James Dean (Home Owner, Co-Founder of Oxygen8) and Stuart Hood (Mechanical Engineer on the Project, Integral Group) talk about some of the notable attributes of the PHI Certified West Bay Passive House including the use of a Cross-Laminated Timber (CLT) superstructure constructed on top of a concrete foundation, floor-to-ceiling glazing providing ocean views, a passive solar design, and an innovative mechanical system design using air-water heat pump technology for domestic hot water and heating & cooling through the energy recovery ventilation system. They were joined by Guest Host Chris Ballard from Passive House Canada. You can read the whole transcript for the video below.
Chris Ballard:
I'm really excited tonight to introduce two exceptional people in the Passive House world. We have James Dean. James is known to many of us as a clean tech entrepreneur with a passion for innovation and healthy buildings and sustainability. He's founded at least three clean energy technology companies; Oxygen8, Core, and Greenlight Power. Before founding Greenlight, James was with KPMG Consulting. And we know that James is committed to sustainability in his personal life. He recently built West Vancouver's first Passive House, certified to the PHI plus standard. James was recognized as one of Canada's Top 40 Under 40, and was a finalist in the EY Entrepreneur of the Year. He's also on the boards of the Home Ventilating Institute, Fuel Cells Canada, and Science World. He's also a member of the Daikin North American Advisory Board. So, really excited to hear what James has to say.

And with James tonight is someone else who's well-known in the neighborhood, Stuart Hood, who brings to tonight's event over 30 years of building engineering experience to Integral Group as a leader in low carbon, sustainable building design. Stuart's project portfolio ranges across all sectors of the building environment, but with a focus on complex facilities such as laboratories, or laboratories for our American friends on the call tonight, museums, law enforcement centers, corporate offices. He has experience working on projects in Europe and Asia. Stuart also brings a global perspective to his clients. He seeks progressive technologies and strategies to incorporate into North American projects, and follows leading edge sustainability trends globally. Stuart is active in the Passive House community and has been involved in designing mechanical systems for many Passive House projects, including, as I said earlier, fire halls, community centers, multi-unit residential buildings and high-performance homes. So, welcome to James and to Stuart. And with that, I will pass the torch to you gentlemen. Thank you.
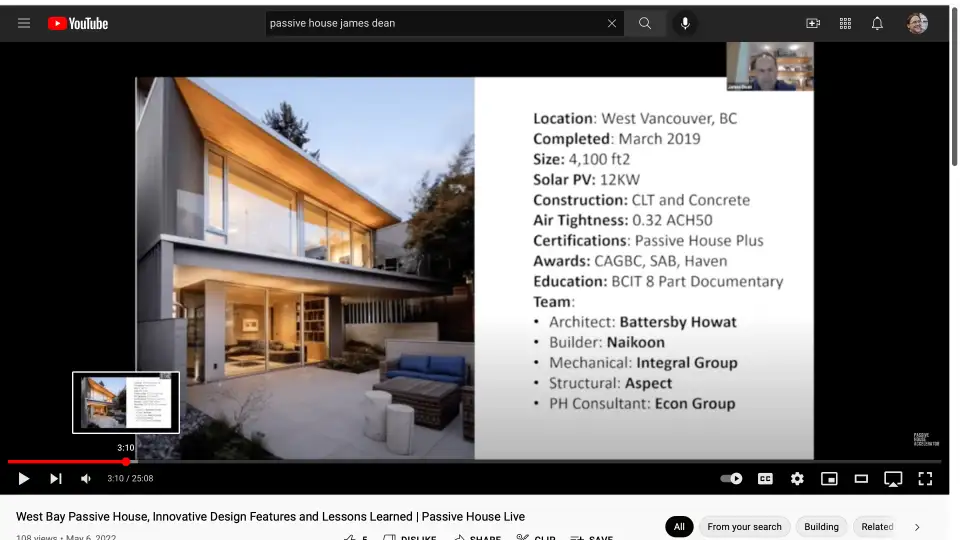
James Dean:
Thanks, Chris, for that kind introduction, and thanks to Passive House Accelerator for hosting Stuart and I. And maybe I'll start back five years ago when I had the idea to build a net zero energy home and became familiar with Passive House through a company I was working with, Zehnder. And I approached my wife, and I think she did what any wife would do and did a Google search on Passive House and came back and said, "James, I admire you for your beliefs in sustainability, but it seems like a lot of these Passive Houses look quite boxy and have really small windows." So, I decided to take on the challenge to see if we could build a beautiful home that was energy efficient, healthy, comfortable, and fun. And we've been living in the home for three years now and really excited the whole family with how it turned out.
So, I want to share with you some of the lessons that were learned along the way and some of the exciting technologies that we used. And we took quite a few risks, because some of the things we implemented hadn't been done before. And I think the key reason for the success, and it's not going to be a surprise, was just building a stellar team. So, I want to give a shout out to our architect, BattersbyHowat, who's known for their contemporary designs. The builder, Naikoon, had never done a Passive House before, but had done a lot of net zero energy homes. And then Stuart's firm, Integral Group, did all the mechanical design. Structural, you'll learn, we built with cross-laminated timber and concrete, which presented some challenges, but Aspect did a fantastic job on that. And some of you may know Marcel Studer, who was our Passive House consultant and did a great job.
So, some details on the home. It's in West Vancouver. And it turns out that the North Shore of Vancouver is one of the perfect places to build Passive Homes because we've got great orientation. We've got beautiful views to the south. And, as we'll learn here, we really were able to take advantage of the solar thermal gain. We started the process five years ago and then moved in three years ago. So, it was about a two year construction process. The house is a little over 4,000 square feet, and we have 12 kilowatts of solar panels on the roof, which has been really helpful. You'll see at the end, we didn't quite hit net zero energy. We're pretty close, but the solar was definitely a big part of getting there.
We were a little bit worried about the air tightness test and meeting the very stringent requirements of Passive House at 0.6 ACH50, and we're happy that we came in at about half of that. And we've won a number of awards. One that I was quite proud of was the Canadian Green Building Council for Innovative Home. And one thing I also wanted to mention I was very proud of is we partnered up with BCIT, which is one of the local colleges here in Vancouver. And they did an eight part documentary following all the different steps of the construction. So, if you're interested in seeing that, you can go to YouTube and download those videos, which are really informative.
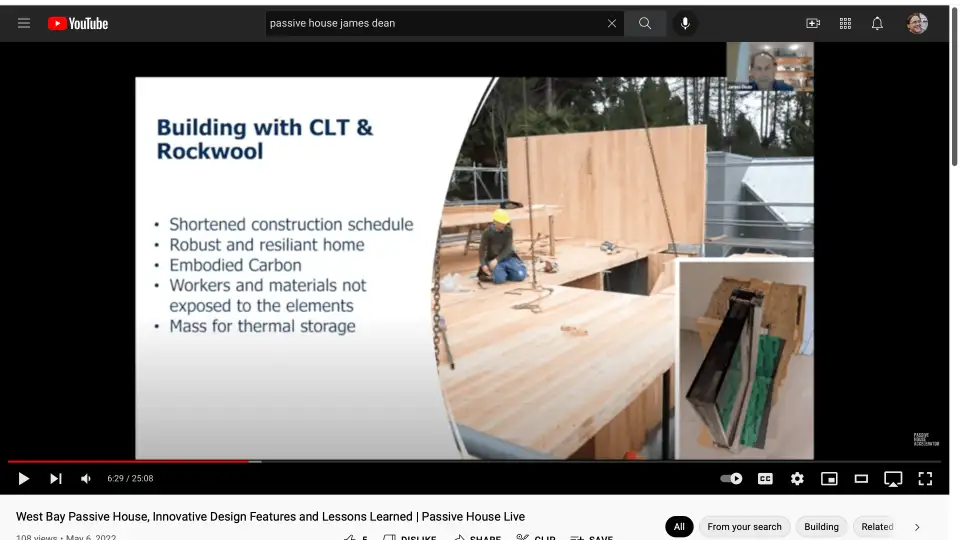
So, as mentioned, we built with cross-laminated timber. And at the time, the main reason that we did it was Naikoon had told me we could take about two months off the construction schedule. So, while they were pouring the concrete for the first floor, it was a factory in Oregon called DR Johnson was building those panels in parallel. And I also like the fact that it was built indoors in a climate controlled factory. Many of you probably know, in Vancouver, it's a beautiful city, but we're also known for our rain. And the idea of carpenters pounding nails in the pouring rain did not seem the best. But for me, having lived in the home for three years, there's a couple of learnings I had. One, just the whole construction with CLT just seemed so much more robust than building with stick frame construction. So, it was really, this is a home, I hope we'll be here for hundreds of years because of the materials that we used. Secondly, I learned a new term called embodied carbon and that building with solid wood panels like that is much better than building with steel or concrete. And I think the biggest thing for me was, and you'll see in that picture down in the bottom right-hand corner, you've got the CLT panel and then either side, we had six inches of rock wall, was the thermal storage that was able to be contained in the homes. And we'll talk about that in this next slide here.
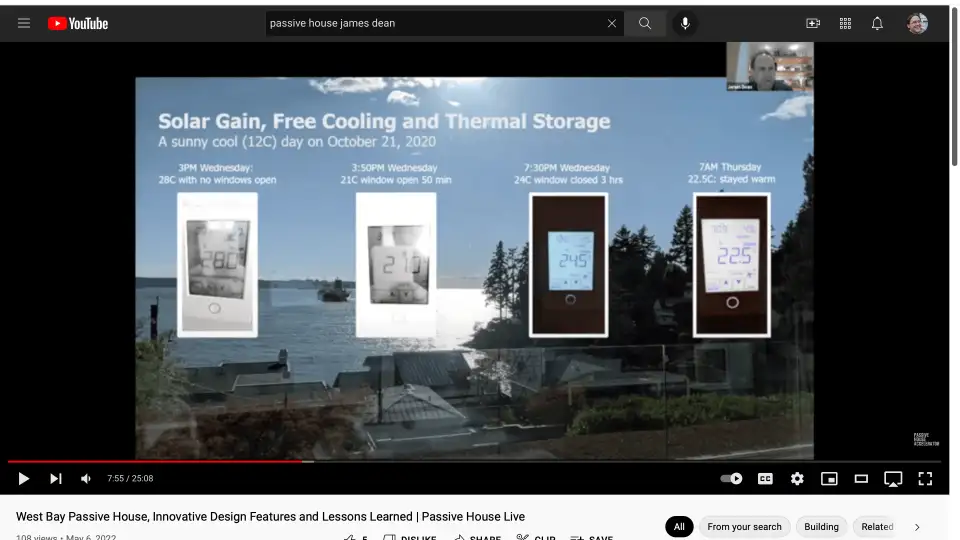
So, this was a day in the fall of last year. It was a little bit cold outside. It was about 12 degrees Celsius. And because of the solar thermal gain coming in, our bedroom was 28 degrees Celsius. So, that was three o'clock in the afternoon I took that picture there. And so we do have a heat pump that Stuart will talk about for cooling and heating, but what I did to cool the bedroom down was open the windows and doors. And so we're basically able to get free cooling and free ventilation. So you can see, for 50 minutes later, we were able to drop that temperature down to a comfortable 21 degrees. And then close the door, and you can see because of the mass in the envelope in the walls, the temperature had bounced back up to 24 and a half degrees. And then I took another picture the following day because I was curious, "How much is that temperature inside going to drop?" And you can see because of how well insulated the walls and the windows are that we just had a small drop in temperature.
The one thing I would probably do different now is put the windows on actuators and tie it into some sort of smart control system that knows when to open and close the windows to get that free cooling and free ventilation. Because what happens now is when you go up to that 28 degrees, the heat pump kicks in and we have mechanical cooling, and there's really no need to waste energy with the mechanical cooling when we can have the free cooling from the outside air. And the ERV we have does have a bypass in it to get some free cooling, but, really, I wish that when we're not home that those windows knew to open automatically. We've had days where it's been below freezing outside and a really sunny day and it's been 30 degrees. So, it was really surprising to me just to see how much heating we can get naturally from the sun. And you'll see on the pictures earlier, we've got quite big overhangs, which are great in the summertime for blocking the sun. But what's beautiful in the spring and the fall and the wintertime when we want that solar thermal gain and the sun's low in the sky, we get that on all three levels of the home.
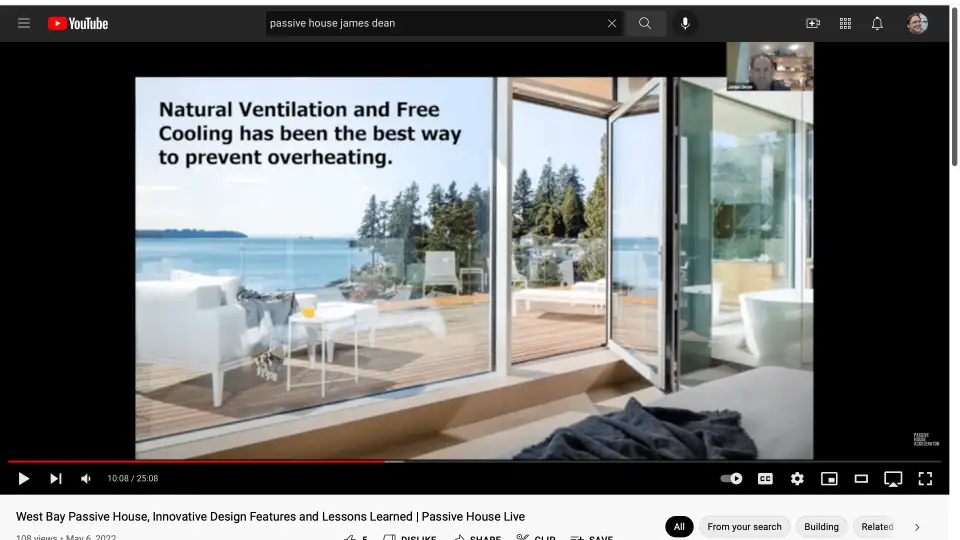
It just shows here that window there. So, we've got one door here and we've got a window in the bathroom there. And those are the ones that I open up on this level to prevent the overheating. So, I'm going to pass it over to Stuart to talk about the mechanical system that we've got and we're quite proud of.
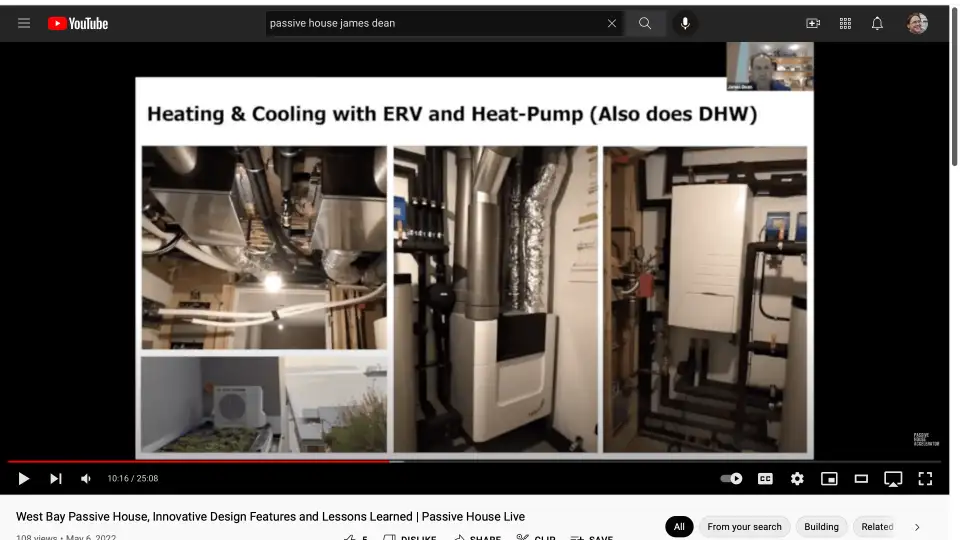
Stuart Hood:
Okay. Thanks, James. Yeah. So, the mechanical system, you have two major components. We've got the Zehnder ERV that might be familiar to a lot of people. That was the Q600. I think it was the first one that came into Canada. And then we have a Daikin Altherma heat pump system. The Daikin Altherma, yeah, it's a air to water heat pump, so very much like a mini split, but instead of air to refrigerant and then to air inside the house, it's air to water and then water to air within the house itself. So, it's a hydraulic system from a distribution perspective.
And what we did, we went with the pure Passive House methodology in that we used the air to do all of the heating and cooling of the house, so the ventilation air. So, what we do is in the top left-hand picture, you can see there's two boxes in the duct work. They're heating and cooling changeover coils. One of them does the upper two floors, and the other one does the lower floor. The lower floor has a slightly different lower profile because it's got a really deep overhang on that lower floor and it's connected to the earth. It's sort of built into a hillside, and so it's slightly different from a thermal perspective.
And so the heat pump takes its heat out of the air and then moves it through the refrigerant to the split heat pump. You see that on the right-hand side. What you see there is the hydro box. The refrigerant pipe comes into that and then transfers that energy into hot water. And it does two things. It heats the air through the ventilation system, but it also preheats the domestic hot water. So, when there's a call for domestic hot water, the heat pump ramps up, heats the water within the heat pump to about 55 degrees centigrade, which is then able to preheat the domestic hot water up to about 45 degrees centigrade. And then the electric heater within the hot water tank does the rest of that heat. And so it just goes to show that you can heat and cool through that ventilation air without the need for that supplementary system and without the need for other devices.
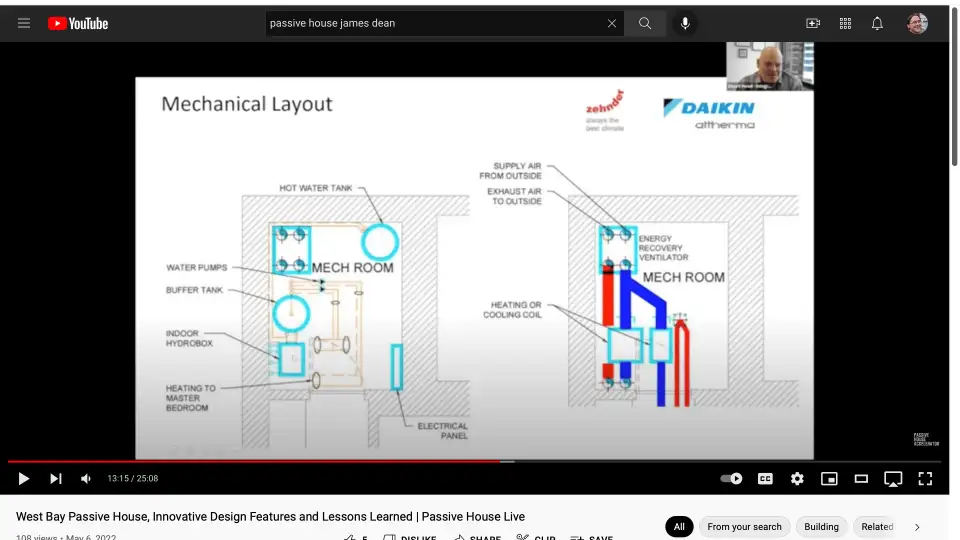
In terms of the layout, you can see there, in the top left-hand corner is the Q600. To the right of that is the domestic hot water tank with the preheating pipe going into the side of it. Bottom left-hand corner is that hydro box that I referred to. And just above that is the buffer tank. So, we charge that with heating water or with chilled water, depending on the season. If that's full of chilled water, then it stays cool. And the domestic hot water preheat doesn't cool that down, it just diverts. You can see there's a branch just in between the two devices. It branches around to the domestic hot water tank. So, it does swing that water from chilled water to heating water in that small volume of water in that pipe, but it doesn't change the temperature of the buffer tank itself. And then on the right-hand side, you just see the ventilation distribution there, the blue being the supplier going through those two coils in those two turquoise colored boxes of the heating and cooling coils for the floors.
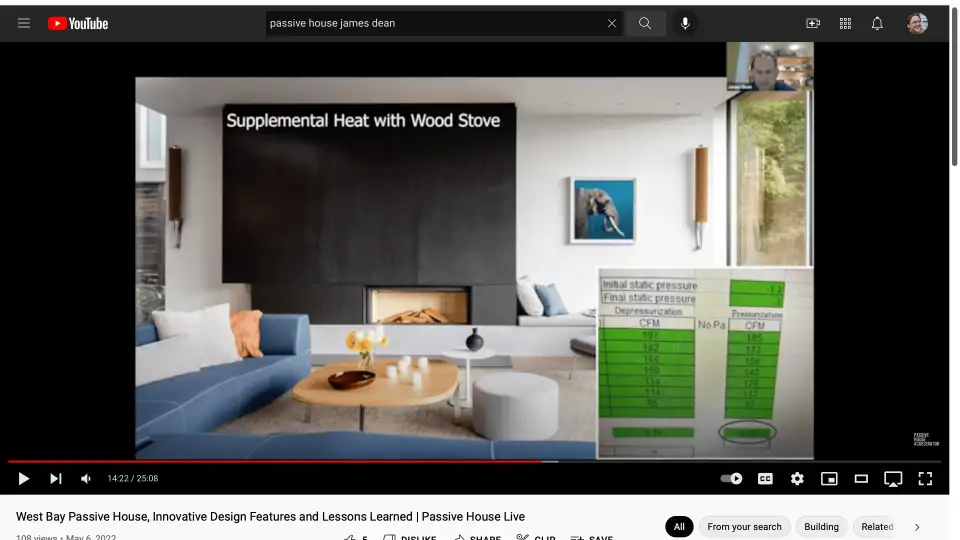
James:
Thanks, Stuart. So, one of the interesting things that happened over the last year was we had a heat dome out here, just probably some of the highest temperatures I've seen since I've lived in Vancouver for the last 20 years. And then we also had a real cold spell where I think it got down to minus eight or minus nine. And what was interesting for me was we didn't even really need to use that heating and cooling system through those events. So, in the wintertime, you'll see here, we were able to install a wood stove. It's from a Swedish company called Stûv. And we were essentially doing heating for the whole house through that wood stove. And then in the days where it was really hot, we just opened the windows and doors. And because we've got the ocean in front of us and the wind blowing across the water there, that's what we had, our cooling system. But it's good to know that with climate change and as temperatures rise or get colder that we do have that supplementary heating and cooling.
I mentioned earlier the blower door test. We were a little bit worried whether we're going to pass that, just having this wood stove in here. But there are dampers that have been installed with the switch over here, so when they're not being used, there is no air leakage going through that. And then there's a glass door that also slides along here. And then on two of the levels, we have sliding glass doors. And we were concerned with the seals that potentially we were going to get leakage there. But the suppliers of those sliding doors had the leak data that the whole team felt comfortable that we were going to still be able to pass that blower door test.
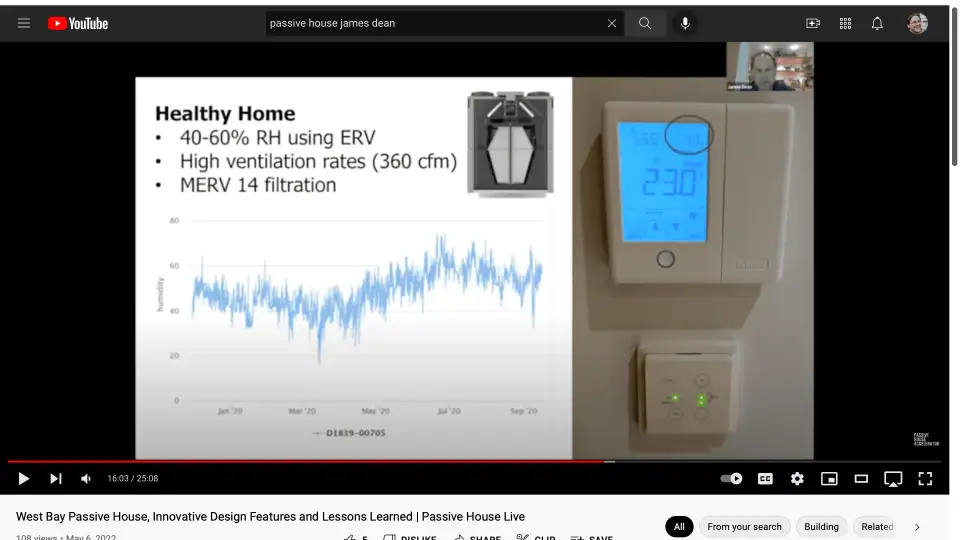
So, one of the things I learned through COVID was just the importance of relative humidity and that we really want to be in that sweet spot between 40 and 60%. And if homes dry out, it can cause the spread of the virus. One is these aerosols can float around more and, secondly, the mucus membranes inside can't fight the virus as much if it's too dry. So, we had some debates about, "Do we put an HRV in or an ERV in?" We knew down in the South you want an ERV and in cold climates you want an ERV. But what we decided to do was put an ERV in here to recapture the humidity. And we think it was the right decision. Because you can see here, throughout the season we were within that 40 to 60% bandwidth.
The other thing for health was filtration. So, yeah, the Zehnder unit comes with a MERV 14 filter on the outside air side. I'll show you in the next slide that we've had some issues with forest fires. And then the ERV is sized for about 360 CFM, so we've got continuous high air change rates through the home. And what was interesting is over the last three years, nobody in our family has been sick. Nobody's gotten the flu, or a cold, or gotten COVID. And I believe that's related to the relative humidity, the air changes, and as well as having great filtration inside the home.
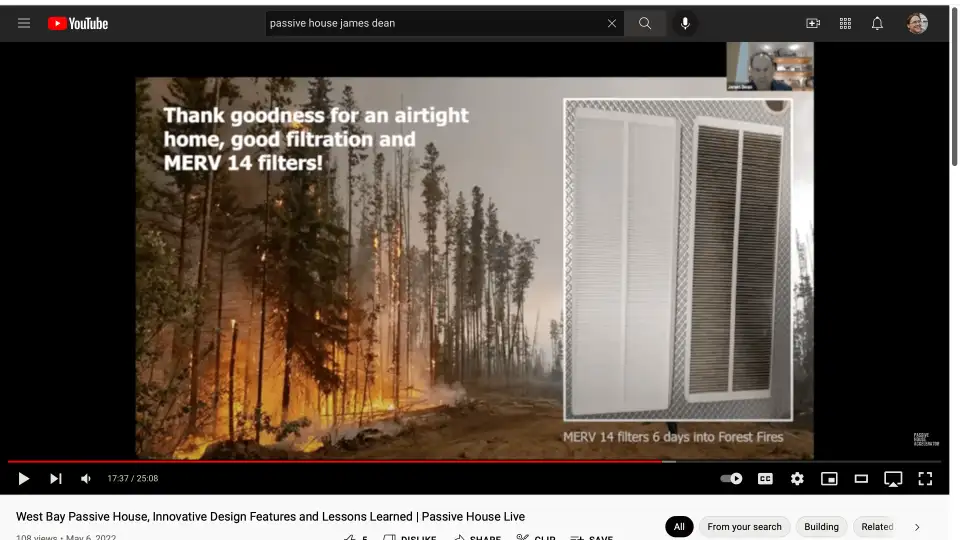
And so I think for the last three years, we've had quite bad forest fires either in British Columbia or down in Washington and Oregon where the winds have blown the smoke up. And so I changed out the MERV 14 filters, the smoke came in. And just out of interest's sake, I went and I pulled out the filter just to see how much particulate was in there. And that was six days later. You can see how black that filter was. So, again, it just highlighted the importance to me to make sure that we've got the right filtration, particularly on the outside air coming into the home. And, Stuart, do you want to talk? I know you and I had lots of debates about whether to exhaust the range hood and the dryer, and maybe talk about the approach we took and why.
Stuart:
Sure.
James:
And I'll talk about whether it was a good idea or a bad idea.
Stuart:
Yeah, yeah. There was a lot of debate over, "Should we take that kitchen air from the stove, from the range, and take it outside? Or should we use a recycling range hood?" And James was second-guessing, but I think one of the biggest things that drove it, actually, was the fireplace decision, right? These range hoods come usually, the standard range hoods that come, these big... Yeah, I think it was a Miele one or something like that, James. It was minimum 300 TFM or something like that. Well, when you do the depressurization test, you only need about 150 CFM to take this house down to negative 50 pascals. So, if you've got a fire on in that stove and then you turn your range hood on, you're going to take the pressure of that house down below 50 pascals, possibly down to 75 or 100 pascals with that much air getting exhausted out of it.
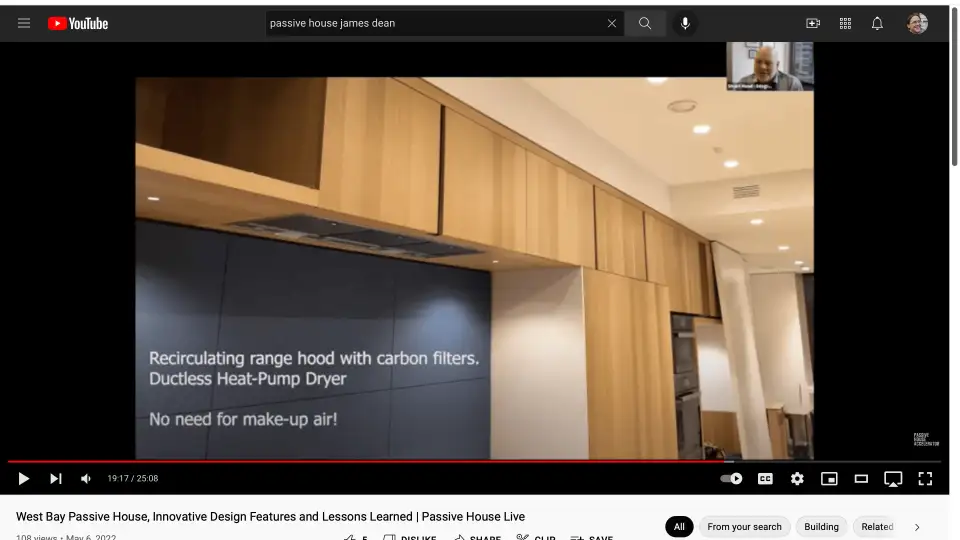
So, without a naked bare system or opening a window or something like that, you're going to potentially pull the products of combustion out of that fireplace and into the home when you open it up. And so we decided to go with the recirculating range hood. We ducted it from the range hood. You can see that slatted grill that's just in that downstand bulkhead, and it discharges out of there. And then you can see just six feet away from it is the kitchen exhaust. So, that's going directly to the ERV. So, we're blowing it directly over there so that we can grab that heat and moisture and take it out of there at high level in the kitchen. But it's already pre-filtered and taken any grease and dirt out of the air stream. So, how does it work, James?
James Dean:
Yeah. No. We've been really happy with it. Yeah. I think the main concern was just odors throughout the house. In the recirculating range hood here, we have carbon filters. And I think with having the returned air, the ERV separated from here, there's been no issues whatsoever. And I think for me, just the simplicity of the design and not having to put that make-up air into the home and then the energy loss associated with that make-up air. And then on the dryer, Stuart, I think we had some debates on that. We ended up going with a ductless heat pump dryer. And I'm happy we didn't need the make-up air for that. It does take a little bit longer to dry the clothes, if I'm honest, with the heat pump dryers versus the traditional type dryers. But, yeah, overall, we're happy with both of those decisions.
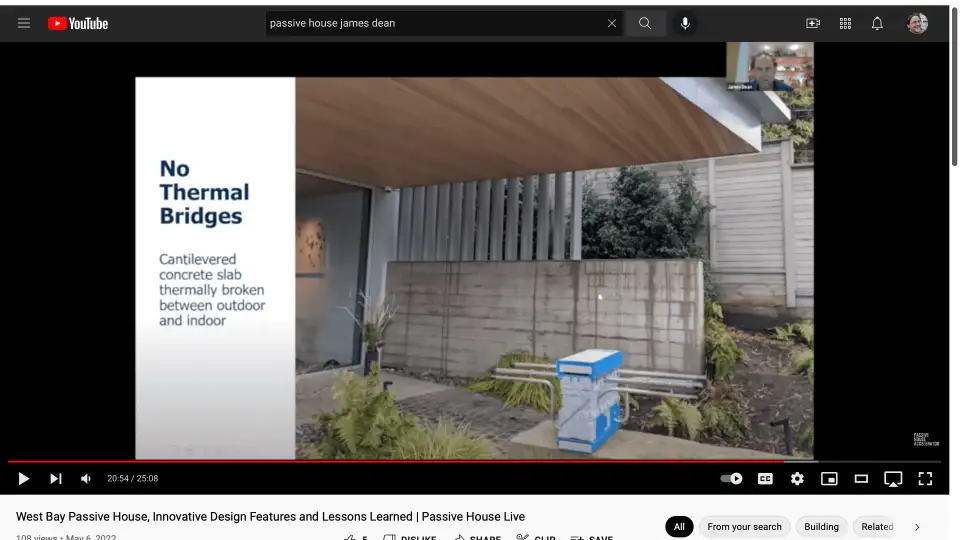
So, I'm sure as all of you are familiar, one of the key principles of Passive House is no thermal bridges. This was a really cool cantilevered concrete deck. I'll show you in the next slide here. There's really only this one post supporting this. It's probably a 15 foot long cantilevered deck here. And then inside the home is also a concrete slab. So, we needed to thermally break that. And we used this product from a German company called Schöck. It's called, I guess, the Isokorb. And so you can see this foam block and then there's this stainless steel rebar going through it.
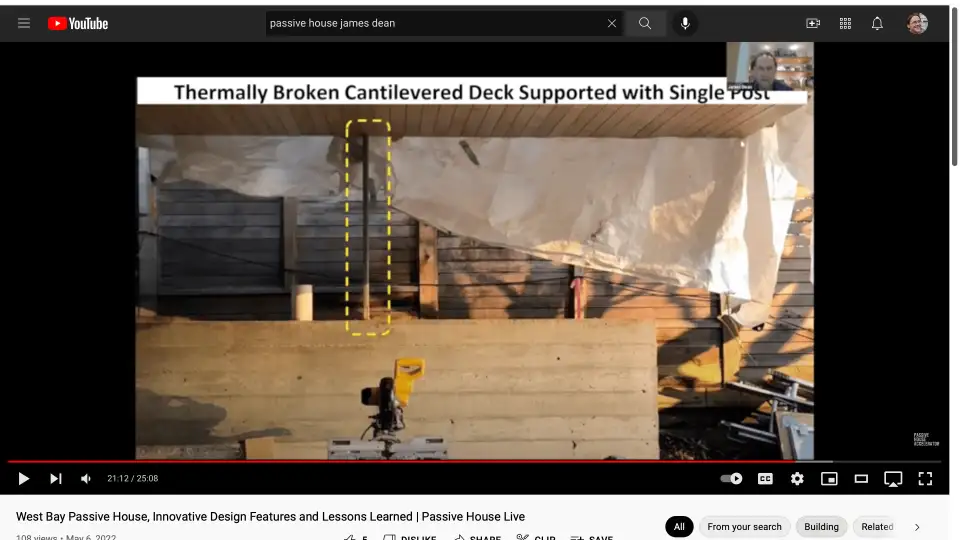
So, for me, I studied structural engineering, and I was just shocked that with that one post and this being cantilevered out and having a foam block separate these two, that it would have the strength. And so Aspect, the structural engineer, reassured me that it was going to be safe to stand underneath that. So, that was an innovative feature.
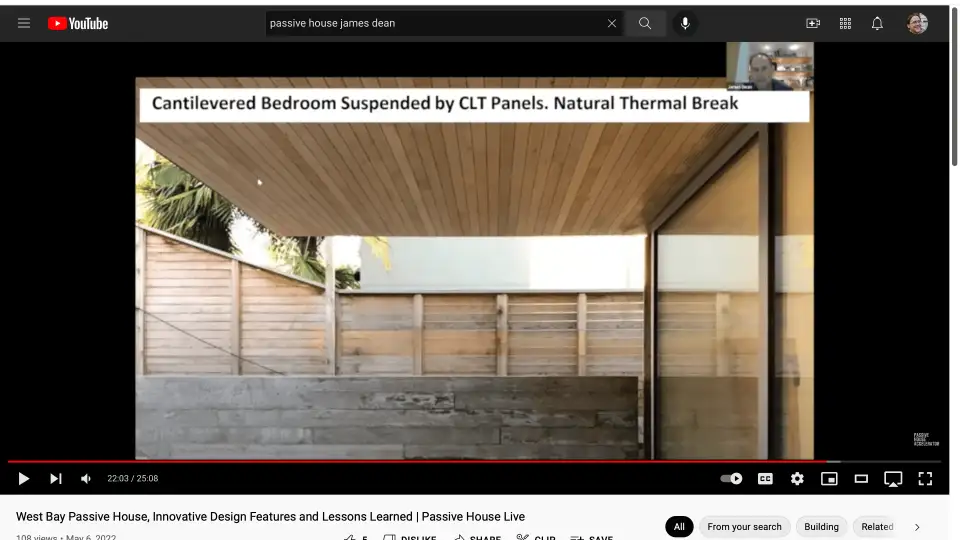
And then the other one I thought what was good, this is one of my son's bedrooms. And you can see that it's cantilevered off of the back and it's suspended from the CLT panels here. So I thought that was a cool design feature. And then the other thing was we didn't need to put a thermal break in here because the CLT panel runs continuously through from the outside to the inside. I think this is Doug fir, the CLT panel here. It naturally has that break there.
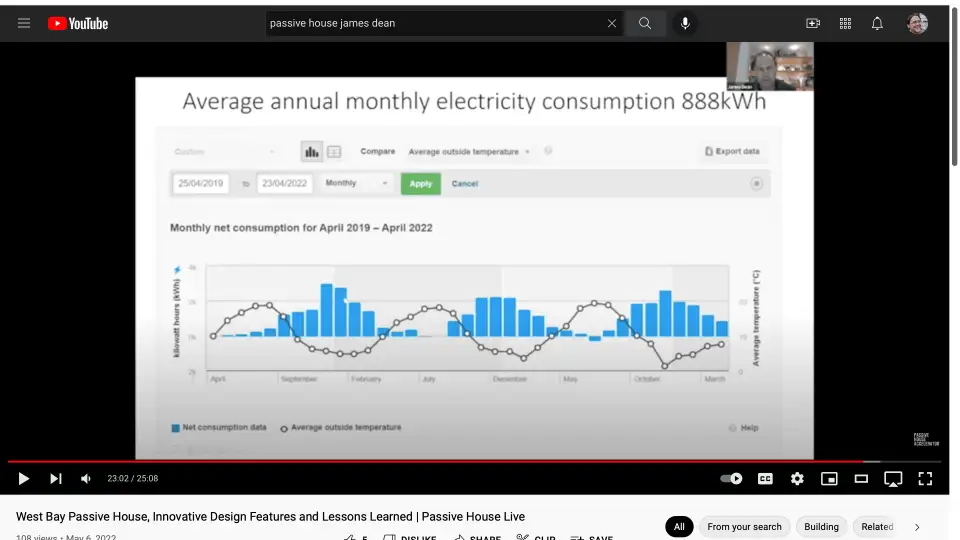
And then lastly, we were shooting for net zero energy. This is our BC Hydro, you're able to go in and track all your energy use. So, I looked at it over the last three years. And so our annual monthly electricity consumption is just under about 900 kilowatt hours. You can see here in the summer months, so sort of March through August, we're pretty close to zero, but in the wintertime where we're not getting as much sun on the solar panels, you can see we are purchasing electricity from the utility. We do have an electric car, and I do have two teenage boys that love to have long showers and leave all the lights on. So, I'm sort of blaming them for us not being at net zero energy. Stuart and I recently have done some sub-metering. So, we put these kind of donuts around to see if there's ways for us to optimize, things like I was talking about earlier of not having the heat pump come on when we get overheating in the bedrooms and having the doors and windows open automatically to get that free cooling. So, we still think there is some room for optimization.
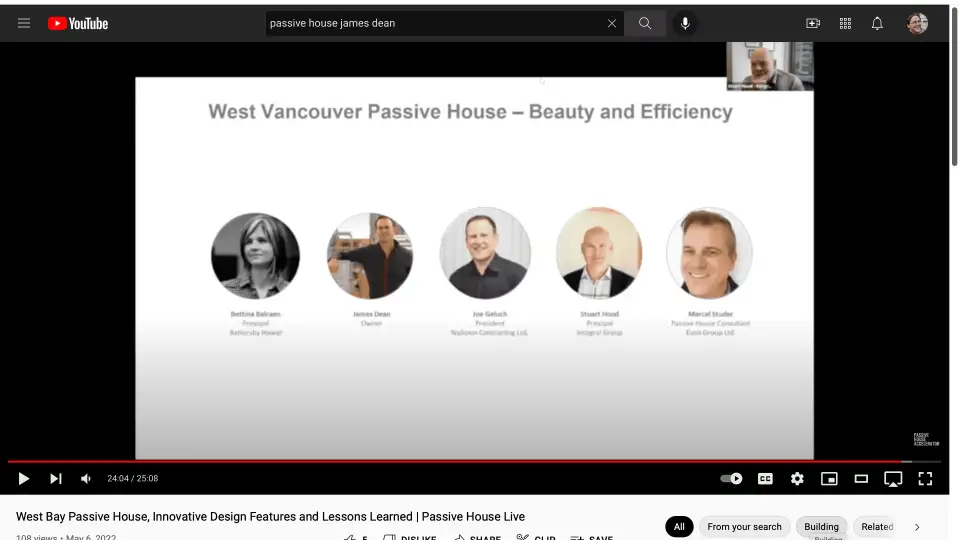
Stuart:
I think the EUI for this, for the people who are interested in EUI numbers as opposed to PR numbers, it's working out at about a 35 EUI over there. But I think there's a lot in the car. It's surprising. I've got an electric car as well and a similar sized home, but mine's not a Passive House home, and it's just surprising how much energy the car uses. I think the car, for my home, has probably added about 25% onto my energy bill for my home, right? So, it's quite surprising how much it... Especially in the winter time, right? You don't get the efficiencies that Tesla boast when you get into the winter time and the colder weather.
James:
So, that's it for the presentation, but just, yeah, finally, a big thanks to Stuart, the Integral team, Naikoon, BattersbyHowat. A lot of things we were doing at the time three years ago was new. And we took some chances, but my wife and boys and I are really happy with the house.