Last week, on October 12, Construction Tech partnered with Phius to bring our devoted audience a sneak peek ahead of PhiusCon, and to pick the brain of the Phius hive mind. Below, you'll find a transcript for the video that includes some opening words Phius Executive Director and Co-Founder Katrin Klingenberg, as well as pared back presentations from Passive House all-stars Alan Gibson, Graham Irwin, Tessa Bradley, Steve Hessler, Ilka Cassidy, and Will Bloomer. Cohost Shannon Pendleton has a bit of a cameo, too.
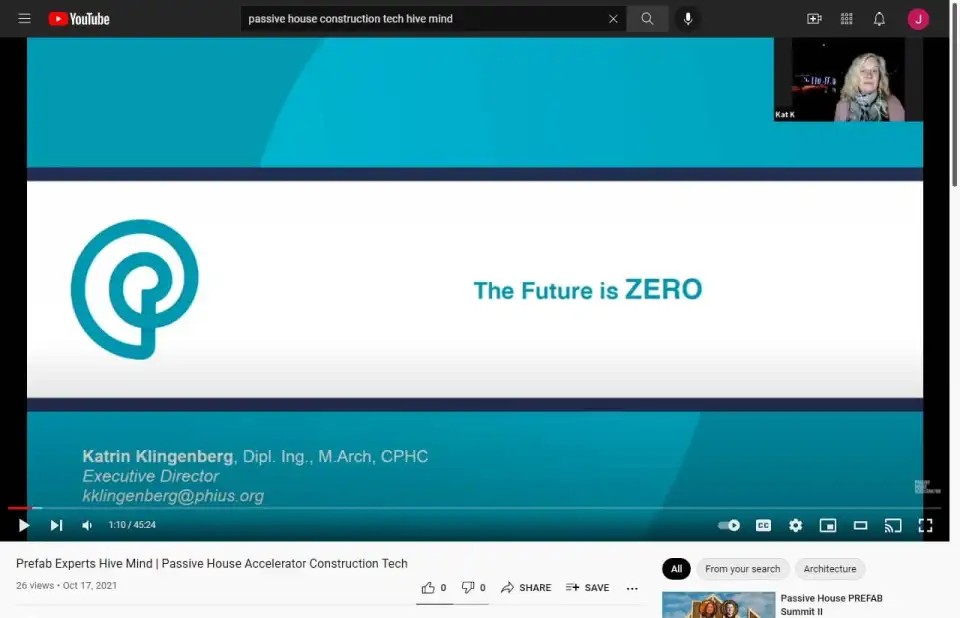
Katrin Klingenberg:
Hi, it's so fun to be with you tonight. This is absolutely fantastic. I don't know if you can see where I'm located. I'm straight from location. You can see the Hudson and the bridge in the back. I'm standing in a parking lot in Tarrytown. Super exciting. Everybody who has already shown up for the conference is super pumped. The first pre-con workshop has kicked off and went super well. Sorry for a little bit of background noise. There might be a train passing by, but you get the full flavor of Tarrytown right here and there. Just have a few slides. I just very quickly want to run through those, not talk too much longer, and not take any thunder away from the prefab folks. The future is zero for us and that's really going to be the message throughout the entire conference.
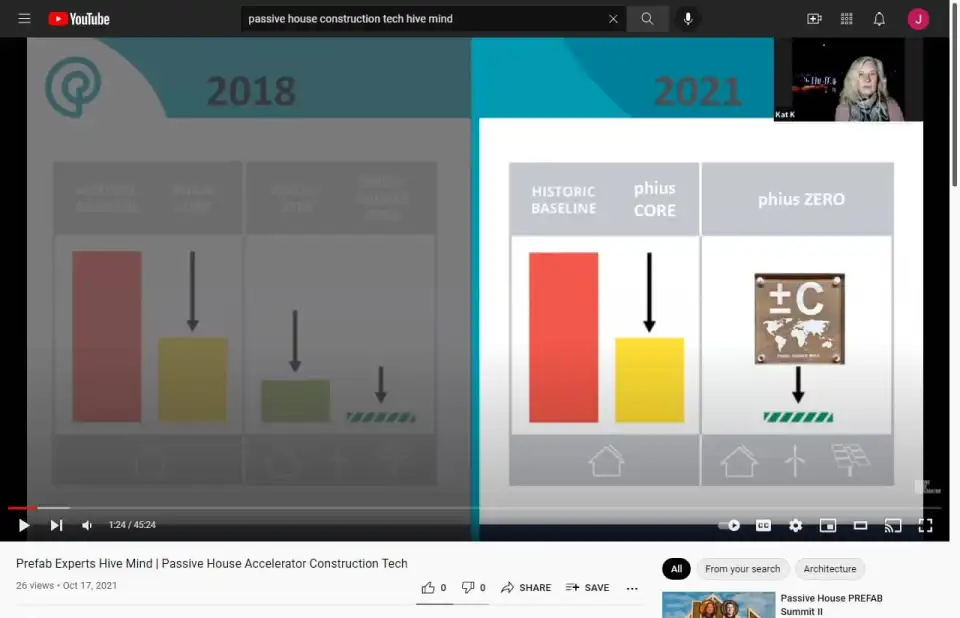
Katrin:
We're driving that with our standards. As you can see right here, 2018, we're still experimenting with halfway to zero, that kind of stuff. But with 2021, with the new standards, we firmly flip the switch and we are now zooming in on Phius Zero is our main certification.
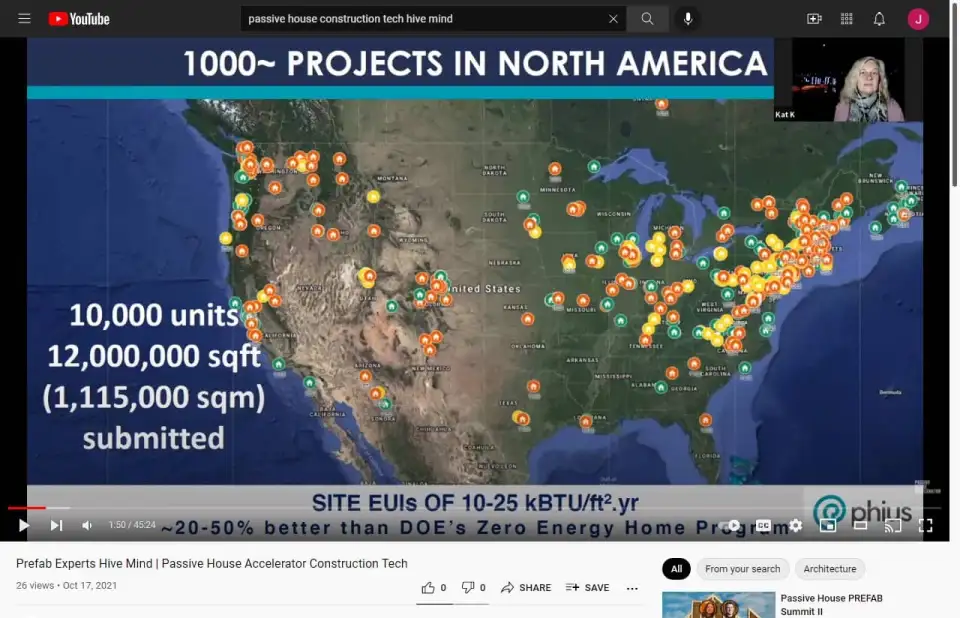
Katrin:
That decision has led to a couple of stats on where we're at with Phius project across the country, which is really super exciting. We've had 12 million square feet submitted now. That's a big number compared to a couple years ago. That's all units submitted, certified, pre-certified.
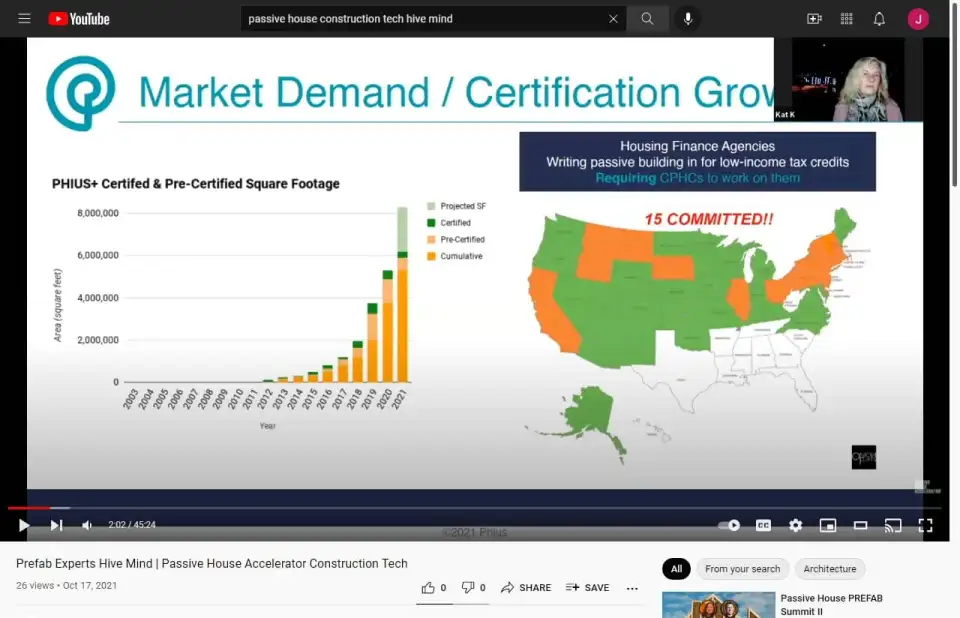
Katrin:
The next slide shows you the actual certified ones. We count the pre-certified once in those counts because they are essentially already under construction. They're a done deal. They have been reviewed. We know those guys are going to make it thanks to really great quality assurance. I know it's so fantastic. Of course, that all is happening because of great incentives across the country, including the housing finance agencies that have been lobbied by folks like Tim McDonald.
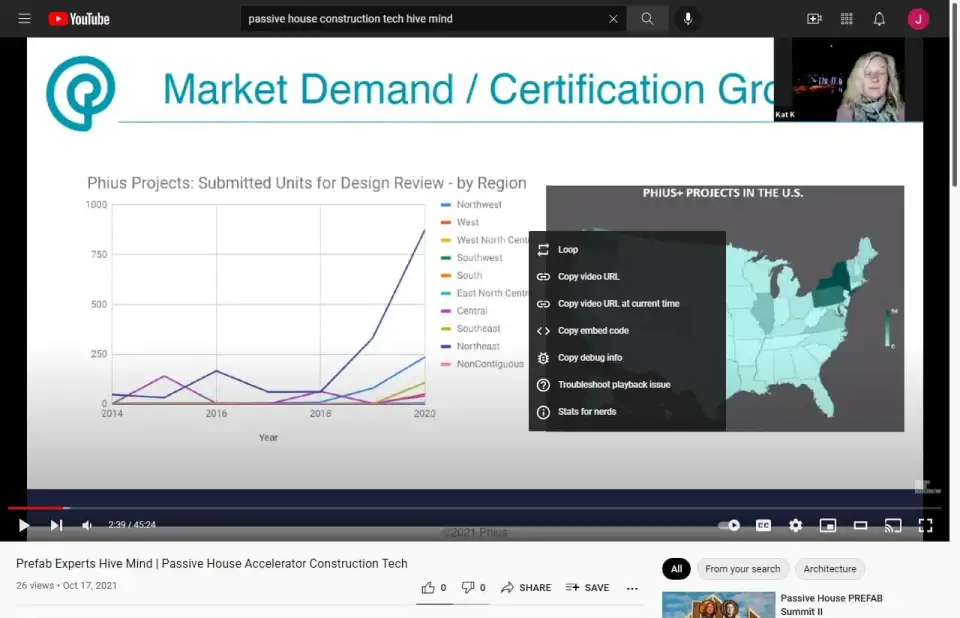
Katrin:
You can see the exponential growth here in projects. In this slide, you can see the density of the project and the uptake. The blue line that is going straight up now! Look at the projects in the Northeast, all ahead in New York City, New York State, Massachusetts, Connecticut. Really exciting stuff. This is where most of the projects that I just quoted in the 12 million submitted are coming from.
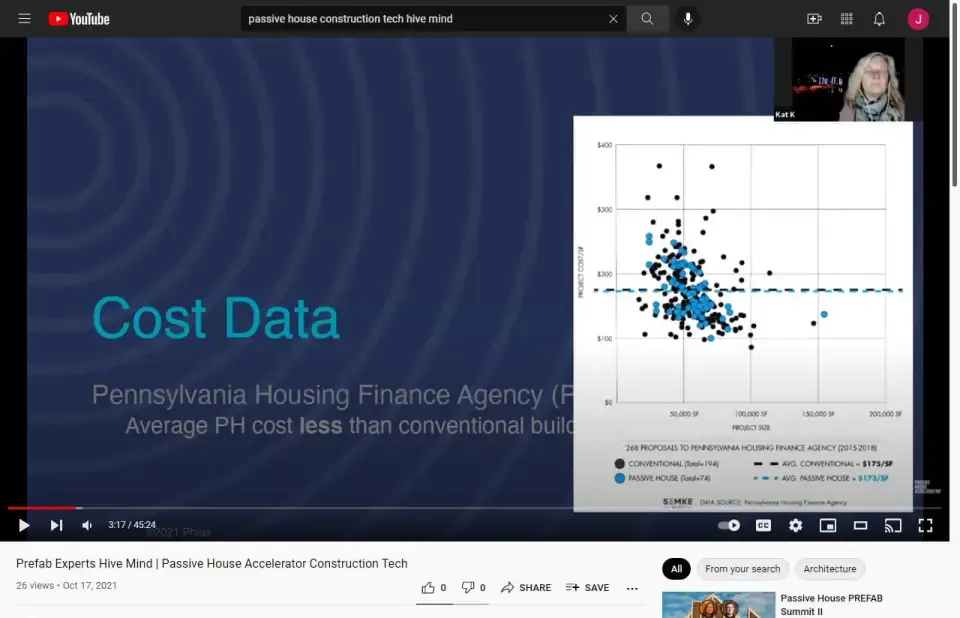
Katrin:
You probably all know this slide. Zack has been pioneering this to talk about costs. Cost is coming in at around 2% additional costs now. For multifamily projects, that's also super exciting. Because of that, we crack the financial nuts. And that is now happening in practice.
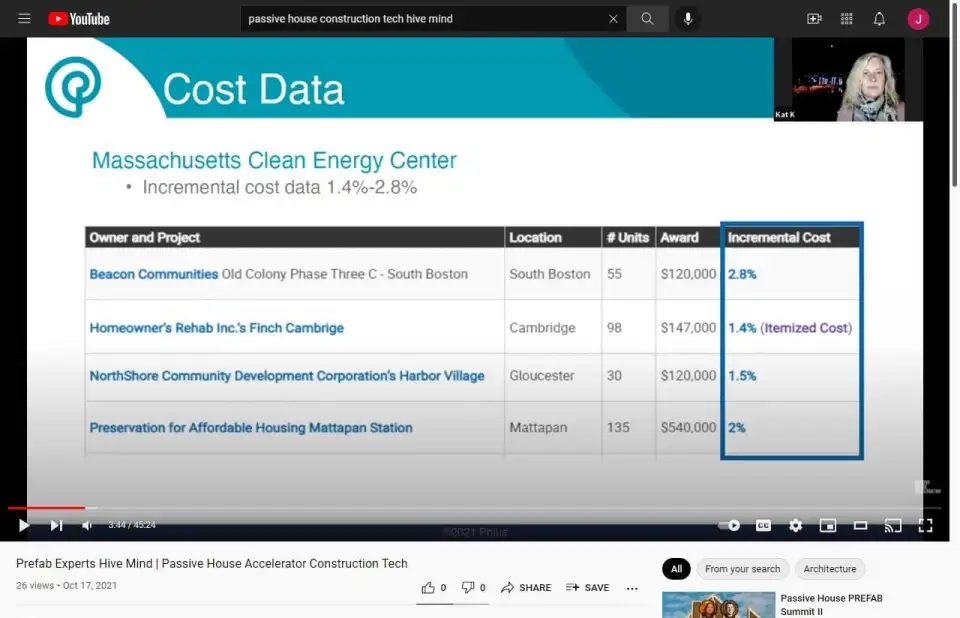
Katrin:
This is actual data from the Massachusetts Incentive Program, and this is no longer projected. This is what's happening on the ground. And so with that, we had a really great quote on our big building tour to New York City. We saw 425 Grand Concourse and Park Avenue Green. The owner of 425 Grand Concourse was asked like, "What made you decide to go passive?" And he had a one-word answer. He said, "Logic." We all just love that quote so much. It just makes all sense, right?
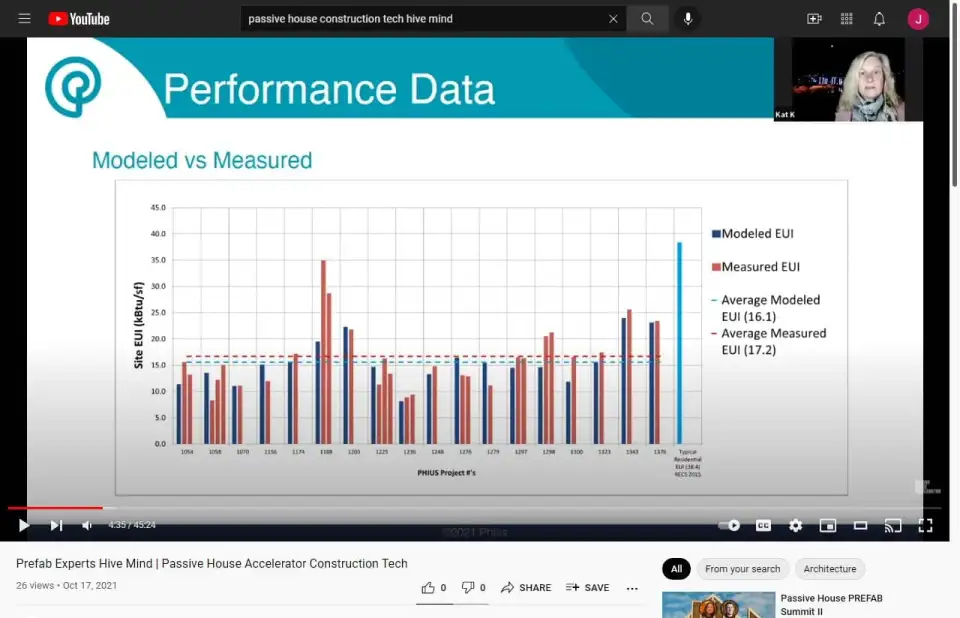
Katrin:
This is all due to just really great feedback loop and us refining our modeling. The results for modeled versus measure are outrageously great. We are off by 7% now. This is really industry-leading. It's also really great news because we want to make sure that the developers get the additional value in savings that we promised them, right? So this is absolutely great data that we now have in the kick-off.
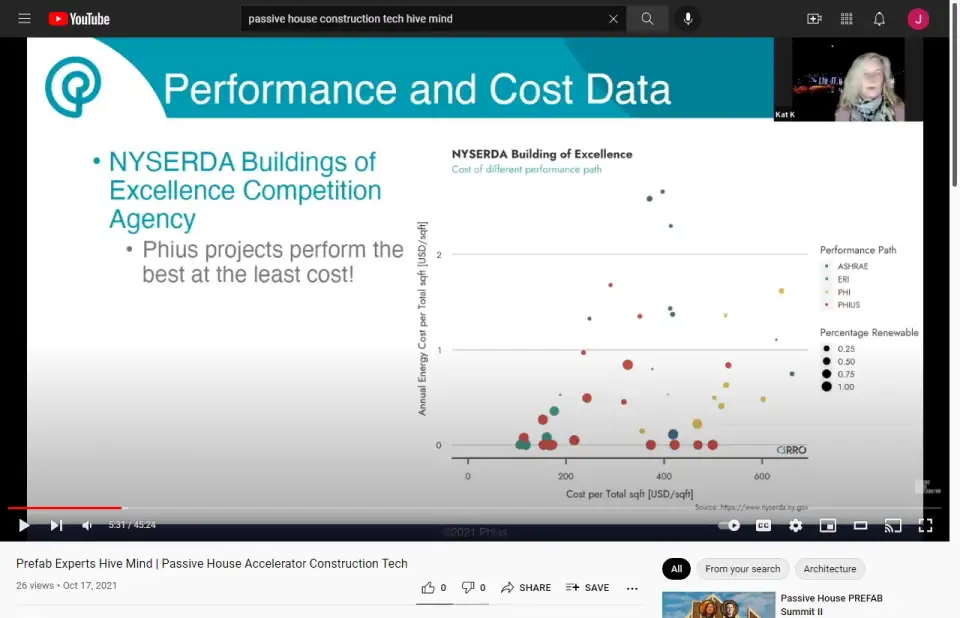
Katrin:
Last but not the least, this is the slide that I'm really excited about. The buildings of excellence program led by NYSERDA finally has data up. This is a graph from a third-party consultant, but data is up that shows cost versus performance. The news here is, again, that Phius projects are performing fantastically well. We are amongst the leading in the lowest costs and best performance. I was so happy when I saw this slide. It's absolutely fantastic. It proved what we've been saying: If you really cost optimize and climate optimize, you can get this done. You can build these projects for really good money and you get excellent performance out of them. It is now becoming mass market solution, so this is really fantastic.
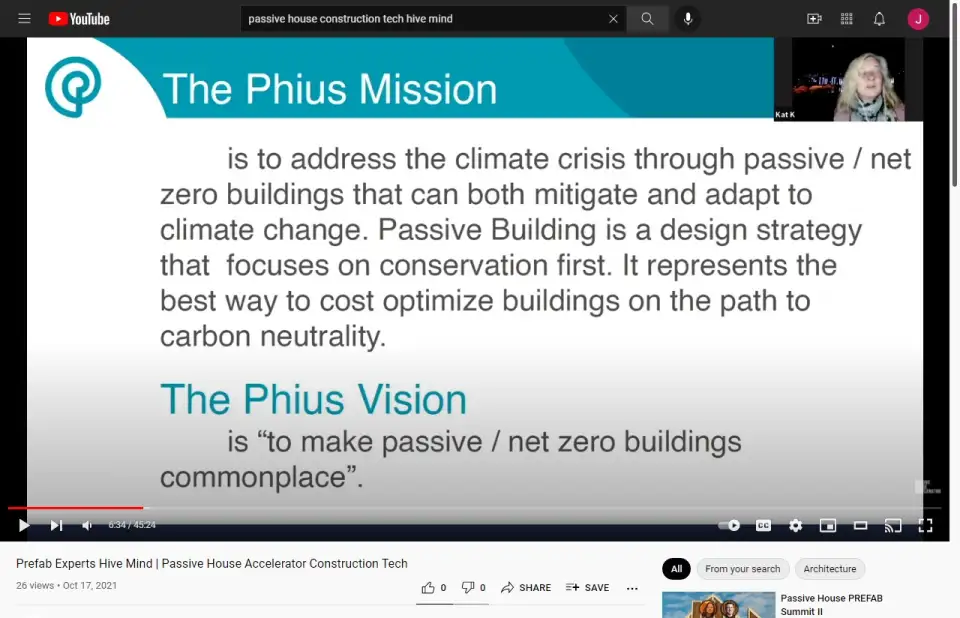
Katrin:
So all this has led to us altering our mission. You probably have seen our mission over the years, but we're now firmly zooming in the combination between passive and net zero building. What we really have to do in the building sector, we have to get to absolute zero. That's a whole different discussion, but net zero is a really great start with the basis of passive. So let's go. Let's do it. We're ready. We're here. I've never been more hopeful. This conference is really kind of the next phase. It's the first PhiusCon to kick off. Yes, we can do this. So I'm super excited.
We will be back next year in Chicago. There's tons of space there, so show up next year and join the party. Thank you guys so much. I'm very excited that you guys are hosting the prefab workshop that Alan conceived of maybe five or six years ago and still going strong. It's something that keeps growing. I hope you guys enjoy the show. This is a little preview of one of the sessions that is happening here at PhiusCon. Thank you for inviting me! It's been really fun to be here and talking to you from location. So, I'd say jump into the show. Thank you!
Shannon Pendleton:
I think that deserves a huge round of applause and a cheers. We have to start early tonight. That was fantastic. It's an honor to have you here and I hope you can stay as long as the rest of us, but if you have to go, we know where you are and we'll see you there soon.
Shannon:
It looks like we have our moderator for the prefab block. Alan Gibson, are you here and ready to unmute and fill us in on what got you started with Phius and prefab, and what's the history of prefab at Phius?
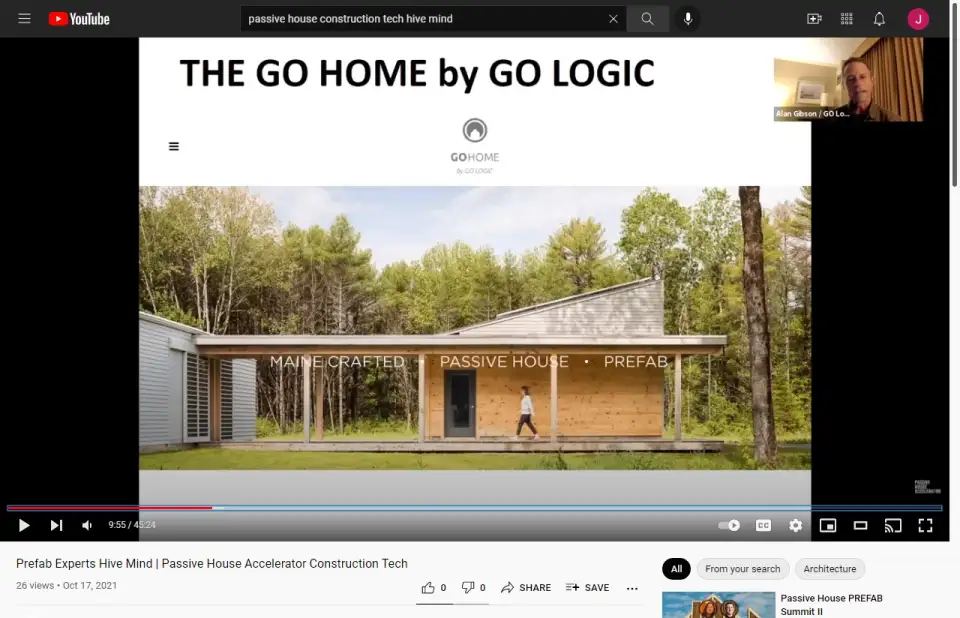
Alan Gibson:
For the last few years at the Phius conferences, there have been panels on panels, manufacturers, and pre-manufacturing in general, and we've had some industry leaders in that come and speak. We've had some DOE folks come and talk about the industry and the move toward panelization. This year, we have an all-star cast coming up at a session on Friday morning here in Tarrytown that includes many of the folks who are on this webinar tonight. I'm the moderator for that, but I was allowed to show some of my own slides because I'm also a panel manufacturer. I'm in Maine. I have a 35-person design-build company. We're general contractors and we've been panelizing for the last few years in earnest. We've developed a line of predesigned homes with the idea that we can reduce the design architecture time and also ideally simplify the build time.
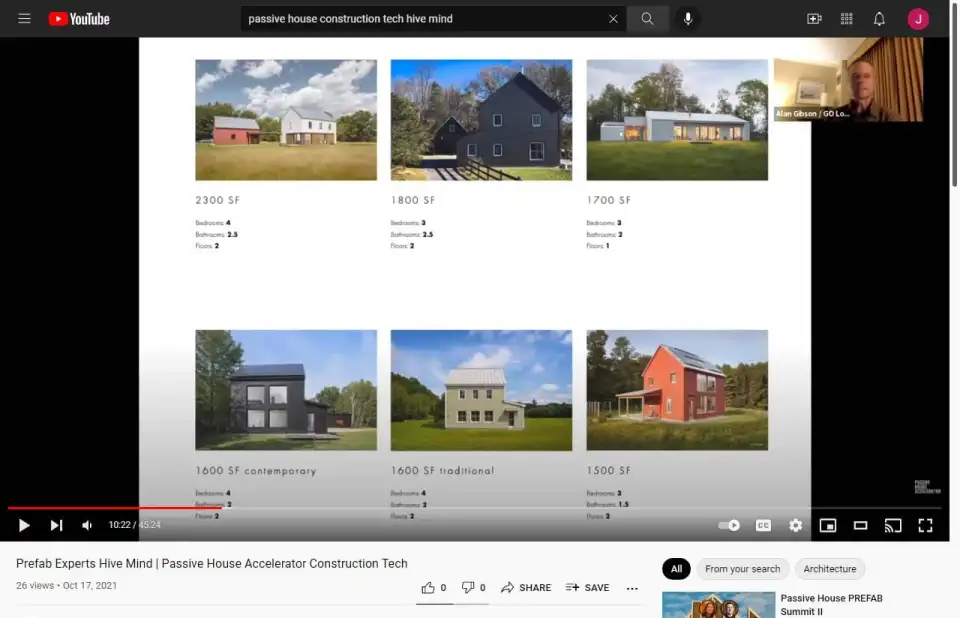
Alan:
These are some of our predesigned models and you can see they're all pretty simple, but we do allow people to customize them. That is something we're looking to try to change, so we can actually turn our panels from a custom process into more of a manufacturing process.
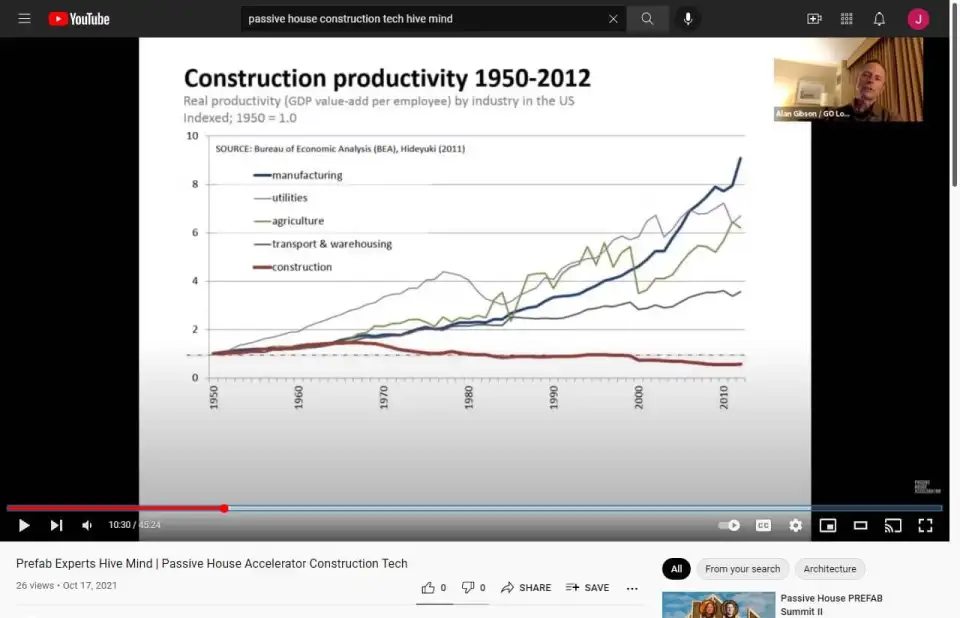
Alan:
Sam Rashkin introduced this concept to me a couple years ago, showing that productivity in the building industry has actually gone down since the 1970s. I think there are a lot of reasons for that. We're building better buildings, so the amount that gets produced per hour of labor is gone down. Unlike all the other major industries that have embraced mechanization, standardization, and industrialized process, the building industry hasn't. A lot of people are talking about how we have to move in this direction and I am working on it of my own process, my own company.
Swedish prefabrication is our main inspiration. I've learned a lot about how they do it over there, which is at a very high level. For those of you who are interested in learning more, I would check out Swedish prefab. Our shop is pretty low-tech. I have plans of building a new facility next year, but I haven't invested a ton of money in this one. We have just built some tables and we do stuff basically with hand tools and pneumatic tools kind of like you would do on-site. We've worked a lot on the BIM [Building Information Modeling] modeling and shop drawing process. We've come a long way with that in the last year with some new software. We tried to put as much in the panels as we can to add value. We install windows and doors. We air seal them. We put insulation on the exterior.
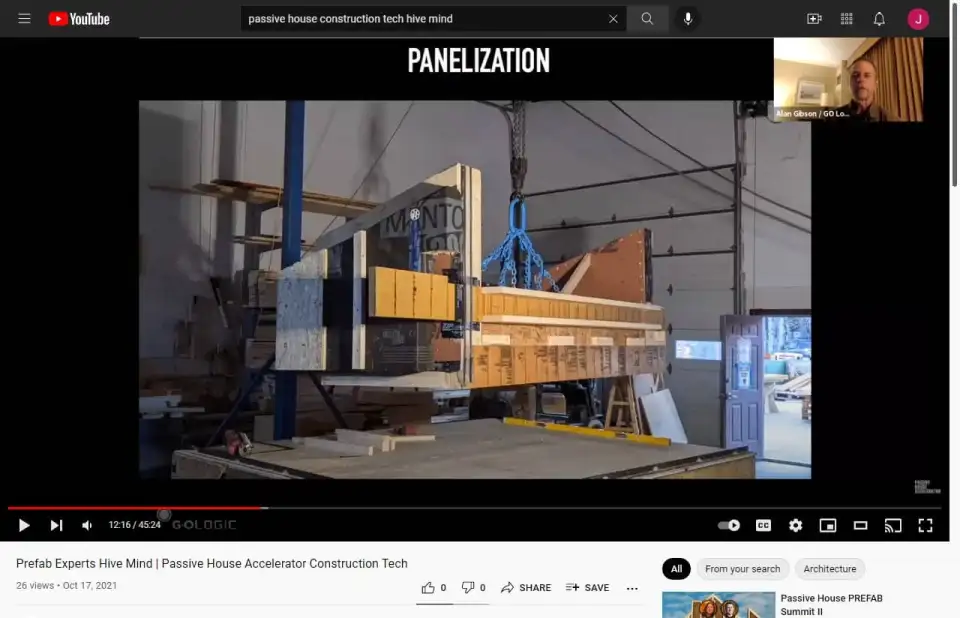
Alan:
We also do stuff like this, which is a Frankenstein monster panel. It's actually an interior ceiling on a kitchen bump out. My crew is very proud of putting this together and it actually fit, but this is not something we should do on a regular basis. We need to really simplify the panels, so they're not unique every time.
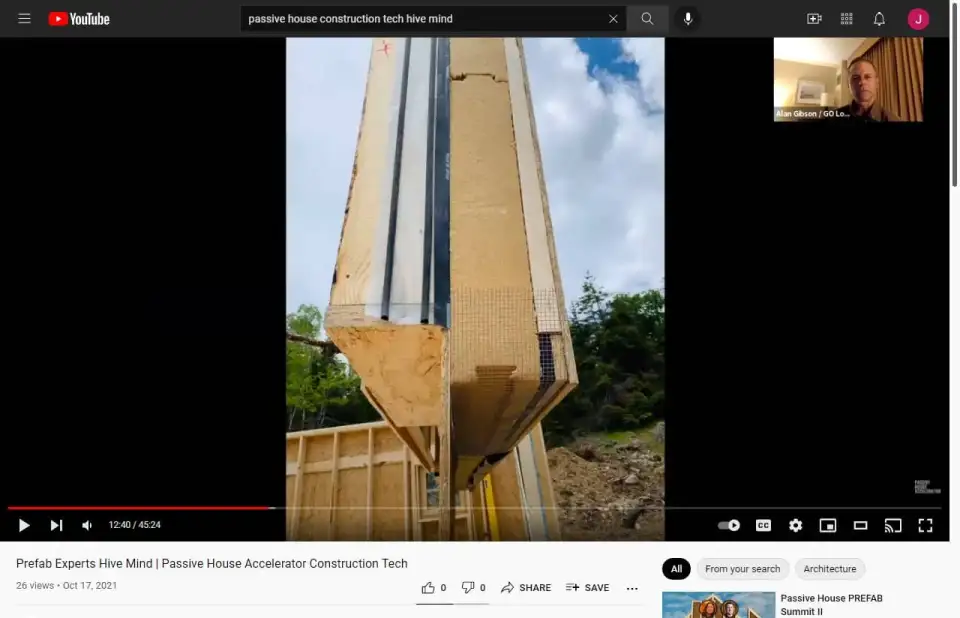
Alan:
Quickly, I'm going to run through a couple of installs. Here's a more simple wall, a typical wall. That's the section of it. We've got a stud wall on the inside with gaskets where they join sheathing layers. There's the airtight layer. Five and a half inches of rigid wood fiber, and then strapping rain screen, additional sheathing for siding if needed.
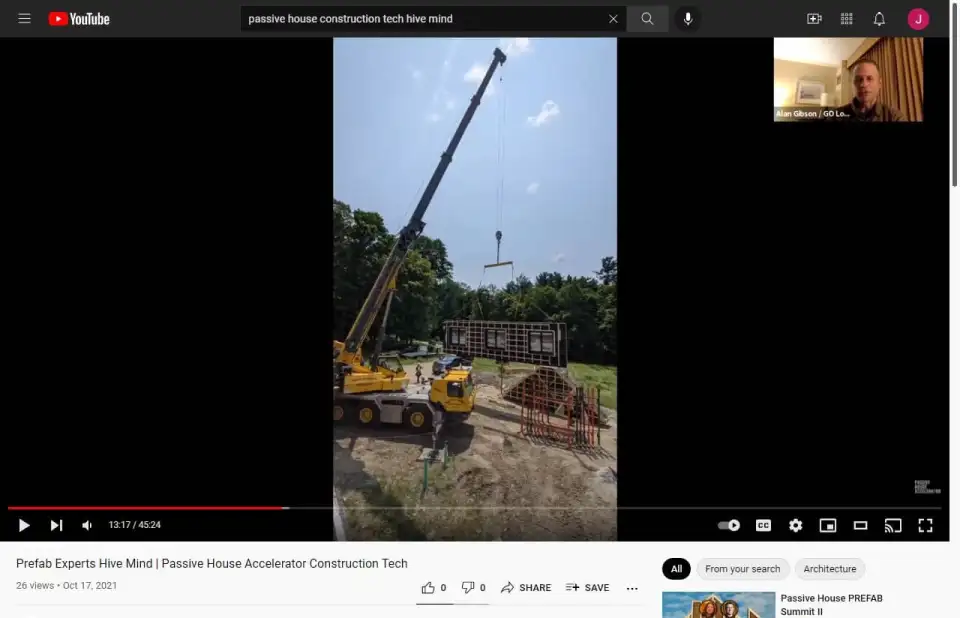
Alan:
I don't know why, but we tend to get a lot of constrained sites and we have a challenging time getting panels in. This is, of course, something you have to face when you bring in large panels into what we typically do, a rural site. But the panels got in there, we are placing the first floor with a lull. And my crews gotten into really big panels lately. This is a 35 or 36-footer in one piece. It's heavy. You need a big crane, but you can place a whole wall of a house in one go obviously with fewer joints. They are air-sealed. They seem to think this was quite successful.
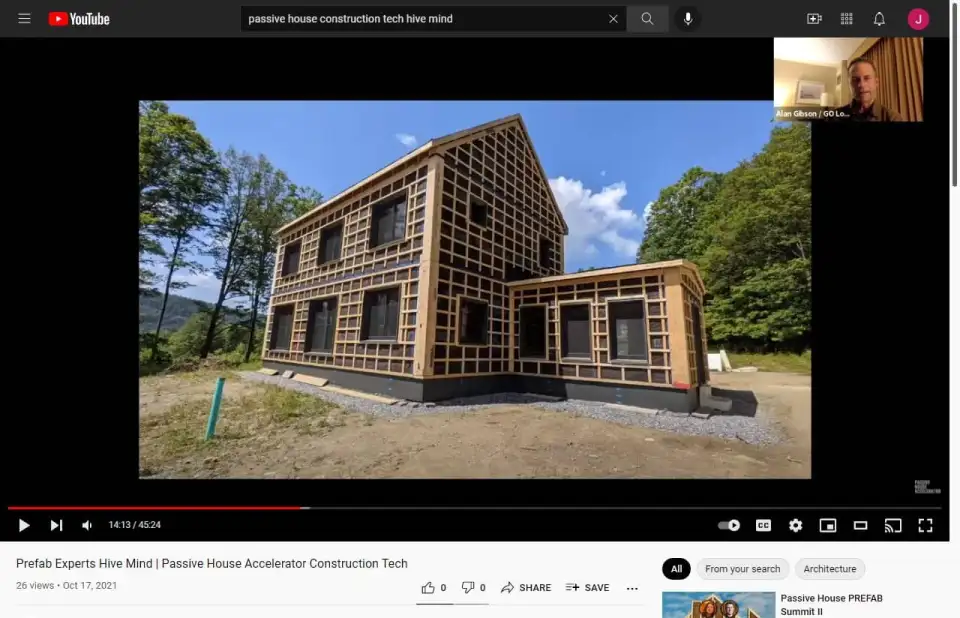
Alan:
This side of the house is a pretty regular two-story volume. It looks pretty easy to build, but on the backside there are a couple of bump outs and this is an interesting question that goes around my mind all the time. This helps the architecture, but it really slows down the panel process because, again, you just have different construction methods for the roof and connections and structure. Should we develop a simpler box that will be much more conducive to a quicker panel process? That's a completed project. The crew put that together I think in about eight days. It's about 2,500 square feet. I must say that the quality of our panels and our installations has increased dramatically in the last couple of years. We're really focusing on not having to make any changes in the field. And this is the case for this project and that's been a real improvement.
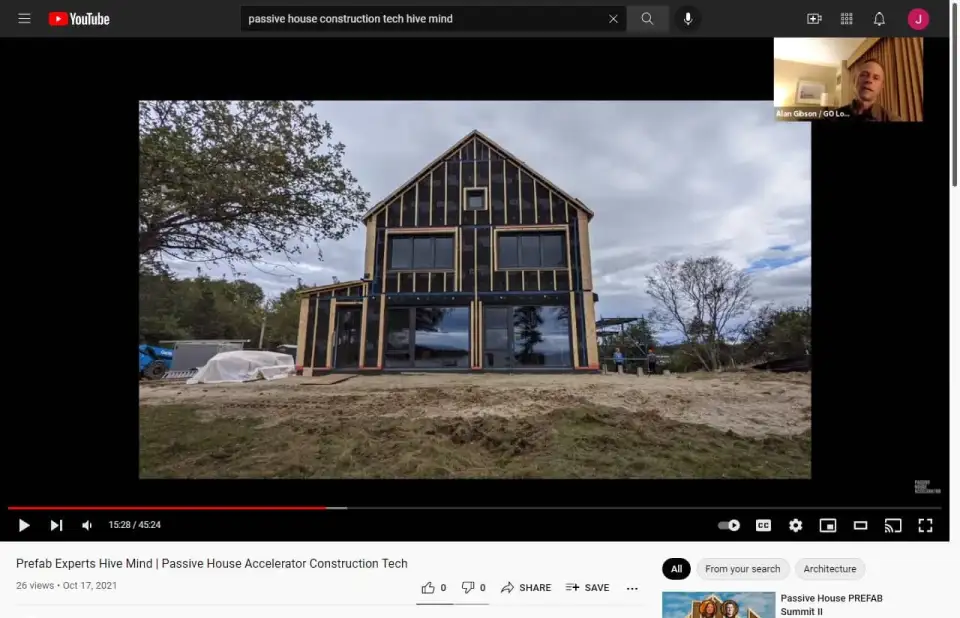
Alan:
The next project we did was another constrained site. This is essentially the same house, but it's on a different site and with different owners who had a slightly different program and they wanted the windows in different places. We basically customized the house again into a bespoke set of panels, which is obviously, again, kind of what we're struggling with. How much customization makes sense? I will say doing it this way isn't really taking much of the costs out. We're not seeing the benefit on the cost side of things, and I am interested in trying to bring that productivity level up, the amount of panel produced per hour of labor.
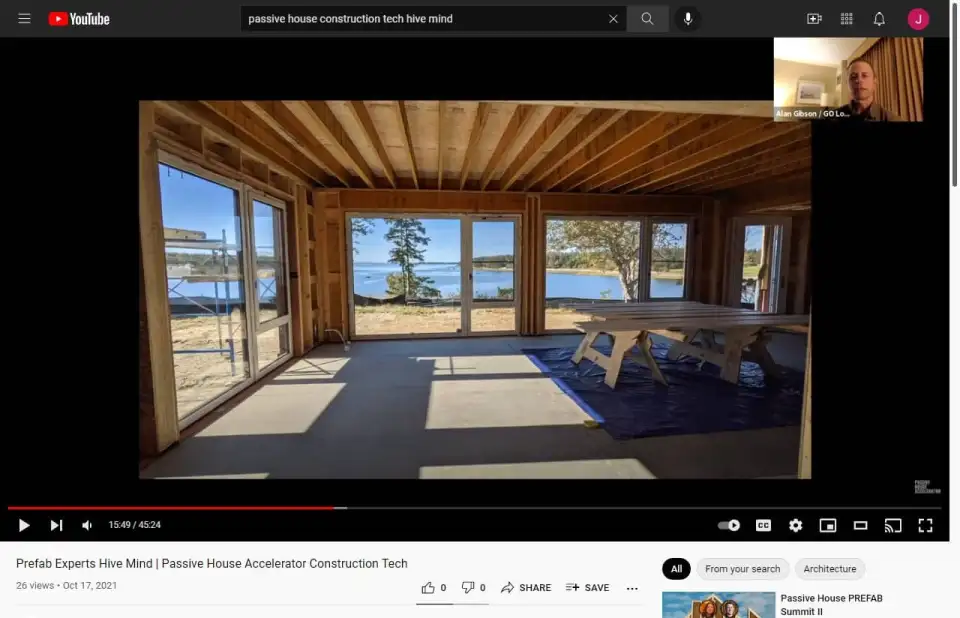
Alan:
Again, same house, a little bit different. The entry sequence on the back. From the interior, that's the view we're taking advantage of. I believe all of those big windows and doors were installed. Most of them were installed in panels. Obviously, when they get too big, we have to site install them. And this was done, again, in about a week on this wonderful site on the coast of Maine, in Penobscot Bay. That's it for me. Thank you. Moving on to Graham, who's going to talk about a very interesting infill project in Los Angeles.
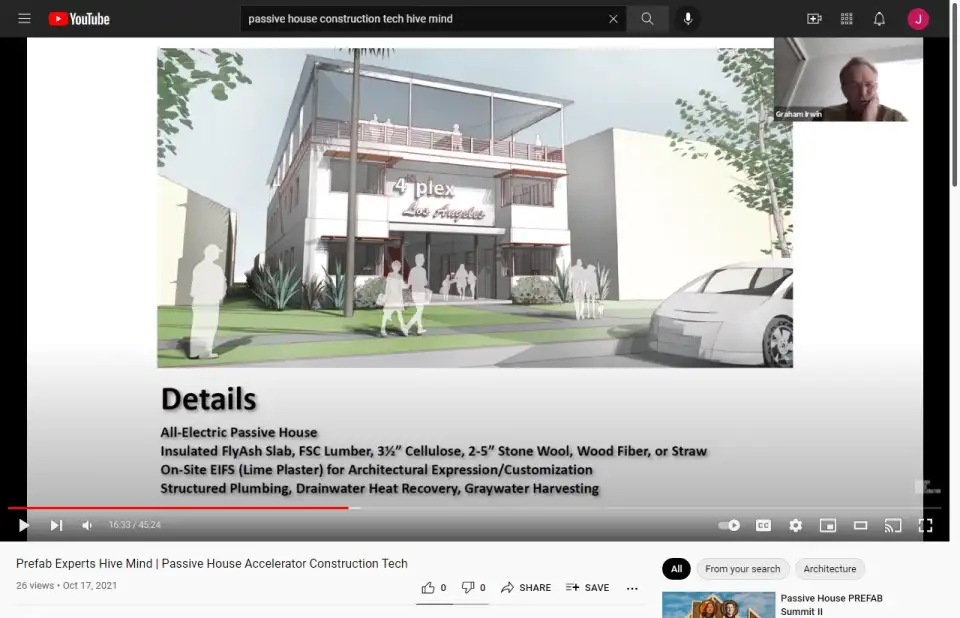
Graham Irwin:
Thank you, Alan. So I'm just going to give a sampling of the longer presentation at the conference, but this is a proposal for a, not necessarily modular constructed, but modular design multi-unit building intended for upzoning single-family properties, which is kind of the program de jure in California at least, and likely elsewhere. Basically, the plan here is all-electric passive house with low global warming potential materials. The suggestion here is that it could be lime plaster used on-site to allow some customization of the building even though it's designed in a modular way. And the idea behind this is a mass customization process so that there's economy of scale rather than this kind of one-off custom home. This is a mass production strategy: structured plumbing, drain water heat recovery, gray water harvesting, also add low water landscape.
On the roof is something that looks a bit like a funnel and it actually is a funnel. This is inspired from an earlier project I worked on. I've integrated the solar trellis more into the architecture. And so it's 55 kilowatts bifacial PV. It generates power both from the top and from underneath. And it's equivalent to covering 110% of the footprint. It's rain tight and it's sloped like a funnel for rainwater capture and there's an interior courtyard open to the sky in the middle and a roof deck, obviously under it. So it's shaded and protected from rain.
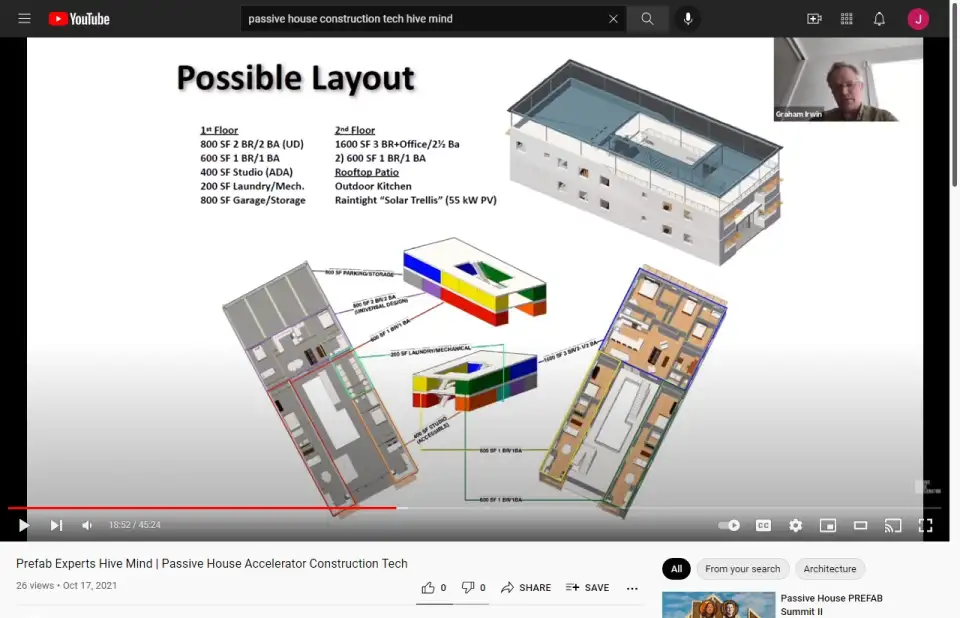
Graham:
Additionally, there's parking EV charging. The other thing about this proposal is that it's supposed to be two stories, but it could be stacked higher in the case of trying to develop transit where you need higher density. It could be stacked higher in strategic locations. Again, while this is a predesigned building, the idea is that it's a modular design, which affords flexibility for the owners of the building and the community needs. This is one example of a possible layout and the entire building is comprised of 10 by 20 modular units and you can sort of see the color coding there. This particular program has a studio, three one-bedroom, a two-bedroom, two bath, and a three-bedroom unit in it and four garages in the back.
I'll go into more detail with this at the conference, but I'm proposing this as an American Urban Renaissance with a triple win: providing more housing which we desperately need; a social equity component that I'll discuss in greater detail; and obviously the environmental benefits of Passive House, renewable energy, low global warming, potential construction, and water conservation. That's basically it for me and I will turn it over to the inimitable Tessa Bradley. Thank you!
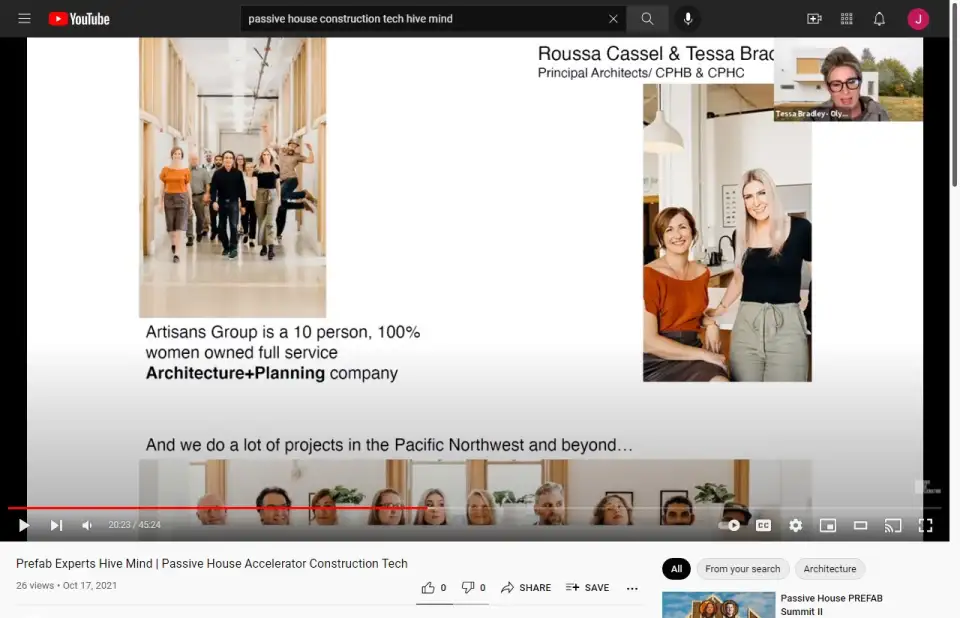
Tessa Bradley:
Thanks, Graham. Killer project. Much like Graham, I'm just going to give a sampling of the presentation that I'll be giving at the conference. I'm Tessa Bradley and I own the Artisans Group with Roussa Cassel, my co-principal. We're a 100% women-owned firm. We do architecture and planning, and we used to be design-build, but it prematurely aged me, so now we're only architects. My hair's white because of that. We do a lot of Passive House work. We've been involved in it from nearly the beginning and it's been a big passion of our company for a long time.
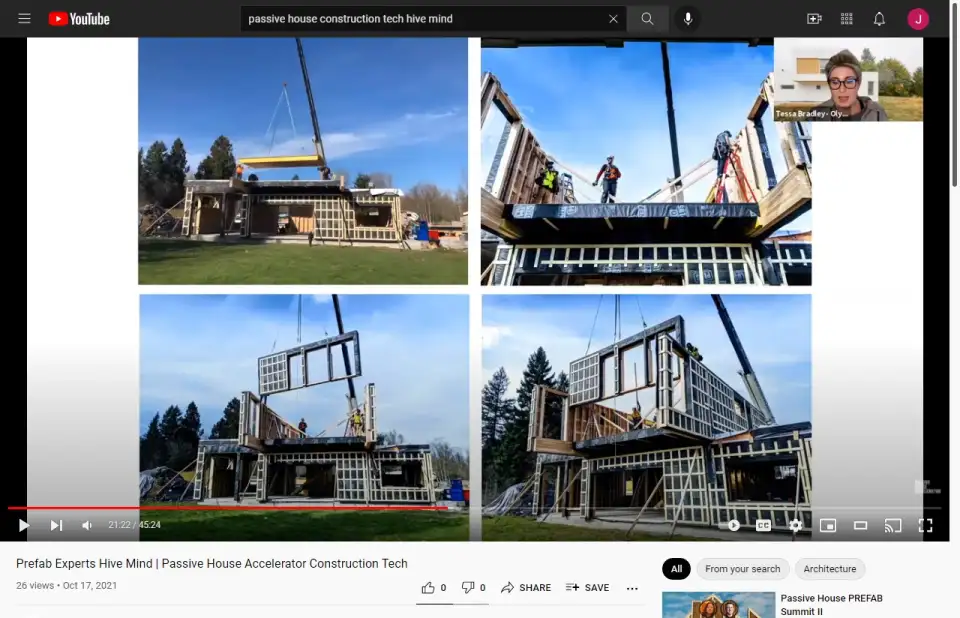
Tessa:
This project is a collaboration with Collective Carpentry, who I find to be a Northwest contemporary of Alan. They're much smaller, but they also seem to have a similar approach in that they do many bespoke panels for custom work and they're also constantly looking for ways to stop being so bespoke. Aren't we all? They're a really awesome company that we have collaborated on several projects with, one of which is this custom home outside of Seattle in sort of a more rural area called Auburn.
Here are the panels coming. They are a different assembly. They're a TJI assembly, even though they do look remarkably similar from the outside to some of the slides you saw Alan present. And you can see the start of the work here and their enormous crane required to do it. This house also has a lot of stupid things that you should not repeat or do, much like the kitchen bump out discussed earlier. It has cantilevers and beautiful soaring covered areas, and it is beautiful and simple. But anyone who has ever done anything in architecture knows that to make something look simple takes a lot of freaking work. So you can see the house going up from the bottom floor there; you can see the cantilever glue lamps that hold the flooring panels; and you can see the balcony to be as the exterior wall slides in place on that bottom right slide.
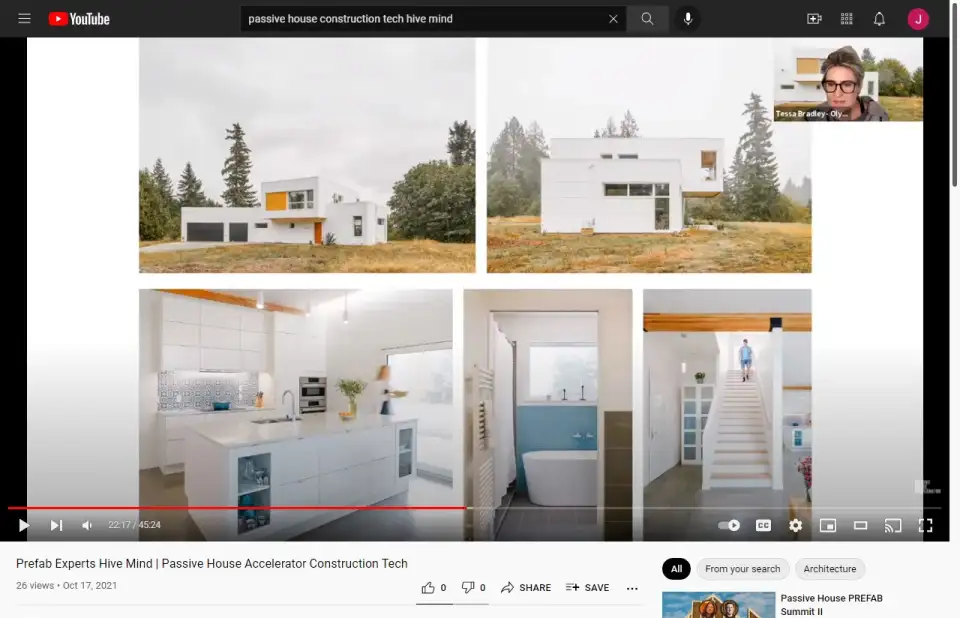
Tessa:
Here's some finished photos of the building. It, obviously, has not been landscaped yet as it is freshly built, but you can see that it has a very clean, almost austere aesthetic that stands in nice contrast to the dry weaving grass of its environment, as well. Several choices were made to keep this project really budget-conscious, as well. It's a really simple floor plan. It's only about 2,000 square feet and there's not a lot of complexity except for the cantilever.
The last thing I will say is that in our full presentation we'll be discussing the multifamily project that Roussa and I are co-developing together on some property that we have purchased. We'll be prefabbing that, as well, and that'll be a six-unit apartment that we'll be doing with Collective Carpentry. We'll be diving into that a little bit more and talking about some of the ways we see moving forward with prefab, to try and make it more cost-effective, and easier for your average Joe to purchase. Thanks very much! And with that, I'll give it off to Ilka Cassidy.
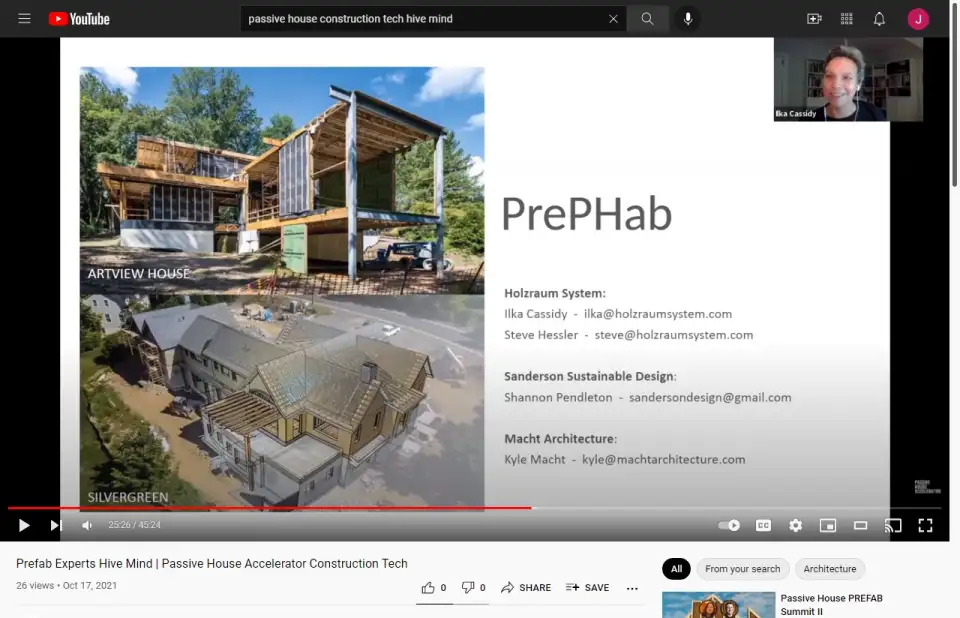
Ilka Cassidy:
Thanks, Tessa. Awesome project. Definitely been a fan of yours for many years now. So I'm also excited to be part of this panel and to be seeing everyone tomorrow or the day after in New York. I also wanted to say thanks for everyone to be presenting and just kind of sharing all their thoughts and progress and information with everyone because it's definitely quite a bit of work to put all these presentations together, but it's just so important to do that because that's how we learn. Our presentation sharing information is definitely a topic, as well. We'll be showing how we are turning a part space model basically into a visual database that can be used by everyone who's involved in the project and hopefully even beyond that.
Our group is Steve, Kyle, and Shannon, and we have been presenting together for a little bit now. Every time we get together and prepare for presentation, it's not a surprise that instead of the half-hour that we planned, we end up talking for two or more, which is pretty awesome because we definitely always just, again, share information, share what we've learned and just talk about how technology has been evolving, how thoughts have been evolving and how that really affects our thinking and what we are doing. I would say our upcoming presentation is definitely going to reflect all this evolving thought around our project, basically, but we are still focusing or talking a lot about kind of what happens behind the scenes of prefabrication or of the images of just final panels coming to the site because there is quite a bit that has to happen before that.
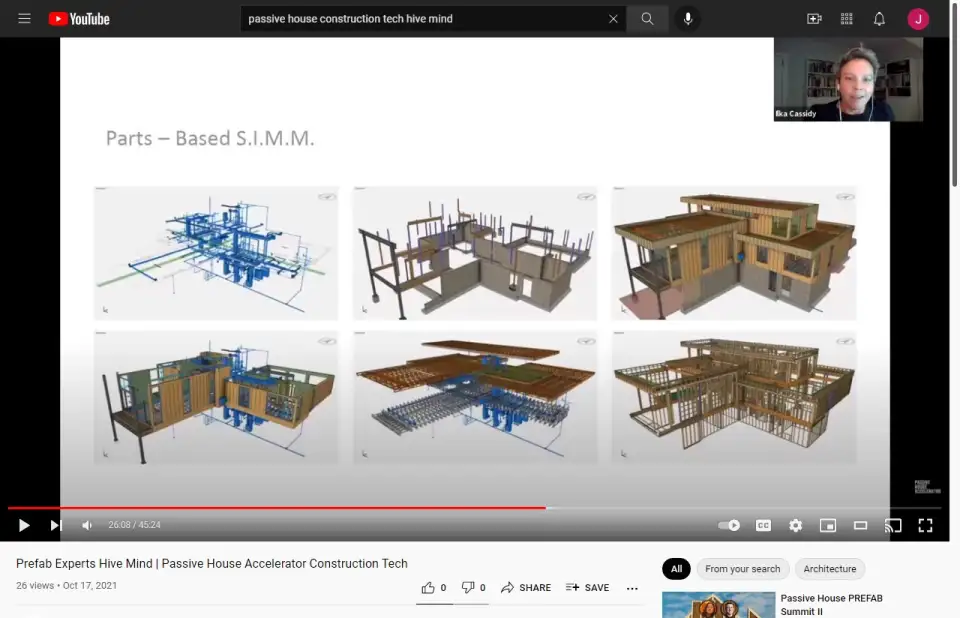
Ilka:
So what we've been working on is just developing this idea of a single integrated manufacturing model that just looks at the architecture or the project a little bit different where it takes design intent and really puts into parts and what kind of exploring what it does to the project and what the opportunities are to use a model like that. Steve, do you want to take it from here?
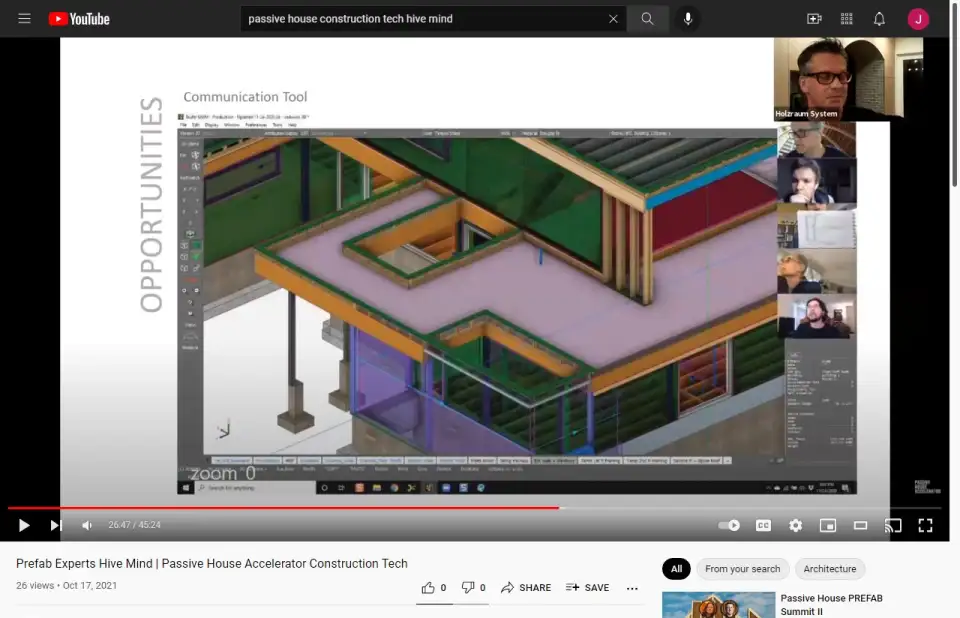
Steve Hessler:
I did also just want to repeat and say we're really excited to be presenting with all these people we've been watching for so many years. It's pretty amazing. The idea of this part space model we can't really stop thinking about it. We keep doing it with all these projects, and every time we bring more content in. We are thinking about how we can support pricing through energy modeling, through acquisition, through carbon quantification and installation, and through purchasing and ordering. It's sort of like the more parts that you put in the building, not only are you kind of cleaning up and resolving relationships that are going to happen in the field, but every time you have another part in there, if there's value to it, you can basically kind of add attribute values.
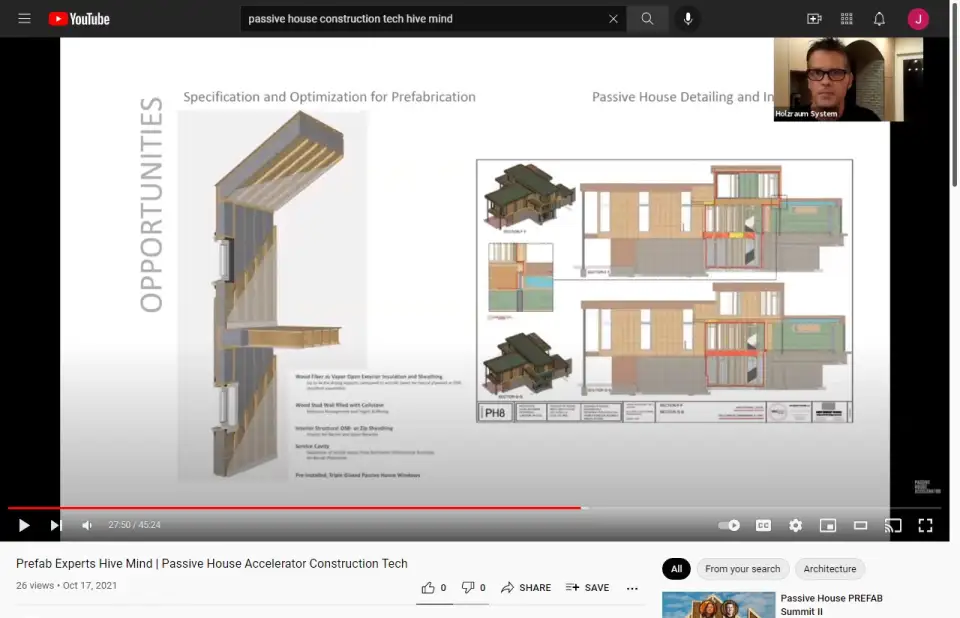
Steve:
The last slide was about sort of the visualization and communication that comes from these parts that are the real building, but one of the other opportunities besides just visualization is being able to work through the Passive House detailing with complex relationships and complex buildings because you've got everything kind of modeled out and you've integrated all the different perspectives like the MEP and the structural steel and the concrete. So, you can also sort of map out and visualize and sort of sell to client and team things like super low carbon materials. When we have them and we can quantify them and quickly price them and move them into projects because they're in our database, then we're finding it much, much easier. We almost never have conversations now with our clients about what's going to be in the building. We're able to specify.
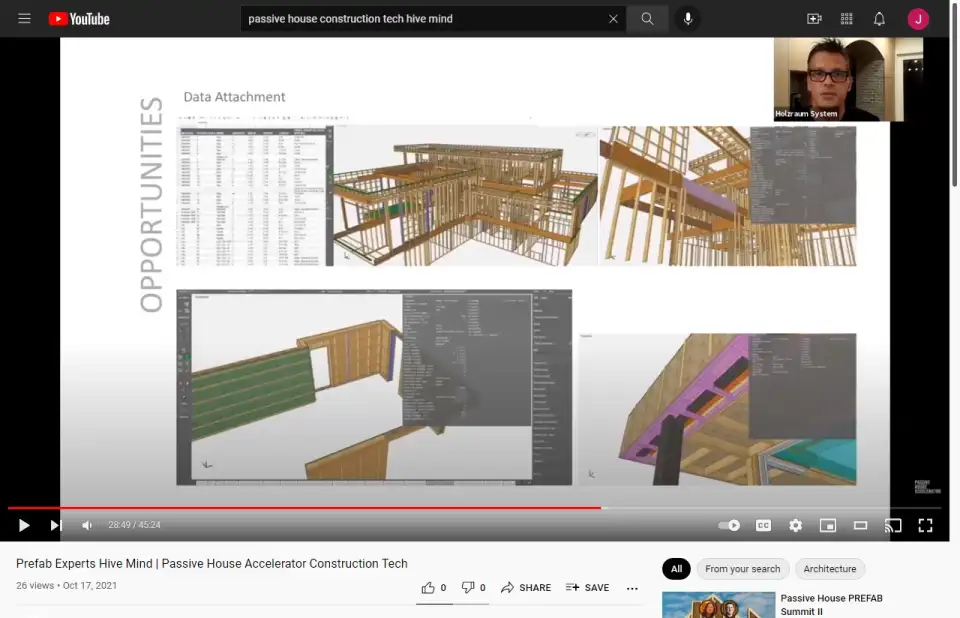
Steve:
Then we get to this data attachment, which is what I was touching on a little bit earlier. A lot of the software that a bunch of folks on this panel are using does this really well, just like our software. So it's not really a new thing to be able to attach data. It's just a new thing to do it and to think about it beyond just even this project. But we're starting to think about what could happen if you have buildings that have data attached. It could apply to even repurposing parts.
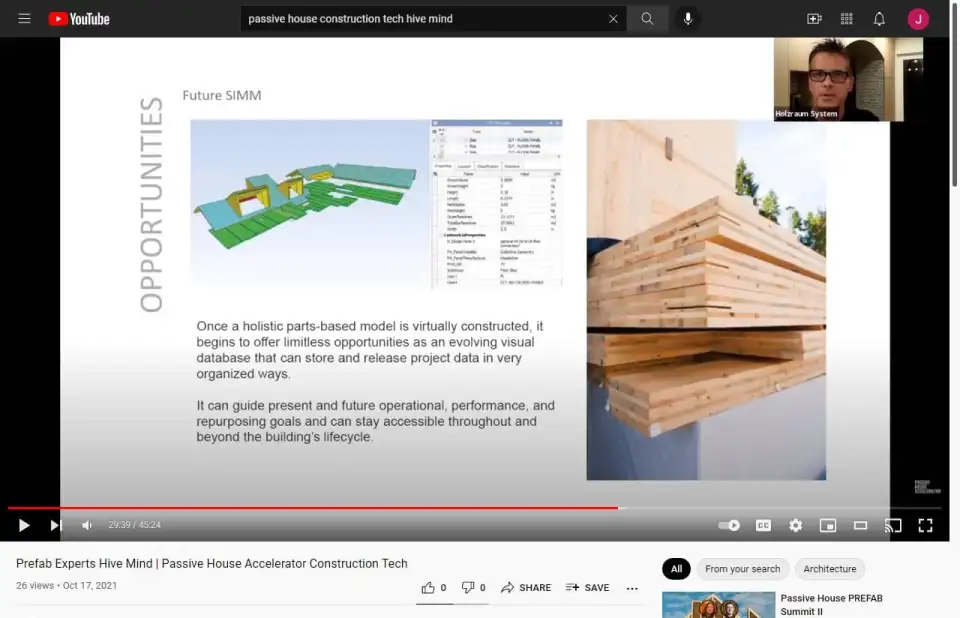
We've been working on developing a system to really get that data accessible, not just to our in-house team, like our project team, but we're thinking about the future. Essentially, through an IFC format or some other format, we envision these buildings that have very, very vast kind of layers of data that can apply to different perspectives. For instance, you could be looking at a stack of CLT that sits in a database somewhere, and if somebody's looking to repurpose a certain type of material, there's no reason right now why we can't have actual quantities in a public or private use library.
We're kind of already there in one way because we've really are putting together this mechanism to be able to very, very quickly, on a mobile device, access all the data in our SIMM models. What we've been talking about with Shannon and Kyle is why can't it go much, much further in the future in a very kind of universal fashion. So we're going to talk about that and we're really excited to be here and thank you very much. I'm going to pass it to Kyle.
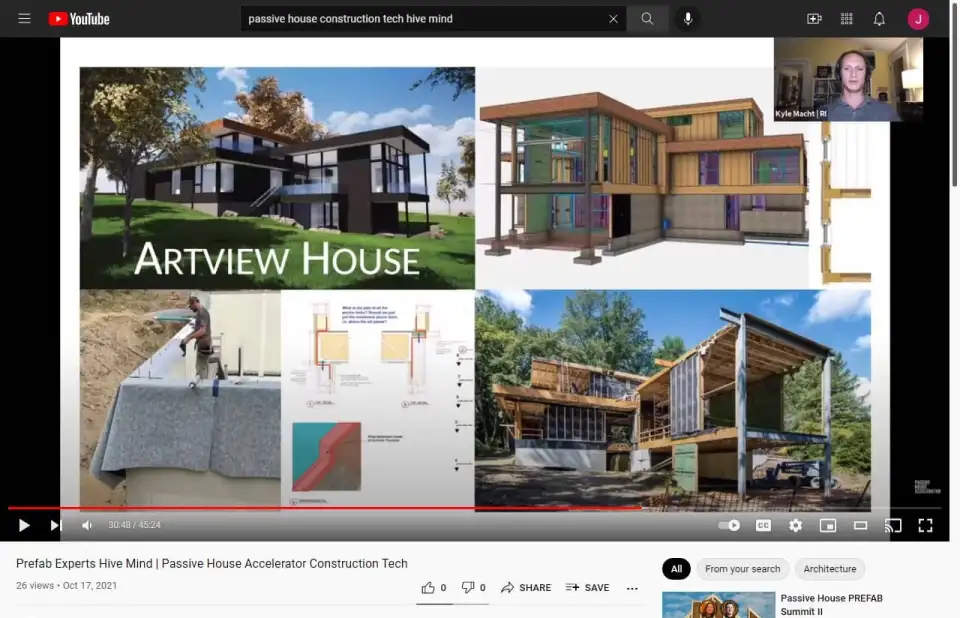
Kyle Macht:
Hi, everybody. I'm going to talk a little bit about the Artview House right now and we'll talk more about that on Friday. So we'll talk a lot about the prefab, but I also want to talk a little bit about connection details and the problems and challenges that came up. Once again, simple architecture but not at all simple; lots of cantilever pieces, huge overhangs, windows that you can't panelize and install on-site. They're not installed right now. This is pretty close to the bottom right image to what the site looks like at the moment. The overhangs are complete, but windows haven't been delivered yet. A couple things have been delayed, partly pandemic-related, but we'll get into some of those details.
One of the interesting details that we looked at was the foundation system, and we panelized that, as well. That was all offsite, thin concrete panels, mostly to reduce carbon emissions. Was it worth it? Maybe. From a carbon standpoint, it was. From an execution standpoint, there were some problems and we ran into some issues here and there. I'm not sure I would do it again after this project, but I'm hopeful and optimistic for the concept of it. There was a lot of different details of air control layer and all the different four control layers and how to wrap them around the different parts of the model and the actual physical building. But we spent many hours debating that and where should that control layer be.
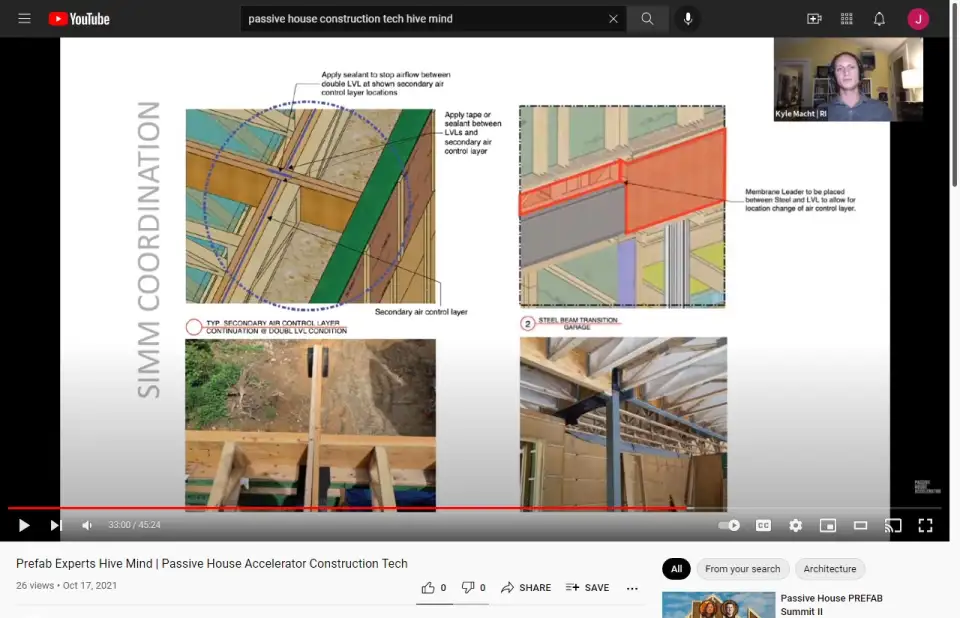
Kyle:
A couple of key areas that we spent a lot of time talking about that I hope to get into more later is how do we deal with all these penetrating beams and how important is the second air control layer or wind tight layer. That was a big topic of conversation. Our interior air control layer on the ceiling was underneath with all cellulose above it. And so, how important is it to seal between these two beams in the top left corner that's cantilevering outside of that control layer there? We went back and forth on a lot of this on how to execute these different details. We did have a few steel beams. We started out with maybe four times as many, and then redesigned things here and there to simplify and go with as much wood as possible.
This is like how do you take crazy...in Tess's words...stupid architecture, and make it as sustainable as possible, if you will, but still make it very cool, very sexy. It was what the client was after. We were very excited to do that for him even though panelization was sort of a wild case study here. It's not cost-optimized at all in this scenario. However, we were able to get a lot of high-quality precision, and I think without the SIMM, and really figuring out every connection detail in the computer first, we would've come to so many problems on site that just weren't foreseen and little things here and there that weren't figured out ahead of time. We'll be like, "Oh, I guess we didn't think about that." Or, "This came up."
So we're trying to hide all the duct work, no chassis, nothing in this house. So it's all trying to be going through the floor systems. It was a lot of complications that I think prefab solved, not from a cost standpoint but more from an execution standpoint. Part of it too was just the amount of sub-consultants on this project. It was more like doing a commercial project, even though it was residential, just with a lot of different teams, a lot of different people involved, a lot of different meetings every Wednesday. We'll have one tomorrow. Going through all the different phases and all the different bits of this entire project. And with that, I'll pass it off to Shannon to close out this presentation.
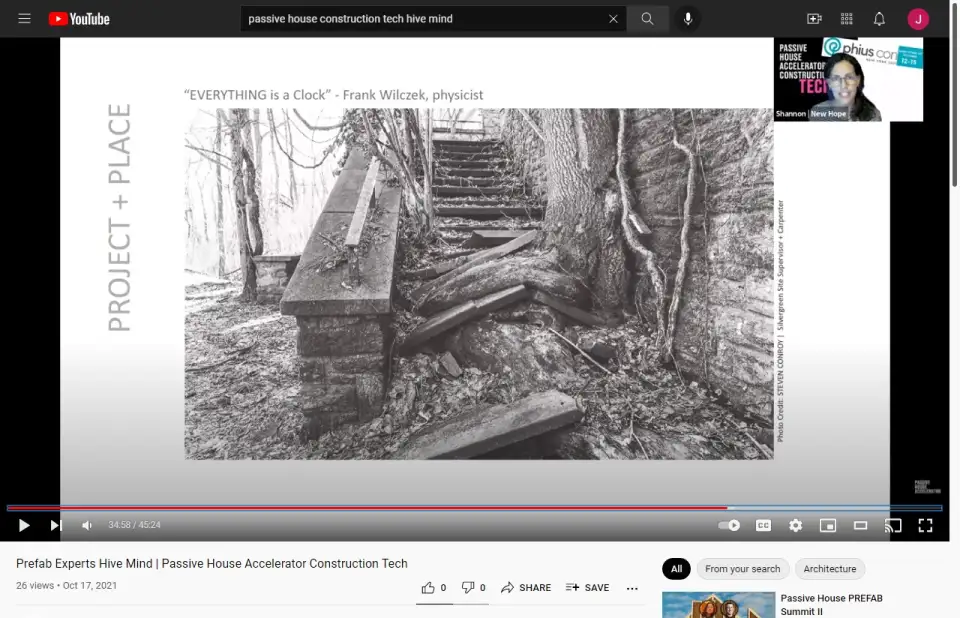
Shannon:
Thanks, Kyle. I appreciate that very much. We do have one more person after me. I'm here. I'm hoping Will Bloomer is here to follow me, but I just love this think tank, and I love that we're all talking about scaling up and bringing emissions down because Passive House looks like it brought us together. As Steve, Ilka, and everyone that we are constantly chatting with to figure out how to make better houses faster, we give an extra measure of care about what we do. So we're not just looking at operational energy; we're looking at embodied energy. We're looking at workforce development. We're looking at keeping it local or using a big manufacturer versus a small warehouse-based manufacturer.
When we worked with the SIMM model, which both Kyle and I did, it just kept bringing up opportunities for all those subjects and how we might use our 3D models after project closeout, right? So this is a wonderful picture that was taken by our site supervisor. And it shows that you just can't plan for everything, but sometimes that's pretty beautiful. So the project location is in Bryn Athyn, PA. This is the first Passive House there and in Huntingdon Valley. We're pre-certified, and we're about to become certified. We're just waiting for our renewable energy credits to come through.
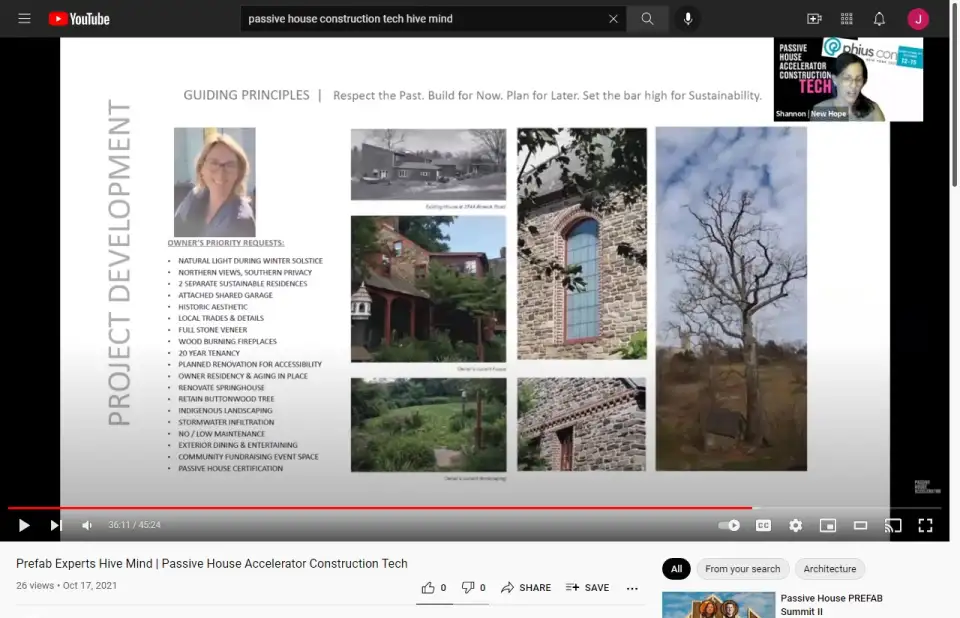
Shannon:
This is our owner, Susan, and she came to us with an existing project. You can see on the upper left, on the site, an existing home that she like to live in. On the left bottom two, source image from a community building nearby. In the middle and on the right, the oldest residents on our steeply sloped site, which is a springhouse and a 100-year-old Sycamore tree, if not a 300-year-old Sycamore tree. I missed the age. She came with a number of priority requests as well, along with her principles of respecting the past, building for now, planning for later, and setting the bar high for sustainability to set an example for the community.
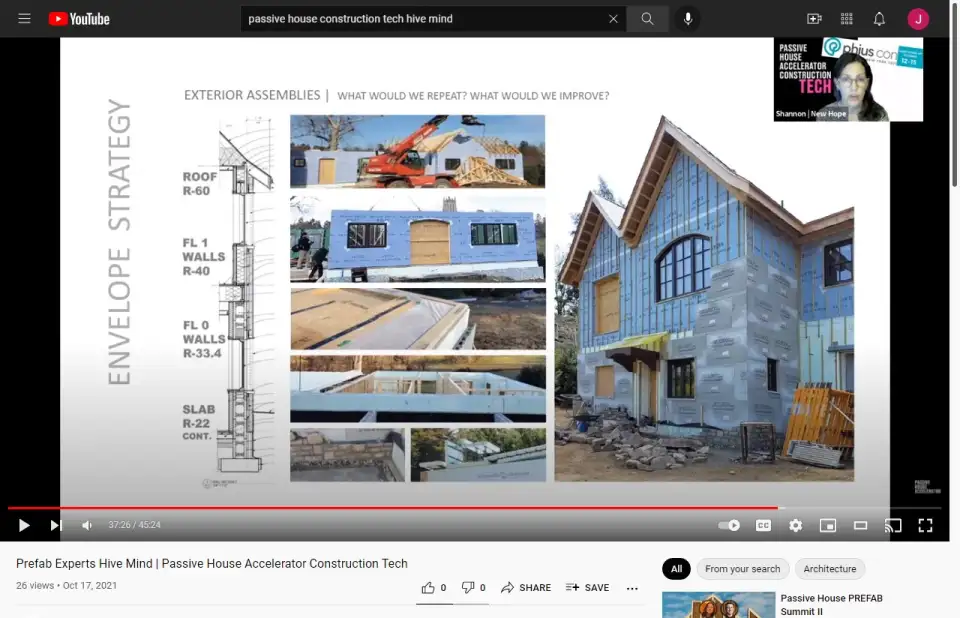
Shannon:
So we had a lot of strategies as we went through, but the most important that we had was to prefabricate because it allowed us to do a lot of things really well and not worry about some of the things that many of us had not done. We had Passive House experts on our team, and we also had Passive House newbies, and a lot of the windows that we were using in order to blend in with the surrounding architecture were really, really difficult to source, first of all, because the mullions and muntins were such a tough thermal bridge in the window, but also because the air ceiling was really challenging for all of these large openings--the Northern views, the Southern privacy that we had to maintain on the site. So, we prefabbed after we got our slab in. We prefabbed our interior lower-level walls, which you can see on the bottom and then our floor decks, as well, and you can see our air barrier coming up over those and being placed under the plate. Above that are upper-level walls coming in to sit on top of our Nudura forms, filled with concrete. Those all had pre-installed windows. The only things we didn't pre-install were the really big door assemblies, which couldn't be done in factory, so we did these on-site. And then to top it off, we brought in the roof trusses. For the system strategies, we basically have a 20-year planned renovation and then a 40-year planned turnover. So even though everything on this job is custom, it's really thinking about building a house that will last for 300 years in a place that is surrounded by a historic national district and a lot of water challenges.
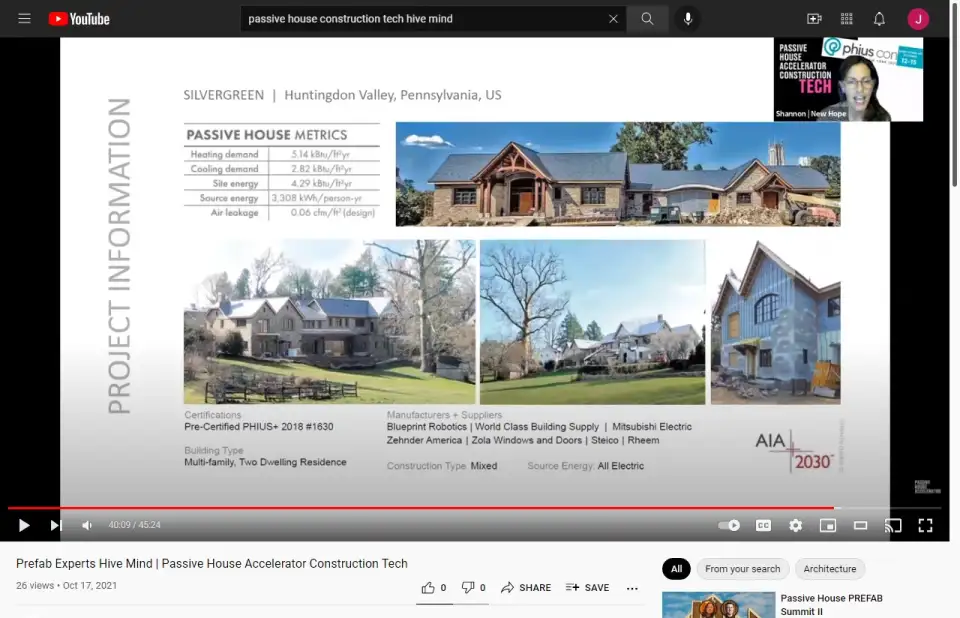
Shannon:
In order to do that, we kept our system strategies the same through all of the phases. The only thing that changed is, right now, we're using renewable energy credits to reach our zero target for energy source. But we do have conduit to the roof and we have our shutoffs in place for the solar panels. We have provisions for a solar shingle coming, and we've blocked out room for the batteries and the charging stations for the cars. All of the penetrations that are through the envelope right now are not going to change. So, we have all the systems in place, all the plumbing in place for all the future renovations, and that was part of the plan.
It was very hard to think that far ahead, and many team members questioned us along the way because they just hadn't done this before. Our client really challenged us to think for three generations, at least if not more. And so our question became, if not us, who? And if not now, when? And every time we ask those questions, we came up with answers. And so this is the project. These are getting pretty old now, but it does show this steep slope site and our Passive House metrics and our 2030 commitment, as well as some of the beautiful combinations of details from the prefab to the site built to give this envelope an impenetrable, robust, resilient nature as it changes residents and functions over time. Thank you so much with that. I am going to hand it off to Will Bloomer from David Baker Architects.
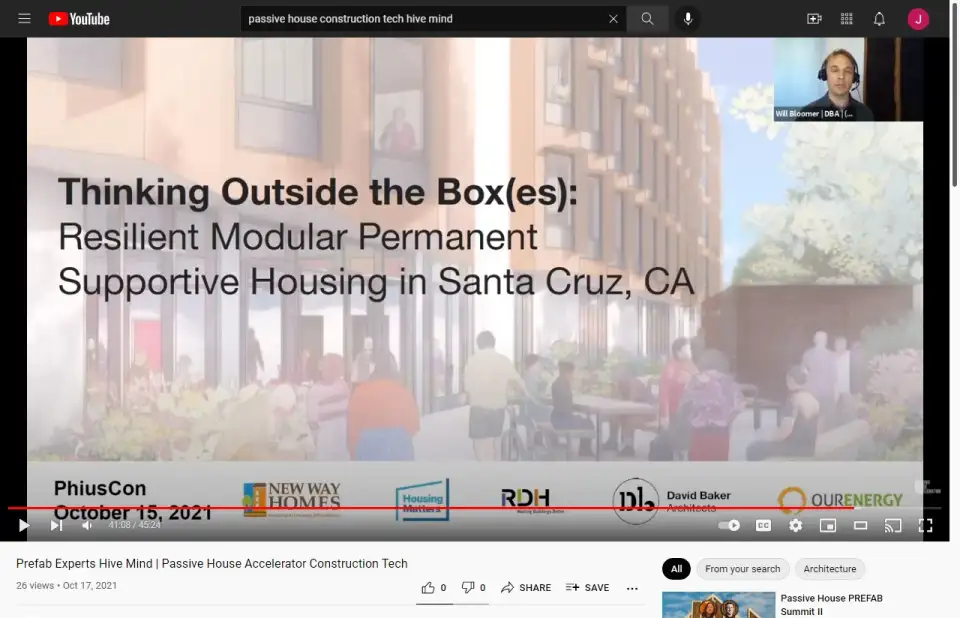
Will Bloomer:
Thanks, Shannon. I guess I will be closing it out, so I'll do my best before our chat. I am Will Bloomer and I'm an associate and also Passive House Consultant at David Baker Architects. I'm a firm leader on all things modular design and construction in our office, and I've been leading this project since 2018. Friday at PhiusCon, we will present Thinking Outside the Box(es): Resilient Modular Supportive Housing in Santa Cruz, and we're presenting alongside New Way Homes, Housing Matters, RDH, Our Energy, and our firm, David Baker Architects, which is located here in San Francisco. We at DBA are multifamily modular experts and create homes for people with a focus on design and sustainability. I'm really sorry that I won't be able to be at PhiusCon this year but excited for those that are and excited to participate virtually from afar and really to learn from you all.
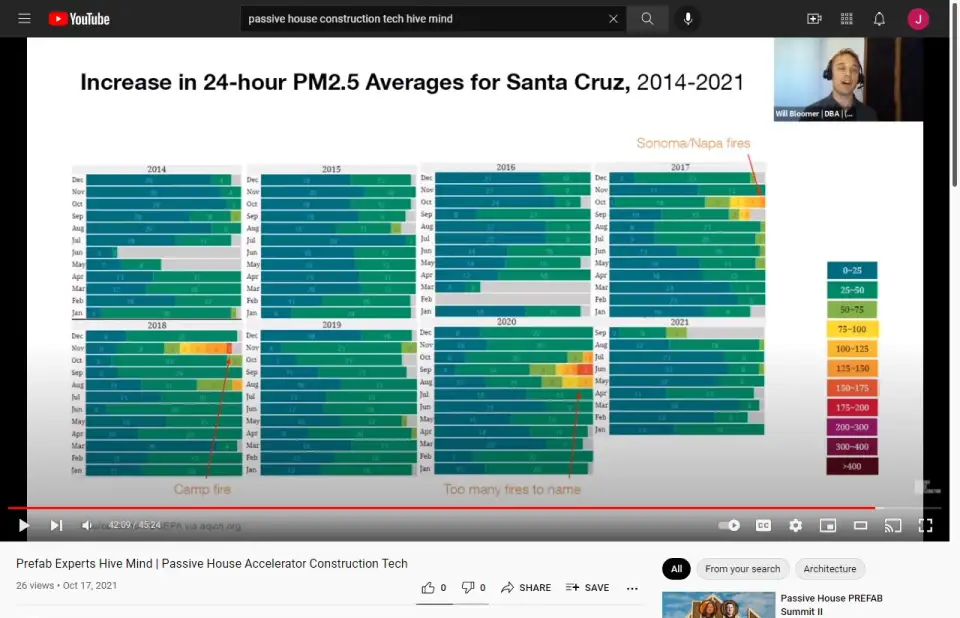
Will:
We only have a couple minutes today, so I just wanted to highlight a handful of items that we will hit on Friday at the conference. Harvey West Studios is a permanent supportive housing for formerly homeless individuals, so the first focus that we will hit on is resilience both from a health and energy perspective and also resident wellbeing. California and the US overall with climate change is experiencing an ever increasing struggle with fires and the associated toxic air quality, power outages, and grid disruptions. You can see the air particulates in Santa Cruz from recent fire events in 2017, 2018, and 2020, and it's just something that we were really aware of in starting this project.
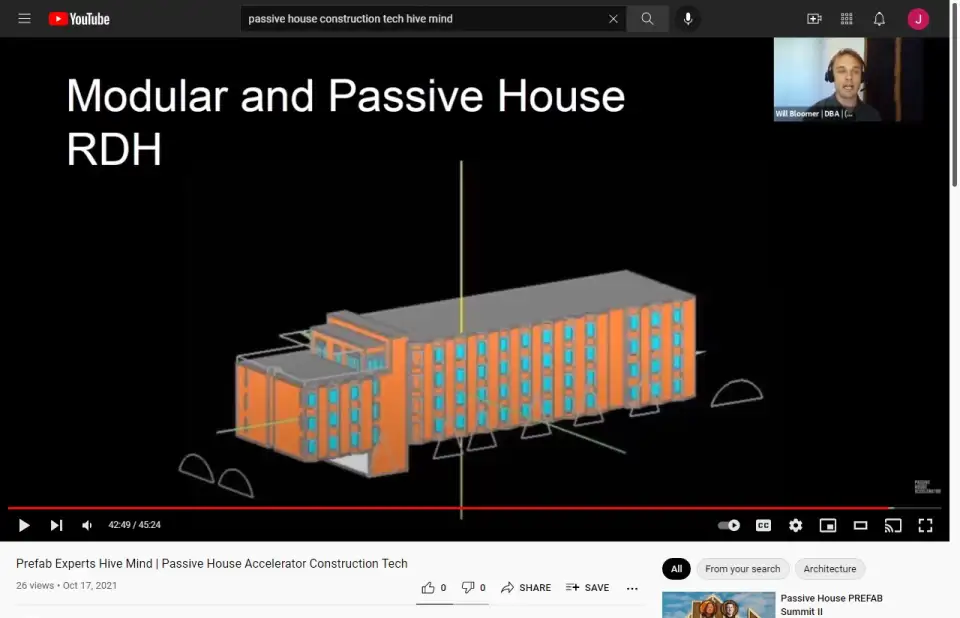
Will:
All these dangers led us to consider Passive House from the very beginning of discussions with our clients, which we were impressed and thrilled with. That's something that's rare for us and we were really excited about that opportunity. Phius was a way that we could prioritize health and maintain low operating expenses for our nonprofit client, and RDH has been our partner on Harvey West Studios. They'll be presenting along with me, and we're excited to share a little bit more of how we're using Phius and how modular has been an asset on this project. With volumetric modular, we have the possibility of better factory quality control and a shortened construction timeline and cost, but I also really want to stress that it is not a silver bullet and it hasn't been and something that I'm sure you all are very aware of in all the projects that you've shared today, which are really beautiful.
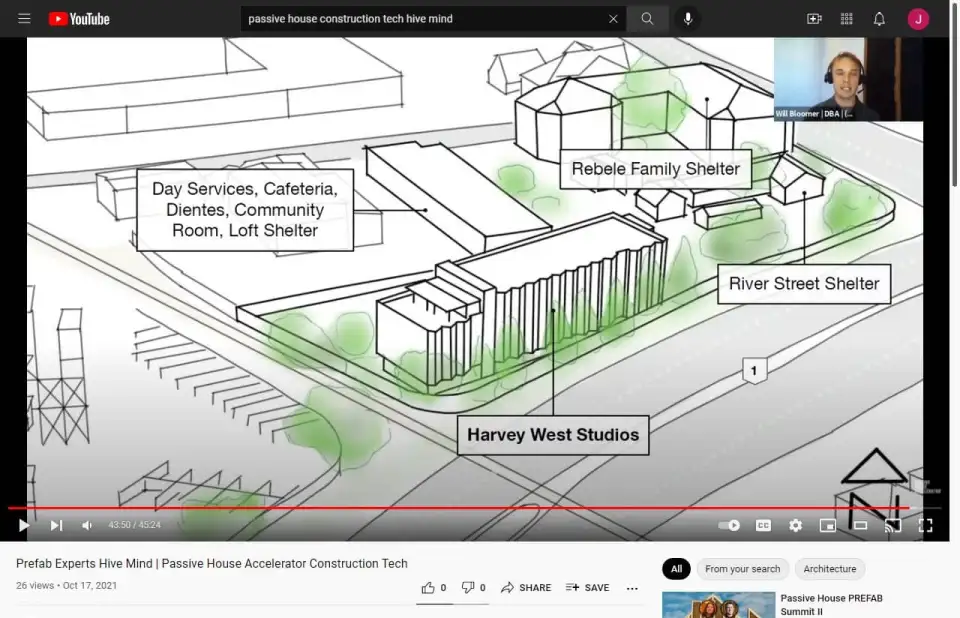
Will:
Here is the project. You can see how Harvey West Studios is located on this Housing Matters campus and all of the associated campus services, which is right next to the highway. The project was designed for volumetric modular, and it has always been a simple massing that simplifies the envelope for Passive House and focuses views to the ocean and also the hills behind it. Our Energy will be there and they are the owners' consultant and they're looking at campus-wide energy backup solutions that is something that we're really excited about, and hopefully, we can implement in the project.
Our presentation will cover four main parts that make up our solution. Each of them go together to support a Passive House, permanent supportive, modular housing. It is this combination of zoning reform, non-traditional financing, modular construction, and Phius, which all make the Harvey West Studios the innovative project that it is. Hopefully, you guys will all join us Friday, and we can learn more about these four pillars together. And you can learn more about the project at buildingwithpurpose.org or at our website, dbarchitect.com. And I'll also be sticking around in the chat and would welcome any questions. So, thank you so much!