It’s no secret that British Columbia has been charging ahead on delivering Passive House buildings in North America. So why would their institutions of higher education be any different? The Skeena student residence at the University of British Columbia’s Okanagan Campus is Canada’s first completed Passive House student residence. Jamie Harte, associate architect at PUBLIC, joins us on Passive House Accelerator Live to talk through the UBC Skeena Student Residence. The six story building will offer 220 bedrooms and amenity space to students at the Okanagan campus (check out our full case study here). Jamie is a Passive House designer with notable projects under his belt such as the Vienna House Social Housing and a multi-unit residential project in Squamish, BC. During his presentation Jamie dives into lessons learned and keys to delivering high quality Passive House design and construction on a tight deadline. You can read the transcript for the video below!
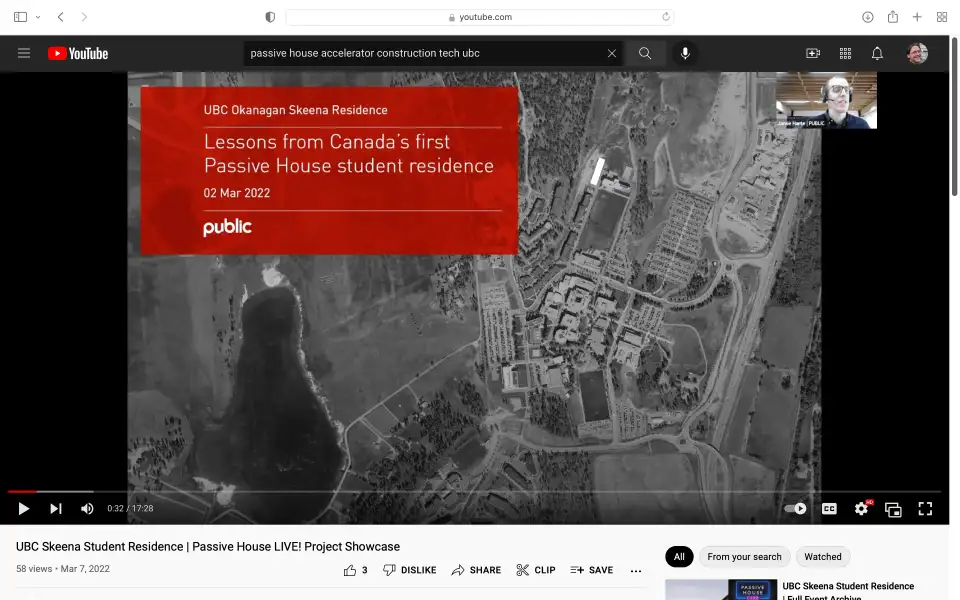
Jamie Harte:
Okay. I'd like to thank Passive House Accelerator for the opportunity to speak to you this afternoon. I've learned a lot from these sessions over the last two years, so it's really great to have the chance to pass on some of our experiences. And as Beverly mentioned, I'm going to be talking today about a student residence building, which we completed about 18 months ago, back in 2020.
First, a little bit about me. I'm an architect and a certified Passive House designer at Public Architecture & Communication in Vancouver, BC, which as some of you may know, is the unceded, traditional and ancestral territories of the Musqueam, Squamish and Tsleil-Waututh Nations. And so Public is a multidisciplinary practice which combines architecture and communication design. We're a medium size outfit with almost 30 people. And as the name implies, we're mainly focused on projects which benefit public life so whether that be public institutions, public housing, public infrastructure and so on.
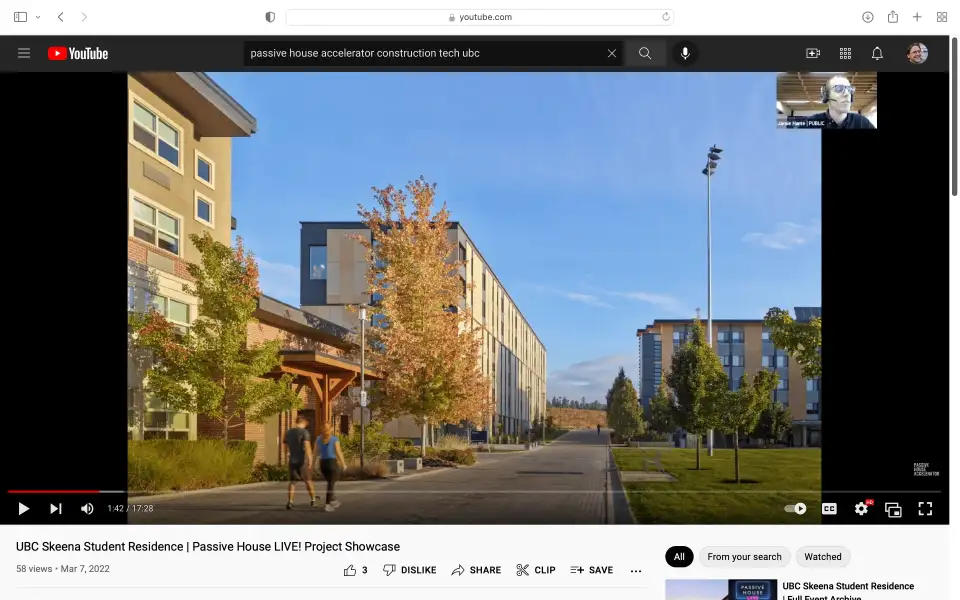
The Skeena Residence, it's a first Passive House project for the University Of British Columbia. It's located at their Okanagan Campus, which is a growing institution in Kelowna. It was also a first Passiv House project for us as the architects and the contractor as well. It was completed in August 2020 through the early months of the pandemic. And an important thing to note is that the nature of student housing is that completion before the middle of August is absolutely essential, so if you miss that deadline, you essentially miss an entire academic year, so failure to meet the schedule is not really an option.
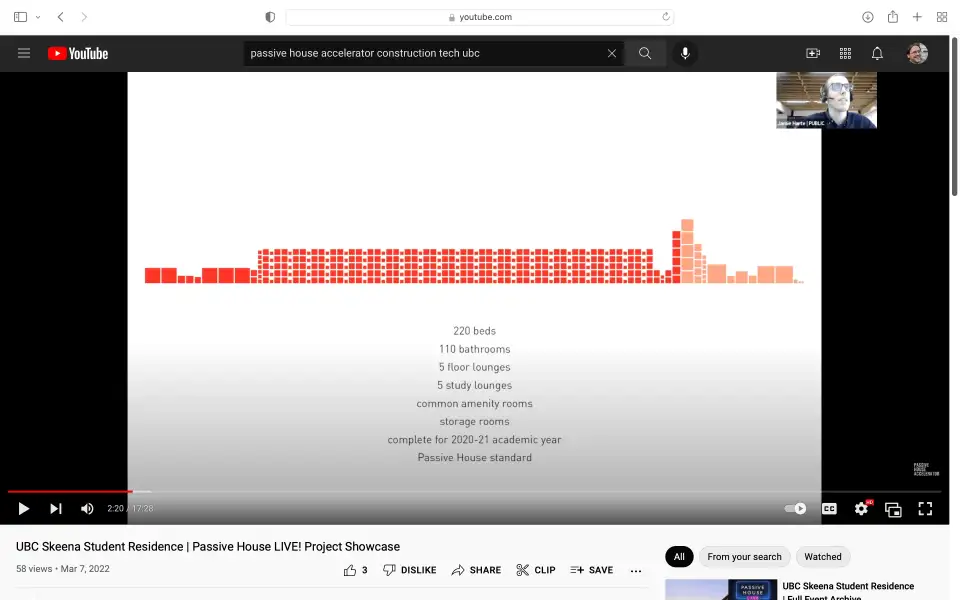
So here's a look at the program or the brief from the client. So it's for 220 student beds with 110 bathrooms, so bathroom shared for each two students. And then we've got study on social lounges on each level, common amenity rooms and storage rooms on the ground floor. That would be complete for the 2020 to 2021 academic year and built at Passive House standard. So, as I mentioned, the project is located in Kelowna, which is about 400 kilometers from Vancouver and about a five hour drive. It's in climate zone five so it sees bigger temperature swings from winter to summer than we see here on the coast. Kelowna also experiences more regular wildfire smoke and air quality advisories, which is an increasingly important factor when choosing to build to Passive House standards. The distance also became a challenge during the early months of COVID when air travel was suspended, because many of the consultants were located in Vancouver. Thankfully we'd already engaged the local Passive House designer, Brett Sichello from Nido Design, who was able to provide additional field review support for us during the project.
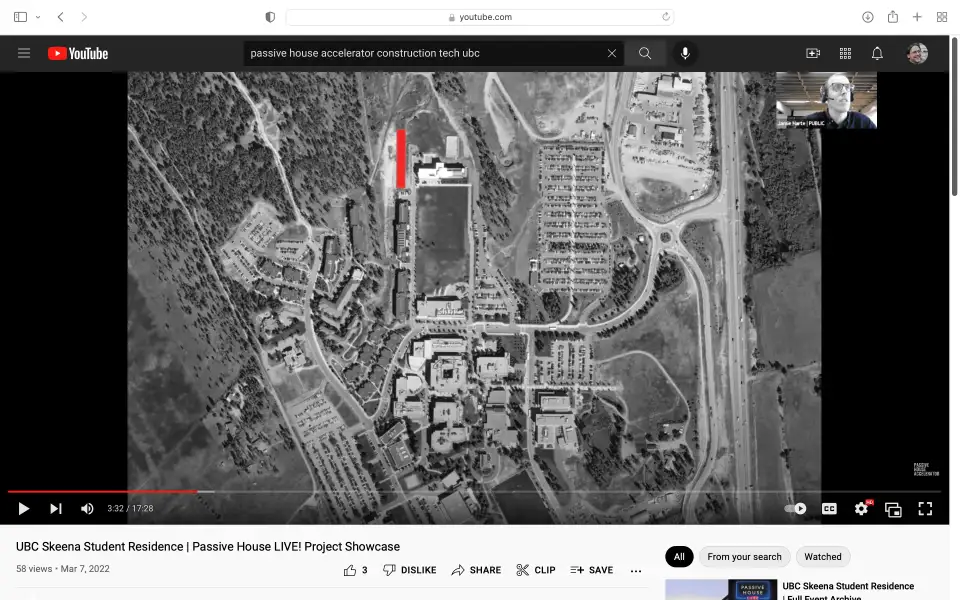
So in red here, you can see the location of the Skeena building, which is in the Northwest corner of the campus. It's backing into a forested hillside to the west, which provides some useful shading from the setting sun. The north-south orientation of the building was set by the campus master plan and the building completes a sweep of student residences facing a large common field for activities.
So the form of the building is really a rational response to the program from the client and then the constraints of the BC building code. So in this part of the world, light wood framing is generally the most economical method for building a mid-rise residential building and the code controls, the maximum dimensions allowed with combustible construction.
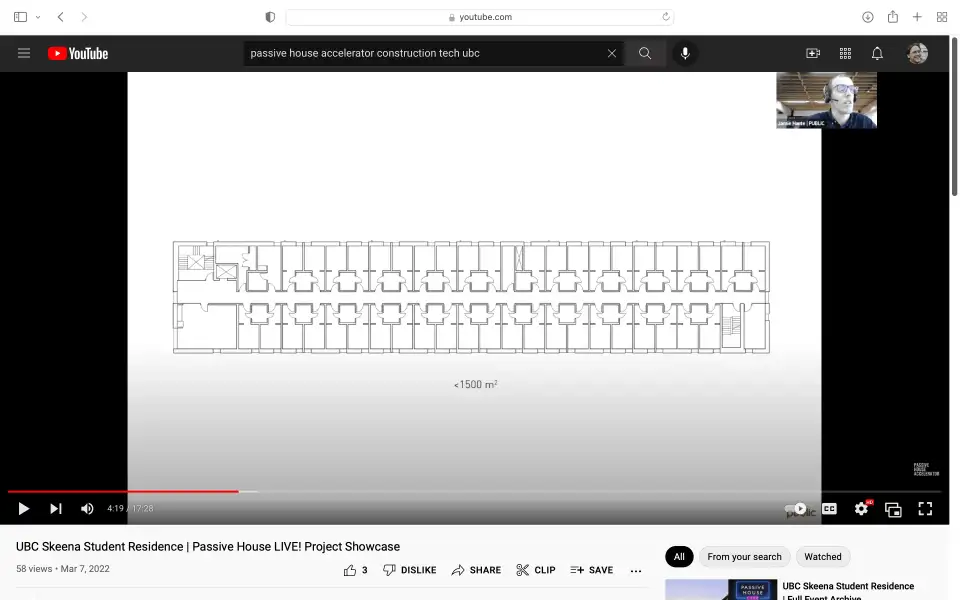
So we have a typical floor plan area which is less than 1500 square meters, which allows for 44 student bedrooms and the associated social and study spaces on each level.
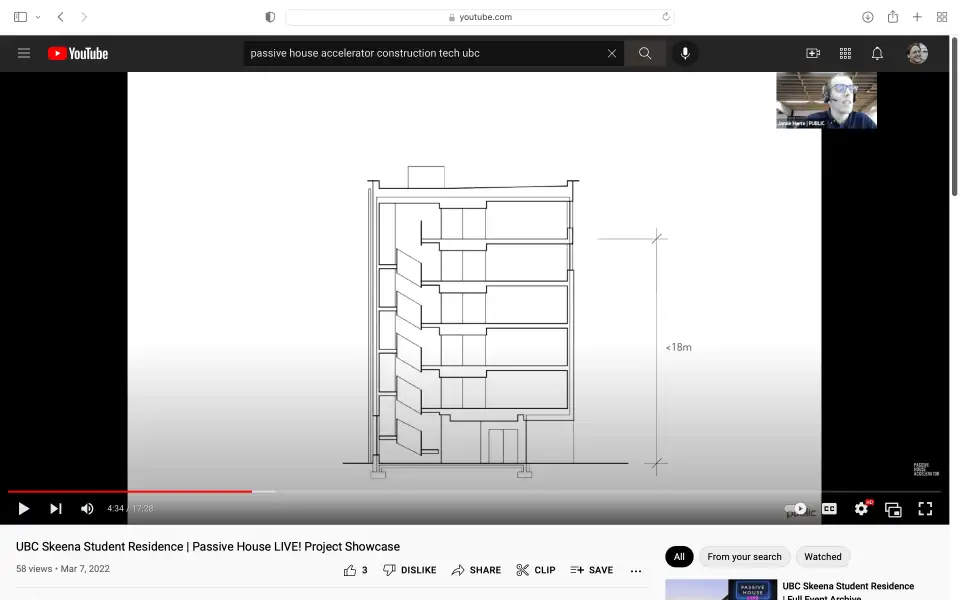
We also have the maximum permitted six story height and just under 18 meters to the top floor. By being less than 18 meters, that this height also means that the project avoids high rise building requirements such as pressurization and venting of the exit stairs, which could complicate Passive House air tightness. It also avoids the need for emergency diesel generators for the elevators. So the adherence to the constraints of the building code and the repetitive programming of the student rooms set us up for a very simplified massing. The challenge after that was defined an architectural expression that could ground the building on such a simple building form in its surroundings and express the function of the building in an honest way.
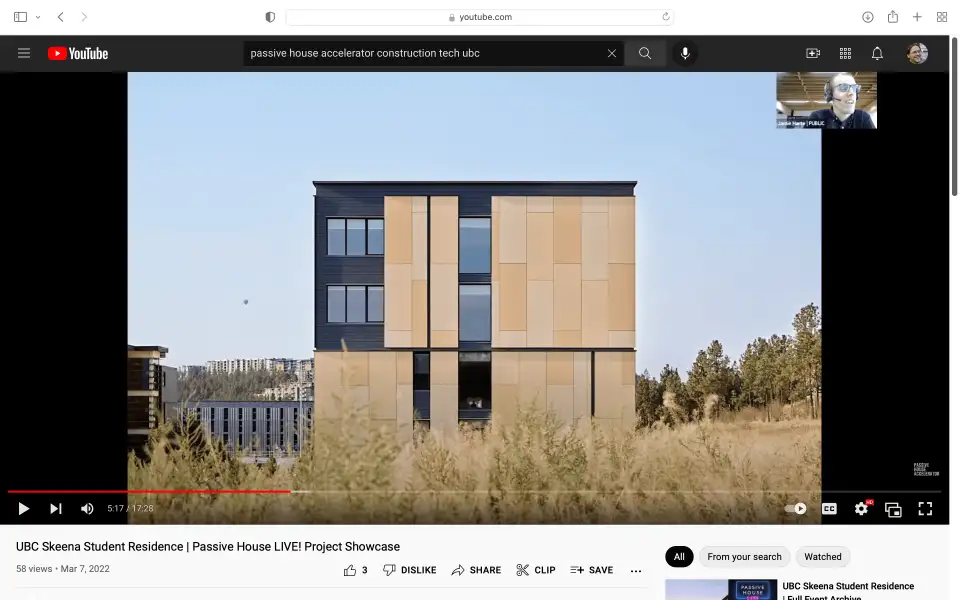
So here we can see the north elevation of the building. And once you can see a hot air balloon in architectural photography that has not been Photoshopped in, it's just a happy accident.
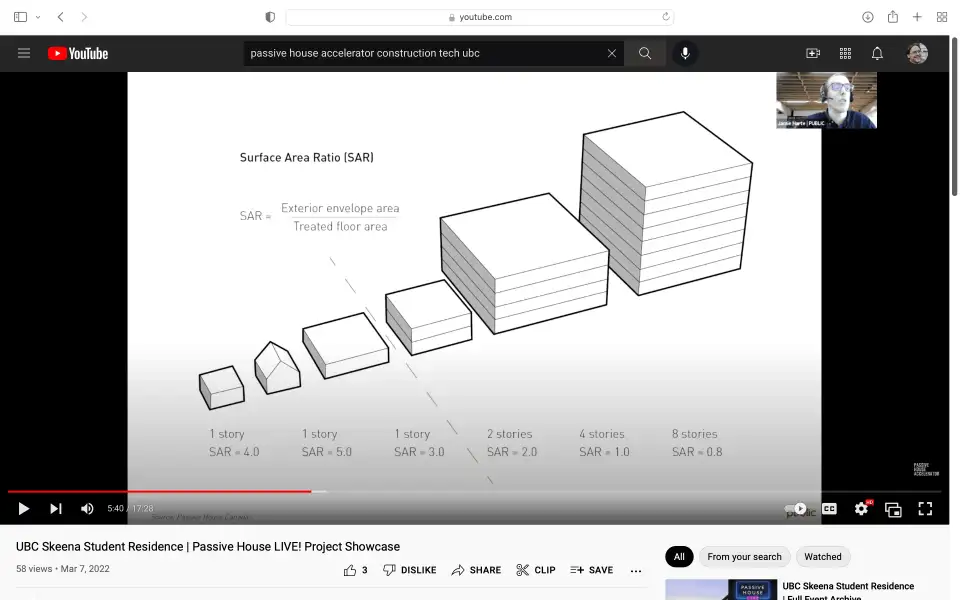
Many of you will be familiar with the importance of a compact building envelope when it comes to minimizing heat loss and beating the Passive House standard. Of course, many different building forms can be built to the Passive House standard, but in order to do so affordably, you need to consider the form factor very early in design. We can express this compactness as a surface area ratio, which is the exterior surface area divided by the treated floor area. Roughly speaking, when your result is less than two, then you're on the right track to affordable Passive House design.
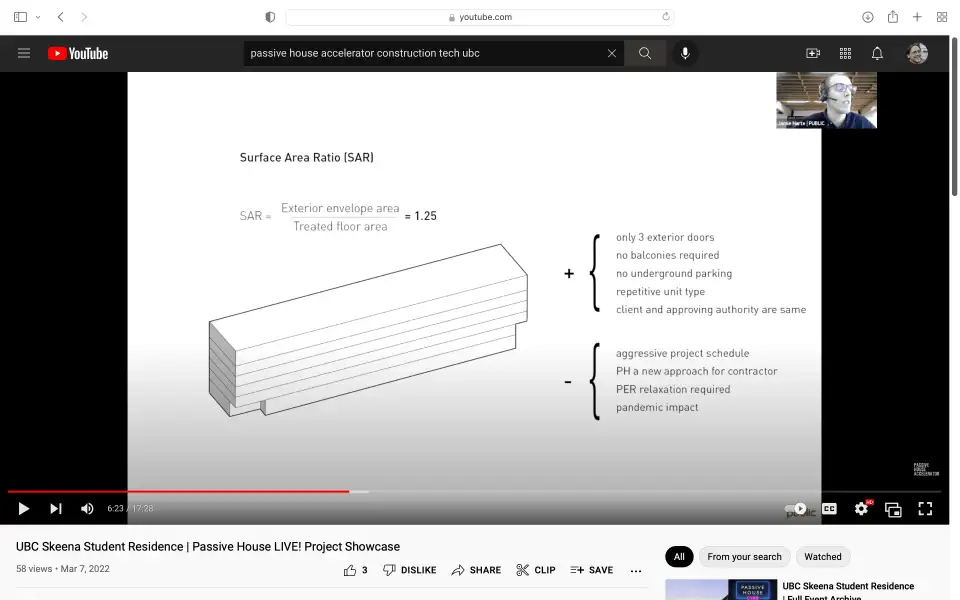
So for the Skeena project, our surface area ratio is 1.25, which reflects the simplicity of the massing. Although it's a fairly long and narrow form in plan. The only real creases in the form are to create entry canopies at the south and north and otherwise it's a pure extruded rectangle. In addition to the simple form, there are a number of advantages for Passive House that come with student housing typology in general, and with our program specifically. So we've only got three exterior doors in the building. We have no requirements for balconies, it's not generally required in this type of project by this type of client. We have no underground parking so vehicle parking is taken care of elsewhere on the campus. We've got a repetitive unit type which helps with planning mechanical systems and so on. And then also in our case, the client and the approving authority are one and the same. So the campus, I was able to facilitate approvals for a building which is much more simple in its massing than precedent buildings around it. And then a few challenges for the project. So we've had a very aggressive project schedule with a immovable deadline. The fact that Passive House was a new approach for the contractor. We required a relaxation to the primary energy targets for the building, which is pretty common for densely occupied multi-unit housing projects. And then also the pandemic impact, which was a unforeseen and unforeseeable challenge.
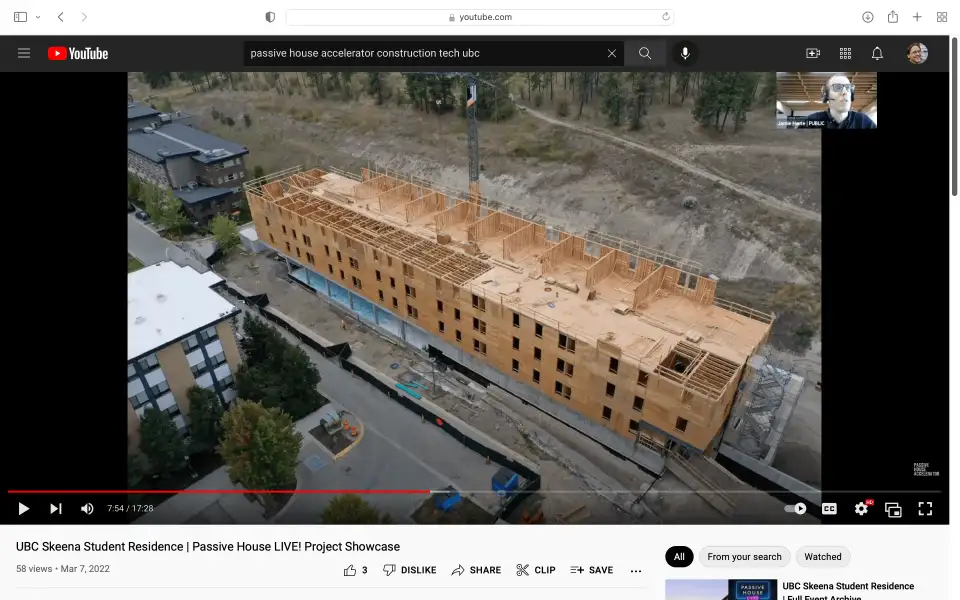
So our approach to the building structure and assemblies was to as much as possible use systems and assemblies that were familiar to trades who work on mid-rise, residential buildings in Kelowna. This was in order to ensure competitive hindering of the work and also to guarantee that we could meet the project schedule. So the bones of the building are totally conventional, light wood framing for the walls and wood I-joists for the floors and roof on top of a concrete ground floor. The on-campus location also provided a lot of set down space for materials so the framers were able to set up an onsite prefab space and just crane sections of wall into place.
Although the project brief from the client firmly committed to the Passive House standard, in reality the final approval for the project budget from the board of the university and their authorization to construct would come only after tender. And so there was always maybe small chance that the Passive House element of the project could be removed just before issuing drawings to our construction which could be a major problem for the design team. This was a known risk so we took steps in design to protect the project schedule as best we could.
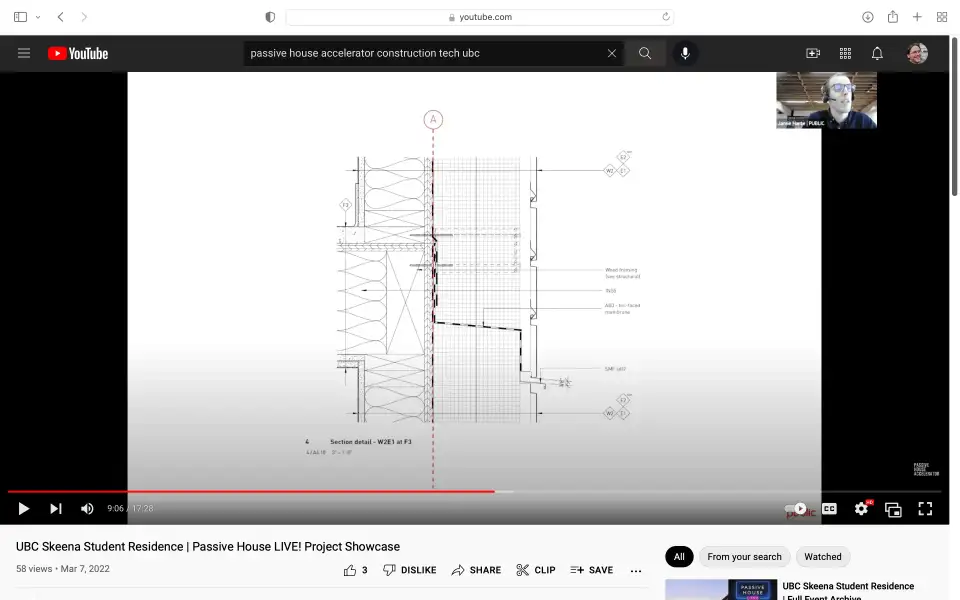
So if we look at the wall assembly, everything to the left of grid line A is standard wood platform framing which is then wrapped in a Passive House jacket on the outside. We have eight inches of exterior Rockwool Insulation and the clouding supported on a thermally broken clip system. Air tightness is provided by a vapor open membrane on the outside of the structure with a vapor retarding primer on the interior dry wall surface. This approach meant that if Passive House was ultimately asked from the project, we could have reduced the exterior insulation thickness as needed without any significant knock on effects. And the structural framing could have proceeded on schedule, thankfully that wasn't necessary.
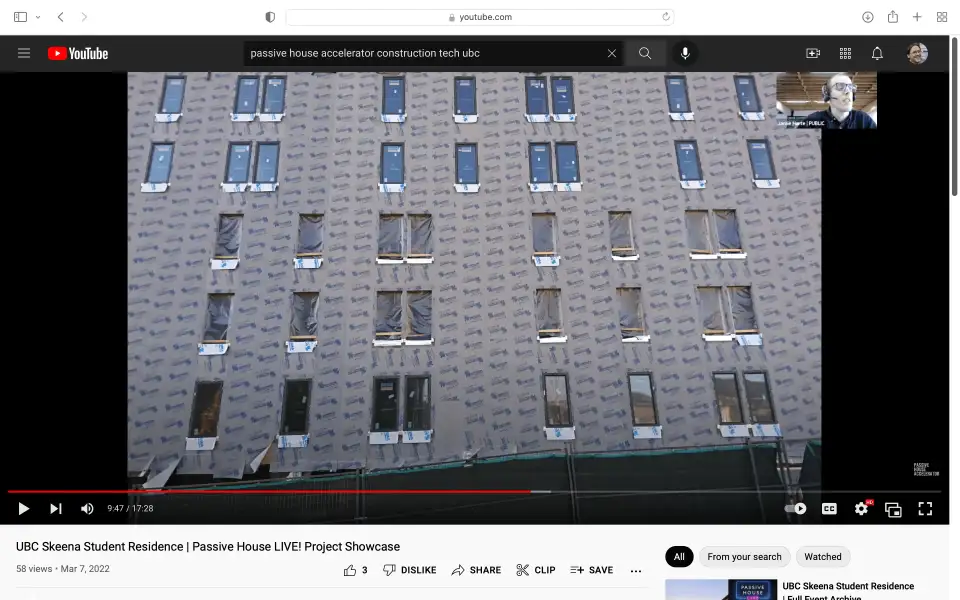
It was also important for the success of the project, that there was a single point of responsibility for all the work from the wood sheathing outwards. So that meant a single responsibility for the air barrier, exterior insulation and finished cladding of the walls. And in this case, that role was performed by TRS Building Envelope in Kelowna and they were certainly a key part of the success of the project. Here, you can see the air barrier in place and windows beginning to be installed. The simple building form meant that the membrane could be continuously rolled down all five stories of the wood framing and it's easy to inspect and repair if any damage occurs or if air leaks are identified. And here we could see the next phase which is the adding of Cascadia fiberglass clips and steel grids to support the cladding, eight inches of semi rigid Rockwell is then installed between the clips.
This is our final blower door test, which shows a result of 0.08 air changes per hour, which is a really phenomenal result for a crew working on the first Passive House project. This would make it one of the most air tight buildings in the country in fact. And I think it's really a testament to the diligence of the trades and the construction manager, which was Sawchuk in Kelowna. The simple air barrier detailing and massing of the building were also a really important factor.
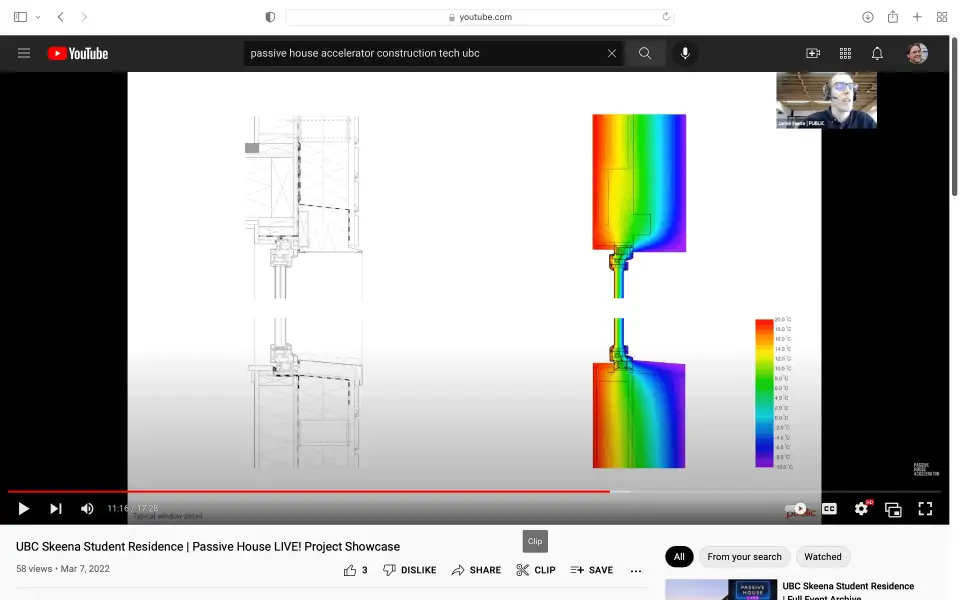
So with regard to windows, we used a combination of Westeck Vinyl window for the typical residential windows combined with Schueco curtain wall frames for the larger openings at the ground floor and circulation spaces. Here's our typical window detail which is fairly conventional. Window frame mounted directly on the wood framing and an interior rod and COG seal for air tightness. We overlap the exterior insulation on all sides, including the seal in order to improve the thermal bridge values around the opening. The seal flashing is sealed to the window frame and then there's an additional waterproof membrane to deal with any water penetration below this flashing.
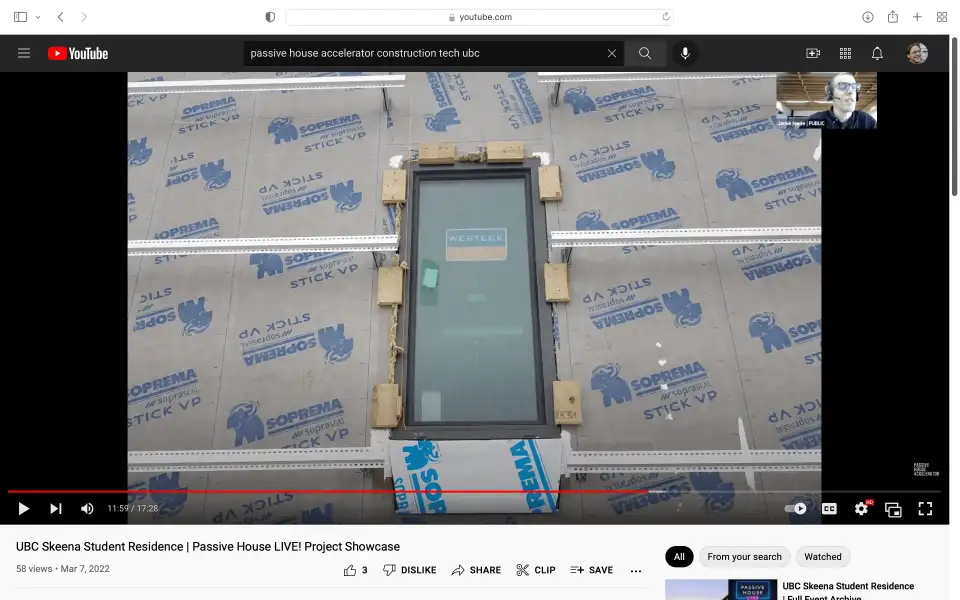
Here, you can see an installed window before the adding of the exterior installation. The opening is surrounded by sections of pressure treated blocking for attaching the jam and head flashings. This blocking is intermittent with installation in between to further reduce thermal bridging.
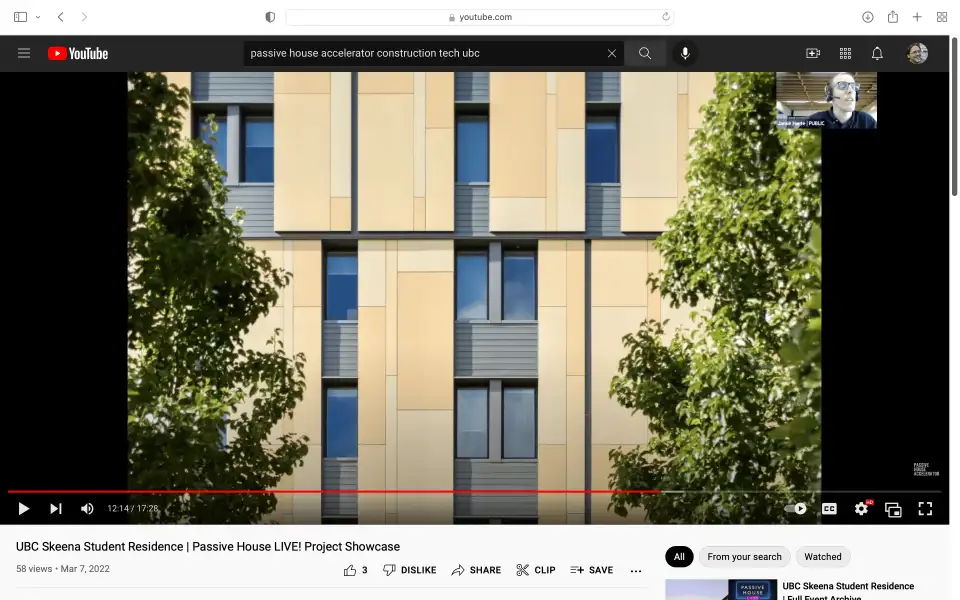
And the finished windows look like this. They're fairly far recessed in the opening which creates some effective fixed shading. And with our cladding design, the intent was to play with this sense of depth and shadow in what's otherwise a very flat wall plane. So we have a primary material of Swisspearl Fiber Cement which projects forward by a couple of inches beyond the dark metal cladding behind. And even with a very simplified smooth massing, there are always exterior components which need to be fastened back to the structure through the exterior insulation. In this image, you can see one of the exterior rainwater leaders on the left, which descends from the roof and means that we could avoid using internal roof drains and the heat loss and complexity that goes with them. These rainwater leaders are oversized to prevent blockages from any ice buildup and to avoid the need for heat tracing them.
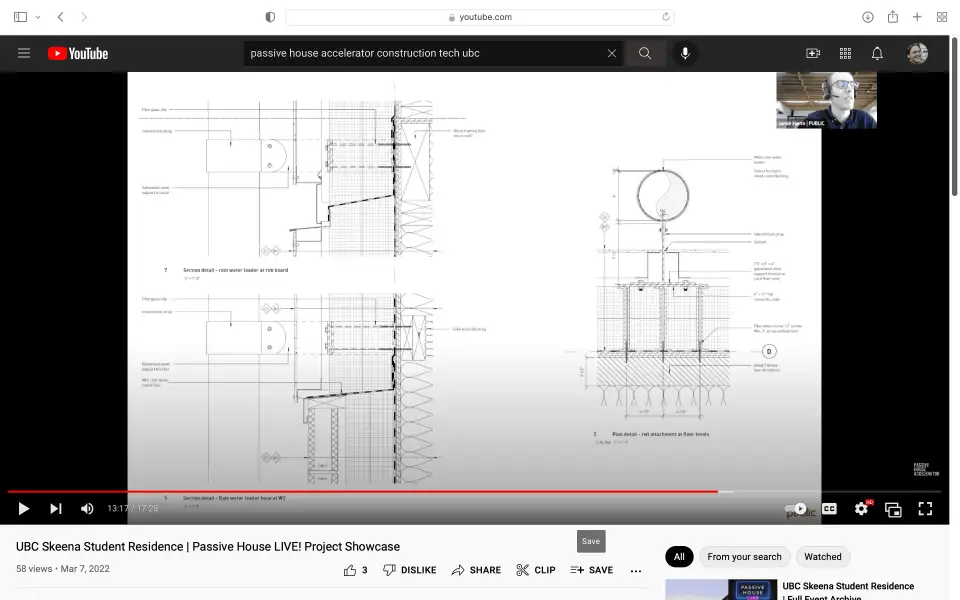
Our solution for mounting them back to structure was simply to guide together three cladding clips at each floor level and mount a DLT bracket to the outside of them so minimal thermal bridging involved.
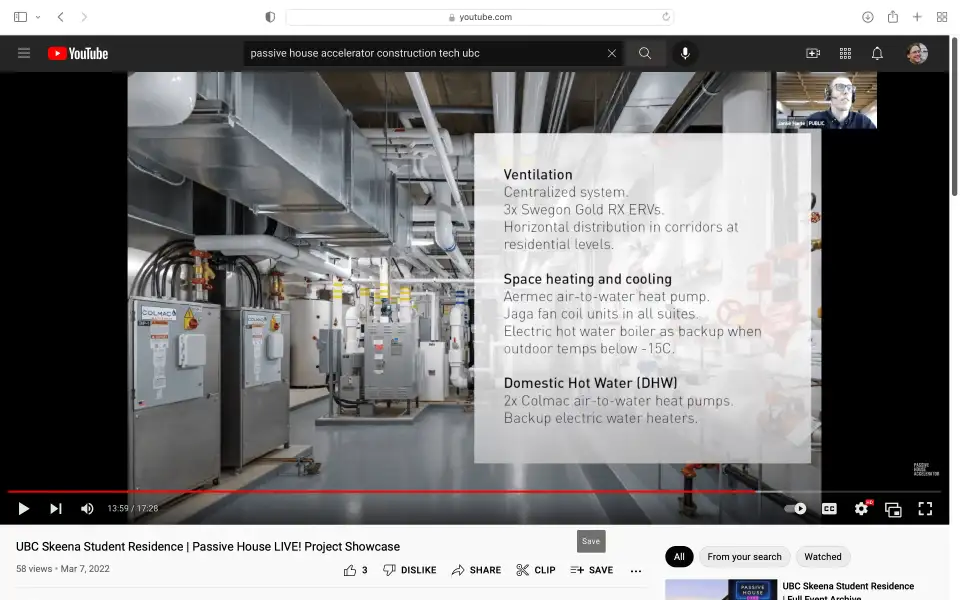
Here's the mechanical room located on the ground floor. The program for the project allowed enough surplus service space on the ground floor to locate the majority of the equipment inside the building. So the roof is free of equipment except for a stub out for a connection to a future potential solar PV system. And the mechanical design was by the AME Group here in Vancouver, contains all electric systems so there's no gas connection to the building. So you can see we've got a centralized ventilation system with three swag on ERVs, one serving the ground floor amenities spaces and the other two working in tandem to serve the residential levels, horizontal distribution through of the corridors on each typical level. For space heating and cooling we've got air to water heat pump which is connected to Jaga Fan Coil units in each student suite with an electric backup for low temperature conditions. The delivery of the air source heat pump was the only really significant element to be disrupted by the pandemic and in the end, it wasn't installed until about a year after the building was occupied. A temporary system was used for the first year, but the delay did push back our final Passive House certification. And then for domestic hot water, we've got two Colmac air-to-water heat pumps and backup electric resistance heat.
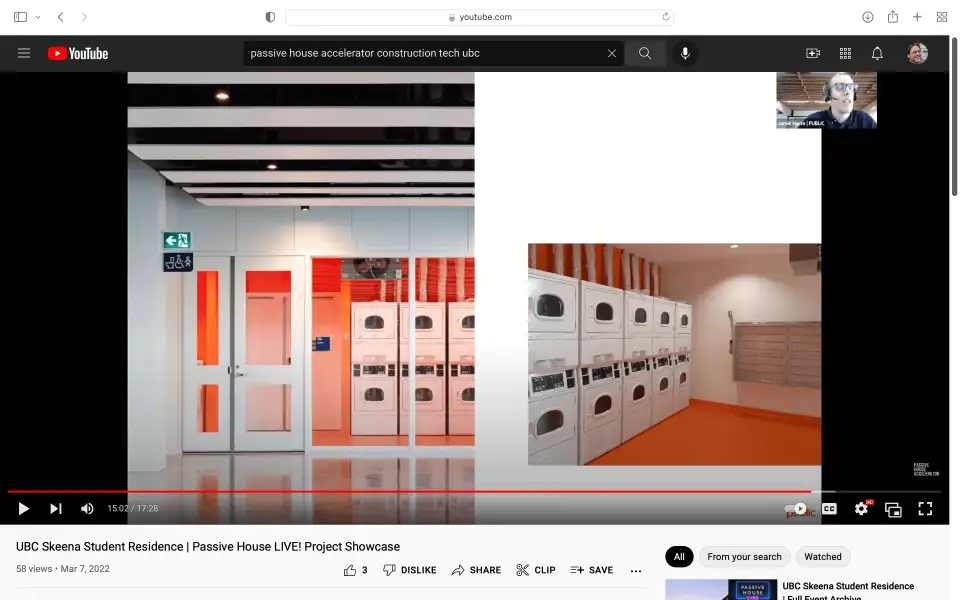
There is a common laundry room on the ground floor for the students. At the time, we were unable to source condensing commercial dryers. So these are conventional direct vent models. The damper that you can see on the right opens automatically when the dryers are in used to draw in makeup air from outside. So this heat loss is then captured in the energy model. The damper is then closed when the dryers are not in use.
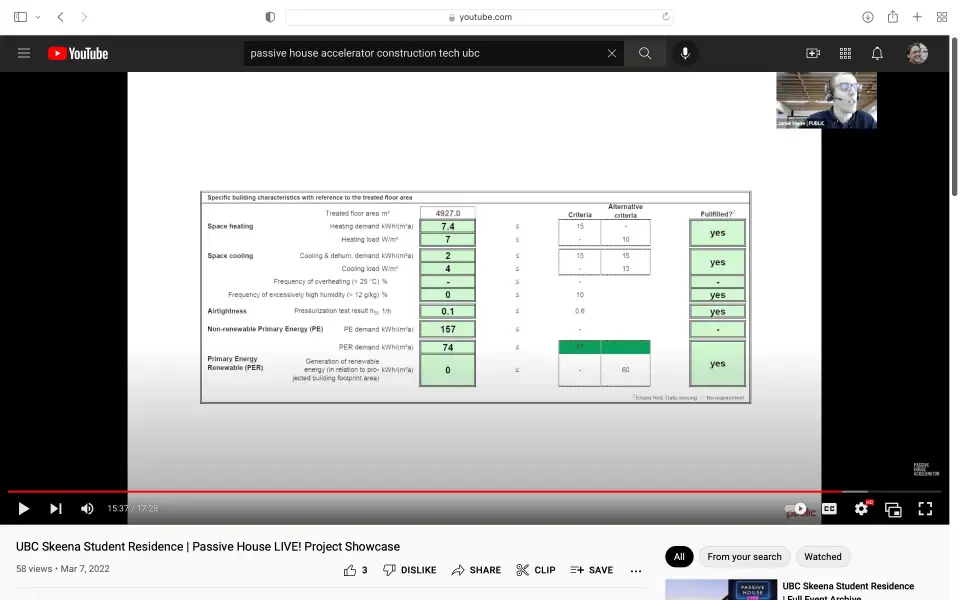
So here's a screen grab of the final energy performance in a PHPP. Heating demand is at 7.4 so it's well under the threshold of 15 for certification. The final blower door test result of 0.08 air changes per hour, pull down to heating demand by more than four kilowatt hours per square meter per year. So it has a really big impact on the final results. As I mentioned, there were some delays with the arrival of the final mechanical plant that pushed back our Passive House certification, but this should be closed out in the coming weeks. As part of the construction, the building was fitted with a series of monitors and sensors, which are connected to the building monitoring system. They measure temperature, humidity, CO2, VOCs and fine particulates, et cetera. This is part of the university's campus as a living lab program where the engineering department is studying the indoor environment and energy use of the Skeena building in relation to other student residences on campus. The building spent its first year at 50% occupancy due to the pandemic, but hopefully they can begin to report some initial findings soon.
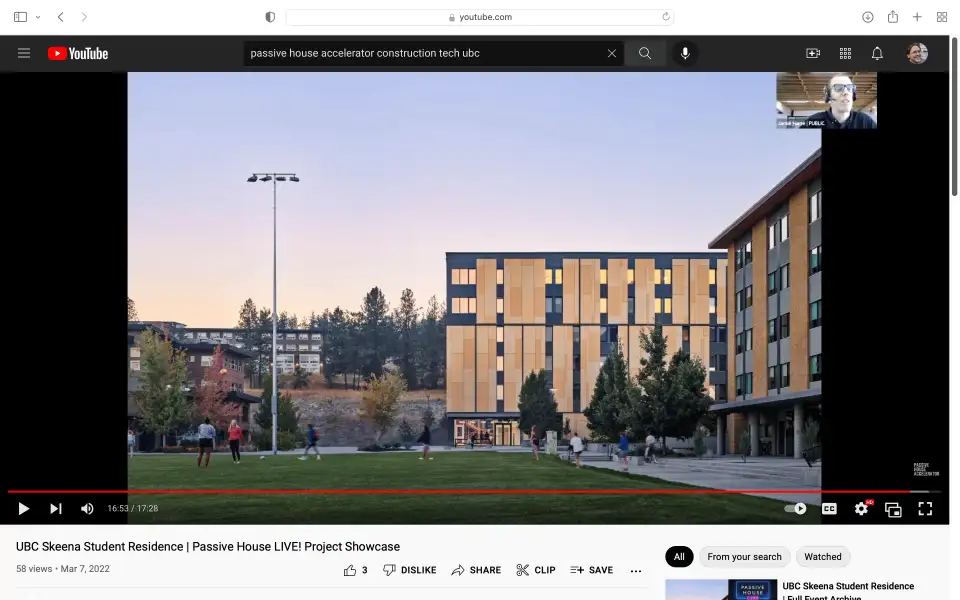
So Skeena residence was completed on time and in spite of the disruption of the pandemic, I think huge credit is due to the contractor, which was Sawchuk Developments for steering the construction through a challenging time and delivering a project that the campus is very proud of. It was also a great experience for us as the architects and we're already putting into effect the lessons that we learned on other mid-rise Passive House projects that we're working on. And so with that, I'll hand it back over for questions. Thank you.