that took this leaky historic home to Passive House performance. The retrofit included a two-story rear extension, an eight-foot cellar dig out creating a living space that does not feel underground, and a tiered rear yard connecting to a four-foot deck off the main level.
Check out the full transcript for the video here:
Michael Ingui:
Great, so thank you very much. Michael Ingui from Baxt Ingui Architects also with the passive house accelerator, working with Zach who's made the accelerator, what it is, Zach and Sydney and team. And I'm excited to be talking about this project. It's a fun one. And it's fun for lots of reasons. For those of you who don't know our office, we do a lot of work outside of the city. We do a lot of apartments, but we do a lot of townhouse work. A lot of brownstone work, both in and out of Manhattan. We're looking at some other projects outside of the city as well, which is fun. And what's fun for me in this particular case. If anybody was on Friday's Engine 16 Tour where it was kind of Amy Failla's baby, but I was still talking a little bit. This one's Frankie Failla's baby.
Michael Ingui:
They both work for us, yes, they're married. Yes, they met in our office and all four of the projects on this screen are projects that Frankie's been involved with. And there's actually two or three more now that Frankie's on. So he's on a lot of our passive house projects. He's been pretty instrumental in helping us create kind of a repeatable approach that we do on our passive house projects. And it's for me, just like another example, I'm happy to be talking today. Frankie's here by the way, for all the real questions, but I like presenting these. They're great, but it's the teams that work with us that are really good. So people have probably already seen me show this slide before, but I'll show it again, because I like it. And it's the five principles that everybody likes to talk about.
Michael Ingui:
And then for me it's the amenities that my clients care about. And I feel like they want us to focus on the amenities. Sealed from all bugs and dust, unwanted moisture, healthy filtered fresh air, windows that create safe, warm, serene environments, warm floors, comfortable buildings. These are all things that they don't want to live without. They want these things. And you describe these things, a lot of which they didn't know they could have, and they really want to do a passive house. So I think they're excited about energy savings. They're excited about saving the planet. They'll donate to a great cause, but a lot of them are coming to me wanting a really great house. But in this particular case, that's not true. In fact, I also talk about contractors and how a lot of our contractors came to us not knowing anything about passive house.
Michael Ingui:
Also in this project, that's not true. This is one of the first projects that came to us where the client who's our first team member there, not only came to us wanting a passive house, knowing what a passive house was actually also introduced us, which we already knew Jose from Jay's custom. They've been doing passive houses or Jose's been doing passive houses longer than I have. And so we worked with Jose and Chris, you can see Chris in the yellow in the background there, Jose's kind of right in the foreground. This is actually a student tour that was being done with one of the local colleges. But this client knew what they wanted. They knew what they wanted. They wanted a passive house. They came to us wanting it. If we hadn't done it, I don't think we would've gotten the job.
Michael Ingui:
We've got a great team. You can see the rest of the project team, but in this case, the client was also really heavily involved in the design. They're also here today and you can talk to them about that as well. Or I think I'll ask them their first question, but the client was really involved in everything from kind of the aesthetic that you'll see with the stair to cabinetry, to just really knowing what they wanted. And they were really, it was an integral team member.
Michael Ingui:
So the project, so these are Collin Aide houses. There's a bunch in a row. I'll go to the kind of this slide you can kind of see it. There's a few across the street. It's in the Brooklyn Heights Historic District. We had these really interesting, small, not energy efficient dormers. House had been empty for a while. Our client purchased it. A lot of the detail had been stripped years ago from the inside. There were definitely some leaking issues. And a lot of times you fall in love with these beautiful old homes, but you don't realize just how leaky they are or how poor performing they are.
Michael Ingui:
In this particular case, we kind of knew what we had. We had a lot of issues in the back. We had a lot of water seepage in the back. Lot of issues around the windows, the cellar had some major water damage. They knew buying this that it was a good candidate for a real retrofit. And there were a lot of opportunities. This kind of gives you again, a little bit of a taste of what was inside you're through the wall air conditioner. We'll see these windows again in a second, kind of the front windows. We'll see them again in the finished photos. But again, a lot of the detail removed, some real water damage, real Boeing of the ceiling roof joints were in pretty rough shape.
Michael Ingui:
So what's nice is we have clients who purchase a house not knowing that we're going to have to do lot of work in this particular case. Not only did the client want to do the work, but they knew what they were getting, which was really helpful. This is that same window. And this happens to us all the time. The project can look incredibly intact in this photo. It could be beautiful. The trim's gorgeous, the crown's there. And when we open it up and people want to know why their windows are so leaky, a lot of times it doesn't have anything to do with the actual window. There's no insulation here.
Michael Ingui:
I mean, there's a lot of structural issues here. So we fixed it all. We parged it all. John will get into that a little bit more, but this is kind of what we're looking at. And in terms of design, this is in a landmark district. It had some additional floor area available, but there's no way landmarks is going to let us put in an addition at the top, we did a small one in the back, but in New York city, one of the interesting places that we like to do a lot of work and again, this client came to us with this idea as well. They knew they wanted to kind of really kind of create a really fun space down here. So they've been really integral in the designs, but these spaces give us a lot of benefit and a lot of real possibilities of what you could do, especially in a landmark project.

Michael Ingui:
So what do I mean by that? So here's a section of the house. Here's the existing rear yard. Come in the front door pretty much on grade. You walk out pretty much on grade, lot of water damage here. Here's the existing cellar. Here's the new rear addition that we did, doesn't come too far out, but sometimes just that amount of feet makes all the difference in the world in the parallel level where this kitchen living dining. But what we did is we carved out a lot of the yard and it creates a really highly functional space down in the cellar. It's still a cellar, it's a rec room, but it's a great rec room. And it's a space that the whole family can kind of hang out and have fun. Here it is from above. You can see, again, this is in a landmark district. In fact, these slides come out of that landmark public hearing. So you can see the yard here. You can see the yard in this particular case. This yard has already been dug out a little bit as well, by the way, passive house wise, you can see the air conditioners on this roof and the air conditioners on this roof which is real.
Michael Ingui:
Again, these are just renderings beforehand, but the actuals result in something like this, where here's that same before here's that same after you can kind of see the terracing of the yard, the deck provides some real good shade. It also provides a great place to be in the rain. And so we talk a lot about passive house in this program, but for us in our office, we're primarily a design office, which is why John's here with me as well. So he can answer the more difficult passive house questions. And it's not that we're not passive certified. In fact, most of the office is we've all taken the course. I think it's important to know what you're doing, but we're really design centric. And just being able to focus on this while we're working with such a good teammate like John is incredibly helpful. Here's some more photos from the outside, some large doors, by the way, the windows and doors in this project are icons. I think Adrian is on this call as well. And they're are aluminum on the back, aluminum outside wood inside, and they are wood on the front.
Michael Ingui:
Here's the original stair. Here's the new stair. This stair was in really rough shape. We knew we had to replace it. This is a great example. I think from our initial meeting, the client came to us with a photo of a similar stair and these stairs are tough. They're hard to do in a house, in a typical house. A lot of times you'll see theses kind of sculptural stairs and they're in a larger home. This was tough, this was built on site. This is a funny story because Jose, when we were describing the stair and designing the stair all the way until the stair was built, I was nervous because he had a guy. He had a guy who could build it. He had a guy. And I didn't really believe him because I've heard that a lot, but he really did.
Michael Ingui:
And he had so someone who built this stair onsite the whole thing, the whole deal onsite. And we'd go there every couple of days. And we'd talk about the curves. We'd talk about how different places and different things kind of weave up. And it brings all this light down, but he really had someone who had the ability to kind of hand sculpt this stair onsite. So it kind of comes down to Jose again, he's been doing passive house forever, but he's an incredible carpenter. So passive house is easy and it's just a piece of kind of what's important in the house.
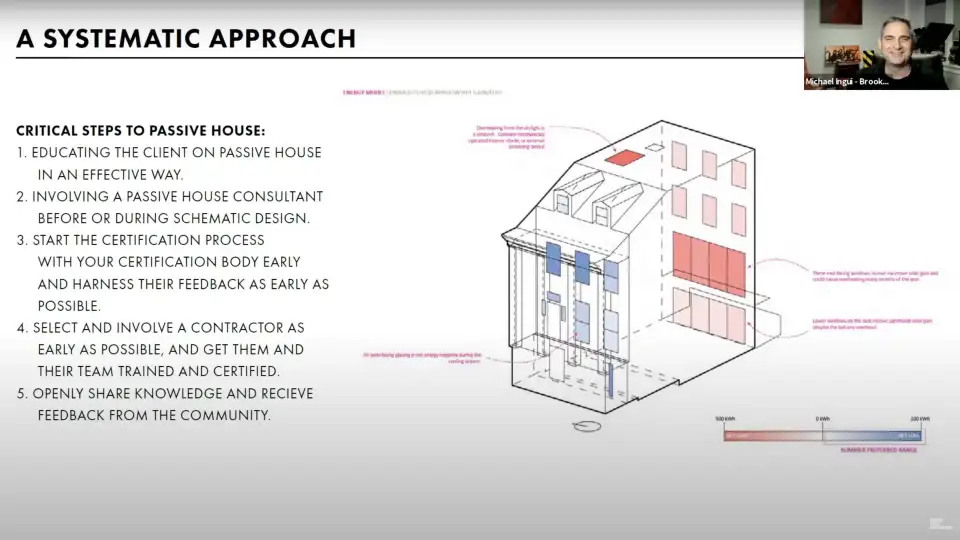
Michael Ingui:
So this will be my last slide before John talks. And this is our systematic approach that I was kind of describing that Frankie and Amy and some of the other people in the office have really been helpful along with John and a whole bunch of the contractors that we work with, but bringing the passive house consultants in early, especially on a project where the client wanted it is important. And I can't tell you just how nice it is to work with John. And Ed of course, and I don't think Ed's here so we'll just talk about John. But working with building types really helpful. Bringing your passive house consultant in early is helpful. And then they were involved the whole way through some of the things that he's going to talk about are what happened during construction. And I think the passive house consultants are under utilized during construction. I think they bring a lot, just a lot to the table. And in this particular project, there were so many ins and outs and difficult elements that having them on was really a lifesaver. It was great. So anyway with that, go for it, John.
John Mitchell:
Thanks, Mike. That was very nice of you. Everything that I'm going to talk about is invisible and all those lovely photos that Mike showed of like the finished stair and the finished building. You don't see the passive house, you don't see the air ceiling, you don't see the insulation. You don't see the design work that went into making sure that there's no risk of mold, condensation, these kinds of things, but it's all extremely important. And it all happens at this critical moment where you have an opportunity to renovate a building like this one. So we get the opportunity to actually take this thing down to its bones and really go to work on it and reveal all of the things about it. We get to reveal the problems with the structure that need to be dealt with. We get to reveal exactly what's been going on for all these many years.
John Mitchell:
And our job as passive house consultants is to help reveal what this thing can be. And part of that is to sort of make real, make visible things like energy flows, things like moisture, things like ventilation and things that are not usually available to people. People don't normally see them or experience it. So our job is to bring all that stuff to the floor.
John Mitchell:
And we do that by first building an energy model of the building and then taking all of that data, which is also quite opaque and bringing it out into something that people can understand. One of the first things we do is have a meeting where we present a full report of the modeled building results and work through with as many of the stakeholders as we possibly can. All of the possible versions of the building that we want to look at. We'd love to have at that meeting the architects, we'd love to have the owner, the builder, the mechanical engineer, structural engineer would be great. Anybody else you could think of? We want to have them at that meeting so we can actually begin to craft the direction that the project is going to go. So we present options for air tightness. We present options for insulation, window and door products, all these kinds of things. And at the end of that meeting, ideally we come out with a plan and our plan will be for this project to pursue an enerphit renovation. Next slide Mike.
John Mitchell:
So the enerphit standard is a version of the passive house standard that is tailored specifically for renovations. As many of you probably know, and it's a performance based standard. So we don't have a sort of prescribed R values of air tightness. Well, air tightness is prescribed. We don't have prescribed R values or window performance. We have to sort of figure out what the recipe for the building is going to be. And so together with Baxt Ingui and the clients and the builder, we came up with the recipe for this building. We were going to hit an air tightness of one air change per hour, which gets us to the enerphit standard. We are going to install our values of R-20 at the cellar floor, R-25 in the historic masonry walls and R-60 at the roof. We were going to build thermal bridge free.
John Mitchell:
So we're going to have very low moisture risk. And we're going to look at all the details on the exterior of the building envelope and make sure that this is the case. We're going to install high efficiency mechanical ventilation, and we are going to install high quality windows and doors, and we're going to install them well. We have to not only buy a good product, but we have to put it in the building in a really sensible way. So that's the recipe for this building. And I will show you then how we sort of go through and assemble this kit of parts. Next slide.
John Mitchell:
So the cellar slab is really simple. R-20 was our target. So we specified four inches of foam insulation. You could get that R-20 using any number of insulation types. We used XPS foam in this case, but we could do that with GPS. We could do it with mineral. Woo. You could do it with gravel. There's all kinds of ways to get to R-20. In a project like this the digging is really important. So having a really high R per inch saves a lot of time and labor. The way that these buildings get dug out is one bucket at a time. These are five gallon buckets that are filled with dirt, carried from the cellar out to the street, nine times out of 10. So it really matters how much you excavate. So we want to really be sensible at how much installation we specify. Next slide, please.
John Mitchell:
This building also, because we dug out, we had to support, or I didn't do this. The team had to support the existing foundation walls. And rather than underpin, they built a bench foundation and that bench foundation holds those existing foundation walls in place and allows you to take that floor down lower. So we insulate below the slab then up and around that bench foundation so that we stop any heat loss and hopefully do that in a thermal bridge free way. So at that slab to bench foundation detail, we actually get a little piece of thermal break insulation as you're seeing in that right hand diagram. Next slide.
John Mitchell:
Here's what that looks like. And the contractor did a fantastic job. You can see on the left hand image here, the continuous foam going up the bench and over the next one is the next step in that process where that sub slab vapor barrier gets wrapped up and over that foam insulation on the bench. And then you see it's terminated with a termination bar up against the masonry wall. So a really nice detail that's going to live there and last for a long, long time. And then on the right hand side, you see the mechanical room in the front of the building where the air barrier for the mechanical room is tied into the air barrier at the sub slab for the sub slab insulation. Next slide.
John Mitchell:
So for the existing masonry walls front and back, we first have to take care of all that brick that Mike showed the pictures of, right? We have to repair all that. We have to do repair any damaged brick. We have to do tuck pointing in some spots. And then we're going to go back and install the air barrier area, the primary air barrier on that masonry layer. We'll look at images of that in just a second.
John Mitchell:
For the main wall, we have five inches of censpack cellulose insulation and we create that five inch space by building a two by four wall and spacing it an inch and a half off of the existing masonry wall. So that first inch and a half between the masonry wall and the wood framing is effectively continuous insulation. The cellulose gets around all those framing members, packs in there and you have a continuous insulation layer.
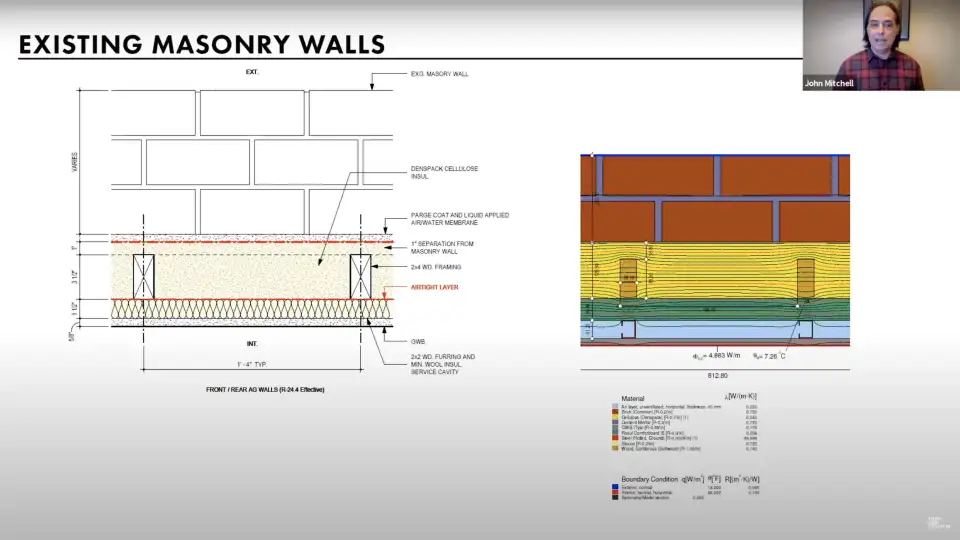
John Mitchell:
So you have an inch and a half of uninterrupted insulation and three and a half in the framing bay. Then we have an inch and a half of mineral wall insulation, outboard of that before the service cavity. Next slide.
John Mitchell:
To achieve the air tightness for this project, we recommend first parging the brick after it's been repaired. So a thin slurry of line based mortars is applied to the brick. Then a liquid applied air barrier vapor retardant layer. In this case it was a Sto-Gold- sorry, Sto-Emerald coat product. Then all of the penetrations into that masonry liquid fluid applied air barrier layer get detailed. So all the joints penetrations, anything that's going to penetrate that layer gets detailed with a flexible connection.
John Mitchell:
Then we install the framing on the front and rear walls and install the smart vapor retarder over that. And then you can see at the roof, we have the vapor retarder going, or the air barrier vapor retarder going across the roof plane and connecting back to those masonry walls there. Next slide.
John Mitchell:
On the left hand side, you can see a sort of, almost completed version of that wall. So five inches of insulation, then the smart vapor control layer, then the framing with the middle insulation and then the tipton finish. And on the right hand side, I included this just because it's the most boring image ever. And I love it so much because it shows how all of that chaos of that masonry wall has been managed. It's been patched, it's been parged. That fluid air barrier products have been applied to it and the joints have been integrated into it. It all looks perfect. Next slide.
John Mitchell:
I also wanted to reveal a little bit of what's hidden in the process in that, as Mike was saying, Baxt Ingui has done a ton of projects like this one, they've done a ton of rear additions and it's always kind of the same set of components, right? You have a big steel frame that has to make the opening for the addition. And then you have a new masonry wall in the exterior. And so they've done that a bunch of times and we've worked with them a bunch of times on those projects. And yet everyone is a little bit different and we end up having to really iron out the details and make sure things work correctly. So this is just one of the many back and forths that we had on this rear wall section, as we are coming to the final version of construction documents with Baxt Ingui to get everything just so. So we don't have any risk of moisture or thermal bridging or anything like that. Next slide.
John Mitchell:
For example, window and door details. Also something that Baxt Ingui knows how to do. We know how to do, they know what we're looking for in our window and door details, but it still takes a lot of iteration to get these things right. And it's very specific to the products that you're using. So one door manufacturer sill will be different than another. So it'll have a different impact on the installation detail. So here, this was how, on the left hand side, how the detail was originally drawn, it looks great. You have a door sill and head coming together at a strip of insulation. That's what we want. And we want the doors and windows to be part of the insulation layer. It looks like it's going to be okay. But when we did the analysis, we realized that actually the surface temperature at that door sill is too low.
John Mitchell:
There's a potential there for moisture to build up for you to have condensation. And so we had to alter this detail in order to hit those temperature thresholds so that we wouldn't have any risk of moisture. And this is one of those things that gets checked and certification and might not get checked in a non-certified project. That's one of the benefits to a certified passive house project is all of these things. All these details get documented and improved. So next slide.
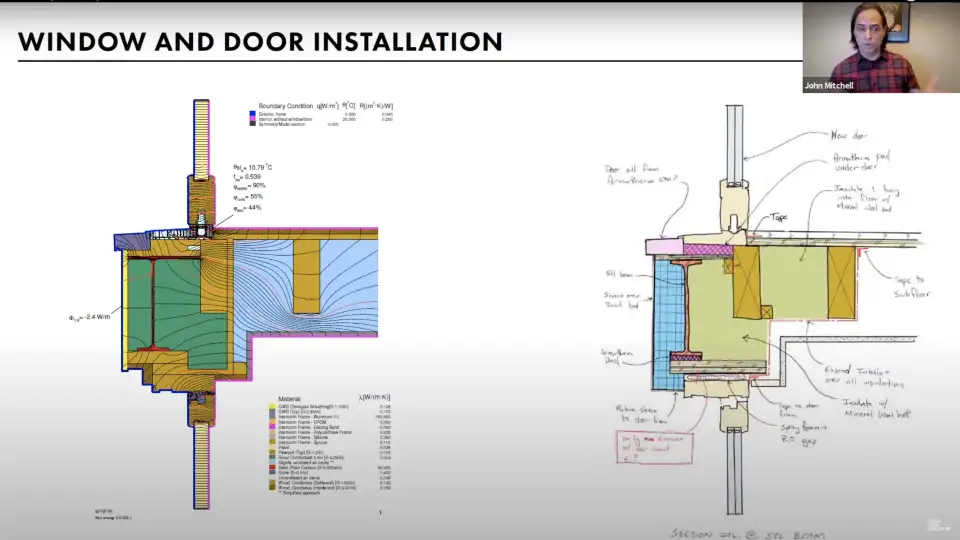
John Mitchell:
Ed proposed a new version of this detail. It's not dramatically different, but it had a huge impact on the surface temperature at that windows, that door sill. And so now we're in a place where we're not worried about moisture or condensation issues with that door sill just by making some little tweaks. So this is how the process works back and forth.
John Mitchell:
A lot of this happens during construction, just because that's the way it goes because conditions are being revealed as we're going along. And we can only address them as they come up. So there's a lot of sort of hands on work as the project is being built. Next slide.
John Mitchell:
The window installation. Again, we want to connect the window into the insulation layer. It's also part of the air airtight layer. It's also part of the weatherproof layer on the exterior of the buildings so the windows are where it kind of all comes together. For this project it was not too challenging. We have a two wide brick wall and the windows sits essentially in the insulation layer of the framed wall that we've built behind that. And so that performs quite well. Next slide.
John Mitchell:
At the jams, we have the benefit of that two inch roughly pocket that used to be the placed where the window weights lives. And we can use that space as we do on most of our projects to insulate, to bring the insulation layer into the window installation and connect those two things together. So instead of installing that window right up against the brick, which would be a terrible thermal bridge, we could use that weight pocket and insulate up to and around the window. Next slide.
John Mitchell:
And just to show sort of the way that we're thinking about air tightness all the time throughout the project. And I throw this in there a little bit for the folks who take the passive house training and who have seen or been told a million times, "you have to draw this red line, you have to do the red line test." And the red line test is really where you honestly look at your drawing with a red pen in your hand, and you trace the air barrier and you make sure that you can complete that line continuously around your drawing without picking your pen up without doing like some crazy shape.
John Mitchell:
This is like the cheapest air tightness test you can do because it happens early. It happens in design and you can identify these places that are going to be a challenge, and you can work through them ahead of time. One of the biggest things on this project is the vestibule. Next slide, Mike.
John Mitchell:
We've got a beautiful historic door and you can see this is actually post construction. This is as it probably looks close to what it looks like today. And you have this historic door that has to look like all the neighborhood historic doors. So we're not going to change that, but it's very leaky and it has single pane glass. And so we need to bring the envelope into the vestibule door, which is easier said than done. So we show how we do that step by step as a way to work through it ourselves, but also as a way to communicate back to the team how these things get done. So next slide, and you can kind of buzz through these.
John Mitchell:
So we start with the existing condition and we go step by step. So the next step is insulation. Then we install the airtight layer at the vestibule ceiling and we tape the plywood on the floor so that would become air tightness layer there. Then we frame the wall and if we hadn't drawn this out, you just know the wall would get framed first. Right? It's just how it goes. Even though somebody might be thinking about passive house, the framer may not be, so the wall gets framed after those airtight layers get installed. Then the air tightness layer on the framed wall itself. Then furring, then the mineral insulation on the interior. And we don't draw the finish cause we don't really think about finishes that's for those guys. Okay, so next one.
John Mitchell:
So you see on the left hand side, this is beginning to take shape. The contractors installed that one super crucial flap of air tightness above the vestibule, above the soon to be vestibule and begun framing that opening. And on the right hand side, sorry, it's a little bit of a poor picture, but you can see that's on the right that's the completed version where the airtight layer, the Intel layer there is taped all around the existing joints. Next slide.
John Mitchell:
Moving on up to the roof, fairly simple. We have four inches of continuous insulation on the roof over the wood framed two by 12 roofing. So we have 11 inches plus of cellulose insulation below. So an R-60 roof in total. Next slide.
John Mitchell:
On the left hand side, you can see we're documenting this for the certification showing that we actually have those two by two inch layers of polyiso insulation on the roof and then the framing below, and then on the right, you can see how the air tightness at the roof plane gets terminated into the masonry wall. So we have dissimilar materials. We have that sheet membrane being connected to the air tightness layer at the masonry, we want to make sure that we really get a good connection there that's going to be durable and last a long time and they did a great job there. Next one.
John Mitchell:
Okay. I'm almost finished, I promise. So we have those historic dormers that Mike mentioned, and we're a little bit limited because they have to look a certain way. Obviously we have to sort of replicate the size of the existing ones in order to keep the landmarks and preservation commission happy and to make it look appropriate to the house. And so we don't have a ton of thickness. So we have four inches of exterior insulation on the walls, over a two by four at the wall and six inches at the roof. And you can see what's happening on the inside, which essentially there's no room for trim, we're just maximizing the space around that window in order to make it all work and have as large a window as will work in that case. Next one.
John Mitchell:
Okay. Finally, the proof is in the pudding we did blow door tests throughout. This is us performing one. The final blow door test was performed by a third party because that's the right thing to do and we did great. I said we did great but the construction team did great because they are the ones who are actually responsible for and installed all these air tightness details. 0.99 air changes per hour at 50 pascals. Next slide.
John Mitchell:
Success. We get the enerphit certification. We met our heating demand numbers. We met our cooling demand numbers. We met our total energy numbers. We got the air tightness that we were looking for. And maybe from my of perspective, most crucially, we proved that all of those details throughout the building were risk free in terms of moisture. And we calculated all those thermal bridges, which are so important to the performance of the building. Last slide. Yes, we did a wufi analysis and then I'll pass it back to Mike.
Michael Ingui:
I know I'm muted. Anyway, I had to do that. So before I get into the importance of sharing, which we're all here doing today, the one thing I'd say is I could listen to John talk all day and it's really helpful to have those meetings. It's helpful to have everything he just described. The one thing that I've said in the past, but you can kind of see it here. So I think in pre-design the passive house consultant and a certified passive house de-risks to a large degree building for architects and during construction. He's de-risking it for the contractor and for me. Checking our details, sending them through the program, really checking it through the certification process. So it's yet one more reason to do a passive house and to do a certified passive house, because it really requires you to go through that next step. And it was a really rewarding project. It was great.
Michael Ingui:
But coming into my last couple of slides, here are some finished photos, because again, it's not all about passive house although that would be great. It's an all electric house by the way. And this is the living, looking into the rear yard. You've got more view of that really cool stair. Again, hand built by small carpentry crew on site. Some upper level pictures, master bathroom images. And it just gives you a sense of the house. So with that, I think we are done. Thank you.