Bright Common studio director Jeremy Avellino and Holzraum System co-founder Ilka Cassidy stopped by PHA Live! to present Zero Six, Philadelphia’s first Phius+ 2018 Source Zero Pre-Certified multifamily townhome development. The team talked about what it takes to design and certify market-rate development in Philadelphia, highlighting the unique challenges of urban infill Passive House as well as the creative adaptability of a project team facing fluctuating economic markets and supply chain shortages. Read the full transcript below for the video.
Jeremy Avellino:
I'm so happy to be presenting to Passive House Accelerator. It is truly an honor to be here with Ilka and with my team. So, first of all, can you hear me okay? How's the sound? Doing all right? All right, great. Before we get started, like I said, if you have a question, toss it in the chat. We're going to try to get to all of them before we're done. I want to start off with who we are. So we are Bright Common, an a award-winning architecture practice in Philadelphia, Pennsylvania founded in 2011. And we have a simple slogan: high concept, low-carbon, all people. We design buildings in this age of adaptation that we're all finding ourselves in. And that includes, for us, deep energy retrofits, market rate and affordable passive housing and mixed use multifamily projects ranging from two to, so far, 120 units and beyond.
And tonight we'll be showcasing a project we designed for Argo Property Group in our hometown of Philadelphia. The focus will be more on what it's like to develop and certify a project like this through a pandemic. I just want to say, give a caveat, it's probably more at a high level to talk about this process. There'll be some focus, some detail, but there's not going to be a lot of these deep dive hyper focus zooms, like you might normally see in construction tech. So I think we're going to be back for hopefully a part two for that stuff. So lastly, all of our work is a team effort and I just want to say one of the greatest pleasures of my career has been to get to know and learn from this wonderful person, Ilka Cassidy of Holzraum System. Ilka and I have worked on many Passive House projects together, including the design of their second Holzraum System house, which just received source zero certification.
So I'm just really happy to be doing work with her. And, Ilka, you want to just take a minute to introduce yourself? I think everybody knows you, but go for it.
Ilka Cassidy:
Yeah. I mean, that's definitely some introduction here. Thank you. And I can just give it back to you. It was definitely awesome to work with you on the single family home, but also Zero Six. It's definitely been quite a journey since the beginning. So I actually had to go back very far into my archives in my Phius folder to dig out all my WUFI files and everything from the start to now. So it's been a journey. Yeah, just to introduce myself, I'm co-founder of Holzraum System. And typically when we present or we talk about, we actually talk about our process of translating design intent into some pre-fabrication, parts based modeling and turning it into prefabricated panels. While we do that, we always look at thermal rich free detailing and air sealing. And we also do Passive House consulting and energy modeling. I definitely like energy modeling quite a bit.
Jeremy:
It's no good.
Ilka:
Yeah. And I was fortunate enough to work with Jeremy on this project. And I just wanted to shout out to Steve Hessler, my Holzraum partner. He's right there. Thanks for showing up. Yeah, I'm excited to show you this project.
Jeremy:
Thanks, Ilka. Let's get into it. So I wanted to start off with a little background to talk about we're in Philadelphia, Pennsylvania in the United States. And this is a slide from Philadelphia's climate action playbook and it just talks about what shapes Philadelphia's carbon footprint. And I think it surprises a lot of our clients.
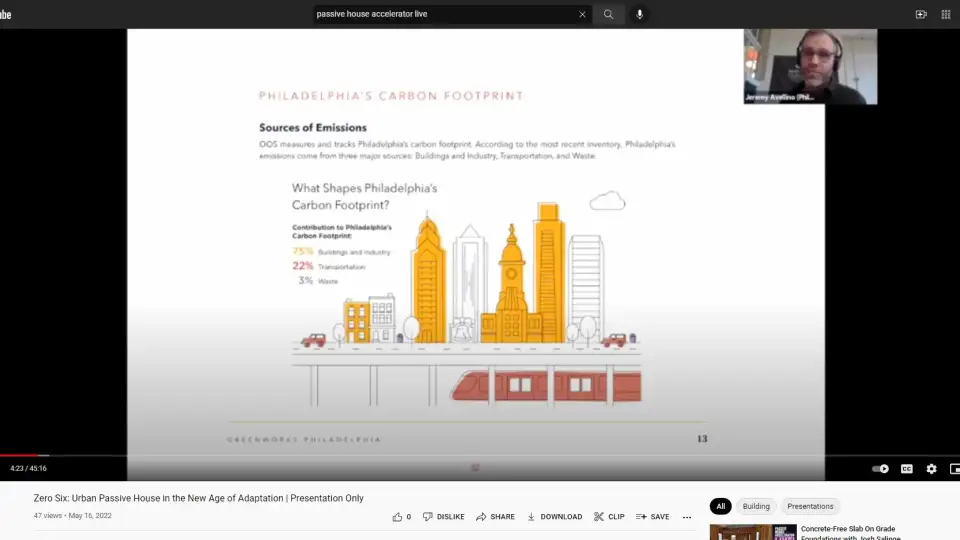
This is Philadelphia's climate action playbook, which is a really wonderful document we show all of our clients. And they're all always really shocked to learn that buildings and industry are 75% of our local carbon footprint. They all think it's going to be cars and it's transportation and waste are about 25%. So that matters, but the carbon footprint of your location matters. For us in a dense urban city, buildings really matter. And so all of our work as architects must respond in a meaningful way.
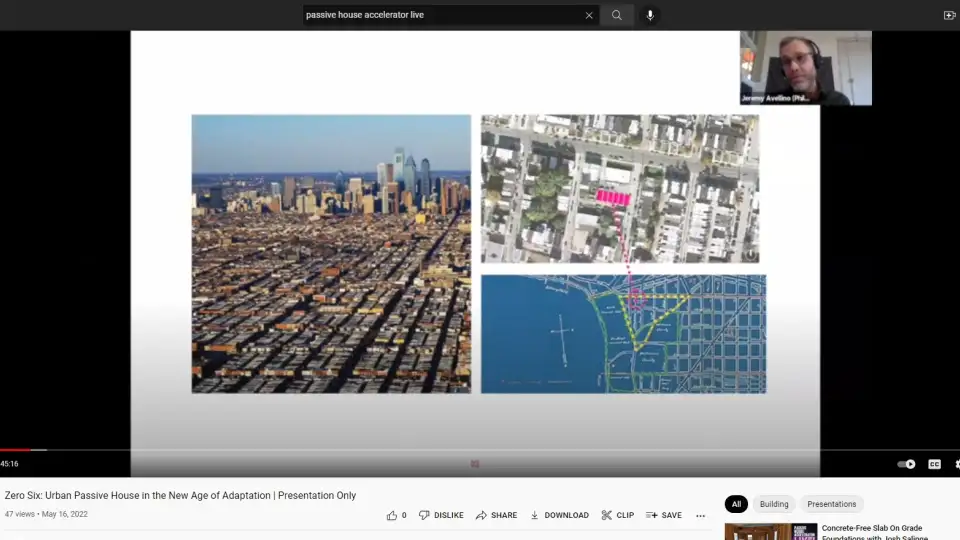
Zooming in a little bit, as you can see on the left is Philadelphia, my hometown, and it is a city of homeless, which includes plus or minus 400,000 attached rowhouses and tens of thousands of empty lots. These conditions have been a proving ground for a decade long design laboratory for us to experiment with urban infield Passive House at multiple scales and markets, pushing us to develop increasingly flexible and iterative strategies that can be applied to almost any site. If you can learn how to do this stuff in a mixed humid climate zone and a post industrial city, you can do it anywhere. So it's never boring and I could say that after 10 years of doing this, it is never boring. I wish it was some days. So from retrofits to fire ratings, encroachments, easements, zoning overlays, underpinning and increasingly bureaucratic city government in all manner of unforeseen and unsavory existing conditions, it has and continues to be an evolving and invigorating landscape within which to design the future of housing. And all of that was before the pandemic.
So we're also fortunate. We also design within a community and I can tell you that it's amazing to be part of the talented and supportive community of fellow Passive House designers, like Ilka and many others, consultants, engineers, and also in this culture of people who are striving in this very DIY way to make the world a better place. I wake up every day and I just feel like it's an amazing time and a place to live and work in and to practice in. Our specific site, if you look at this map down on the right, is in a neighborhood called Allegheny-West or it's also called Paradise. It is the small yellow triangle. It's only a few blocks wide and it's bounded on three sides, this green shape. It's bounded on three sides by three historic cemeteries, so the neighbors call it paradise because it's like being in the afterlife.
Read into that as you will. In urban infill construction, we don't get to pick orientation or adjacent conditions, but we lucked out here as the long axis, you can see on this top right image, these are the six town homes here, that faces south. That never happens. And also there's no buildings to underpin on this site, which also never happens, but our luck ran out a little bit during design as we found out very quickly that the street, Lippincott Street, that they face on did not have a sewer. So the developers had to foot the bill for a private sewer, so that will kill your insulation budget right there. All right, I'm going to try something. Shannon, did you get my message about the countdown timer?
Shannon Pendleton:
No, I did not. Kim?
Jeremy:
Okay, cool. That worked out. Do you have a countdown timer on your iPhone or something or just a countdown time or whatever?
Shannon:
I'll find one.
Jeremy:
So one of the things when we did in the pre-call was I realized I kept using the term rowhouses. And if you're not from Philly, you don't know what a rowhouse is, you may not know what a hoagie is. We're not going to talk about hoagies right now. So I want to be a little bit more inclusive and so I went to the trouble of preparing this presentation within the presentation. And so, Shannon, if you could keep time for me, I'm going to attempt something I've never done before and that is to share a brief history of the Philadelphia rowhouse PechaKucha style to do 10 slides, 20 seconds each, totaling three minutes and 20 seconds. And so put your seatbelt on. This is going to get a little bumpy. Let me know when you're ready, Shannon. We got to synchronize our thing.
Shannon:
I am synchronizing my clock. The timer is ...
Jeremy:
I actually have a countdown timer to my interval timer. We're going to do this right. Five, four, three, two, one. Oops. All right, Quaker and Pacifist, William Penn's Green Country Town was a revolutionary, but naïve, idea in 1682, when he founded Philadelphia. His first land purchases quickly subdivided the sprawling lots, immediately abandoning his ideals. He did get his wide streets on a rectangular gridded plan, though. Industrial capitalism demanded dense worker's housing along the prosperous waterfront, proving once again that with few exceptions the built environment is nearly always the love child of economic and political forces made with the cheapest available materials decorated in the style of its time.
118 years later in 1803, Thomas Carstairs, a feisty, no nonsense Scottish immigrant carpenter designed to build 22 brick rowhouses for William Sansom, creating the first speculative housing development in the United States, what is now the south side of Jeweler's Row. Why is Philadelphia a red brick city do you ask? And I heard you ask. Well, English settlers who survived the devastating Great Fire of London in 1666 embraced Georgian construction with shared fire resistant party walls. Plus, Philadelphia sat on a high quality brick clay bed so extensive that after two centuries of mining has still produced more than 200 million bricks by the year 1900, adjacently spurring the patented invention of multiple brick making machines. What is a rowhouse you are still asking from the Philadelphia rowhouse manual? Philadelphia rowhouse most simply is a one to four story house, occupying a narrow street frontage and attached to adjacent houses on both sides.
What are some rowhouse types you asked? And I did hear you. There were many variations of rowhouses to house the rich and poor, cheek by jowl. At 300 square feet, the bandbox, or trinity, was America's original tiny house with 10 foot by 10 foot floor plates. Carstair's row is a London house plan doubling the tiny trinity. Wealthy Philadelphians dwelled in Georgian townhouse, like this one on the bottom. By the end of the 19th century, Philadelphia had become the workshop of the world with 50 square miles of rowhouses and factories, in large part owing to the expansion of the humble rowhouse. Later described as a successful mix of immigration, employment, coal, real estate and banking, it had become the quintessential object of industrial Philadelphia. In 1893, 25 million people visited the Columbian exposition in Chicago, which included Philadelphia's full scale display of a two story workingman's house.
This exemplar for egalitarian housing stoked the desire for the American dream so much, though, the visitors to the exhibit wore out the floorboards, or so the legend says. With their built in adiabatic walls, rowhomes make excellent candidates for Passive House retrofits. Here's a diagram of a foam free, all electric one we designed that made our clients very happy. For all the info you could handle, and then some, on the subject, download collectively authored Passive Rowhouse Manual from Green Building United. North Americans today predominantly live in detached single family homes with two prominent exceptions. The majority of New Yorkers live in multi-family buildings with 20 or more units and in Philadelphia about 60% of us live in a single detached residence or what we call rowhomes. Does this make Philadelphia uniquely unAmerican or radically progressive? You decide. How'd I do? Let's hope you got any of that in. So that's the rowhouse. Now you know what it is.
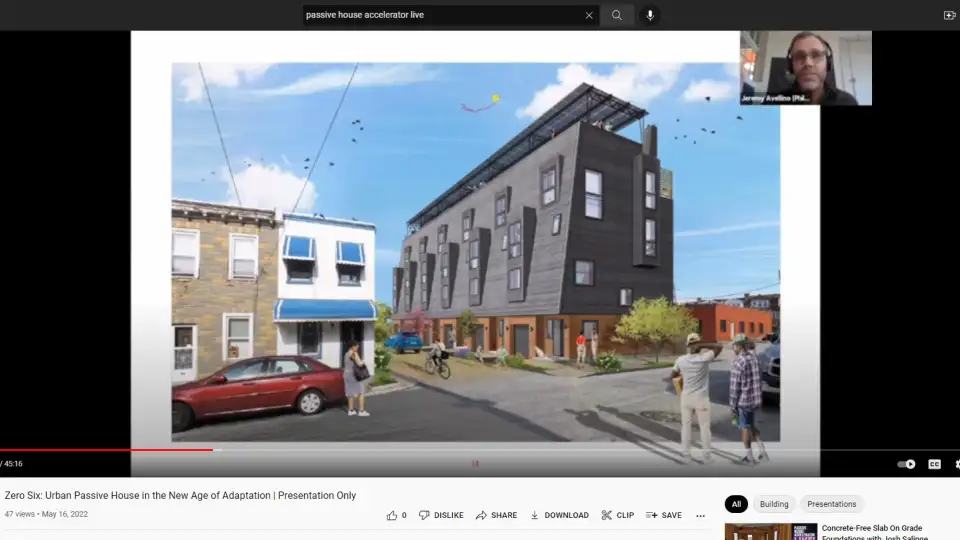
I'll do a PechaKucha on the hoagie at the end of the thing. And I promise Ilka's coming up any minute. I want to talk about next about what it takes to make the next generation of row housing in what we're calling this new age of adaptation. So what you're seeing here is a rendering of the project we're going to present called the Zero Six. It is six attached town homes, which in some ways they're more multi-family than multiple single families. And that is going to come up time and time again, but in a neighborhood filled with smaller attached homes we didn't want it to look like a big box. Philadelphians hate multi-family housing. We hate it, including the ones I design. After subdividing the parcel, we were able to fit six four-story town homes and they each have a footprint that's 20 foot, 10 inches wide, which is really wide for a rowhouse. And 31 foot, seven inches deep, which is actually really shallow.
So they're really tall, small wide houses, if that makes sense. The home's massing is meant to nod back to traditional Philadelphia rowhomes, like the way Carstair's Row has these mansard roofs and gabled roofs with dormers at the fourth and fifth floor, things like that, but in a modern way. So it has this three story, what we're calling a super mansard overhang in the carport broken up with one and two story dormers, just to throw things off a little bit. They're clad and slate shingles on the front and painted fiber cement lap siding in the rear. There was really limited space for solar PV on this project, but we were, thanks to Ilka's help and Solar States, we were able to attain Phius+ 2018 source zero energy pre-certification with the canopies. And more on that in a minute. And finally, what you've been waiting for, Ilka Cassidy.
Ilka:
Yeah, so I was very fortunate to be part of this team, which was very exciting to look at this row of town homes. And, as Jeremy talked about there, it's interesting because how do you look at a building like this? Is it a single family home? Is it a multi-family? How do you wrap your head around it? And I think initially we all sat down, we're like of course it's a single family home because it's going to be sold individually, it's going to be metered individually. So going through Passive House certification, of course we would treat them as single family homes. And that's basically how we started out with this project. And what was really interesting was that we signed up for this with Phius for this project and there was a deadline to when we needed to sign up before they switched completely over from the 2015 certification goals to the 2018.
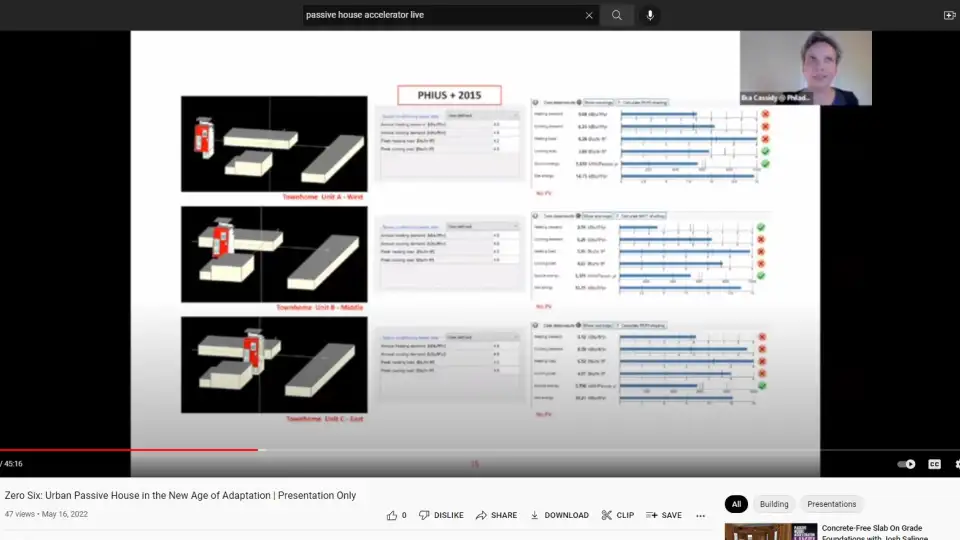
Somehow I knew about that deadline and I was like, "Jeremy, let's just sign up before and so that we have both choices," because I didn't really know. I hadn't really modeled anything through the 2018 criteria, so I wasn't sure what's going to be beneficial for us or not or what the changes were. So we basically started out with modeling this under the 2015 Phius certification and treating everything as a single family home. And basically we have three different units, one on the west side, and then there are four in the middle, and then one on the east side. And when Phius switched to the 2015 target or certification, what they did is to make everything climate specific. So your targets that were automatically generated in Phius were climate specific at that point, which differentiated them from PHI at that point.
So, as you can see, each one of those cases has the same targets in terms of heating, cooling, demand and loads. And there's also a certain source energy goal. I think it was a little over 6,000 kilowatt hours per person per year. So I modeled each one of those units and I actually originally signed them up, each one, six different buildings with Phius. And then we realized it's impossible to get there. And these were already modeled with very hefty assembly, so it wasn't just going from code or starting out with code. This was, I think, already R-40 walls or something. So something pretty substantial and we realized that there's no way that we can actually get there. And, as you can see, what's interesting is that each one of those models pretty differently.
So the one in this Phius 2015 scenario, I think the middle one actually had maybe the most chances of actually getting certified at the end. Again, we realized this is not going to happen, so we switched over to the 2018.
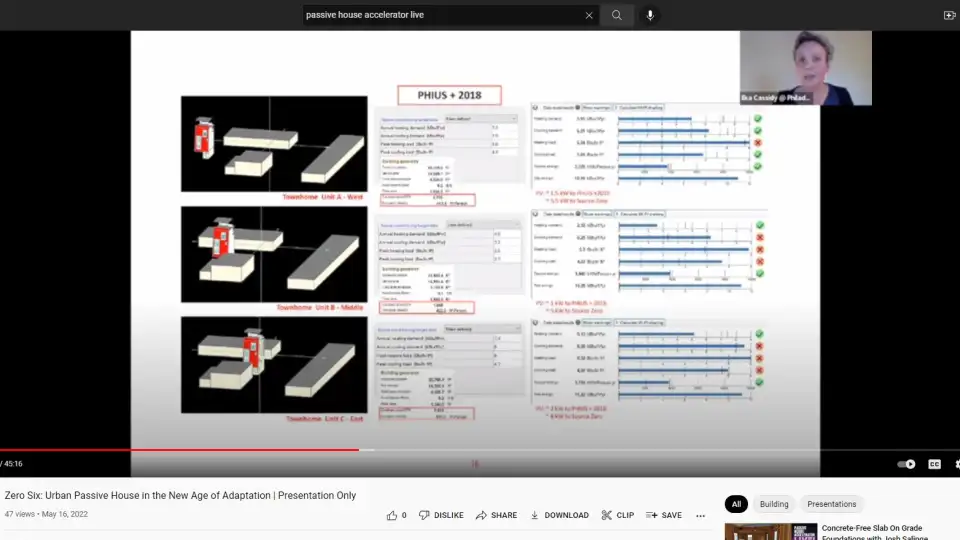
So this is now switching over to the 2018 and the big change there was that it wasn't just a climate specific, but also a project specific. So there's a calculator online that determines basically your targets for heating, cooling, demand and loads. And I have to input certain criteria that makes its projects specific. And then each of those scenarios basically gets a different targets. And for the middle one, that actually didn't work out so well. So it's really interesting because overall you can see that your energy demand is the lowest on the middle one, but because of how the calculator works with looking at the envelope surface it actually has way stricter target goals than the other two scenarios. I think only, though, the one on the west actually had chances to meet certification.
Jeremy:
Yeah, that's right.
Ilka:
Yeah, so we were scratching our heads pretty heavily and we were like, "Okay, what are we going to do?" So then we actually thought maybe we'll scrap the whole single family home, town home, idea and just look at it in terms of one big block as basically a multifamily project. And that's what we did, so next slide.
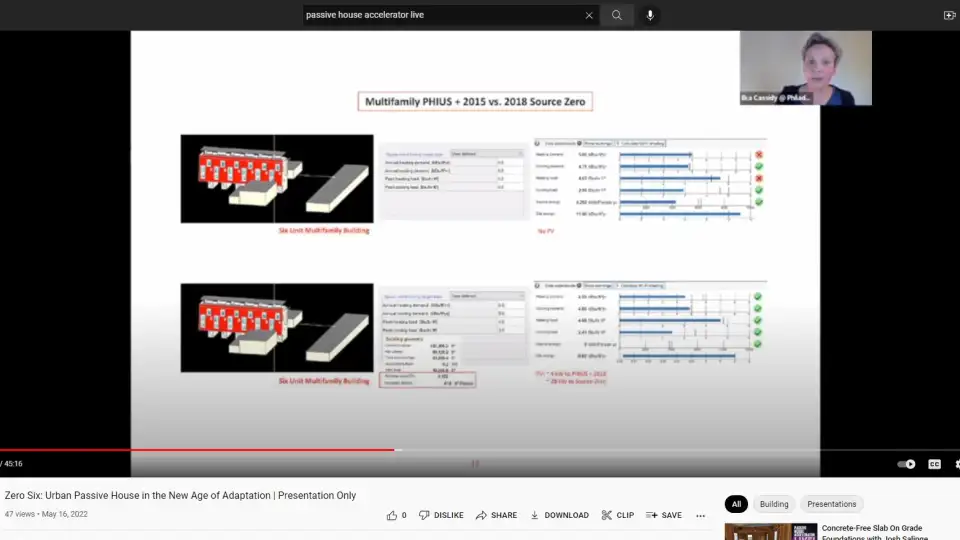
And, again, I ran it through the 2015 versus the 2018 certification goals and it turned out that the 2018 were actually working out better because our targets were calculated differently, were project specific. And through all of this, these are all the same assemblies. I didn't really change any assemblies up to that date. So this is really just going through how everything behaves under basically the same circumstances. So we saw that 2018 is going to be the way to go.
If you go with the Phius+ 2018, one of the things that changed was that the source energy goals were getting stricter. So if we wanted to meet source or Phius+ 2018, we realized that we had to include some PV. And then at that point we were like, "Okay, once we include some PV, we might as well go all the way out." Yeah, basically that was our marching order. We set our parameters and we knew how we were going to certify and how to go about it. Next slide.
Jeremy:
And it's interesting to note, just so everyone knows, another thing in Philadelphia that I always try to not design houses with these fussy roof decks, but apparently you cannot sell a new construction home in Philadelphia if you do not better roof deck, that gets used three days a year. That is just the truth. You will not win with any developer, even if they agree with you. They can't sell it. And these also have garages, too. I'll get into that in a minute, but you'll see that they stand on one leg because it's more of a carport than a garage, but that's becoming a thing, too. Yeah, you can leave that alone, but when you have to put solar on, it means a canopy. So there's a lot of extra costs.
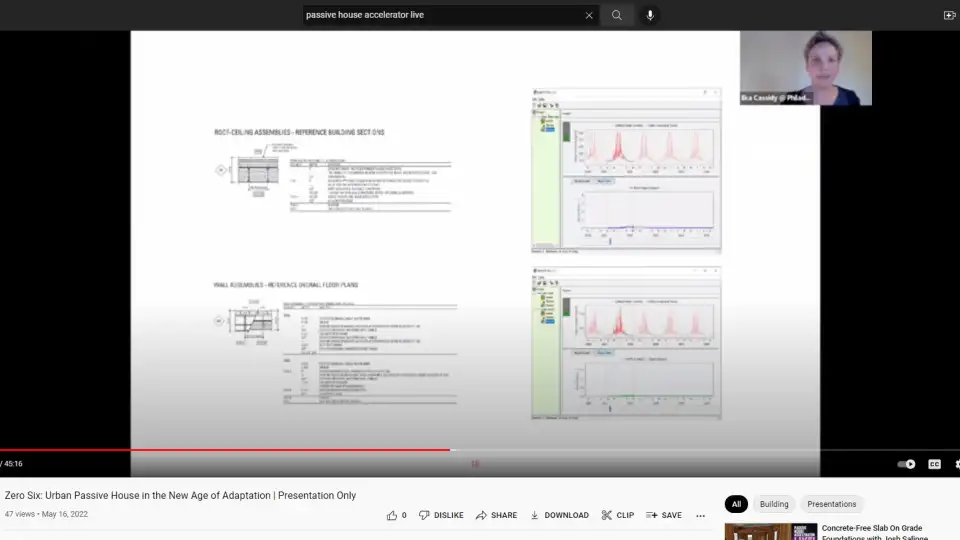
Ilka:
Please. So now knowing what we were going to do, we went ahead and Jeremy and Jordan from Bright Common really just dove into all the details and assemblies together with the energy modeling. They basically created all the drawings for this. And at this point I would like to just talk about a little bit what it actually means to go through certification because a lot of times these days a lot of people say we build Passive Houses, meaning that they're highly insulated and blower door tested, but they might not necessarily go through actually the certification. And I just wanted to point out how much value there is in actually going through certification because there is a whole other very, very knowledgeable third party that's going to look at all your drawings and basically prevent you from making mistakes.
So there are certain criteria for assemblies that are set by Phius. And if you don't meet those criterias, they ask you to do a hydrothermal analysis just to make sure that everything is going to perform well and not start molding, and make sure that your indoor air quality is okay, so I feel like that's a huge service for the developer, for the architect, everyone who's responsible for this, for me. I mean, I can look at it and say it looks good, but I think it's something totally different if there's these people that are so experienced really just making sure that everything is good. So we did have to do a couple of hydrothermal analysis, one for the roof, and it turned out to be okay. It turned out to be safe. And then one for the wall assembly and one big reason for that was because there is different conditions for the siding or the cladding. So on the bottom there is brick and brick really holds moisture pretty well. So it was important to look at is this all able to dry out accordingly, so that was helpful. That's something that we went through and got a green light. Next slide, please.
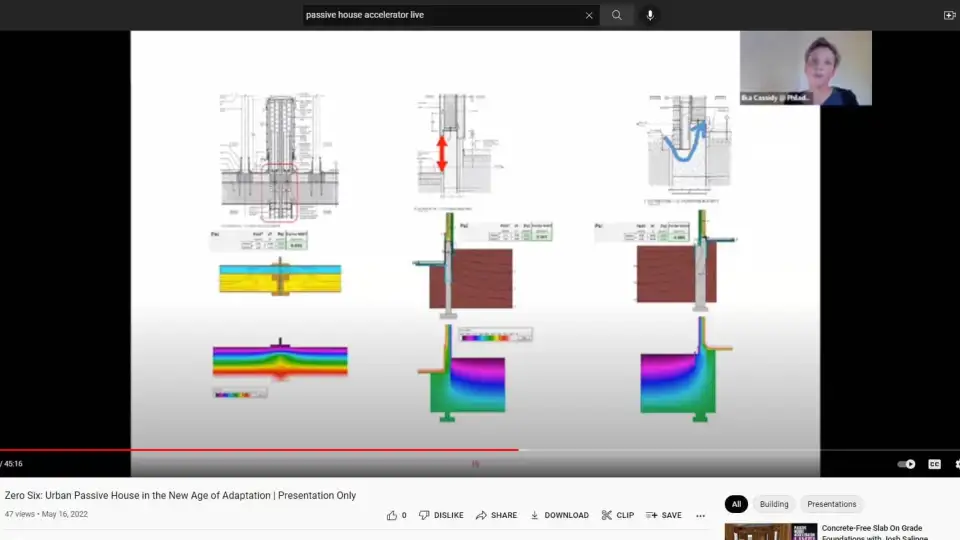
And then the other thing is thermal bridge analysis. So, again, Bright Common dropped these details and we submitted them. And then Phius looked at it and is like, "We're a little concerned here, we're a little concerned there. We can see that there's a thermal bridge there." So one thing is to do the thermal analysis to get the value to put into the energy model, because that's something that has to be counted for, for energy purposes.
And the longer, of course, this condition is the more impact it has on the energy model. And we did see some changes there. And that's the interesting part, too. Once you dive deeper and deeper into the project, there are all these things that come up and the needle swings here and there. And sometimes it's a little bit nerve wracking because you still want to stay under that target line, but, again, it's all valuable information because, besides just the heat loss or the thermal bridge itself, what's really important, or accounting for it, it's really important to also look at condensation risk. That, at the end, turns into mold and bad indoor air quality. So it's really important that someone really looks at this and says, "Okay, this is a thermal bridge. You have to account for it, but it is safe. So you can build it that way." You're not going to encounter any kind of moisture or condensation accumulating at that spot. So, again, very, very valuable. So we went through all of this. We basically went through a few review rounds and we're almost there. And then the pandemic hit.
Jeremy:
Did it happen? I don't remember anything at this point.
Ilka:
I remember getting that email.
Jeremy:
That was a tough day, Tom Hanks got it and this project. That was a tough day, but, hey, here we are. We're still in it.
Ilka:
Yeah, so I got that email from Jeremy saying, "Well, I guess we are stopping this." And I was like, "Jeremy, we're almost there."
Jeremy:
Oh, my gosh. We were literally at the finish line.
Ilka:
Yeah, there were just a couple of things that we just had to submit and we're like let's just go for it. There are things where we could optimize this, definitely. I think definitely going through these rounds and adjusting and everything, we didn't realize at the end, and there is a little change in the Phius calculator, too, that at the end we realized these assemblies are definitely robuster than we need them to be, but we can't really have...
Jeremy:
I felt like we were just like just get it in and get that placeholder in. It was 99% figured out. We knew there was still things figured out, but if we did not get that pre-certification it was never going to happen ever.
Ilka:
Exactly.
Jeremy:
Ever. It was done.
Ilka:
So we just went for it. Next slide. And we got that pre-certification for source zero. So that was a good day, but we didn't know how it's going to ...
Jeremy:
And we did not know what it meant, but it was a very good day. It was good news in a sea of particularly confusing news at that time in human history.
Ilka:
Yeah, so it's back to you, Jeremy.
Jeremy:
Thanks, Ilka. It was really, really fun and to walk down memory lane, too. We've been at this for a while. I mean, that's thing, is we designed this project prior to the pandemic and had such a good process with Argo. They felt wonderful to work with and still committed to this stuff. We've been working with them for years and they came to us, designed some multi-family work and weren't familiar with any of this stuff. And walked them through it and, really, very into it, thirsty for it, but move from just making buildings all electric at first to just stepping up to beefier and beefier assemblies, introducing ERVs. And then when they came across this one, they're like, "Well, do you want to go for Passive House?" And it was like we have to. And that's been the everyday, is should we keep doing this?
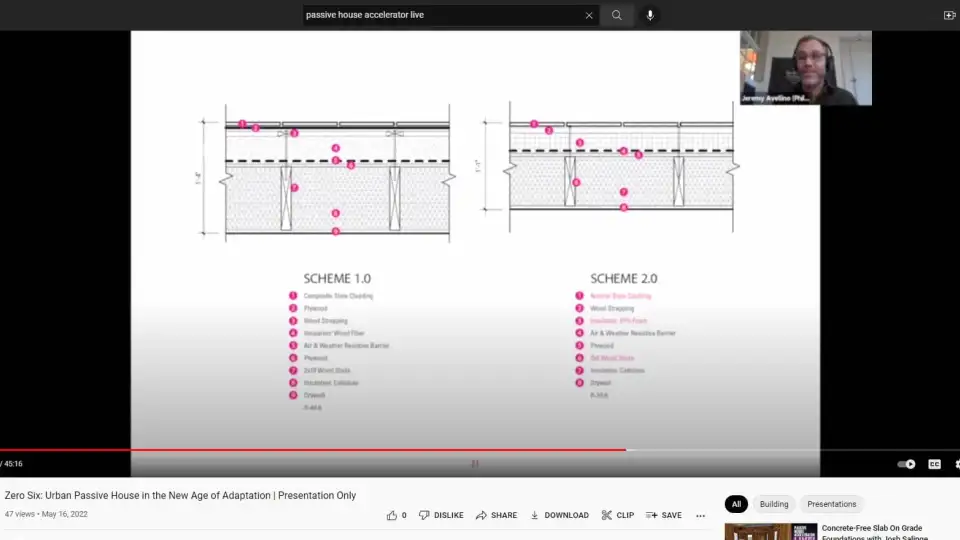
Yeah, we have to. It's impossible, but we have to figure it out. So it's this really wonderful and tight relationship to the point where sometimes I'm just yelling, "No, we have to," and I'm just going to raise my voice to pretend that's going to make a difference. And I'm going to do all caps texting and pretend that makes a difference. T9 predictive texting even. Anyway, so one of the coolest things about Argo is that they decided to become post-pandemic, after it died, it came back months and months later. They said we're going to self build this thing and that's the only way in hell it's ever going to happen to have a fighting chance of making this. And they even became certified Passive House builders in the process, so just big shout outs to David Ross and Jeremy Terr and Neil Henner and all the crew.
They went for it because it's bold and every day continues to be a real challenge. And that's the new age, adapting within the adaptation, and we'll get to that. What you're seeing here on the left is some of the assemblies pre-pandemic, post-pandemic after it got a little bit of a booster shot. Probably too soon for those jokes. We should just cut that from the recording, but the one on the left is our low embodied carbon wall. Most of it is our go-to plant and wood based materials, like we love wood fiber exterior insulation. It's four inches out there. Two by eight, the vertical walls we're able to get two by eight. This banked front wall was a little funky to deal with. Nobody knows if it's a roof or a wall to this day.
And we just threw a two by 10 for now. We knew it was too much, but there's a lower R value branch in the wood fiber, as much as we love it. And that can make it difficult to pass these condensation sniff tests. And it's a little more expensive, so we had to go a little bit less on the cladding. And so it's composite slate cladding out there over WRD. Sadly, the lesson learned after looking at 20 manufacturers is they all require this extra layer of plywood outside of the exterior insulation to keep it from cupping once the sun hits it. It was really disappointing. So, again, we got it in and said we're going to deal with this later. We know we're going to redesign it.
This wall assembly is not making total sense right now. So supply chain shortages and everything everyone else is dealing with has led to a redesign of the wall, which really all made us look at this again. For instance, we finally got wood fiber on a project for the third time and David went to order it and was like, "It's two years out." I'm like, "That's not even a lead time. That's the time it probably takes to make a new plant, I would imagine, and develop a ... It's just insane. And mineral wool was out a year. Okay, great, let's just get the good foam. Polyiso was out for six months. You couldn't get it anywhere. EPS, I think David drove down and got it himself. Something like there's a wild story there, but he got the last of the EPS in the world and stuffed it in a warehouse. It was like hoarding insulation.
That's what we were up against. And I know you were, too. It's a tough time. So scheme number two on the rights where we're at now, three inches of EPS exterior insulation. Two by eight framing for all of the exterior walls. This has a higher R value per inch slightly. Ilka can talk about this. We could have made a two by six framing. Two by six worked in the WUFI model, but Ilka, God bless her, said you got to have a buffer. Always have a buffer. And I said, "No, I live my life fast and loose. I'm from Philly." She said, "No, you have a buffer. I'm from Germany. You have that buffer." Thank God because it saved our asses in the end and Ilka could tell that story.
Ilka:
Yeah, I just wanted to go back to the changes after the pandemic because basically it wasn't just the wall with all the challenges that Jeremy just explained. It was also a huge switch in our window spec that drove a lot of this because, again, as I mentioned before, the building that we had pre-certified, we realized that we could have slimmed that down already, but we still pre-certified it. We used all the best of the best materials and or what we felt like low embodied and really high performing windows and everything. And then we basically entered this second round and really evaluated is what we pre-certified really what needs to be built, which we knew it's a no. So what could we do here? So besides the switch to different materials, there was also a switch to a window that was slightly lower in performance. And we all know how much impact windows have in a WUFI model.
So that changed quite a bit. So we basically went for the wall assembly went back up to two by eight wall, but also realized that there is the solar heating coefficient in windows have a pretty big impact, too. So if we went with a slightly higher solar heating coefficient, again, we would've made it to the two by six wall. We also were aware, and there was quite a bit of talk at that time, about specifically in multifamily homes, Passive Houses, that there is a danger of overheating. So we were very concerned about that because we did not want to, or Jeremy and David did not want to, build a house that is great in performance, but uncomfortable for the occupants. So we actually picked a window that had a lower solar heating coefficient to avoid overheating, but that meant that we actually had to go back to two by eight wall instead of two by six. And I'm very proud of that decision because it's just going to get hotter, right?
Jeremy:
Totally.
Ilka:
So we don't want to just blast air conditioning into this home.
Jeremy:
And the developer/builder was very amenable to that. Even though the framing costs were going up, they understood the idea of a contingency, even if it was a thermal contingency. It made a lot of sense to them.
Ilka:
Yeah. So then what happened is, because there are so many changes, we actually had to resubmit for pre-certification. Typically, if there are smaller changes, you can basically just log it during certification, but changes like this, which is basically almost all of the specifications for the envelope, required a resubmittal. So we basically started not from zero, but from the beginning and we did not have to change any of the geometry of the building, so that was good from a WUFI perspective because we didn't have to ...
Jeremy:
And a zoning perspective. No reamendments for building permits or anything, so that's really good.
Ilka:
Yeah, so I was basically figuring out, playing the whole game again, where how do we get to meet certification here? And what happened is that so formally we had these robust assemblies and we were easily able to cover the solar to meet source zero. By switching to less robust assemblies, that actually had an impact on the solar canopy.
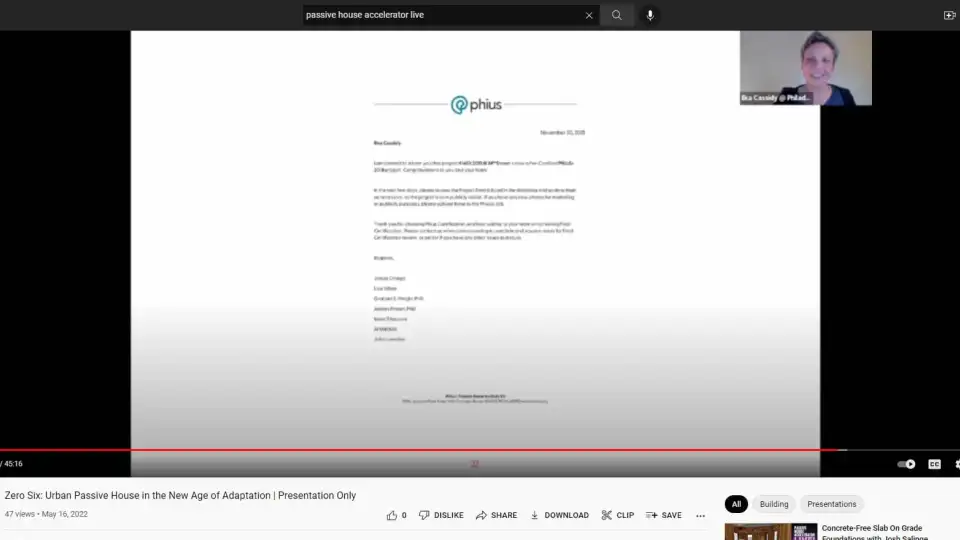
We weren't really sure if we can still meet the source zero, so the next round of certification was actually then certified as a Phius+ project. We knew if we are able to meet the requirement for the PVs, that we could switch that to source zero once we get there, but this was our second certification for this project. And then it changed again.
Jeremy:
Changed a third time. Third time's a charm, friend. Third time's a charm.
Ilka:
Yeah, so because we got the news that everything got so expensive.
Jeremy:
Solar panels got COVID. They're out.
Ilka:
Yeah.
Jeremy:
Turns out massive steel canopies to hold up solar panels, that came in far more expensive. Price of steel went up, price of labor, price of everything went up. Everything's crazy. They came in higher than anticipated, let's put it that way. It wasn't just the steel, it's just everything and we're just looking for ways to value engineer it. And I really thought, again, that the Passive House was done, but we were going to save a couple hundred thousand dollars just getting rid of the solar panels and the canopies. As much as that stinks, I said, "Okay, well, Passive House is out, too, but Ilka and I talked and we thought about it." And there's this whole myth about green power purchase agreements with Phius, where if you can't put solar on you just purchase green power. I've never been able to figure out, nor do I know anyone who has been able to figure out, how you work that out when you're selling individual market rate homes to people on spec and you're supposed to include that into a mortgage clause or something like that.
It's a myth. And so I know that it's a great idea, but that's why I think Phius 2021 Core was developed to just give so much more leeway. And Ilka worked with Phius. They were extremely helpful and said do we have a green building rating system for you. We know how hard your life is and they worked it out. And it was music to our ears. As sad as it is to lose these things, it allows us to keep certification and offer solar panels and even the canopies as a buyer option because we had already had the sub-structure installed for the canopy to attach to the extra engineered lumber. So we're solar canopy ready, as crazy as that sounds. That could be a buyer option if there's presales. And I'll link those presales in the chat in case you're looking to move to Philly. These are a deal. I'm telling you, these are a steal. There's nothing like this in Philly. Come and buy one. I'll be your friend.
Ilka:
Yeah, basically we had to do another switch to then the 2021 Phius Core certification, which allows us to not need PVs or solar. And that's what Jeremy said before. And I didn't want to bore you with more WUFI pictures, but basically what happens ...
Jeremy:
I love those Wolfy pictures. They're renderings made in a geo city's website. They're just amazing. Or Microsoft Draw from 1993. I love them. They're great.
Ilka:
Yeah, maybe I should have put them in. Anyway, so what happened once I switched over to the 2021, so there's another calculator which calculates your targets slightly different. And I don't want to get into all the differences. I don't know if I could actually explain all of this, but basically our targets changed a little bit. And because we had a buffer from the beginning, we were still able to meet all the heating and cooling targets in order to not need PV. To hit that target for source energy, we have to make a little change to basically be a little bit more airtight or pick appliances that are slightly more energy efficient, but on the end we have to provide parking spaces for electric.
Jeremy:
You have to provide one EV ready parking space per unit. It's so funny how this locked in. If they didn't have garages, you're out. Which is sort of weird because, and this is just a bit of a critique on the whole thing, is the whole system, including the building code, nothing is set up for urban infill work. This is my big violin right now. 10 more seconds, but nobody's thinking about urban infill work and the retrofit work. You can't set up a system for that. They can't. So we got to stop thinking about single family homes as these places where you can just toss a car in the driveway. We don't have any room for that stuff in the city and cities are dense and sustainable and all the infrastructure's there. So even to have the EV ready space, we just got lucky because we happen to have our non-urbanist garage in these things. But if we didn't, certification was out, so it's worth noting that. I think that should be optional, frankly.
Ilka:
Yeah. Well, for us, it worked out.
Jeremy:
It certainly did.
Ilka:
So we went from '15 to '18 to '21 and here we are.
Jeremy:
And who knows? '23. Hey, let's keep going. Who knows? We'll get it done. How about that?
Ilka:
Yeah, let's get it done.
Jeremy:
Thank you, Ilka.
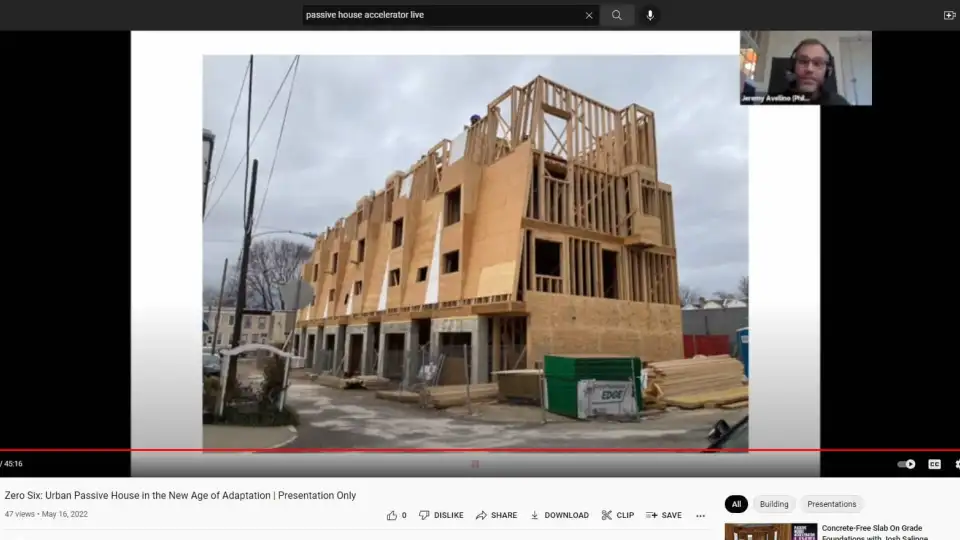
Here's a picture of it under construction. I might toss up a Instagram page here in the second, too, but completion date, 2022. Supply chain shortages and some unfavorable subcontractor pricing has kept all of us on our toes, triggering ongoing design and detailing revisions to the installation, window install, cladding. By the way, with that EPS foam we need far less layers. So with EPS, we're looking at natural slate cladding now, which is favorable in pricing to the plastic stuff. That was radical, so we're looking at some folks in Pennsylvania and Vermont to stay regional. As long as CUPACLAD from Spain doesn't just buy them all up tomorrow. They're just buying everybody out. All that aside, we are adapting within these forces that it just feels like a meta adaptation. We're adapting within the forces while adapting to the climate crisis.
It's been a non-binary evolving circus of adaptation. Super fun, just amazing. Solar canopies, they're out. We talked about that. Green power purchase agreements, we talked about that, but it's just been super, super fun. Anyway, let me see if I can actually bring that up because there is a better.
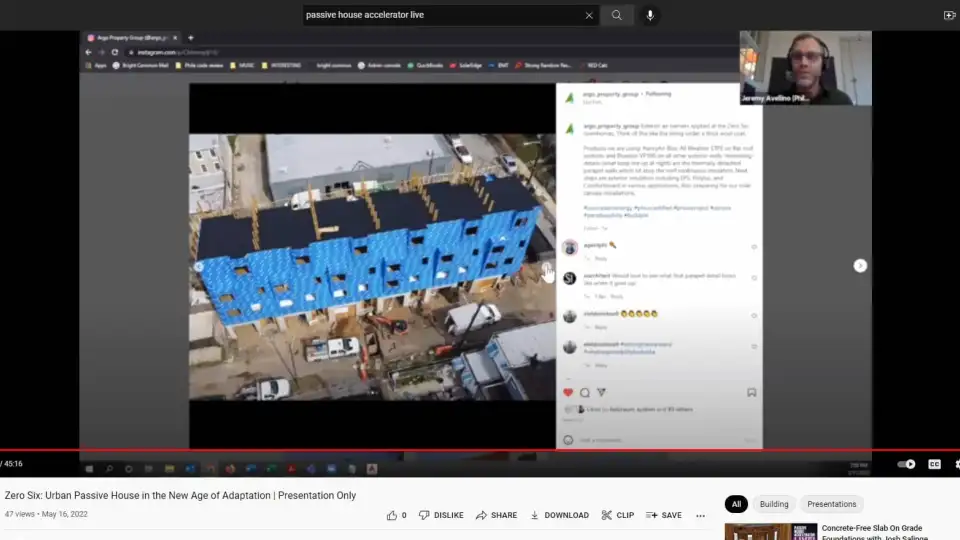
Look at that. This is more recent. This is Argo's Instagram page. Woot woot. Isn't that great? There we go, little drone footage. Look how small that street is. We wanted to make it a Woonerf or living street, but nobody in Philly knows how to pronounce that, so it just couldn't happen.
Man, how do I get out of here? There we go. Figuring life out. Okay, here we are. Think we got some time for Q&A. That's all we have, unless, Ilka, you want to jump in there. I wanted to have a little bit of time for chit chat and these are project stats.
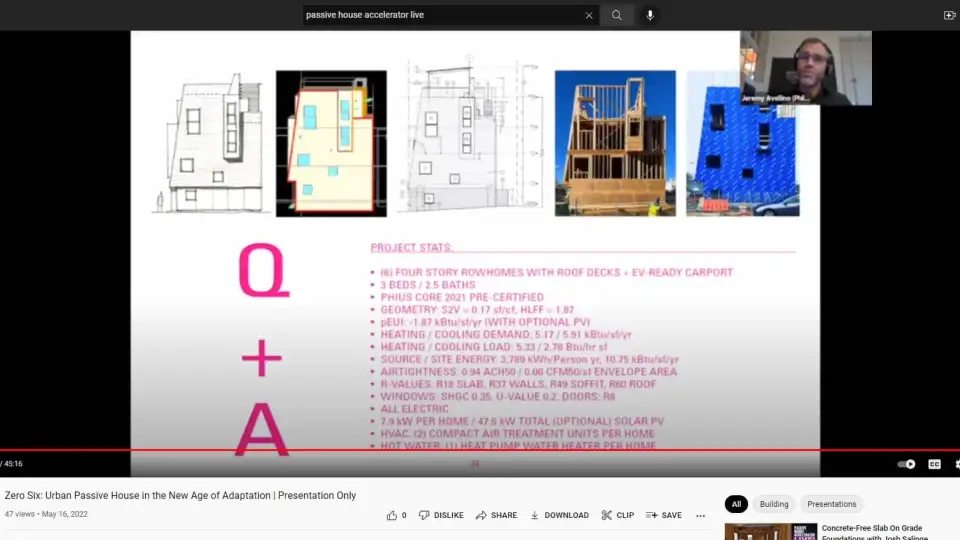
And I'm not going to go over them. You can read them. Feel free to nerd out. You can ask questions about them, but just the stuff at the top there is like I'm always really proud of this. And it's always so rare when this happens, when you have a concept sketch by the brilliant Amanda Bonelli. And then it gets to Ilka Cassidy. Look at that, amazing Microsoft Draw rendering she did. It's so beautiful. WUFI models, so cool, and then the construction document elevation, and then framing, and then beginning to do cladding and waterproofing and all that.
And it just all looks like the same thing and that's always amazing to me when that happens because of all the things that could prevent that from all the way going through. So thanks so much for your time. It's been a real pleasure.