Sy Safi of Ubergreen Spaces + Homes joined Construction Tech Tuesday to talk through his journey of mainstreaming high-performance homes and buildings through best design and building practices using Passive House, Living Building Challenge, and the WELL Building Standard. On his 15+ year journey, Sy has focused on improving design, construction means and methods, development, prefab, modular, and more. Sy discusses how his work has centered on health, resilience, and regeneration, and about how he has achieved some Passive House firsts in Kentucky along the way. Read the transcript for the video below!
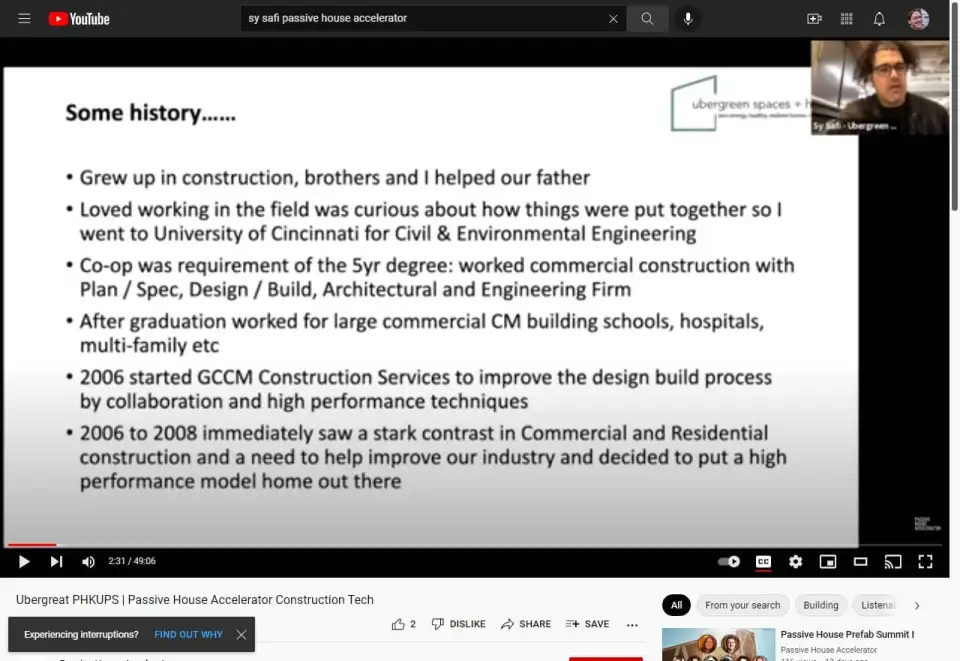
Sy Safi:
All right, Ubergreat PHkUPS by Sy with Ubergreen Spaces. So I'll give you a little bit of history. I did grow up in construction and my brothers and I, we helped our father at a very young age and so it was a lot of fun. We really enjoyed it and it always kept me curious and that curiosity went on to civil engineering at the University of Cincinnati. While getting that five-year degree, I actually got more exposure for commercial construction, plan spec, design build, and I worked for an architectural engineering firm. So I had three different co-op experiences, which was really nice and eye opening. And then after graduation, I worked for a very large commercial CM building schools, hospitals, multifamily, things like that, that really broadens your scope of what construction and design can be.
But along the way, it became a little more frustrating, in 2006, that's why I went ahead and started GCCM construction services because a lot of times and say, I remember a hospital project we were building, hearing the owners come up to you and say, "This is not performing." You're like, "Well, we're building exactly how you have it on plan and spec and talk to your engineer, talk to your architect, they're the ones that stamp the drawings. We're doing exactly how it's shown." But that was a constant issue that came up, we would get blamed for a lack of performance. And so that made me want to be looking at the process and try to improve things by, when in 2006, I started GCCM construction services to do CM work but to do it in a collaborative way where I had some involvement with the design, because being in the field and trying to build it, you obviously learn about construction means and methods, you learn about the industry, you learn about what's going on out there, what works, what may not work.
And so with that, in our first commercial project, immediately also saw... We're working for a nonprofit, very large commercial building, a school and a community center, and the folks that were on the board, they were on a nonprofit, so they all had day jobs and they're essentially coming to me asking questions like, "Well, what's this change? What isn't changed?," or, "What is this? What's going on?" So they didn't really understand construction, not commercial construction at least. But then as I started explaining things, a light bulb went off and they're like, "Oh, well, when I had my house built..." or "When I had a renovation..." So everything kind of related back to a house that helped them make sense. But then immediately it came those complaints about the lack of performance of the home and the discomfort and come see this, come fix this. So being a good person that's building something for this nonprofit, I go and I check out these things and it becomes very frustrating early on.
It's like, man, something could be done better here. And this is like 2006, 2008, I see the LEED for homes pilot program come out and I'm like, well, okay, this has got a lot of great things on here and it looks like it's touching on all these challenges that's really missing in the residential industry. And so I kind of took a little offense to that in a sense that we're working really hard in commercial construction, you got a lot of folks that are being diligent about design, and checks and balances, and making sure at least it's done right, and that's relatively speaking. And so I'm like, well, we need to apply some of these techniques and diligence to residential. And I thought, well, LEED for Homes looks like a great idea, so I found somebody, they're willing to go along with it, and so 2006 through 2008 we gathered a bunch of folks that were interested in doing something different and doing LEED.
We found a client that was interested in doing it and they're willing to allow us to basically test out these theories, and products, and methods that everybody was kind of scared of because they didn't really believe. And so this is just a little entertainment for you all, a video that we threw together early on, because this, mind you, is in Louisville, Kentucky, and it's a bit challenging certainly. Just a little back history on Kentucky in general folks jokingly say like Mark Twain said it best, "If the world were to end today, I'd move to Kentucky because they're 20 years behind everyone else." And so there is some truth behind that and the methods and code is, I think we're still on like 2006 or 2009 building code for residential, so it's still back behind there. And so we needed to basically put some videos out there to help legitimize and let people see the different techniques, and I'll just play this one real quick.
Sy:
Hey Zach.
Zack:
Hey, Sy. How are you?
Sy :
Great.
Zack:
Good to see you.
Sy:
Good to see you too.
Zack:
Those are hand scraped hickory.
Sy:
Oh, wow.
Zack:
Both FSC certified and formaldehyde free. Kind of a different countertop.
Sy:
Yeah, it is. I mean, it's really heavy too. It seems really durable.
Zack:
Here we are.
Sy:
Oh, wow. That is great. And I can see there's no lights on in here.
Zack:
No lights on. Yeah.
Sy:
None at all.
Sy:
You know, Zach, I could take up your whole day here. I feel like I'm a kid in the candy store.
Sy:
Dave.
Dave:
Sy, how you doing?
Sy:
How you doing? Good. Great to see you.
Dave:
Good to see you too.
Sy:
Thanks for taking the time out of your day.
Dave:
Oh, this whole combination here gives you your heating and cooling for your house and your hot water at the cheapest possible way to get it.
Sy:
Right.
Dave:
I don't care how well you insulate in between these stubs, you still get energy transferred going through the stubs themselves.
Sy:
Where has this thing been all my life? You know? I mean, this is what I want and this is something that we definitely want to be able to use now.
Sy:
Right, so what am I looking at here? You got a can light in a ceiling of a home?
Dave:
Can light in a ceiling of a home, exactly.
Sy:
So above the ceiling is the attic?
Dave:
That's the attic.
Sy:
Okay.
Dave:
And so it was insulated at the flat level there.
Sy:
Okay. After you get done with your clothes, you pull it out, put it on top, fold it all up, and then take it to wherever you got to store it.
John Doe:
She's trying to get one that'll fold your clothes, but they don't have it yet.
Sy:
Oh, is that right? Well, when they do, you let me know about that. I want that.
Sy:
Almost half of our nation's energy consumption goes towards powering our homes and buildings. Now that's expensive and we can do something about it. Right here on this vacant lot we're going to build one of Kentucky's most greenest energy efficient homes.
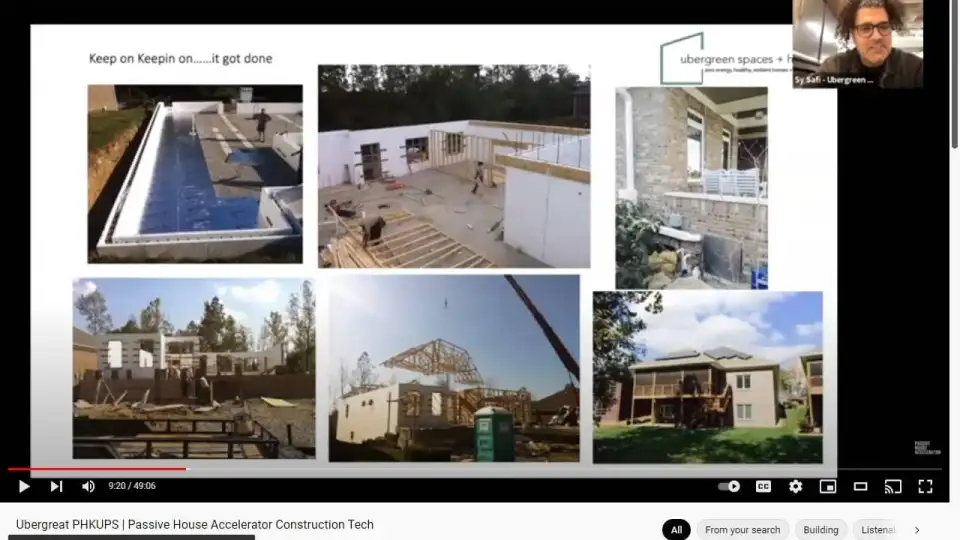
We kept on moving from there. So what's funny is that, it's not really funny, but I'm typically pretty reserved, and so as I'm working on this stuff everybody that wanted to gather around me to do these things that are different are like, "You really need to put this out there. You really need to share it. You need to..." So I was like, "All right, fine." So we had do a little acting, we had to do a little drama, we had to make it appeal to what folks are used to seeing on HGTV and DIY, just give us some credibility as best you can. And so a little entertainment there, but interestingly, and sadly, things haven't changed a whole lot when it comes to the energy consumption with homes and buildings from what I said back then in 2006.
But the great thing is that things are becoming more mainstream and a lot of these techniques you'll see here we've worked to improve, and improve on materials, and stuff. And so here you can see some of these pictures, this was insulation underneath the slab. It was a crazy idea, "Oh, you're nuts." And so we just made sure we engineered the right stuff and we did it. And that gentleman standing in there is Bill, he's 70 some odd years old, and he could swear that he could walk in his wood shop that's right about there barefoot on the slab in the winter and be real comfortable. So here's some more pictures of the basement. We did ICF all the way up and we actually did it all the way up on the exterior walls.
And then some cool things we did too is we, actually on the right corner, you see there's a porch, but what we did was we created a cistern, a rainwater collection tank underneath it. So we capture all the rainwater off the roof. We worked with our sprinkler folks and we invented... Well, I wouldn't say invented, but we made a system that would not use the city water, the meter that services the irrigation, it would use the water in the cistern first, and then if it got so low we had a float that went down and it would turn a valve and then it would open up city water to use the city water pressure instead of using energy to use the pump that we had, which is really cool.
Then we did solar, which is really neat about this too is that we ended up only needing 15 panels to get to net zero, which is pretty... Back then, when you think about it, people that were trying to jump on solar early on for a home like this they had to do like 60, 80, even more panels to get to zero or net zero and we only needed 15, which is pretty amazing.
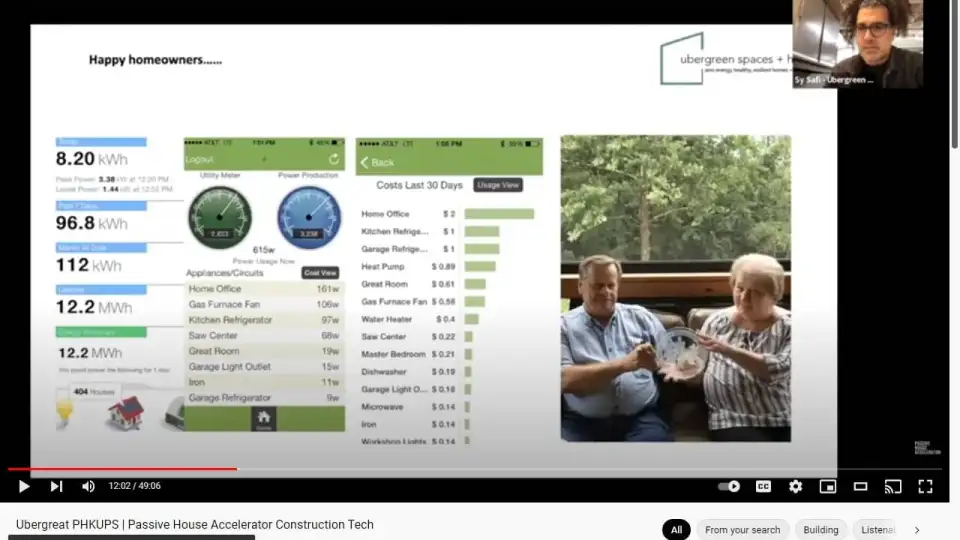
And this is cool, we had some happy homeowners. There's Bill and Linda. We got LEED Platinum. We also got net zero water just from the amount of water we collected. I think it was a 3,000 or 4,000 gallon cistern. And we were all geeked about this energy monitoring that we had and some of the cool things like down below here, I don't know if you see it, but it says that for the amount of energy we produced for whatever day we took this screenshot, for one day we could power 404 houses, which is pretty phenomenal. And then they got these little odometers, it shows that we're producing more power than we're using, which is really cool. We had sensors on every one of the circuit breakers so we can just follow what was being used and you could see the activity of what's happening in the house and they were cool with that.
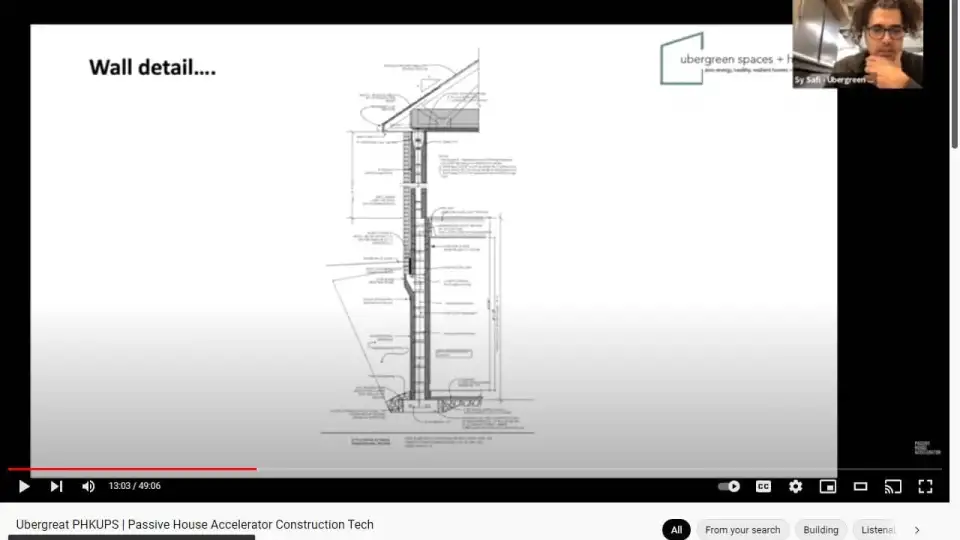
But it's neat to see the rooms that people prioritize and then the rooms that they don't even use, and it's like, "Do you need that space?" Not really. But that was really cool. Here's a wall detail just so you see, we did ICF all the way up, we did insulation below the slab. And there are some things I'll note here, but then up in the ceiling we did do a blown in cellulose, which like I say, was not a fun idea later to have to get up there and cut in a solar tube or just do anything up top there was no fun. But this was a pretty stout home, and the way we approached the detail with the walls, and back filling, and things like that, we approached it similar to commercial construction. We backfill compacted and so those are things that aren't usually typical in residential.
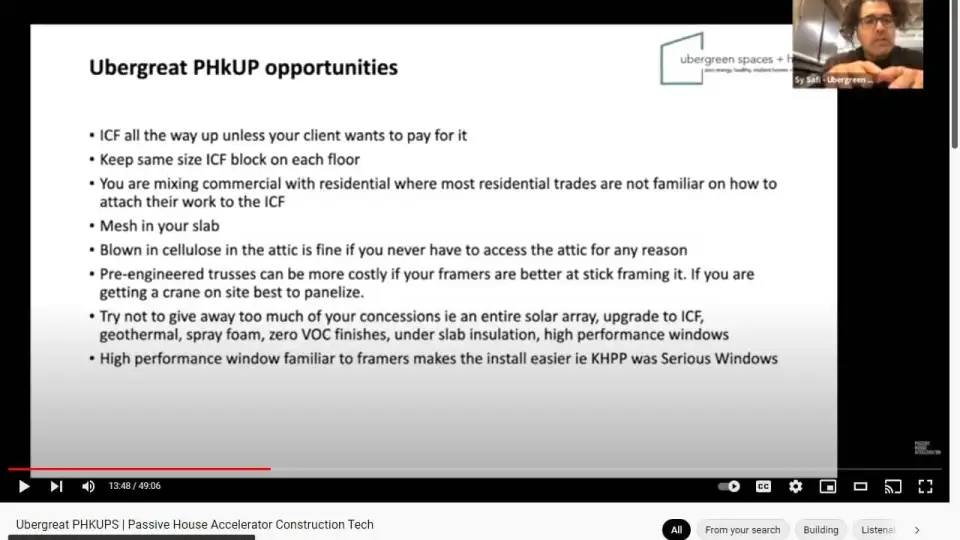
So here Ubergreat PHkUP opportunities. So ICF wall all the way up unless your client wants to pay for it, so back in... Interestingly, this project didn't happen when we wanted it to happen in 2006, well, 2008, because the economy went to hell and the neighborhood that it was in went to foreclosure, and so the owners waited four years and we actually did in 2012. But it was pretty awesome that they did wait around and that we were able to make it happen. So keeping the same ICF, some more PHkUPs, keep the same ICF block on each floor. So if you look back here, we went from an eight, I think it switched to a six or a six to a four, I can't remember. Yeah, it was six to a four, that was not a fun detail. We thought we were being smart by saving money and that was no fun.
In a scenario like this you learn that you're mixing commercial with residential where most residential trades are not familiar with attaching their work to ICF. So either you got to do some training to them to help them understand how to be able to work with that or really you're going to end up limiting your pile of folks that you can get. We had electricians that would not work on a job because of just being able to run their wires and so there's ways of getting around that. Put mesh in your slab, they're going to freak out. If you compact it 100% with your stone and you pour it should be fine over the right density type of insulation, so you're looking at probably 1.8 pound density of insulation or another insulated product that would be able to take that weight. Blown in cellulose was not fun and if you get up there, you got to suit up sometimes or you got to really wear masks and stuff.
Pre-engineered trusses, they could be much more costly of your framers being able to do it. It is kind of tough certainly when it comes to detailing in your air barrier and stuff like that. In this case, we had to obviously go with the drywall ceiling because they did a blown in, but if you're going to spend the money on a crane you might as well do a panelized, which is what we've obviously learned after time. Try not to give away too much of your concessions. This was the first type of project we put out there. It was a long time ago. No one was doing anything like it, but we did give away... Actually we owned the solar array. We took it back later, put it on another project, but the upgrade to ICF, geothermal, spray foam, zero VOC finishes that were very hard to find back then, under slab installation, high performance windows, we ended up paying for those upgrades and that came out of pocket.
But we looked at it as us teaching ourselves and an educational opportunity for us to learn from and to be able to carry on to the next one and it was great for marketing. High performance window, if you are to pick one and you're not able to install the European ones or ones that aren't familiar to your framers, usually framers are ones around us that do install them. KHPP, they used to be Serious Window, they're awesome. They're out of Pennsylvania. It looks just like a window that you would see standard wise, if it's super heavy, it's got the little film in the middle. I think Alpen Window kind of carried on after that later, but this is a great window to go with that they can put in without any training.
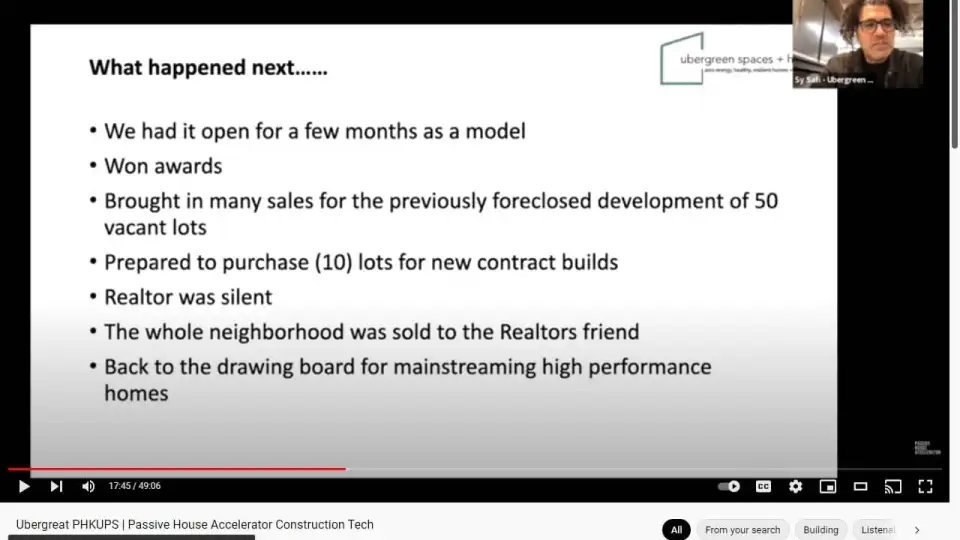
So what happened next? So had that open for a few months, we won some awards and we're flown to Germany with Saint-Gobain and we won runner up on sustainability and stuff, which is really cool. It brought in a lot of sales, which was great because there was like 50 lots that were vacant in that neighborhood and we sparked... We were the first to build in there since the economy turned and it started to come back in 2012, we were ready buy like 10 lots for new contract builds. And these new contract builds, the realtor didn't respond. We didn't hear, we talked to bank, finally he responded and then told us the whole neighborhood was sold to his friend. And so we helped start up some building in that neighborhood and then we didn't get to keep it going, to keep it mainstream. But we had to go back to the drawing board.
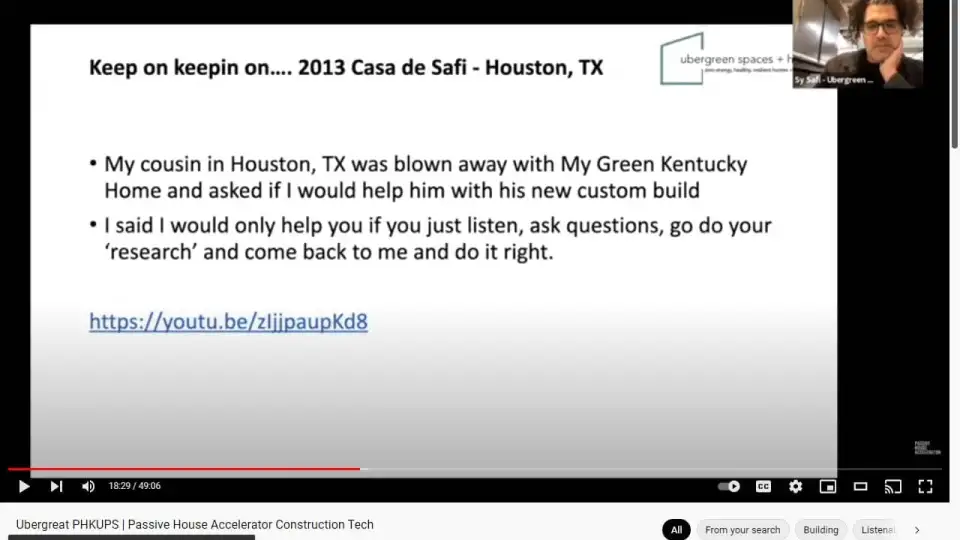
So we kept on keeping on. My cousin in Texas was pretty blown away with it. We called that My Green Kentucky Home, playing off of the song My Old Kentucky Home. And he'd asked if I'd help him with his custom build and I told him I'd help him if he just listened, asked questions, went back, did quote unquote research. That's for you, Zach Semke. Your wife PhD tells you that you do not do research when you are preparing for your speeches. But so he came back to me, he's like, "Well, this stuff makes a lot of sense." And he decided that he wanted to take a jump and run with it, and so here's a result here.
Sy:
It's not Kentucky. We're in Houston, Texas building one of Texas' greenest, most energy efficient healthy homes. I'm Sy Safi of GCCM Construction Services, I'll show you how it's done.
Ziyad Safi:
Sy, Sy.
Sy:
Safi, how you doing?
Ziyad:
I'm doing good. How are you? It's great to see you. Well, hold on, let me shut this. I'm not going to let you see inside the house.
Sy:
You look great, man.
Ziyad:
Appreciate it, appreciate it. You look great too.
Sy:
You got to show me around.
Ziyad:
Okay.
Sy:
I feel like I'm in this oasis, this garden is gorgeous.
Ziyad:
Well, first thing you notice all the landscaping in this whole house.
Sy:
Okay.
Sy:
All right. Are y'all able to still hear me? I'm going to take you to the end because it was all just a bunch of show.
Ziyad:
... and language and he told me, "Go do your research and come back." So you know what? I did my research. And you know what? It all just makes sense. If you just take the time to do the research and understand it, it will make sense. The cost to the benefit is just phenomenal. Me and my wife sat down, we talked about it and I was like, "You know what? Why am I not doing this? Why do I not want to go like this?"
Sy:
Yeah.
Ziyad:
Why are people building houses the same way we built in the 70s, put a little spray foam and call it efficient? There's more to it.
Sy:
But you know what's interesting? I feel like you're talking like me now and I would be doing you a disservice if I did not expose you to what we all don't know about.
Ziyad:
Exactly right.
Sy:
And that's scary not knowing that we are putting our lives at risk. We're putting our environment at risk. We're putting so many things out there. We're doing things that might be status quo that we don't really know.
Ziyad:
Yes, all the energy efficiencies and all of the environment friendly stuff that we're doing to improve the air quality, but you know what it's also doing? Saving the money in our pocket.
Sy:
Yeah.
Ziyad:
And that makes a big difference for the average homeowner.
Sy:
It does.
Ziyad:
If they want to save money, and if you can use the building science to save money and help mother nature, it's a win-win for everybody.
Sy:
It's a win.
Ziyad:
So teacher to student and hopefully I will have a student to pass it on to.
Sy:
I hope so too.
Sy:
Wow. What is most impressive to me is how he embraced sustainability with LEED. The end results are amazing. Not only is he helping his family, but he is also helping the environment. I'm Sy Safi with GCCM Construction Services. This is how it's done.
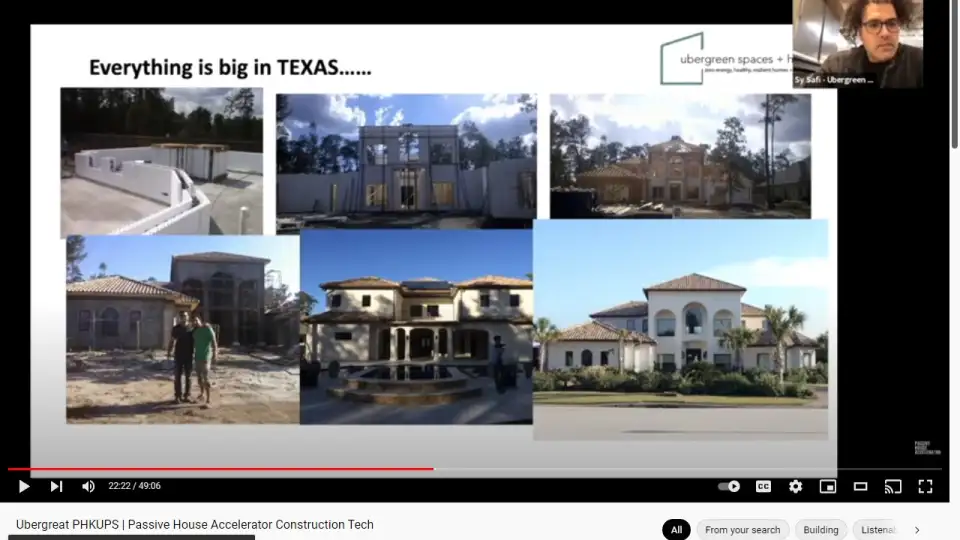
All right, so that was another thing that we put together to try to get folks to just kind of normalize it and be able to get them to see that it's being picked up. And a lot of times when you do get a client, someone that's willing to go along with your craziness, then that's the person that you want to run with. And let's see if this is the right screen as I jump back. That was cool and stuff and it's interesting because a lot of times the challenges that we have with people that have a lot of money, they kind of don't value that and a lot of times an energy bill doesn't matter to them, but we're starting to see that kind of shift a little bit, which is great.
Normally, it's like we won't do monster homes and stuff like that. We don't encourage it. But I mean, you have to really... If somebody's asking you about this stuff and they are open to it, then it's better we do it than somebody else because if we know that we can at least have the conversations with folks that are building an almost 8,000 square foot home and an ADU on top of that, then at least we could do it Passive House, high performance.
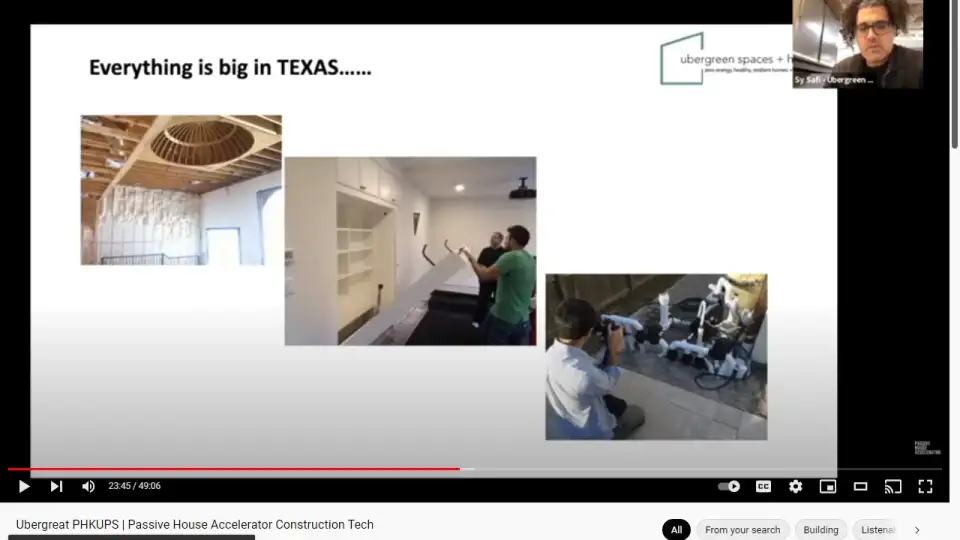
And so we actually had the conversation about Passive House, since I didn't do it on the previous My Green Kentucky Home he was worried about putting that on top of there, but we still implemented Passive House principles, and so we did do ICF, and you can see here the house. They did do solar in the back, you can see they got 20 panels, I think, on there.
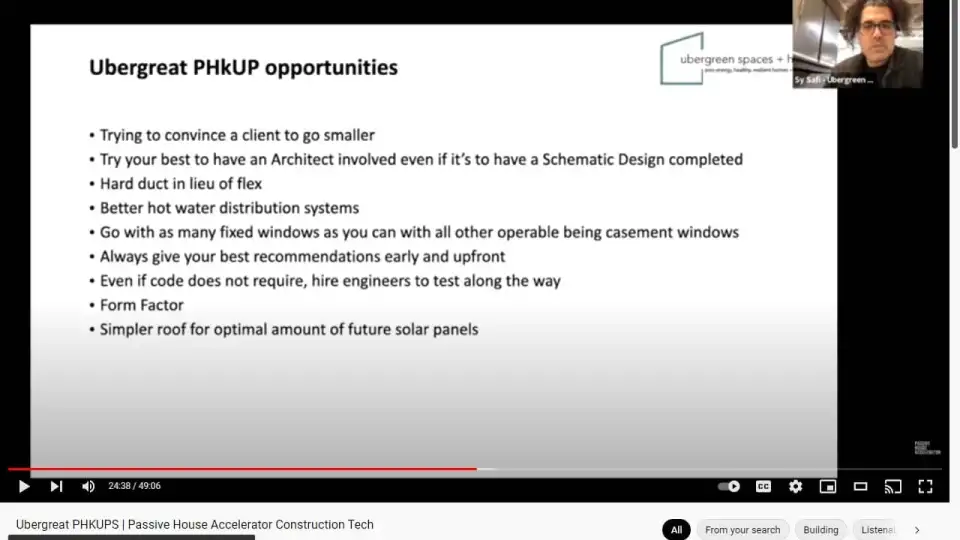
And believe it or not, this house it performs phenomenally. They did do... Well, for the areas that were load bearing over top of ceilings and stuff, we did a split wall up top. So you can see in the top left corner of that picture that's a frame wall on the exterior. We encouraged built-ins and then something kind of cool down there in the bottom right corner for pools, because pools are very prominent in Houston, in Texas in general, going with a California 90, doing two 45s helps you get a lot of efficiency for your pumps and stuff, which is cool. So some PHkUPs, trying to convince a client to go smaller, if they don't want to do it, they're not going to do it. In fact, they kind of added some room on this. You want to try your best to have folks to get a real architect involved, even if it is talking with schematics, and especially if you can get an architect that's a CPHC. Even an architect that says they're green may not necessarily understand the form factor and so that's a huge thing here.
The hard duct in lieu of flex, better hot water distribution systems. They got 10 bathrooms. I mean, they could have done something better there. So something they did listen to also was go with as many fixed windows as you can because at least those won't leak air. And then if you're going to go with an operable window, go with a casement, because at least you can get them to shut and seal all the way around. Steer them clear away from the double hungs, and stuff, and single hungs.
And then don't be shy, if they're going to call on you to ask for help to build something, always give your best recommendations early and upfront, because you have to let folks know that, "Listen, you came to us for a reason and we're here to look out for your best interests. And the fact that we are encouraging you to decrease the amount of your program and the size of your home is really for your best interest. And if you're thinking about numbers, most builders want to go larger so they can have a higher fee on that. So if we think about it, we're not really thinking about the money, we're thinking about you."
So in Texas, you can almost get away with... If you're building your own home, in different parts of Texas you could build without an inspection at all, especially like in this space, they didn't have to build with any inspections, but we always recommend to hire engineers to test along the way: geotechs and structurals and all that. So form factor again is big and then the simpler the roof you can get them to do is optimal amount of for future solar. So if you look back here at this roof, you got those two bump outs there with the hipped roofs on the right and left. We could have easily made something flat and just one hip or something like that, but they went that way. So they kind of lost some opportunities there to do more solar on top of there. They are looking at... Actually, we're talking today. They're looking at bifacials, they're looking at putting some outdoor structures for the outdoor spaces.
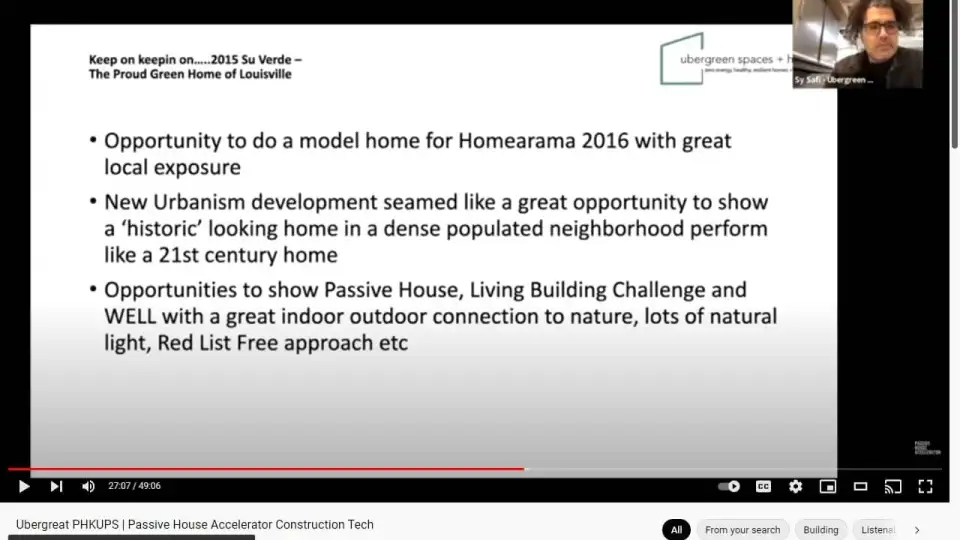
So then we looked for another opportunity to do another model home of some sort while still doing commercial and residential of other projects. And so 2016, Homearama in Louisville, Kentucky was a great opportunity because it was a new urbanism development. It's like, oh great, we could touch on so many things with Passive House, Living Building Challenge, WELL. Being on a small lot close to homes you could still show people that you can have a lot of indoor outdoor connections in nature, lots of outdoor space, lots of natural light. You can produce energy, you can make it look like an old home, historic, because it's kind of pretentious in a way by recreating, I guess, the past, but it's what that neighborhood is.
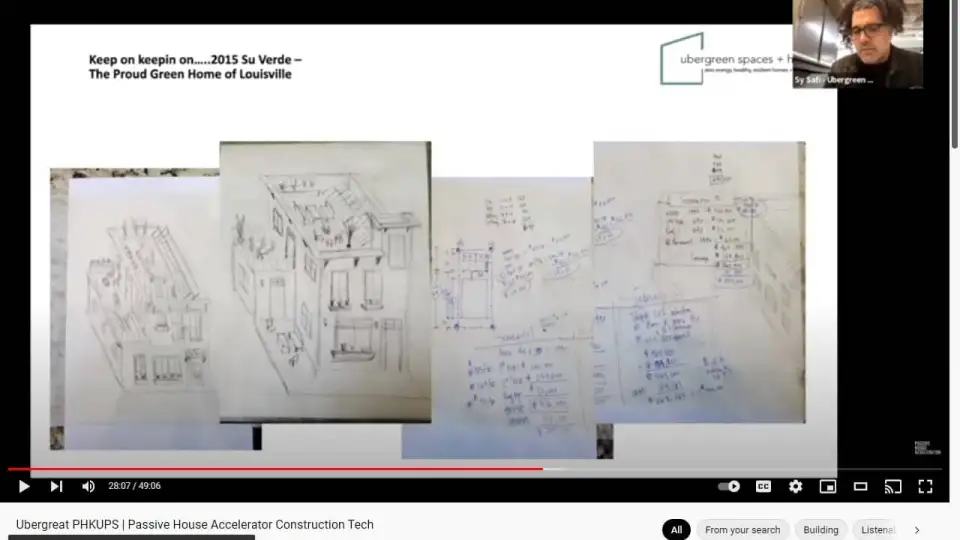
And so we started out with just some fun sketches and if you look on a left I'm like, all right, let's see if we can do this. It's like a shotgun lot, it's a deep lot, it's narrow. Try to keep it simple with the form shape. And I know that we have a lower roof deck and we want outdoor spaces, and the second iteration was kind of like another idea. Threw some numbers at it, we're like, "I don't know, $700,000.00, okay, maybe we can do it for that."
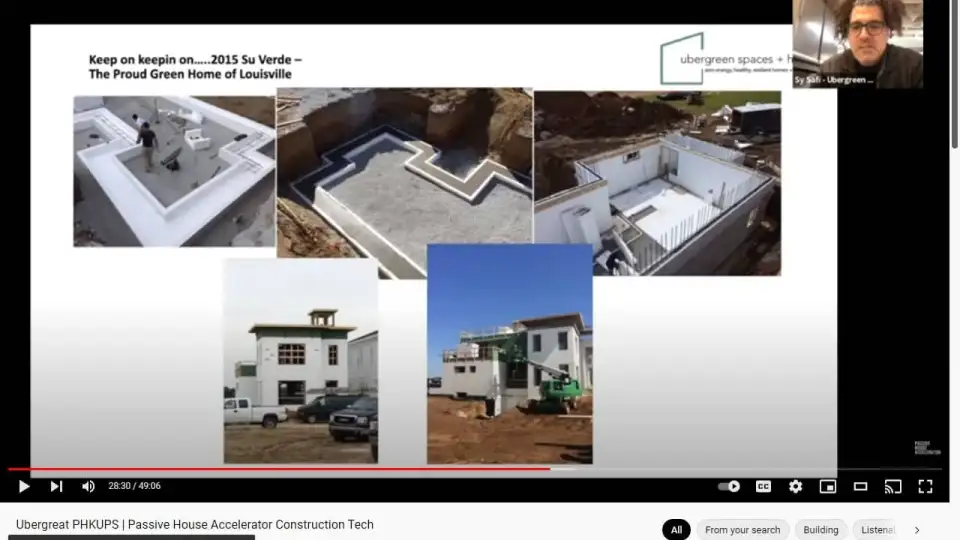
So we get going and then my juices get going like I got to show everybody everything. You know? So it's like... We had the footings made with geofoam troughs and you can see them, we put rebar in there, they're pretty amazing to work with, poured them, they were great. Did the six inches of geofoam beneath the slab and look at the shape of the thing it turned out to be... Our architect really wanted to have a lot of features and it got chopped up. And I wasn't happy about that, but we were under the gun to get on the way and had to keep the team happy too because you have folks rallying behind you, and so you want to make a feature home.
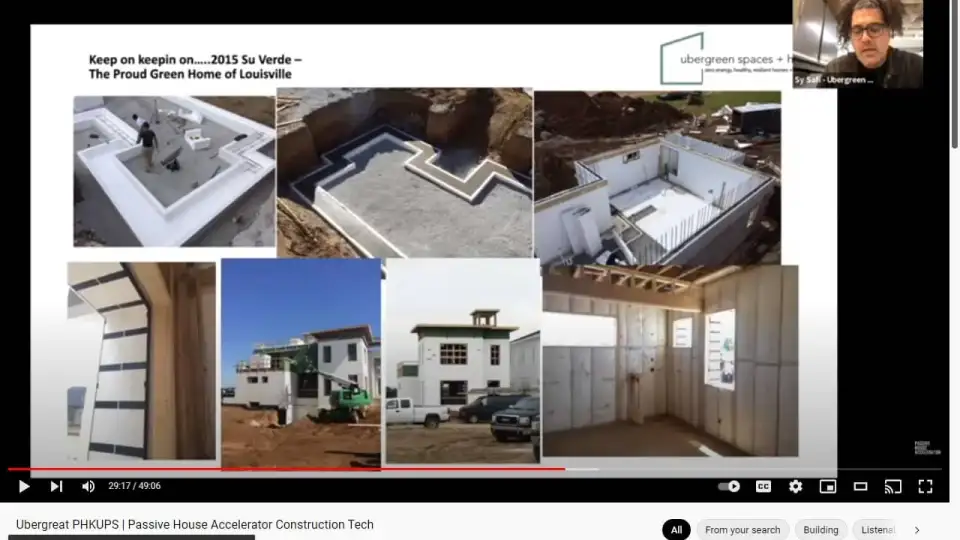
Down on the bottom right picture you can see that little, it looks like a hole dug down in there that ends up being a rainwater collection tank under the patio. Then you have... Let's see. These bucks here on the left, I got a window buck, that ICF window buck that's going to thermal break. And then you could see to the right of that on, this is the bottom left picture, to the right of that there's a two by four stud wall frame there. So prior to this, I got my CPHC and my CPHB and I'm like, all right, WUFI was not terrible to model being that we had a bunch of squares, which was great, but the actual getting to where you need to be to meet the heating and cooling demand loads, and the marks that we needed to get it certified, we needed an R40 wall when in this area you could get away with a 30 or less or so. So that's why we had to fur that wall out on the inside, and then if you look down at the bottom right picture we even did a dense pack fiberglass in there, so that got us to an R40. It turned out beautifully.
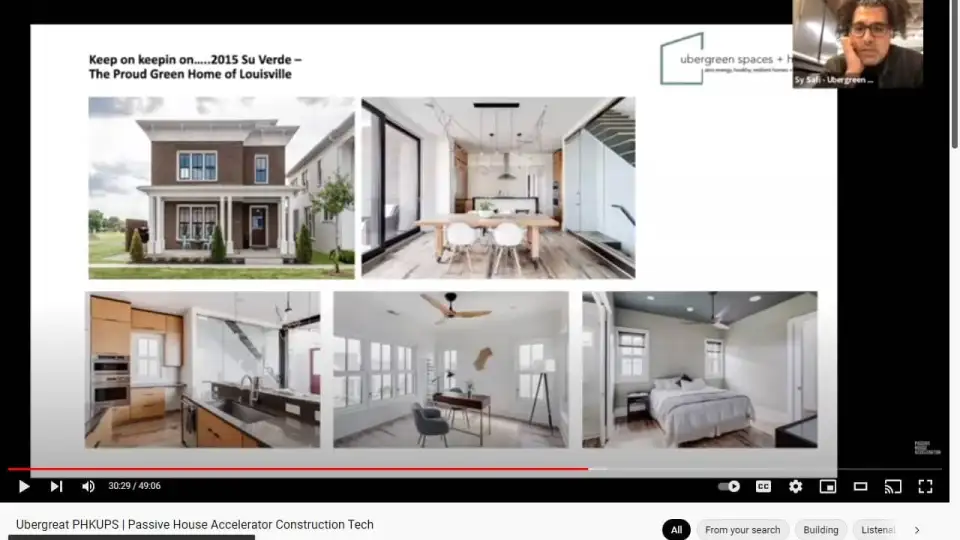
This won some awards, got a lot of attention locally and just around other areas. So we followed... WELL, we followed Living Building Challenge with some Petal Certifications and Passive House. And so every bit of this was done by hand, all of the ceiling was with PROSOCO, and some tapes, and zip, and we got this thing by hand down to 0.5 ACH on the first try, which is pretty amazing. But it took this lift down here to get around the whole thing and it is costly, but it's a beautiful result.
I don't know if you know Russ Smith, he used to be for the University of Louisville, he's playing pro ball overseas, we had this for about four years as a model, he ended up buying it. He was on the 2013 National Championship of the Cardinals. And this is another video we did just to put it out there to help folks, I guess, get an understanding. So we learned that when you speak too much technical and building science people don't understand, so I had to come in and try to do it as relatable as possible. And I'll just do a brief...
Sy:
Welcome to Su Verde, the Proud Green Home of Louisville. I'm Sy Safi with Ubergreen Spaces and Homes. You are in for a treat. This house was designed around health and wellness in spaces. We consider that indoor air quality is usually three to five times worse than the outside air and what we've done to make this home really healthy is we've sealed all the cracks in the home that you typically find in the windows, and the walls, and the ceilings, and through the doors, and we've also insulated this house really, really well. So you see the walls are very thick with insulation and we have a window that is thick and sealed on the inside of the sash and also on the frame, and when you close it down, it closes like a vault. So this is like your savings to energy and comfort and since they're European windows, they tilt as well for fresh air if you'd like it.
Sy:
One of the other great things that we do in this house for health and wellness is that we have all these windows on the south side allowing a lot of natural light to come into the space, which is very important because the color of light that goes through our optic nerve will affect the way that we operate, and our energy throughout the day, and it'll also affect the way we sleep. Now, since this house is air tight, what do we do about the solution of having....
Sy:
So essentially, went downstairs, looked at the Zehnder Comfo 550, and we got the ICF walls we showed, we show what's under the floor, and the Stego, and the tape. And then we got the EWS, our dealer for the whole home filtration systems. And we go to the top, and we look at the solar, and then we show the energy bill for...
Sy:
Paying for the basic service charges...
Sy:
About 12 bucks.
Sy:
I'm Sy Safi with...
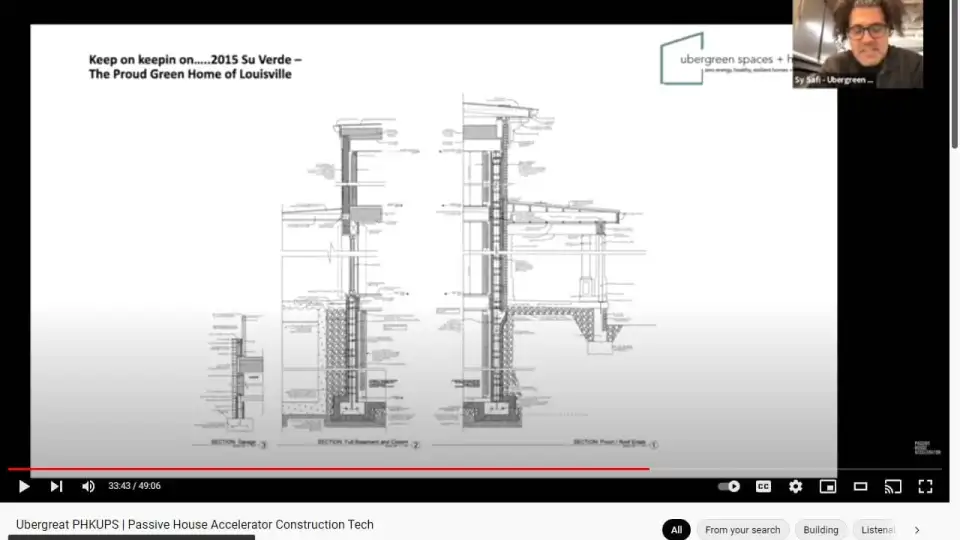
And so that's that and then here's some details. Another thing that's like dang it should not have gone all the way up with ICF, but we did it because we wanted to show it, and we wanted to talk about fortified for safer living, and we wanted to talk about durability, and resilience, and all those great things. But if you look at this detail, you see the footing. We do have former drain down there on the sides of the footing, which is really cool. We do have the footing trough. We have the ICF going all the way up. We got the framed wall on the inside of that. And then in the ceilings, we actually did do spray foam underneath the one, excuse me, primary roof. The flat roofs we did a commercial type roof with layers of POLYISO and then dense pack fiberglass.
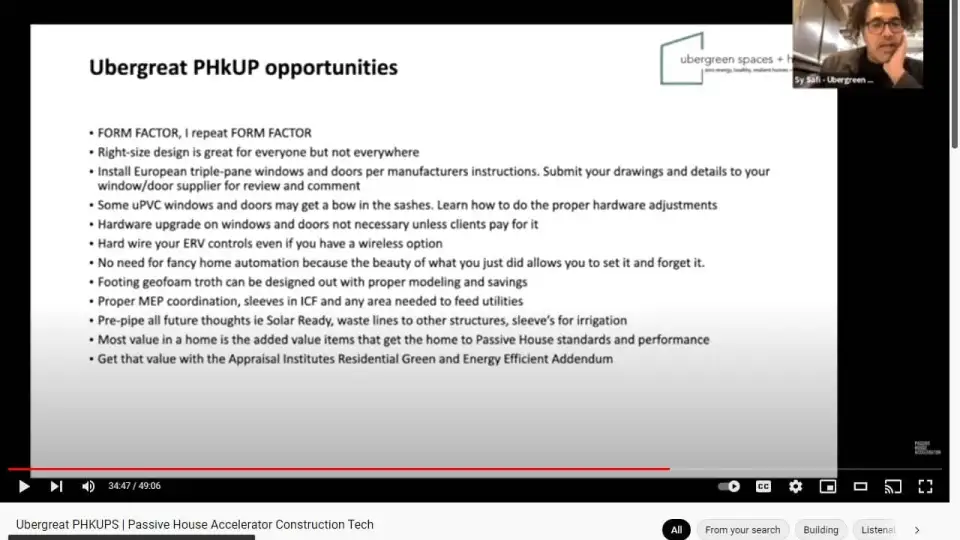
And then an area of a second floor wall that was over top of an area that could not bear on ICF, that was a double stud wall, which was interesting, we did a kind of a flash-and-batt on that. And then form factor, goodness form factor, gosh. Yeah, we had an R100 in that attic and we did not have to go that far, but that's what we had to do to get this thing to meet these certifications, because all those inside, outside corners, geez. So right size design is great for everyone, but not for everyone. So in Kentucky, and really in a lot of places in the country, you're dealing with folks that get... Excuse me. They get wowed by just, wow, this room's big, wow, this room's big, it's great, so they put a lot of value in those things. European windows and doors, make sure you do them per manufacturer's instructions. Send your submittals or just details to them because they have great information and great learning, stuff they'll teach you for installation that'll make you get it right the first time.
So don't be scared if some of your uPVC windows might have little bows in those sashes because sometimes they do have a little warp in it, but you just got to learn how to properly adjust them and the seals will take care of it. Hardware upgrades aren't always necessarily worth the cost. They function, right? But if they're going to pay for it, they'll pay for it. Always hard wire your EVR controls, even if you have a wireless option. So when you have that switch or that button in the bathroom, just hard wire it to the units so you don't ever have any issues. No need for fancy home automation if you don't have to because the beauty of what you're going to do here allows you to set and forget it, and you can go on and enjoy your life.
Footing geofoam trough, you could design it out with proper modeling and savings, so if you have continuous insulation under the slab hitting your walls and things like that. Proper MEP coordination, sleeves in the ICF anywhere you need it or just regular foundations and whatever's needed to feed utilities, pre-pipe of all future thoughts like solar ready, waste lines to the other structures, irrigation. So most value in a home is added value items that get the home Passive House standards and perform. So those are areas that we started to being like, okay, the structure is really where you get the biggest bang for your buck and that's, if you're following Passive House, you're talking about the site, the orientation, the way the sun's going, and then you're designing the walls and such, and the roof, and then fenestration, then you're getting into fresh air and all those other things.
But we notice here that you truly can get your value out of that Appraisal Institutes Residential Green Energy Efficient Addendum and if you don't use it, you're not going to get appraised properly. This house appraised much higher than other homes in the neighborhood. I think like $360.00 or about $375.00 a foot when other ones are like $200.00, $250.00, $220.00. I have another example of another home we did after this one that was... They initially worked with a lender and they used this Energy Efficient Addendum like we said, it appraised at like $770,000.00, it was pretty close to where it should be. And then they went with another lender, the other lender didn't listen what their appraiser... It appraised at $550,000.00. So there's a big difference in whether you use this and the appraiser uses it or not. If your appraiser doesn't use it, get rid of them and find another one, or make your bank get another one.
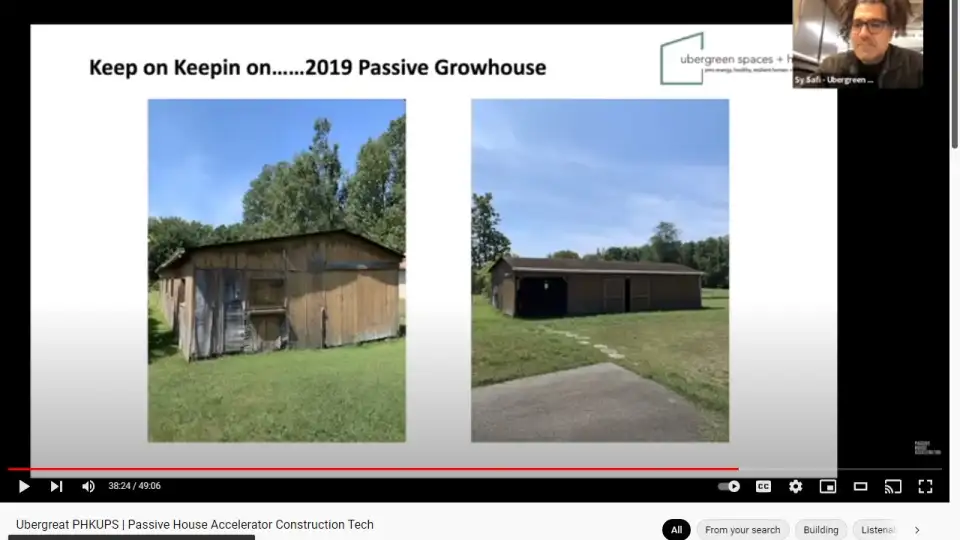
This one's really cool, in 2019. This is a shed on a small farm in Kentucky. They wanted to create a grow house out of it. And I was like, okay, a Passive House grow house. And so they fixed the structure up and stuff and so we came in and we did the peel and stick. And we became an AeroBarrier dealer at the time because we've learned through these different projects over the years that there's not a lot of folks that know how to do these self-performed things or subs that can do it, that's why we taught ourselves to do it.
We went from a 33 air changes an hour to three air changes an hour just in this stage of the building. We're mainly just kind of playing around with the equipment, but we did go ahead and finish it off. We built out the bucks, did PROSOCO, we did the three inches of EPS, vapor open, did the furring strips, and then we had solar on top. When you can't find any Passive House barn doors, you just make them, so we made them and here's some more pictures. They like redundancy and so they wanted to be able to multiple mini splits, they wanted to have multiple fresh air systems. We did the Zehnder, which one was this one? This is the really nice one. Right now it's escaping me. But it also balances itself, which is pretty amazing.
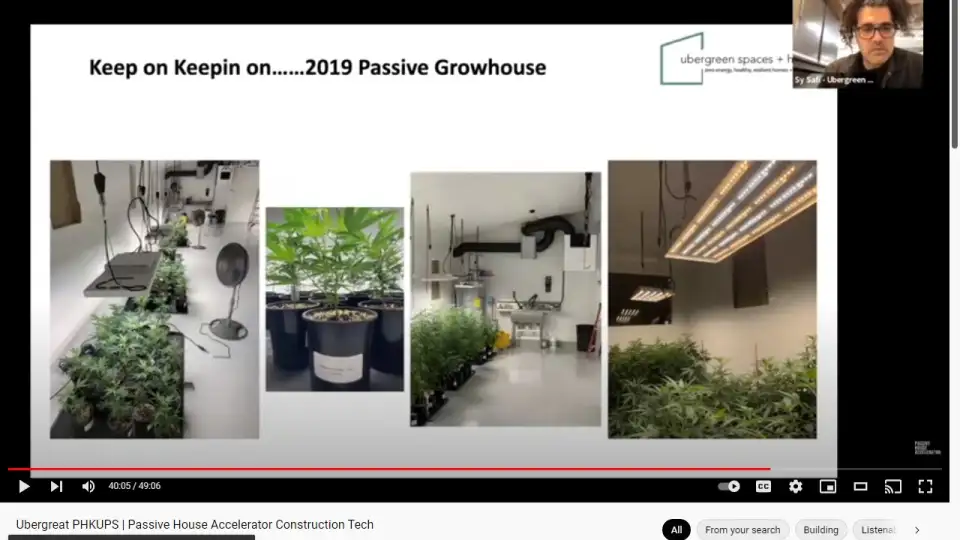
We install those ourselves. Yeah, I think it's the 600, but anyways, it's great because it does balance itself out. And we've never done a grow house, but they wanted to use this because they make their own grow lights, which is really cool. And they're growing hemp and they're using it to make seeds, and Kentucky doesn't allow marijuana yet. But what was really awesome is that we're able to apply Passive House principles just understanding what they needed to do to grow these plants without crosspollination was a big thing. And so we made this thing air tight, then we had layers of different filters within the system. I don't know if you can see in the background where the Zehnder unit is up in the air, there is like a manifold there and that has, I think, layers of charcoal filters and different MERV whatever filters.
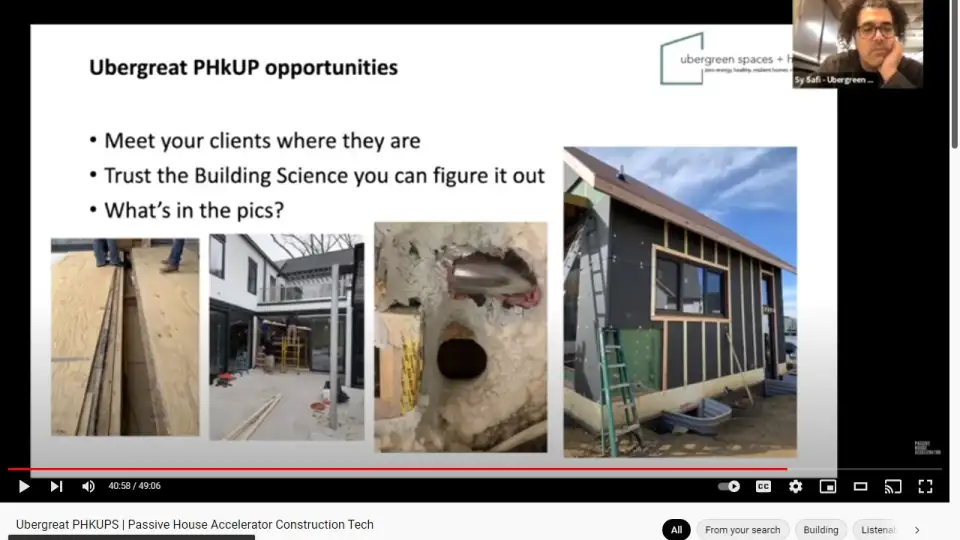
And then we got called to other projects to fix things for people. And essentially we are... There are folks that use Zola. We consulted on this house years ago, they didn't do exactly what we told them to do and they didn't communicate with Zola at the time, so on the left you see there's only two LVL beams. There really should be six. And so this 12 inch wide, three panel, 18 foot wide, 10 foot tall lift slide door was only one third on a load bearing and so we had to change it. $60,000.00 later we had to actually toss what was there and put new in and it works swimmingly. One thing that's kind of cool, we're trying to get away from certainly high carbon materials with a lot embodied energy, so when you look at this third picture from the left that's kind of an idea that's like, no, no, you don't want to spray foam over mechanicals and stuff, and so that was really hard to find mechanicals and reroute things for the things that had happened there.
And the picture on the right kind of also put us in another direction a different house that we were working on and it's like, so much time can be saved and money can be saved and sent back to the clients if you're able to panelize. And so this 2019 project got us looking for a warehouse to do panelization, split wall, and so look at the ladders, look at every little dot of joint and seam filler that we had to do over nail heads. There's a lot of work involved there.
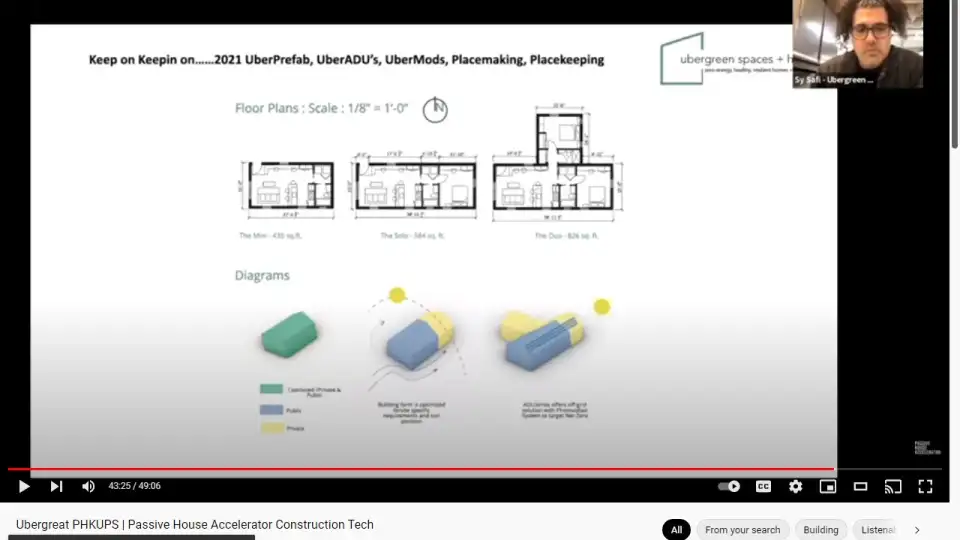
So we have a seven and a half ton crane in the space we have, there's a wall panel, there's a couple examples. We got into mods. We've done some containers. We are doing some right now. So we're looking at ways to help provide solutions. We're also into place making and place keeping, and so helping communities and this was for a community college that is in a downtown area, it's Louisville. Then we're getting into ADUs, we're rolling out an ADU series. And these are some elevations, trying to keep them simple. This gives you an idea of three options, the solo, the mini solo, and a duo. You can add on if you want, trying to keep it simple. And we actually... We did draw a tiny because some people wanted something even smaller, so we took the mini and chopped out the program to the north there and left little hallway.
But these ADUs are... These are these standard size cabinets, standard size appliances, because they're a little easier for people to grasp on, but they're from 435 square feet to 826. And let's see, here's another shot of it. We're working with an affordable housing developer trying to help them come up with an affordable Passive House. And this will be penalized soon, so we're taking any turnkey projects we have and panelizing them. I've also become a partner or I started a development company a couple years ago with a few other colleagues, and so we're looking at urban revitalization in areas that are kind of like forgotten place in cities. And so trying to build pathways to equity, and workforce development, and obviously doing it the way we do it with Passive House, Living Building, and WELL. Sorry about the noise.
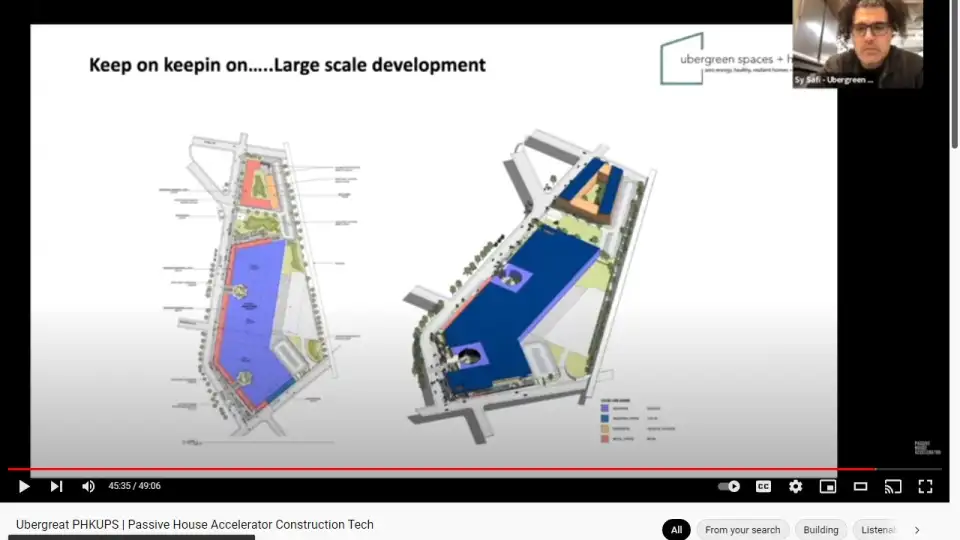
And so this is a 17-acre brownfield that we're working on right now and I'll keep it from being disclosed just yet, because we've gathered information obviously from what the city has talked to the community about what their needs and wants are, but that kind of engagement was just kind of like a night thing, one evening at the community center. But we use that information to kind of inform these things because we have to create a pro forma, we have to be able to create our capital stack and get this thing funded, but this is on the hush. I can't obviously handle something like this in this volume and do the development at the same time, that's why Onion Flats is our partners, Tim and Howard, they're our design architects and Luckett and Farley is our local architect of record who's also doing design as well.
But this is something that we're working on to hopefully have happen sooner than later. To the north of the site is affordable housing and portions of it could be workforce housing. It's going to be all Passive House. There will be WELL buildings involved and Living Building Challenge involved as well. But our premise obviously, of building science is Passive House. The dark blue you see here is solar, so we'll be producing more. This large building at the bottom is a distribution space and offices for a local company that is a pretty big company. And an iteration of what may happen to this too is that we're probably going to have a different tenant share space here and take about a 100,000 away from the distribution for a health and wellness focused entity, and that could add another 130,000.
So we got 240 units, I think 300,000 right now as you see it, but we'll do 220 for the distribution, all green clean manufacturing as well, and then 130,000 square feet for a health and wellness type entity. Then along the street front in the pink on the left you see is also beautiful commercial retail that also is amenities. Here's what you could see from the street and you don't really see a warehouse, you see something beautiful and it's pedestrian friendly. And that's a beautiful, big canopy there with bifacial solar. And here's some gathering areas and that's it. Thank you everyone and I thank a lot of friends and colleagues. It's been a long journey, certainly and we're trying to take this in a direction that hopefully can help volumes and volumes of people, a lot of people.
And that's why I've been focusing on taking this to a lot of the turnkey projects, implementing our panels, and excuse me, and then offering it hopefully to everyone that would want it. And we also are self-performing a lot of things that people don't do, the ERBs, putting in those tough windows and doors, and all the things that we had to learn on the way through that we think that we can help others. So we work for builders, we work for homeowners directly, so we try to help everybody. And by doing large scale stuff too we hope to be able to be a solution with Passive House and the other great programs out there.