Sian Taylor presents a New Zealand Institute of Architecture national award winning Passive House project, Threepwood Passive House. Threepwood is a small single-family home located on the South Island in one of the coldest parts of the country. Sian, founder of Team Green Architects, was inspired to build a high-performance home for her family after years of designing Passive Houses across New Zealand. Learn about the functional detailing, compact design, and creating flexible spaces for working and living by reading the transcript here or checking out the video above.
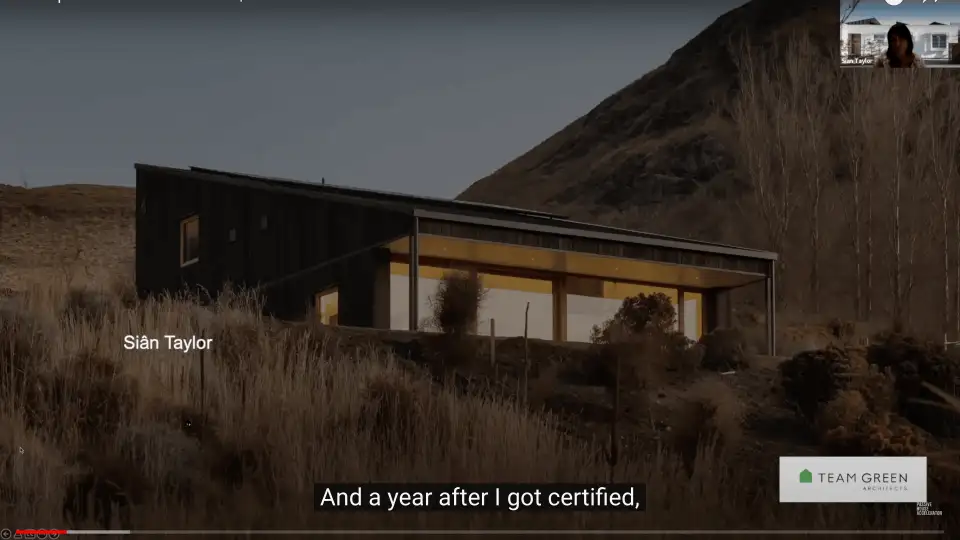
Sian Taylor:
As Bev said, I am Sian Taylor, I'm from Arrowtown in New Zealand, which is the South Island of New Zealand. I became Passive House Certified in 2012. I'm an architect by trade and continue to be. A year after I got certified, we started Team Green Architects. That's my partner and I. We design residential buildings in our region, and they are all using the Passive House process. We use PHPP. Everything is highly insulated, almost always using triple glazed European joinery because our climate is very extreme here in Arrowtown. We have very cold winters with snow, some minus nine and we have very hot dry summers. Thermal bridge, as free as much as possible and air tightness, and balanced heat exchange ventilation in everything that we do. That said, not everything reaches Certified Passive House, but this house, which I'm going to talk about, which is our house was Certified Passive House.
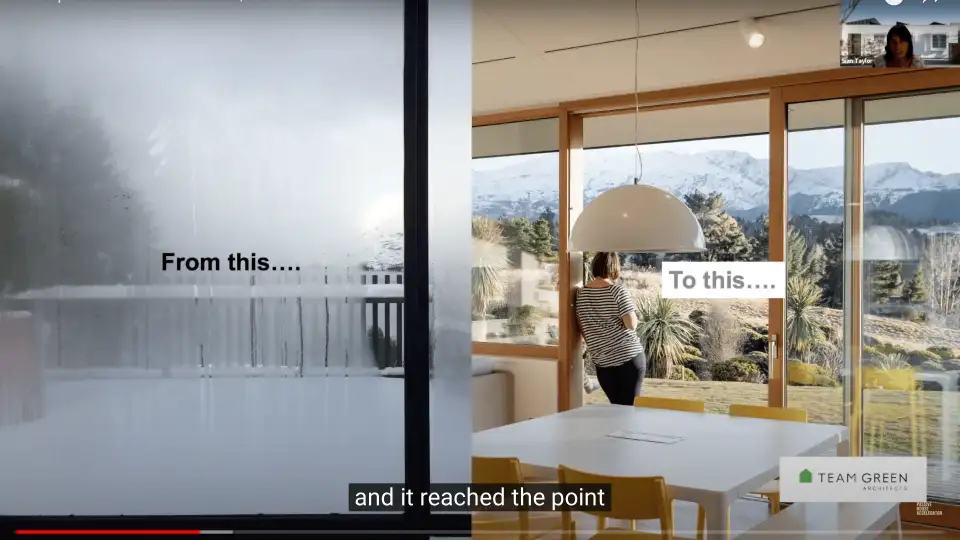
The story is this, our building code here in New Zealand is pretty woeful, and this is where we were living, and this is what we wanted. We're in a typical New Zealand house, which this house was built in the 1980s, very thin sort of 90 mil walls, aluminum single glazed windows. Although this view is absolutely stunning in the summer, we've got Lake Wakatipu here, and this mountain range is all around. In the winter for two or three months this is what we were looking at, which is condensation or that's if we were lucky, if we kept the curtains open, because it was so cold, often the curtains would close. Whilst we were living here, we were building homes which were warm, comfortable, healthy, low energy and it reached the point that we had to do something ourselves, which is what led to this.
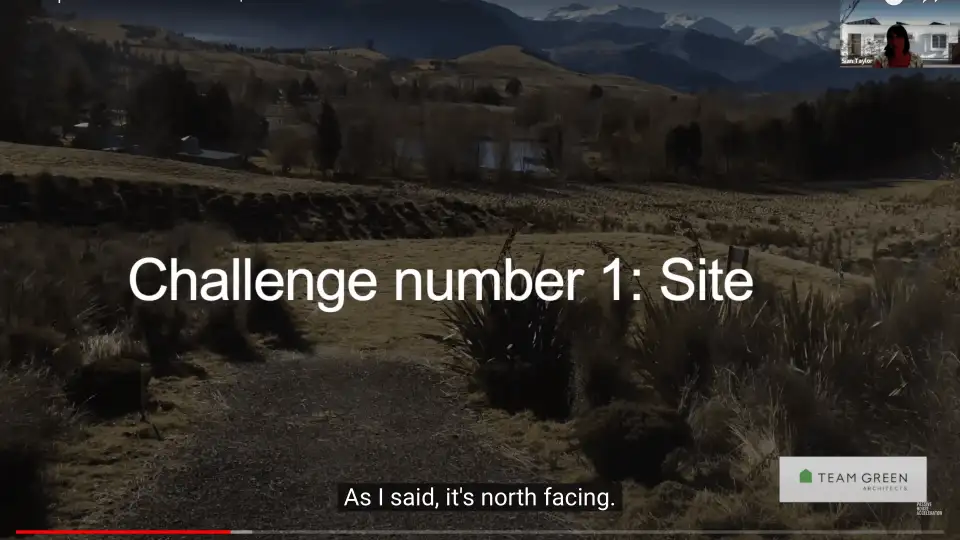
The first thing was where do we build? What we were looking for was land, which was north facing. This is the site that we bought, but we fell in love with this piece of land for a number of reasons. The view is incredible. It's quite sheltered, as I said, it's north facing, but this farm here used to be Mark's granddad's old farm. He has lots of on memories of this area. It was also somewhere which was really undervalued at the time. I couldn't understand why we were building lots of houses in this region and looking over at this land thinking, why is no one living there? Now, almost all sections are developed and it's completely different in terms of the valley. At the time we just fell in love with it and thought as well, that this big piece of land here was big enough for us to build quite a simple flat site house.
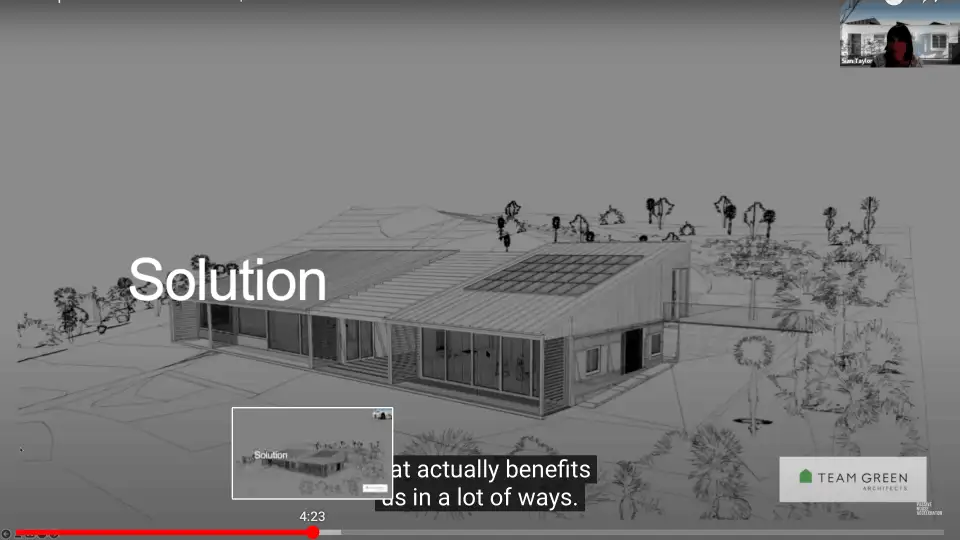
But as with everything, when you were overtaken with the emotion of how great it is, we actually didn't realize just how much the site drops off here in terms of the area you can build on and goes back up the hill over here. In fact, the incline of this site was incredibly steep to get a flat, a building that could have suited a flat site. But as with everything, the challenge meant that we've got a solution that actually benefits us in a lot of ways. This is the final design as in what we aim to achieve, if we ever win the lottery. What we've built right now is this bit here and this essentially is a two bedroom. There's two bedrooms, we live down here, there's two bedrooms in the back and a bathroom, and then a living kitchen room, dining room and that is around 80 square meters. As I said, this is north facing. I believe most of you're probably in the states so you're probably wondering why the hell it's north facing that's because that's where our sun is.
The roof slope also benefited us because then we could get solar panels on that roof. The slope of the land meant that we could build this second story, which allowed us to build what originally was going to be a guest accommodation for my parents. I'm originally from the UK. It's a bedroom, bathroom living space, but we moved in a couple of weeks before the first COVID lockdown. This had to become immediately, now a office space and within a very short space of time, I said to Mark, "I didn't want to go back to our office in town." Not only is it wonderful living out here, but this house is just so comfortable, warm, and pleasant that I knew. This is where we wanted to be. As a result of all that, we've completely gone to remote working. Mark and I work in what was supposed to be the bedroom. We have a sort of client meeting space in what was the living room, and this is our commute to work up here every day, which is I realize we're very lucky to have.
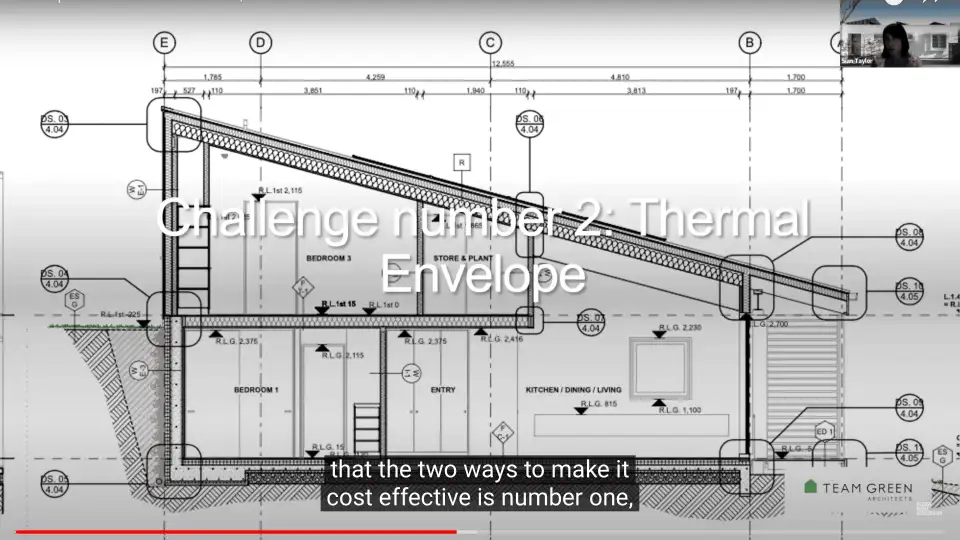
The next challenge was the thermal envelope and achieving Certified Passive House. I know from the work that we do that the two ways to make it cost effective is number one, get your orientation right, maximize what's free, which is the sun, which we already had in terms of our site. Then keep it really simple. Essentially the plan of this is a rectangle, almost a square, and it's just got one roof. It's a really simple thermal envelope, which is critical to keeping the cost down. But it did come with its challenges. We've got this area at the back that we needed to retain. We had to have a different type of construction for retaining at the back here. But essentially what we did, every single wall aside from this rear retaining wall is 165 mill SIPs panel.
But this came with its own challenges because we have blockwork, retaining concrete block here. We have a hundred mills of XPS on the outside and we needed to line up the SIPs panel with this XPS and the structure needs to line up as well as the insulation, which it's not doing. That was one of our first sort of thermal bridge detailing challenges. This detail here shows what we ended up doing. This is the blockwork wall, this is the inter story detail, this is the hundred mills of XPS, this is the SIPs panel.
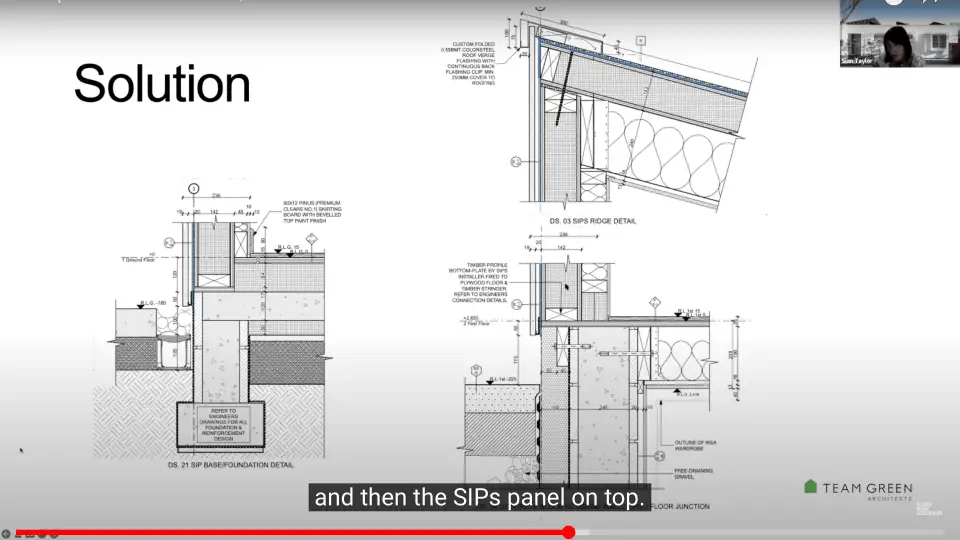
All we've done is bolt a piece of two by four to the wall here and that supports the inter story ply and then the SIPs panel on top. But what it meant is that the rafters, which are here, couldn't actually be supported on the structurally insulated panel, which they typically would've been because the load line was not direct. We had to put an additional 90 mil frame, which is the only place we've had to do this along the back wall to support these rafters. Everywhere else we've got the SIPs and then we've got 45 mills, internal cavity fully filled with New Zealand wool insulation. The roof is a warm roof, even though it's sloping, we've got a warm roof construction. The airtightness actually is here, but we put an extra insulating batt underneath and we ended up, it's not shown on this detail, but we actually ended up putting in [inaudible 00:09:03] here as well. Even though we've got our airtightness up here, we just wanted to achieve the highest level of airtightness that we could.
Then our slab detail, again, was just trying to keep things simple. Typically, in New Zealand, we insulate below the slab and a lot of people have exposed concrete slabs, but to maintain a really simple thermal bridge free situation, we've got the SIPs and then we've got the insulation above the slab as it's shown here.
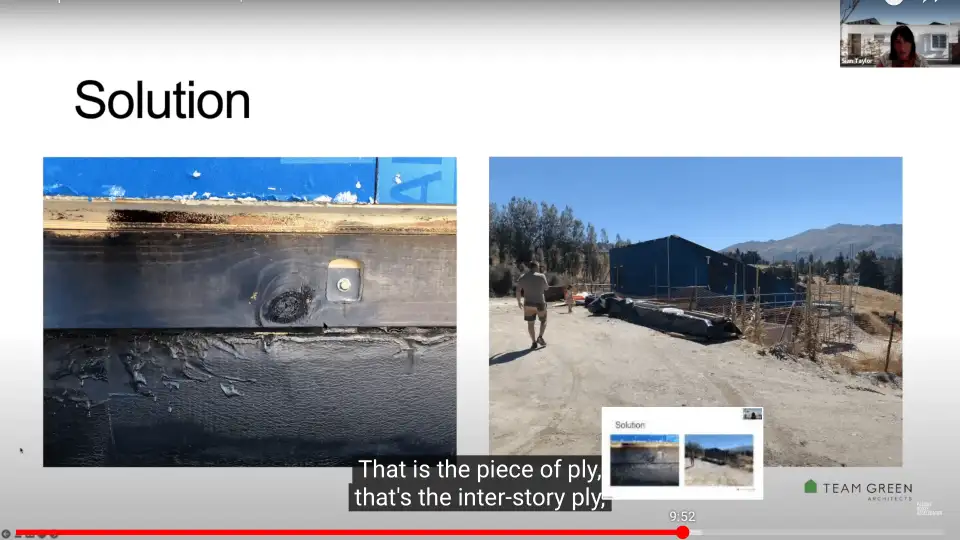
This just shows that's this is on site. That wall down here is where this is, this is the piece of timber that was bolted to that wall, this is the SIPs panel, that is the piece of ply that's the inter story ply, and that is the tanked insulated blockwork wall below.
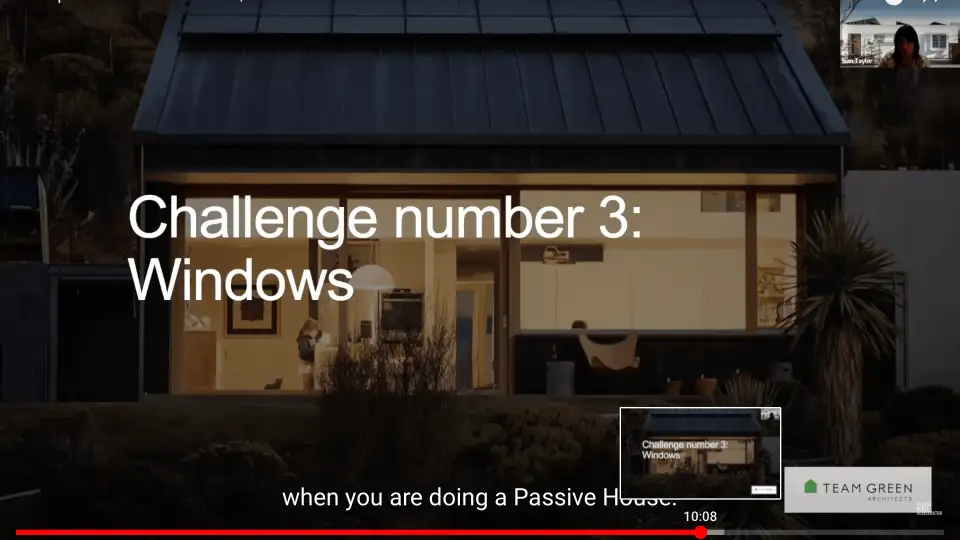
Next challenge was windows. Windows are expensive when you are doing a Passive House. If you look back, I'll just take you back to here, the original design just kept it really simple glass all the way across, but when it came to it, that was going to cost too much money. This big window here, which is the biggest slider that you can get, especially when you're transporting overseas, this whole window costs about $17,000 and every other window in our house, other than these two here is very simple. We've got, I'm just trying to show you. We've got square windows, which just repeat themselves these little squares and they were about $900 each. Then we've got this massive expensive window here. To keep cost down, we changed the design and went for the biggest bit of fixed glass that we could get here. We've got an opening panel here and it meant that we could have a change in the feel of the room because this is the kitchen dining room here, then we move into the living space here, so this is a lot more cozy. We've got a sofa behind here and it just changes the feel within what is actually quite a small space.
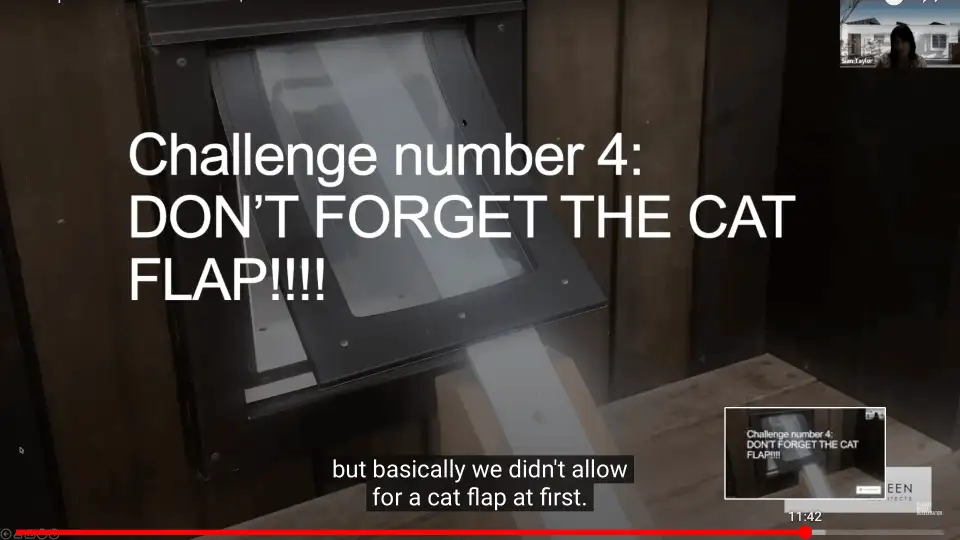
Then the cat flat. This was an absolute nightmare and it's embarrassing to say, but basically we didn't allow for a cat flap at first. Before we moved in, we weren't sure if we were going to get a cat or a dog and then we got a cat. We moved in and then as I said before, it was lockdown and we found two little kittens in our garden, which was our lockdown project. We now have three cats, which is not the intention.
We had to put in a cat flat and being architects were a little bit anal about things like lining up with cedar panels. Every single window lines up with the cedar and each wall finishes on a complete cedar panel. This had to line up. The cat flat in itself is expensive. It was bought, it was a U.S one. I think it was, I don't know, seven or $800, but it took a build of two days to cut this into the wall, form the flashing so that they perfectly suited this seal cutting, and the cats can't use it because it's too heavy and too airtight. After all of that, we've got this ridiculously ugly piece of timber with a bit of plastic holding the cat flat open and creating a hole in our airtight building to let the cats in and out, which seems absolutely ridiculous.
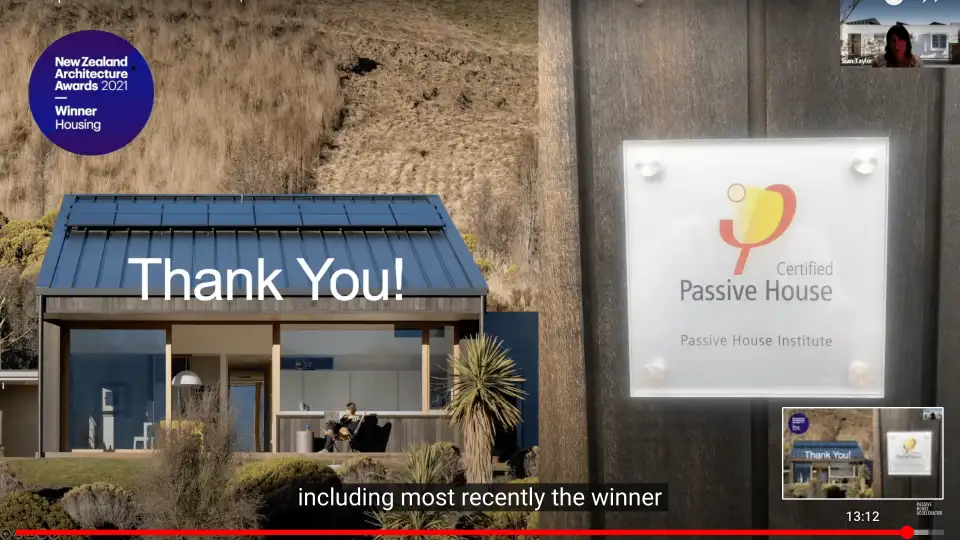
That's it, as I said, Certified Passive House and we've been lucky enough to win a few awards, including most recently the winner of the housing award for New Zealand Institute of Architects, which is a great pleasure and that is our Passive House.