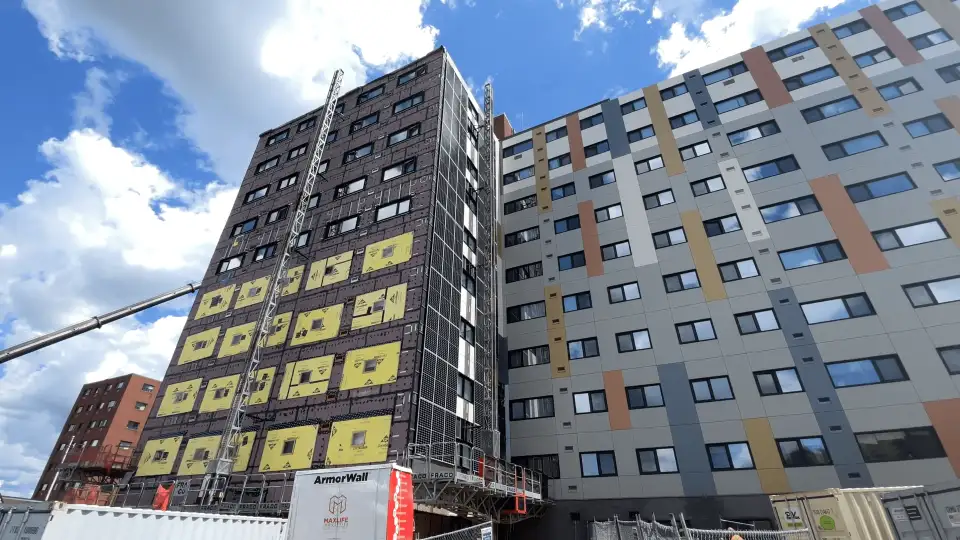
“We call this project the Salem Opportunity because most of the exciting things we got to do were because of the building condition,” says Julie Klump, Vice President of Design and Building Performance for Preservation of Affordable Housing (POAH). She stands outside of the massive, 281-unit Salem Heights development in the city of Salem, Massachusetts, which is currently undergoing a retrofit that will hopefully be certified by Phius when the project is complete. Though the team has been met with a lot of surprises throughout the retrofit, Klump maintains that these unexpected challenges allowed them to try out new solutions and high-performance components that they may not have considered.
Salem Heights is not POAH’s first major retrofit, nor is it its first Passive House project. POAH is a non-profit developer, owner, and operator of approximately 13,000 units across 12 states in the Midwest, Northeast, and Mid-Atlantic (plus Washington, D.C.). The organization is dedicated to promoting economic security, racial equity, and access to opportunity for all by preserving, creating, and sustaining affordable and healthy homes. In some cases, this means new construction (see “Putting Passive House in the Loop”). In other cases, it means acquiring existing affordable buildings, and then retrofitting them to improve occupant health and comfort.
One of the more unconventional aspects of Salem Heights is that the retrofit is occurring while occupants are still living in the buildings. To minimize the inconvenience of being temporarily displaced, the team created columns of hotel suites on each floor (two per floor). Occupants need only move down the hall while their unit is under construction. Once it’s complete, they can return to their unit.
However, what makes Salem Heights truly novel not only among POAH’s other projects, but within the world of high-performance building more generally, is that it is being retrofitted prior to the release of Phius’ retrofit certification program, and it may serve as a pilot program that better informs Phius of some of the more common complications and obstacles that are likely to arise while performing a deep energy retrofit on a multifamily building. Given such a unique relationship, this project may receive more leniency than future retrofits seeking Phius certification, though certification for Salem Heights remains an open question even now with construction ongoing and the project slated for completion in June of 2023.
Long before this retrofit was initiated, POAH—and the residents of Salem Heights—faced a more immediate challenge: keeping the property from becoming market rate. When Salem Heights went on the market in the early 2000s and was acquired by POAH, its affordability contract had expired. Home to around 500 residents, the property is a crucial source of affordable housing for the city of less than 45,000, and the local government recognized the need to extend the contract. After working with the city of Salem to finance the acquisition of the property in 2003, POAH managed to prevent the conversion of Salem Heights to market-rate apartments, but the acquisition costs did not leave much in POAH’s budget to perform a comprehensive renovation at the time. Ultimately, POAH was only able to invest $3 million in making improvements to the property.
By 2018, it had become clear that Salem Heights was in need of a more substantial rehabilitation, so POAH applied for and received $55 million in tax-exempt bonds from the Massachusetts Development Finance Agency (MassDevelopment) and Low-Income Housing Tax Credits (LIHTCs) from Massachusetts’ Department of Housing and Community Development. The financing in place, work on the site began in 2021.
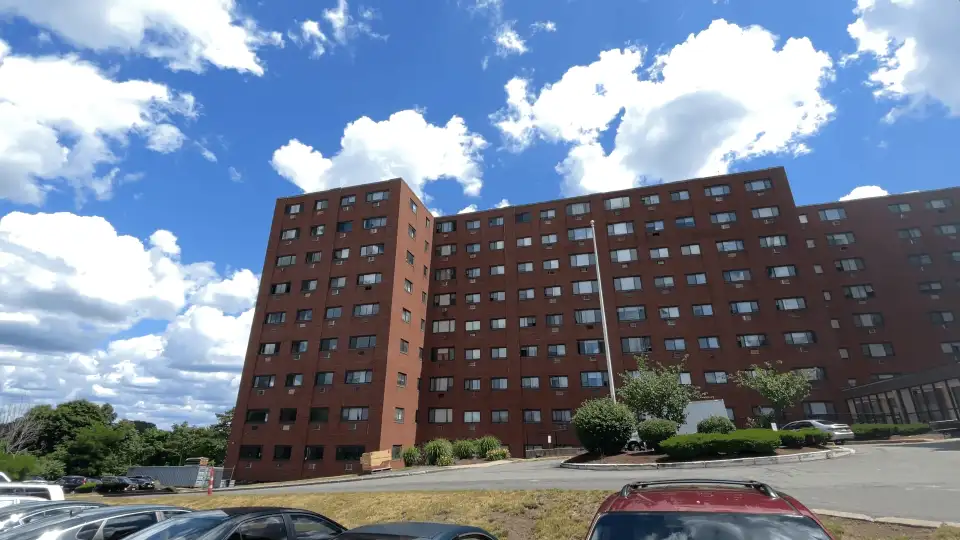
The First Salem Surprise
Salem Heights was originally built in the early 1970s as affordable housing under a U.S. Department of Housing and Urban Development subsidized loan. It consists of two buildings—one that stands at nine stories, the other at ten—that are connected by an enclosed hallway. Of the 281 units located across the two buildings, 274 are rented to households earning no more than 60% of the area median income (AMI). Before work commenced on the property, Salem Heights looked like other HUD-subsidized buildings erected in the decades following World War II—particularly those that populate bigger Northeastern cities like Boston or New York—down to the autumnal coloring of their brick façade.
When the team arrived onsite to assess the condition of the buildings, POAH believed that the retrofit would center largely on remodeling and updating the living spaces, and that improvements to performance would focus on the interior rather than the exterior envelope. The façade, they believed, would not be a major issue. While the team knew that the masonry system was somewhat unusual, because the brick was supported from the ground up and attached to the lateral support system of the wall with a series of tabs and pins, they thought the repairs would involve a more or less standard repointing job.
This was far from the case. After making approximately 20 exploratory penetrations in the brick, the engineers found that the masonry was beginning to separate from the rest of the building in some places. In others, significant cracks and gaps had formed, allowing water to penetrate the brick and significantly weaken it. Based on the overall condition of the masonry, the engineers determined that the façade could not be repaired. It would need to be fully replaced, which would mean completely reimagining the exterior envelope.
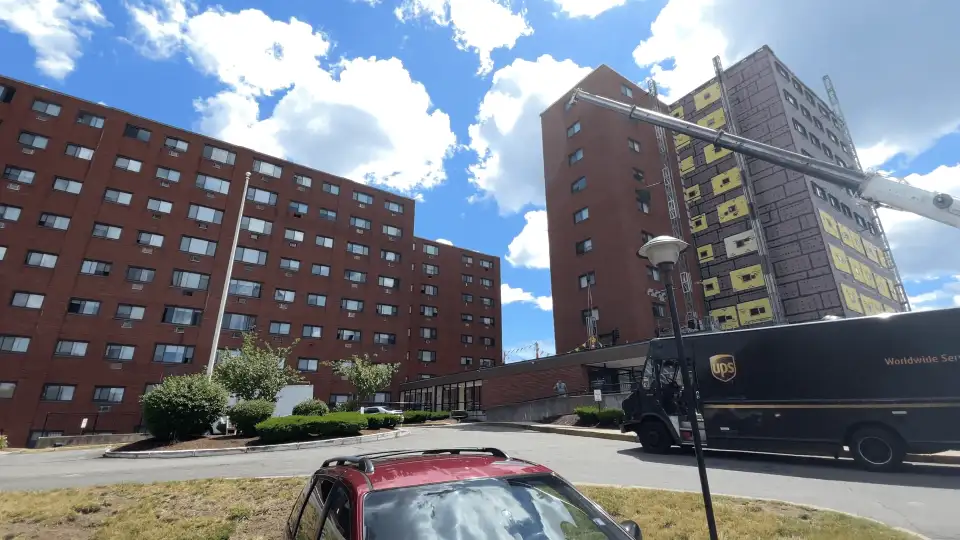
A Panelized Solution
Instead of frustrating efforts to retrofit Salem Heights, the condition of the façade incentivized the team to look for innovative solutions and opportunities to not only replace the wall, but to greatly improve the thermal performance of the exterior envelope. After some research, the team opted to install the ArmorWall structural insulated sheathing (SIS) system. Developed by DuPont, ArmorWall is a panelized system that includes an air and water-resistive barrier and a layer of poliyso insulation. Additionally, the panels provide fire-resistance because the exterior face of the sheathing is coated in a half-inch layer of magnesium oxide. As Klump explains, once the SIS panels are set in place and the seams and fasteners have been sealed, the system can serve as a high-performance continuous insulation layer and contribute additional R-value to the overall wall assembly. Another benefit is that once it’s attached to studs, the cladding attachment becomes completely thermally broken. These SIS panels were also installed on the interior of the garage to help insulate the foundation and the apartments on the first floor.
While there are several products in the ArmorWall line, the team went for the thickest option, which has an R-value of 21. According to Klump, the existing wall system had been outfitted with fiberglass batt between the metal studs, so the addition of the SIS panels increased the R-value to 28. This may not seem particularly high given that the property is located not far from Salem Harbor and the notoriously frigid winds off Massachusetts Bay, but modeling suggests that a combination of the buildings’ airtightness, insulation, density, and triple pane windows will keep heating loads down.
For most of the exterior, the SIS is protected by a layer of metal cladding, which was chosen because salt corrosion can quickly eat away at paint and inflate maintenance costs. “We’re not very far from the ocean,” Klump says. “We’re high on a hill. We wanted something super durable.”
There are also gaps in the metal cladding along the south- and southwest-facing elevations, which have been outfitted with vertical photovoltaic (PV). As Klump notes, the ability to install these panels is one of the benefits of being high on a hill. As there are no obstructions blocking the sun, these panels will be able to generate significant amounts of energy for much of the day. Once the rooftop PV panels are installed on one of the buildings, the entire system will likely produce 300 kWh annually, which is around half of the buildings’ energy load.
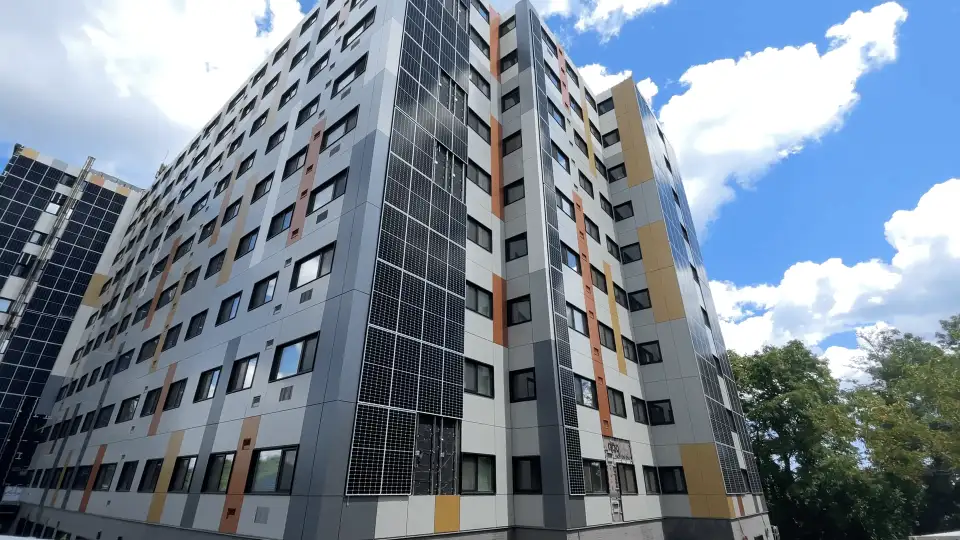
When the renovations are complete, the roof will have a minimum R-value of 30. However, only one of the buildings will be outfitted with a PV array. The roof on the other building was not strong enough to support a similar system and fortifying the decking was unfortunately beyond the budget. Klump notes that the installation of a solar array may be possible in the future. At that time, they may be able to add an additional 120 kW to the total capacity of the property.
Meanwhile, the original windows also had to be replaced. “The windows were pretty bad,” Klump says with chagrin. They had lived well past their useful life, many had been installed incorrectly, and their performance was poor to begin with. They were ultimately replaced by triple-pane windows from Vistaza.
HVAC in a Box
Beyond the issues with the façade, the team also realized that their original plan for the heating, ventilation, and air conditioning system would need to be revised. Initially, the team thought that they would install a centralized VRF system on the roof and ERVs on each floor, and then run ductwork down the hallways and into each of the units.
Building Evolution Corporation, the Passive House consultant on the project, did an analysis of conditions in the hallways and quickly found that this was not going to be possible. There was a massive steel beam in the interstitial space between floors where ductwork would have to be installed, and there was no way to snake the ductwork into the units.
The solution to this obstacle was clearly decentralization, and what they needed was a self-contained HVAC system designed to condition just one apartment. Eventually, the team found the manufacturer Minotair, which makes such a product. Based in Canada, Minotair has been a pioneer and leader in the autonomous/decentralized mechanical solution space since being founded a decade ago. They manufacture an all-in-one HVAC/D system with no outdoor unit known as the PentaCare Series that is all-electric and heat-pump based. According to Alex De Gagné, a co-owner and Vice President of Sales and Marketing for Minotair, the unit got its name because it takes care of five things: it provides occupants with ventilation and the highest level of heat recuperation as certified by the Home Ventilating Institute, as well as heating, cooling, dehumidification, and medical-grade air filtration. The latter can help keep occupants safe and healthy during wildfire smoke events, De Gagné notes.

“It answers all our needs,” Klump says. “It takes up a little bit of room because we had to build a closet, but the air quality is amazing. As complicated as it seems, it’s a pretty simple unit.” Once the system has been set up, tenants can adjust the controls for temperature as if they’re operating a basic thermostat. Beyond that, they only need to let in maintenance staff to replace the filters.
The closets for the Minotair units take up minimal square footage, which are typically taken from the bedroom to leave the space in the living room intact. It then supplies the adjacent bedroom and living room with fresh conditioned air. Meanwhile, internal ductwork connects the bathroom, the kitchen, and other living spaces, providing them with conditioned air and the ability to turn on exhaust boost in the kitchen and bathroom with switches located in those rooms. There is minimal ducting for the unit’s intake and exhaust; in most cases no more than just a few feet because the closet housing the unit is built along the exterior wall. The Minotair units are ideal for passive construction because installation requires just two penetrations in the envelope—one for intake and one for exhaust.
What was not entirely clear from modeling was if the units would be large enough to supply heat to the apartments, though preliminary evidence obtained from the field over this winter suggests that they are staying toasty even when the temperatures plummet. However, just to be safe, the buildings’ boilers and baseboard heating systems have been left in place and this system will be connected to the Minotair units with a control valve so that they are never competing. Once enough data has been collected showing that the Minotair units are sufficient, the original heating system may be removed.
Will it Be Certified?
Unfortunately, certification continues to be an open question. According to WUFI, the buildings’ overall thermal performance is good enough to meet Phius standards, but several obstacles to certification remain. Some of the difficulties faced by the team, in conjunction with budget restraints, may keep certification out of reach.
For example, the pedway between the two buildings is essentially two walls of windows connected by an uninsulated floor and roof, and its terrible performance is hurting the overall metrics of the property. However, outfitting the connector with the necessary insulation and glazing systems to optimize performance would provide minimal benefits to occupants and eat up resources that could be far better utilized elsewhere.
Another issue that adversely impacted performance concerned the foundation. The optimal solution would be to install sub-slab insulation, but this is simply not possible for buildings of this size. As an alternative, the team is extending a layer of insulation past the slab edge in areas where excavation and grade changes are already happening (see image above), but budget constraints prevented the universal application of this detail.
Though certification remains an open question even now, the use of Passive House principles to drastically reduce energy use and optimize performance has undoubtedly made the building better. Moreover, the lessons learned during the project will undoubtedly help POAH on their next Passive House retrofit.