Rounding out our month of airtightness, Shaun St-Amour joined us on the Passive House Live Construction Tech edition. In this video, Shaun, co-founder and co-host of Construction Tech, dove into the tiniest issues that can pose some of the biggest challenges to the blower door score: pinholes.

Shaun St-Amour:
Here we go. Buckle in. You've got to listen to me for a little bit, but there'll be a little bit of interaction. So we're talking about how to not put a pin in it. Let's dive into it. So every building you build from now on, you're going to think it of it of a balloon and anytime that there's a pinhole, you just pop the balloon and we don't want that. So we're going to focus on air control. Now, there was a little bit about me. I'm just going to add a little bit more so as the indicated for those who don't know me, just turn into VP of Operations with Clay Construction, been with the accelerator for almost two years we've been doing this. This is amazing. I'm also involved in Haven, which is the Local Home Builders Association of Vancouver as Co-chair of Technical and the Education Training. So you can tell, I love this. You're going to hear about how much I love this. And that also means I get to be a VP of Airtightness for the team at Clay Construction.
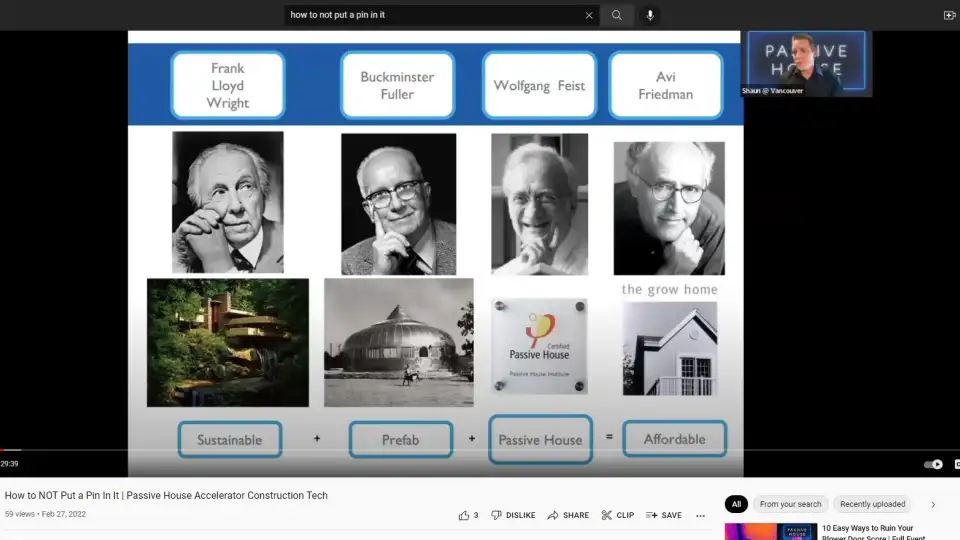
I've got a great family, two beautiful daughters, a beautiful wife that honestly make my life so warm. Unfortunately, though, the kids are growing up and I've been demoted as Master Builder in the Lego world. I'm now a Master Supervisor. I don't know if that's a promotion or demotion, but I'm taking it. So I'm just a big kid having a lot of fun. Now I'm very passionate about sustainable prefab passive homes, and they should be affordable. I have to say language is critical and I'm kind of using that word resiliency a little bit more in the last few weeks of watching a Monti Polson presentation. Now, the Harvey's out there, when we talk about affordable, high performance is affordable because the air control should be a line item in your mechanical budget.
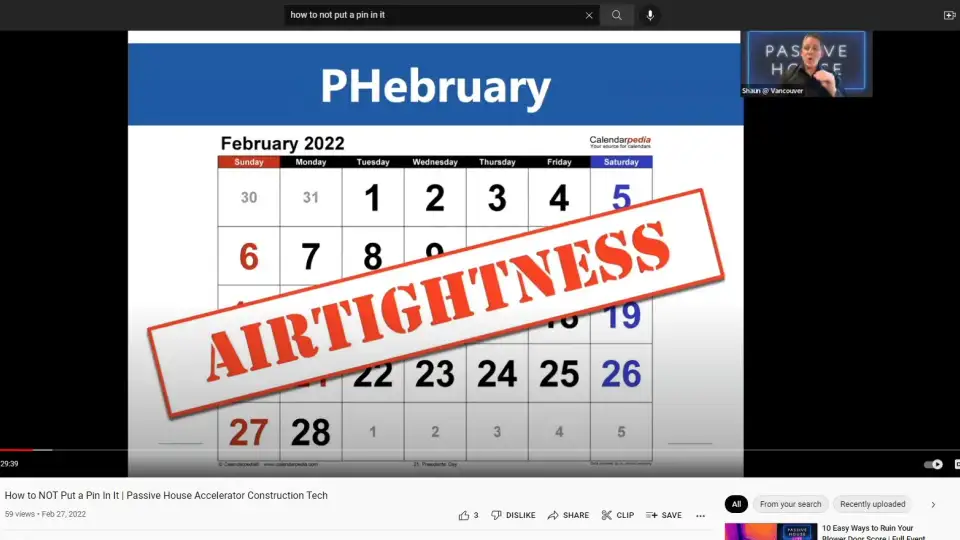
It's not in the W-R-B budget, it's not in the vapor control budget, it's in the mechanical budget and we're going to dive into it. So pin that idea about cost, because we'll dive into the questions. So February has been a very exciting month here on Passive Accelerator live. Of course you see what I did in spelling. The whole month has been on the theme of airtightness and we've had a great lineup of speakers.
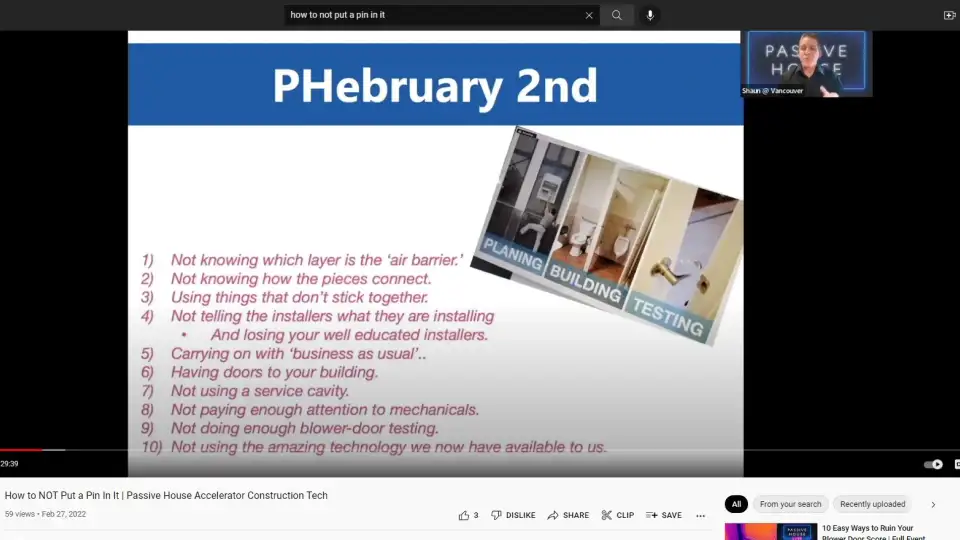
We had Ed May who literally we could listen to every Wednesday if he could. And he gave us great 10 tips. I really like how we defined planning, building and testing in terms of air tightness.
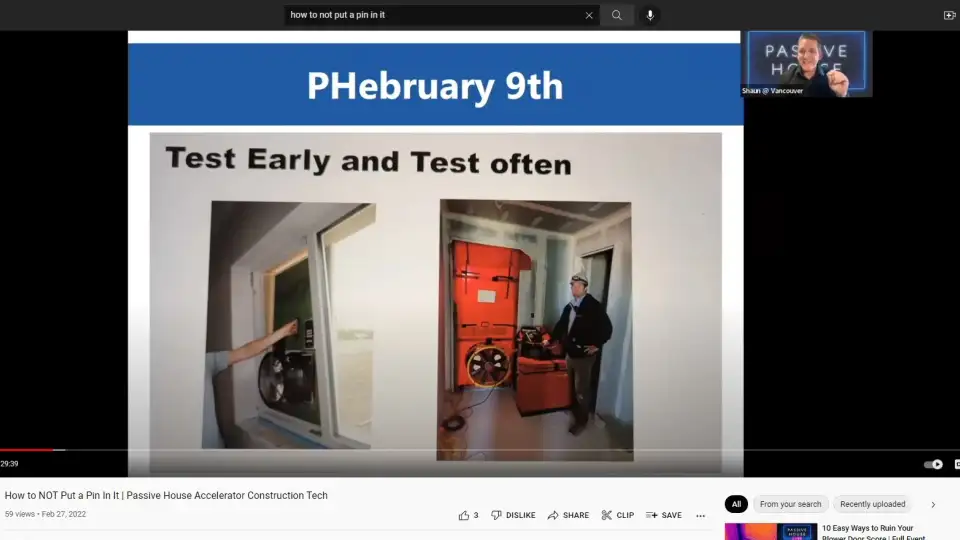
Then we had good old friend Kevin come on and one of the slides that I love, and again take this away for you as well if you missed it. Test early and test often. Wise, wise words, Kevin.
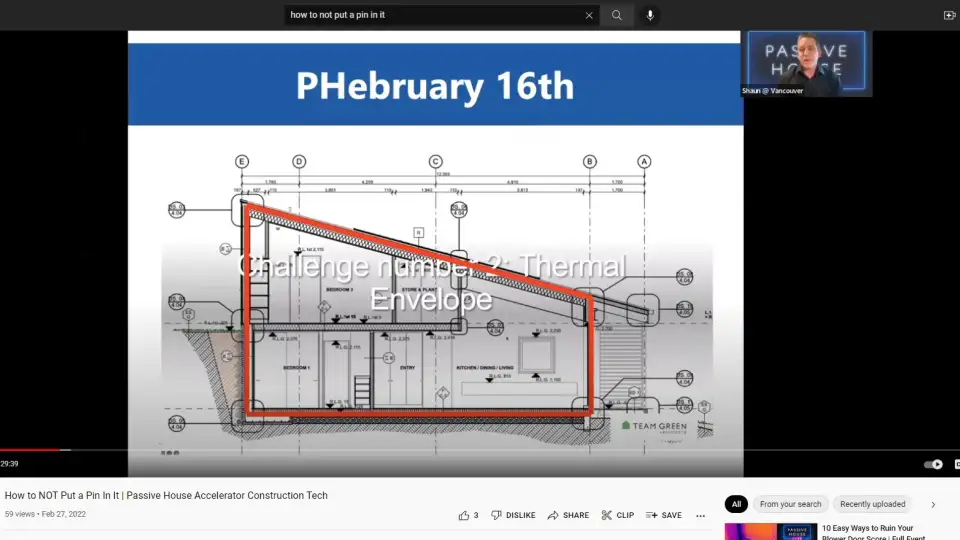
Last week we had Sian Taylor. We went down across the pond where we got to see this really amazing home that they created. And I love how their office is in the upstairs. And so they have a pretty short commute to their office. But you can see, look at that red line test, that is pretty simple to define and make sure that you've got your air barrier under control.
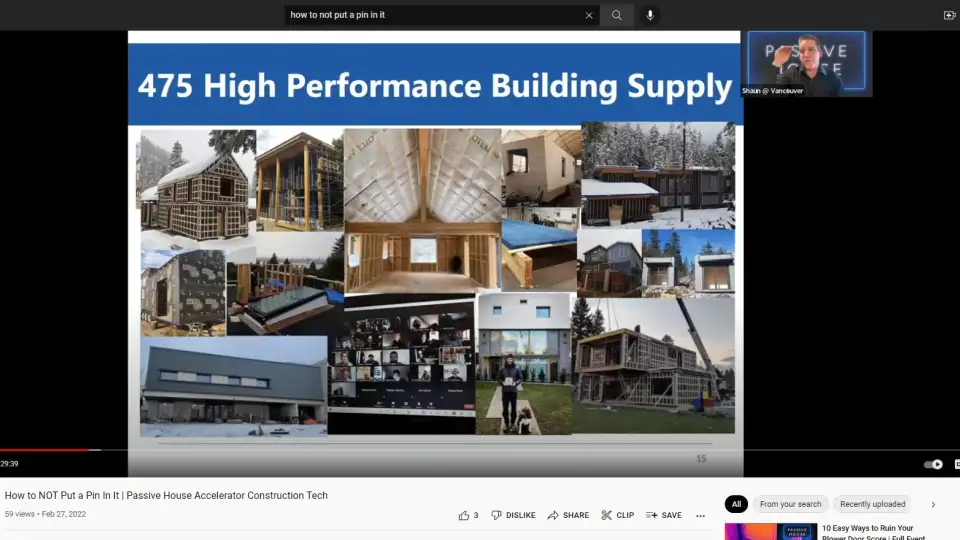
So now it's a little bit of my turn, so you've had great speakers and now I got to wrap it up. Well, I have to say, I think I can provide a couple of nuggets left in the month of air brief for air control. So 475 High Performance Building Supply for about three and a half years, I got to work with some amazing clients, trades people, builders, some buildings that I don't know if I will ever max, but they're definitely the benchmark for me, where they were passive house, really good air tightness scores, living building challenge, and really working on that zero carbon home. Really exciting things and so I've been able to learn a few things that I want to share and as Mike said, I will share with you all of what I have all day long because we need to scale this big time.
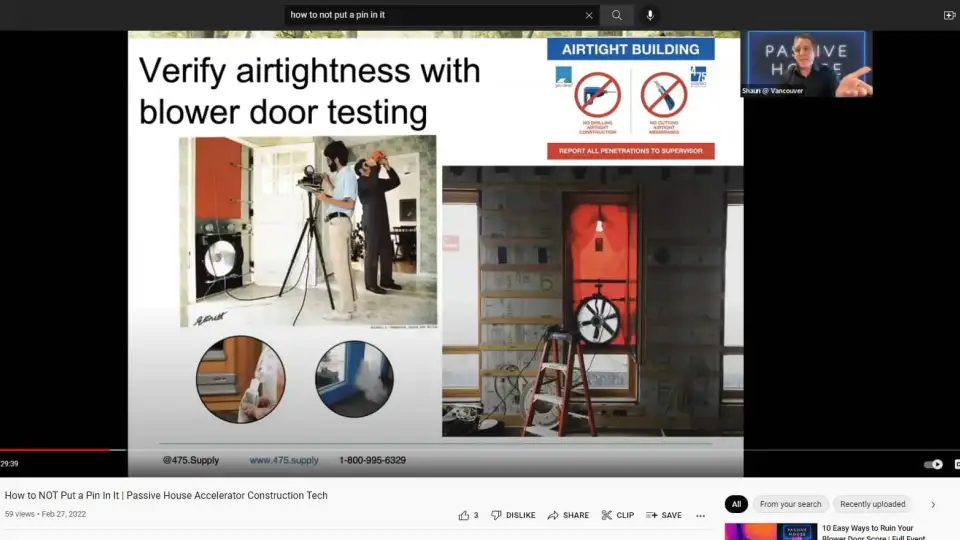
So take all this information and let's run folks, because we know that if we can measure what we're doing, we are then able isn't that the best retro photo ever of a blower door. But not also a blower door, in case you're not sure if we dove past, if you're a bit of a rookie tonight that hasn't been to our event, how about draft detection? Okay. We always get caught up with blower doors. You can really think about you're measuring the drafts in your home. So I want to make sure we're a little clear on the language. The draft detector doesn't lie, you measure things.
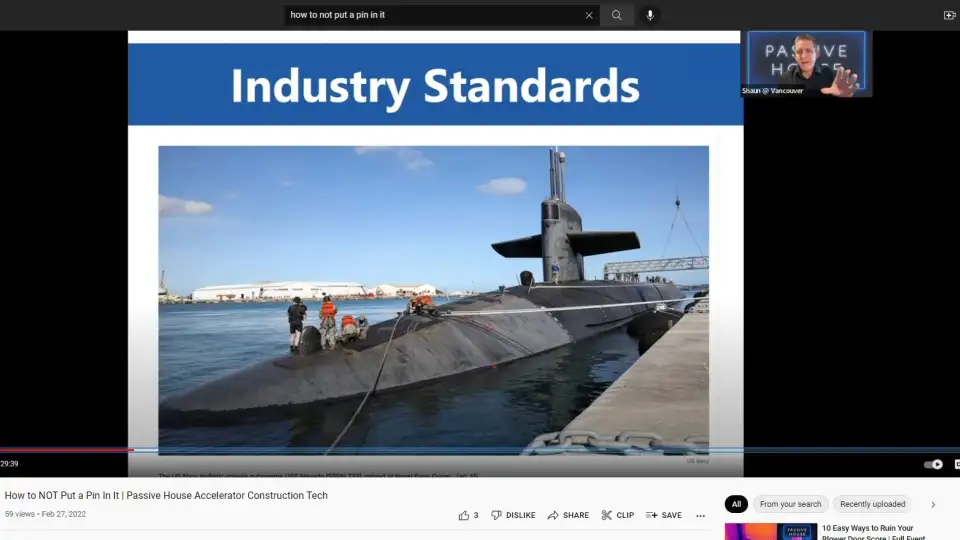
And so, if you don't like the idea of your building being this balloon, well what about thinking about that all of your buildings are a submarine that if it's water tight, it's probably going to be airtight too. And if you don't like thinking about your buildings as submarines, what about spaceships?
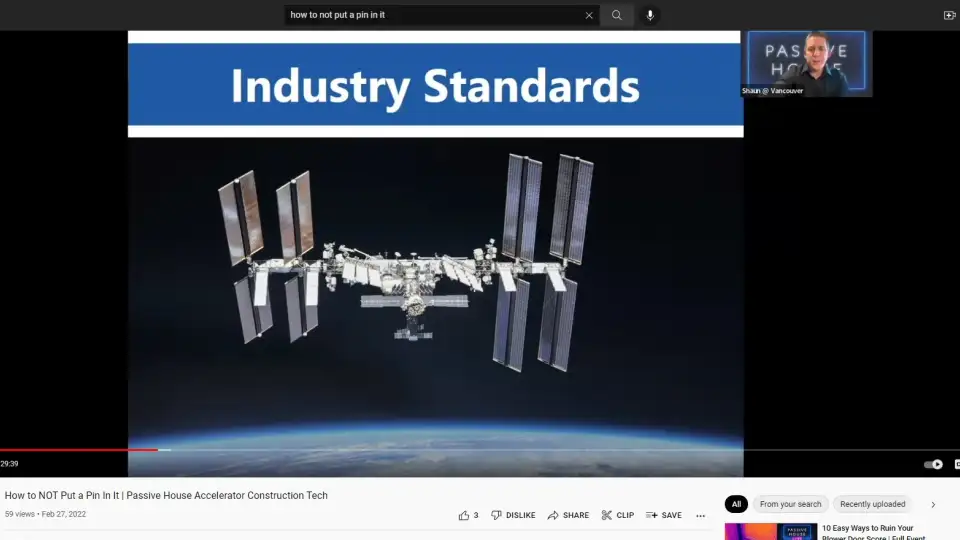
I would love to find out what the air leakage on these things. Two years ago, when we started the Passive House happy hour, I came on and said I would love to see it. It's been two years. I've got to figure this out before they cancel this and bring it back and Elon Musk brings up another one. But could you imagine measuring, putting a draft detection device on the international space station, bit of a bucket item for me. So we've got a system now, I'm trying to get you to look at your buildings differently, that we need to make sure we're looking at all the pin holes in your air barrier.
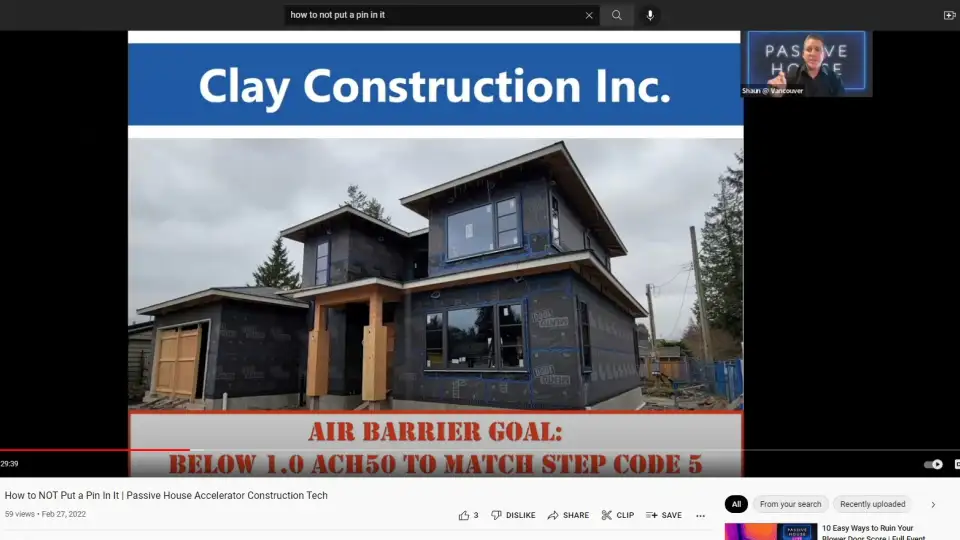
So at Clay Construction, I've got a bit of a challenge. We set out that from now on, we are going to only build to step code five. That's 10 years ahead of the code. [inaudible 00:07:06] the code in Vancouver or Serene BC, is now at step code three. So that means the minimum that we have to meet is 2.5 air changes. To me, it's not good enough. If we're putting a membrane on our buildings, if we're putting on the air tightness, we should be able to get to a lower score. Now, this is a building that we got to work on, it's at mid construction, already hovering around one and we're going to fine tune it because you know I'm competitive. And so one is what we need to be in 10 years. So we are future proofing our homes today. That's future proofing with a PH of course, but we're giving our clients homes that they won't get to for other competitors for 10 years.
Now the thing about this is you look at this, this is looks different, right? It is different because we're taking the time to gift wrap this home so when we present this home to our clients, we're gift wrapping it to them. We're saying, Hey, you wanted a house? Guess what, we gift wrapped it and you know, on the front door, I'm going to stick a bow on it and say here you go. Your home is now future proofed to a code that is 10 years ahead. And all what we did is pay attention to the details. It already got wrapped. We just wrapped it better. We looked at how we connected things from one section to another. We took the time to make sure the pin holes were in check. And where did this all start from?
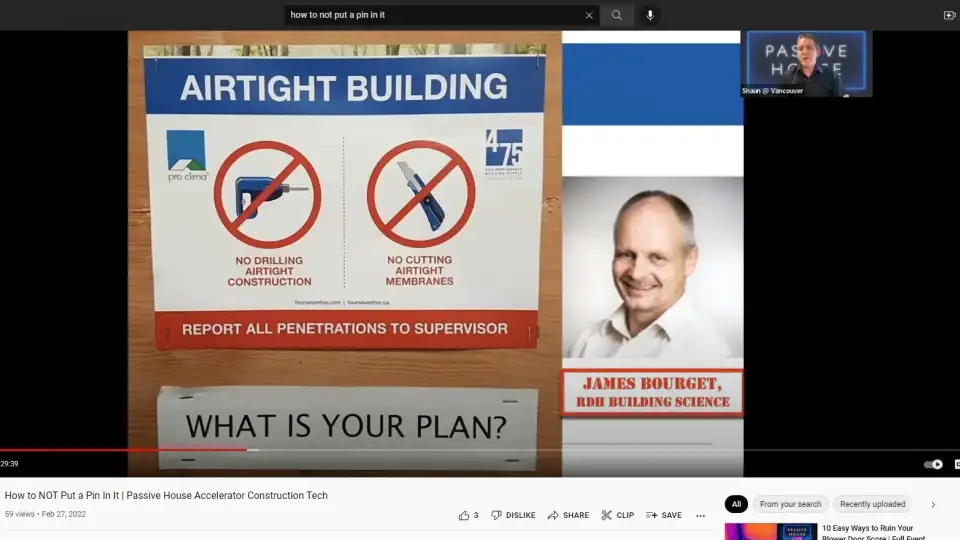
Because we had a plan. Now here is the one thing you saw folks today, if you take away one thing, it's this, because if you've been falling along on our construction tech, we've always talked about mentors. Many years ago when I got involved in this, James Bourget was really working hard with the city of Vancouver builders to figure out what is going on with builders and managing air tightness. And about five years ago, the average air tightness in Vancouver was 4.4. Next year 4.1. The next year they implemented some new bylaws to the code. It was minimum 3.5. It's now 2.5, but this gentleman trained most builders in Vancouver and he wasn't maybe as nice. He's maybe a little harder around the edges, but guess what? When you heard, what is your plan? What is your plan? What is your plan? What is your plan? I'll say it again. Folks. What is your plan? You left that arena, knowing that you had a plan.
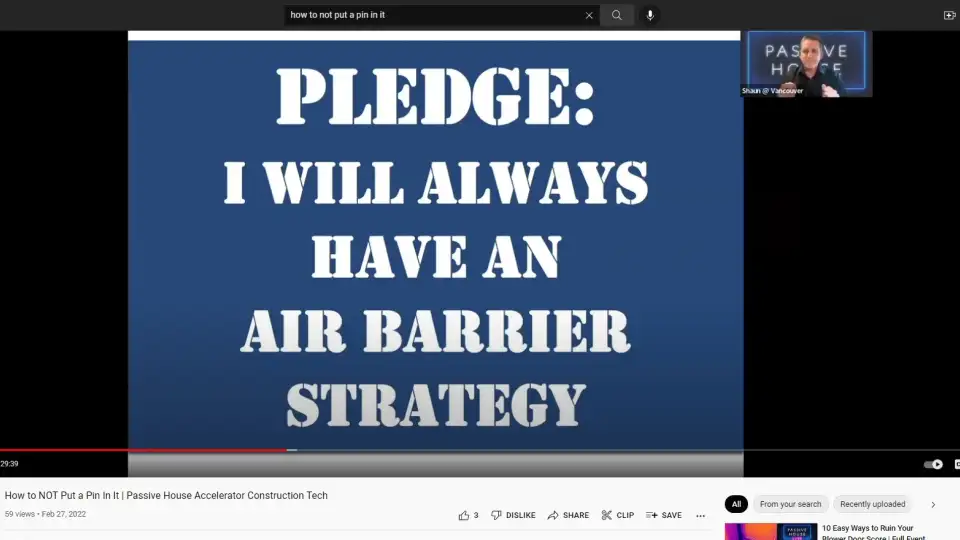
So this is where we're going to take a little stop because today we're going to do something we've never done on any of the Passive Accelerator events. We're going to make a pledge. We're all going to say, I will always have an air barrier strategy, in a couple seconds, you're going to unmute and we're all going to say this together. We're going to have a pledge that all of you, the 92 of you that are here against 91, you will from now on, always build a building with an air barrier strategy. Okay? Folks undo your mute and let's say this together on the count of 3. 1, 2, 3…
ALL:
I will always have an air barrier strategy.
Shaun St-Amour:
Fantastic. Okay. Mute yourselves. Now we're going to leave this slide up a little longer, because I want you to not only take a visual picture of this, take a picture and post it, tag friends, because from now on the 92 of you will always do this. And if not, I'll be coming after you like James Bourget came after all of us many years ago to ensure that we have a plan. So you can take your mental photo. I'm going to make sure I have this because I want all your lovely faces in there. And I'm going to tag all of you in my post night. And I'm serious. I'm going to leave this on for another 10 seconds, from now on I've thrown that pledge at you to make sure every building you do, you have an air barrier strategy. And the reason this is so important is because when we first look at buildings, the first thing we do from a design standpoint in order of importance we manage, water.
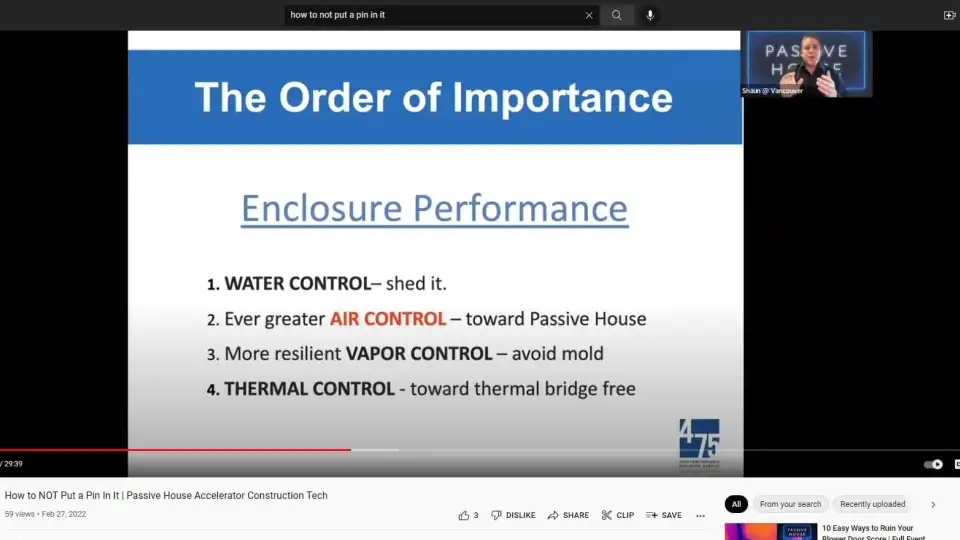
And so this is a point where I want you to think of Bruce Lee. So Bruce Lee, if ever he's in school he says be water my friend. And of course he spelled friend wrong. Oh, whoever's unmuted, we'll just have to mute you. This is the point where when we're designing our buildings, we want to make sure the key thing is keeping bulk water out of our buildings. And so bulk water is a design issue. We can take care of that out front. The vapor control is a design issue as well. We can take care of that, we can design for it. The amount of outsulation we put on our buildings, it's a modeling issue, it's also a budget issue.
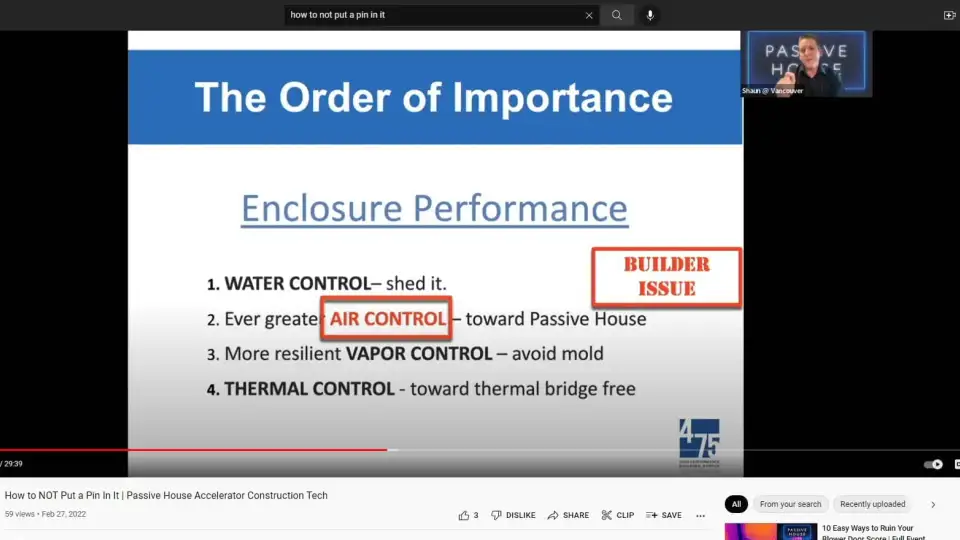
I would want you to have more insulation on, but some people give up at a certain budget. The air control, however, is a builder issue. This is something that you can do horribly wrong and maybe get a 10, or you can dial it in with a plan and get control of it.
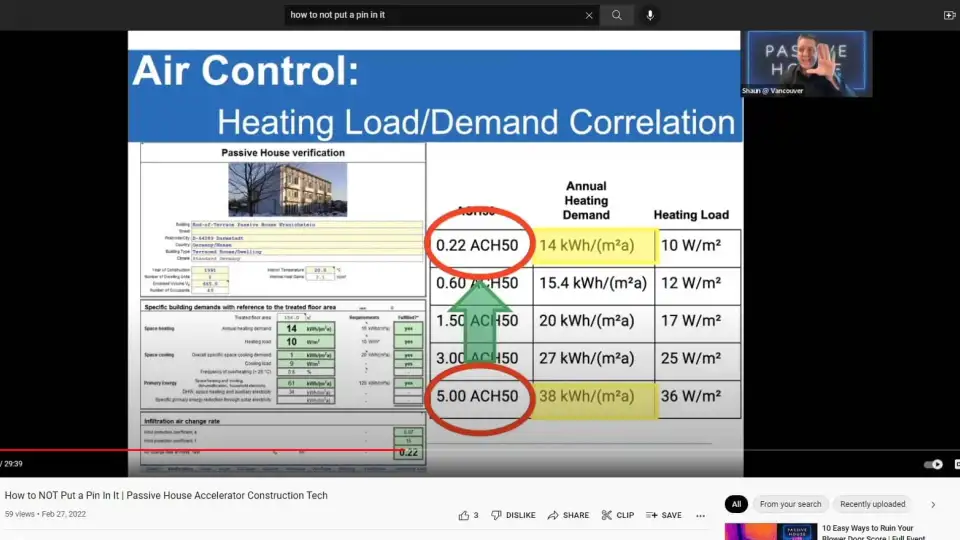
So all of you builders out there, this is where you can take control of your buildings. And when you look at it, when I said, Hey, the air control is in your mechanical budget, it is. Because we're talking heating and cooling right now. We're not talking about how of the membranes and how the building is wrapped. That's separate. Right now we're talking about the heating and cooling device. And this particular item is now quickly driving your heating and cooling costs but more importantly comfort. So I actually really think that the membranes in [inaudible 00:13:14] community, should change and remove the Swiss and German and Italian labels and put W-R-B air barrier, the testing that's required for the building [inaudible 00:13:26] and then liberate comfort, energy efficiency, health, resiliency, durability, because if you walked up to a building and it was white with Tyvek or a really cool color and said comfort, healthy resiliency, which one would you buy? Because that's the material we're doing when we put on our product and we take the time and effort to dial this in. And you can see the numbers here going from 5, 3, 1.5, .6 and remember, this is Wolfgang fight's home that he's been had for 30 years. Air tests every five years and its been hovering around the .22, and he's making it look real good. So again, this is the certified passive house, green numbers.
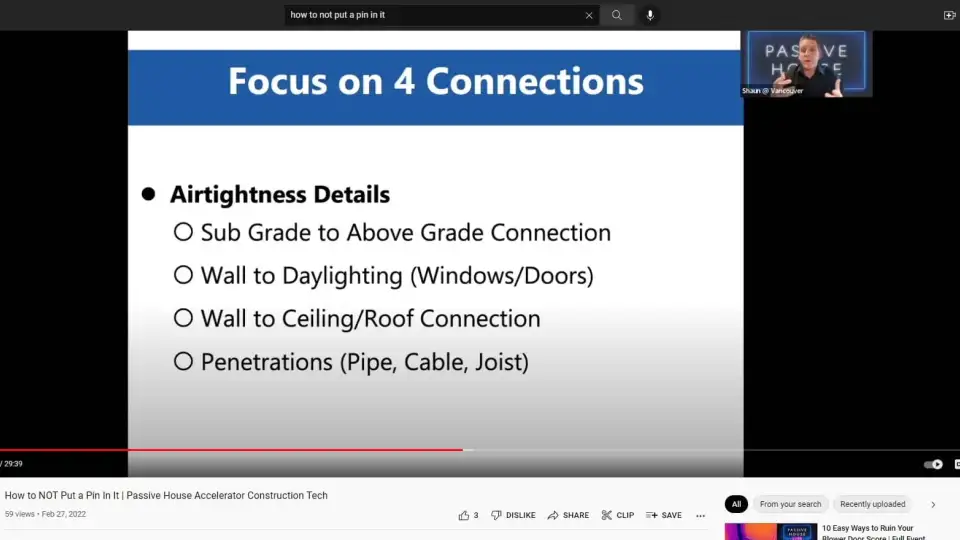
So now that I've got this whole concept now about how the air control is, we can now look at things, we can break down and be okay Sean, I get air control is really important. I get that you've dumped it into the mechanical budget. I can wrap my head around how to put this and make it work. But how do I do it? Well now there's four main areas that we need to identify of how we can work on making sure that our plan will work out in the performance.
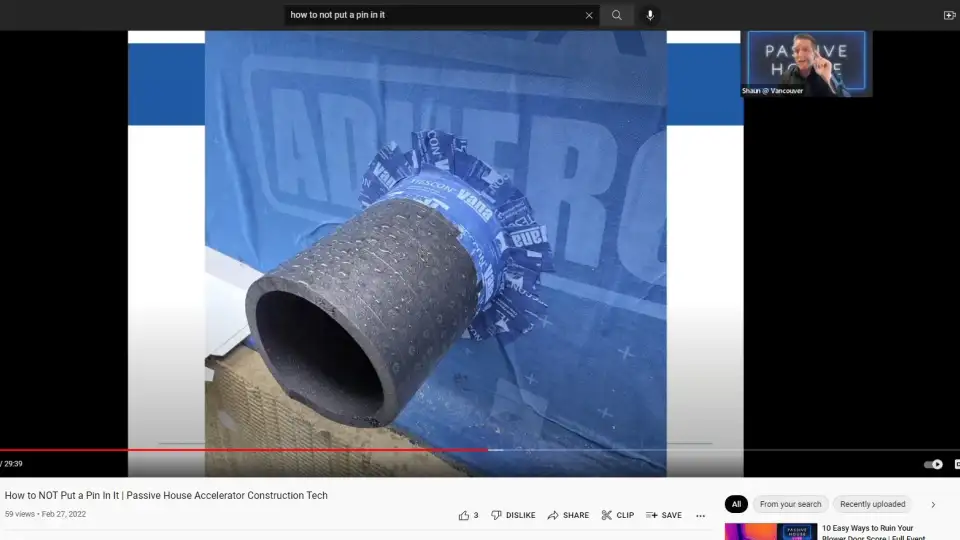
So we have the sub grade to above grade connections, wall to day lighting, wall to ceiling and penetrations. And so even out of the four, you'd be like, Hey Sean, those are four, I don't quite get how to connect those. Where should I start? Well, we'll break it down again. We're going to start in the penetration section, the pipe and cables, because we're going to want to eliminate the biggest hole in your air barrier. Now this is actually a good penetration. This is the intervene that you want. But there are many other penetrations in your envelope that you want to get rid of. You want to get rid of some of the mechanical ones, the steel pipes, if they're not sealed properly, they're leaking. They're not efficient. You want to get rid of your bathroom fans. You want to get rid of your dryer ducks. You might even want to get rid of your hood fan. And I know that's going to come up with the questions, but if you like to have a good fan, then you invest in mechanical damper to make sure when you when it closes off, it's nice and tight and actually helps out your air barrier.
So we're now eliminating our eight inches holes, our six inches holes, our four inch holes and now we're getting down to pin holes. We're getting down little things. And when we look at part of our plan of getting to zero carbon, we're probably going to electrify a lot of the equipment we're using. And by electrifying the units, guess what? The ductless dryer you're putting in, guess what? The four inch or six inch duct gone, the hood fan gone. The fresh air machine is replacing all of those leaky bathroom fans going out. So pretty quickly by you making some decisions up front, you're actually helping out your air barrier strategy and we're getting down to the pin holes that we want to eliminate.
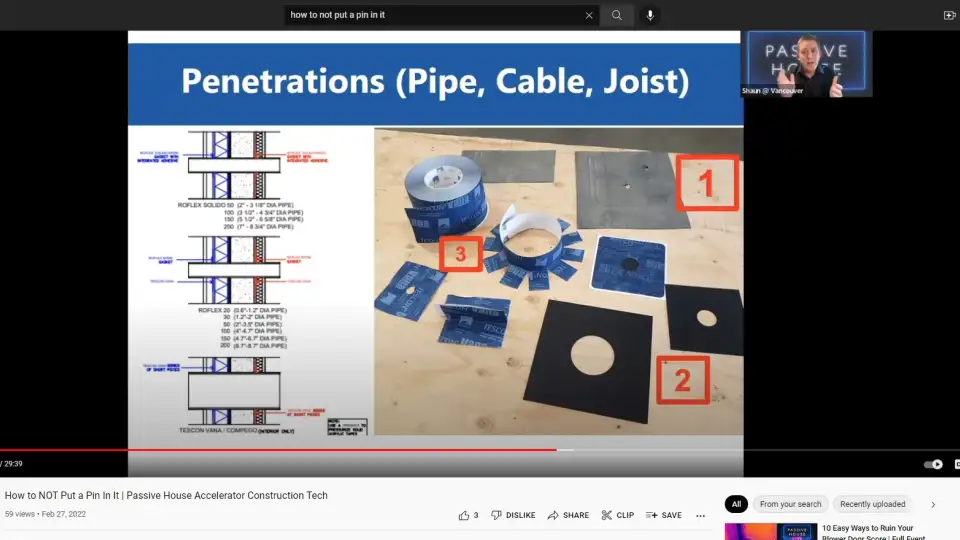
So let's talk about penetrations and materials to use and how to make it work. So again, breaking down for you like, okay Sean, I have three choices here, which one's the best one? I'm going to tell you the first one you want to use, go to a lumber store, buy yourself a two foot by a hundred foot roll of rubber EPDM gaskets that you now can use. If for some reason you're organized, which hopefully you will, you could buy gaskets on the market. Otherwise you're using tape and tape is expensive. So you want to look at some more affordable options.
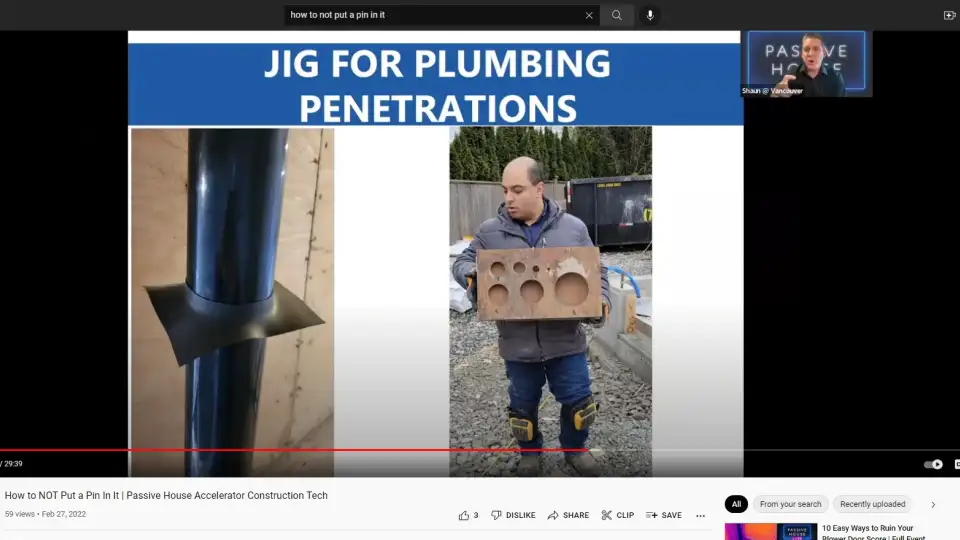
Now we talk about mock-ups in a little bit. You know, I love a mock-up. Well, this case I really like jigs. And so here is a jig that you create that you literally have the roller rubber, a knife, and the jig sitting on the shelf when your trades come and say hey, I have a penetration that I need to cover. Now, this is an older jig. We just decided to create a new jig because you know, things get older. But you can see now how quickly that gasket on the left goes around the pipe. Pretty simple. You can see each hole on that jig is either half an inch or three, four inch smaller. So when you cut it out, you go over the pipe that is there, you can see that really nice seal. You can tape it or you can leave it, but now you've got four sides of the square, you can easily tape and make sure you're there. This guy is happy with his brand new jig. Works really well. Again, my good friend Norm did this on his project. Look at these really good detailed gaskets he did and the connections. Norm, Bravo. Love it. Had to include you in this.
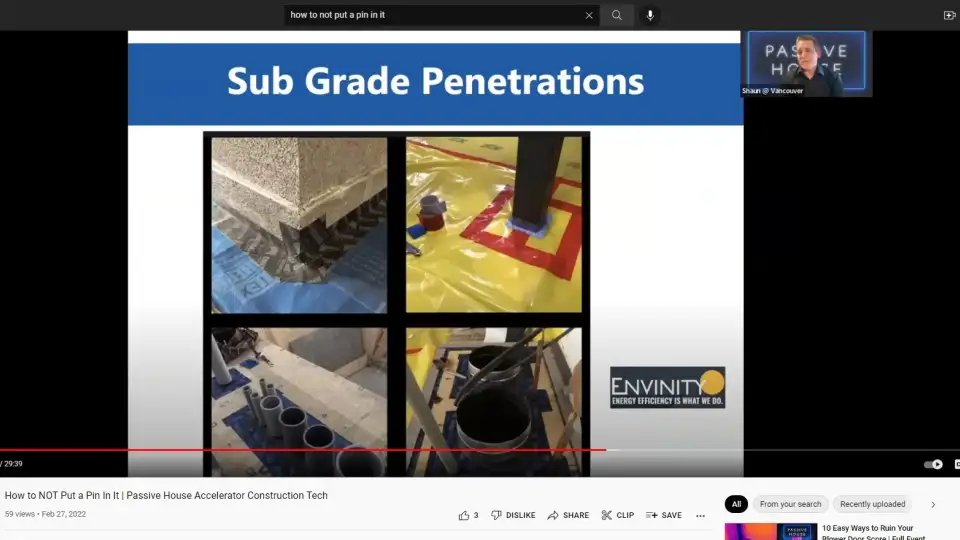
So now that we've got the penetrations and the pipes all figured out, now we have about 200 penetrations, inner envelope which are, anybody guess? Lighting, switches, plugs and we can quickly eliminate those by creating a service cavity. By creating that service cavity, we're now not hurting the air barrier. The air barrier is now effective and of course you know who was going to throw a prefab photo in here at some point.

So we've got these great examples of prefab where you can see the service cavities installed. So now we've gone from about 200 to 220 penetrations, correct? Because you think about in all of our lovely top floors now, in our bedrooms, we've got anywhere from four to eight pot lights, you add that up in all the different rooms, you got a lot of pot lights that are affecting.
Now, if you can't do a service cavity, what you could do from all your scrap plywood on your job sites is make light boxes where your cans can sit in but now your plywood box is air sealed in the corners, you can either use tape or liquid ply air barrier or sealants to make sure this is undone. And of course, when we've got our electrical cords going through, what's the rule? One wire through the hole once only so you can properly tape and seal it. So now you've got your lights, they're contained, they're within the air barrier and now you're dealing with about a dozen. So we talk about a dozen, we know those dozens is going to be your HRV exhaust supply, couple of hose bibs. Probably in the front door you're going to have maybe a camera, a doorbell, a light and a couple other lights.
So all of a sudden we went from 200 down to a dozen. And so now we can look at those pin holes because the scope of work is reduced by making sure the air barrier is on the outside of these devices.
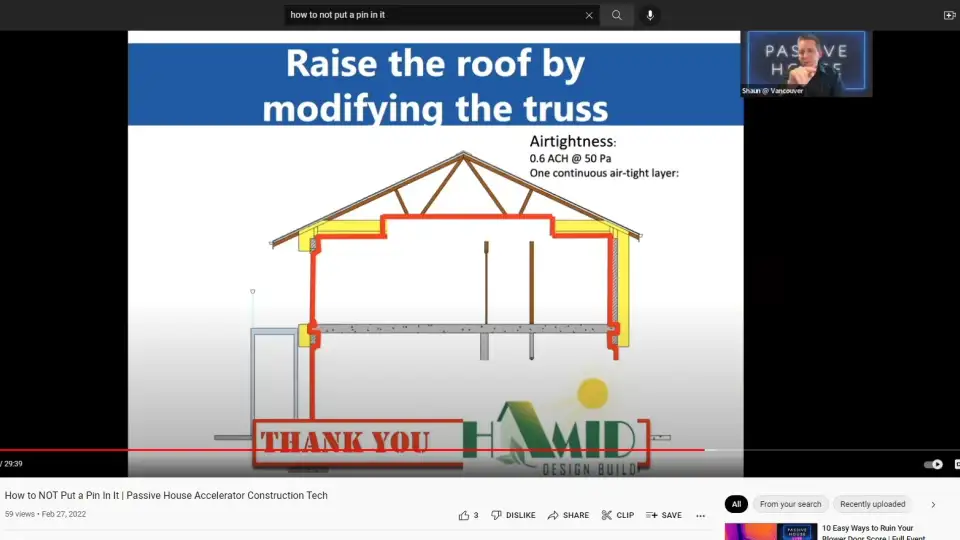
Now here's a really cool option too is if you can't put a service cavity in your roof, you could actually order a different type of trust system. So how this trust system works is you could have it two or three feet coming on the sides to make sure you can get the right amount of insulation on the upper slopes. But now you have the little cavity where you could put in your lighting and it's on the interior side of your air barrier. Trust companies now are considering this, if you're not sure, reach out to your local trust manufacturer, be surprised of how they can make this work for you.
So you can get the insulation you need on the ends, but also make sure that you can have a really cool air barrier strategy. Now, what did I just talk about the wire? Again, one wire through the membrane, tape it, seal it and you're off to the races.
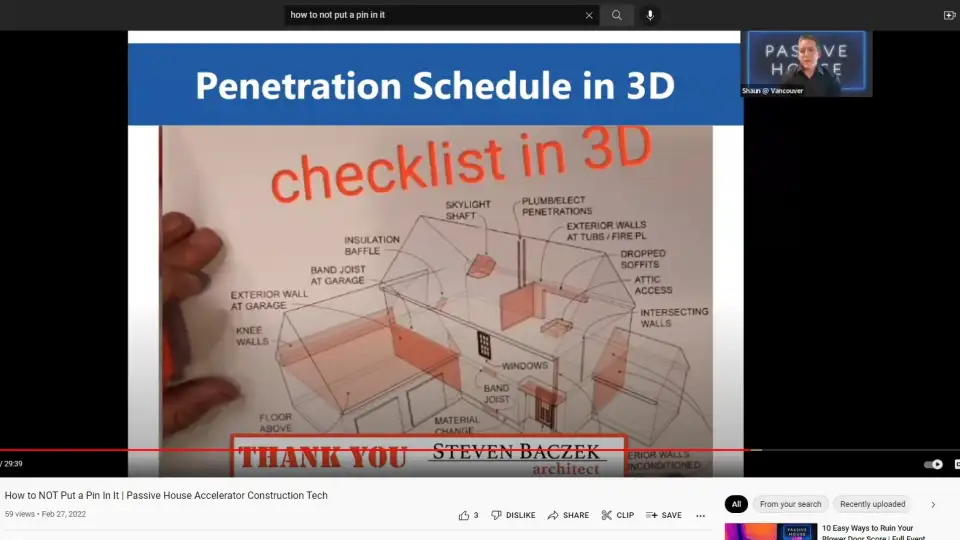
Now I wanted to create a penetration schedule, but you know what? Somehow the universe works out. Well, I know Prudence when she did her presentation a year ago has a really good penetration schedule, but I just found this out this week, energy star actually has this thermal bypass inspection checklist that I'm hoping someone will throw into the chat. Again, I'm giving away stuff, giving away stuff all day long. Now I thought this was fantastic. Yeah. Like good old friend, Steven Baczek says, why don't you have a checklist in 3D because then everybody can see where all of the issues are.
Now you could take this to pretty much anybody and say there's the penetration in the air barrier, we should be able to fix that. I love this. It's such a great thing. Hopefully more of you will adopt this in your buildings because it's pretty clear of entering the building, if you have this posted where these issues are going to be. Okay. So I just dealt with penetrations, the next thing is day lighting, the windows, because in a typical house you're probably going to have 20 to 25 windows and guess where the pin holes are, they're going to happen in the corners because what happens in the corners? It's a tough part to either seal with rod and cop or with tape. And so typically you're going to have four pin holes. So that's an area where you want to make sure you get the right tool to get it done. Now, depending on your window, you might have brackets coming in and you want to make sure those are properly taped off and sealed as well because right on the little edges you've got pin holes.
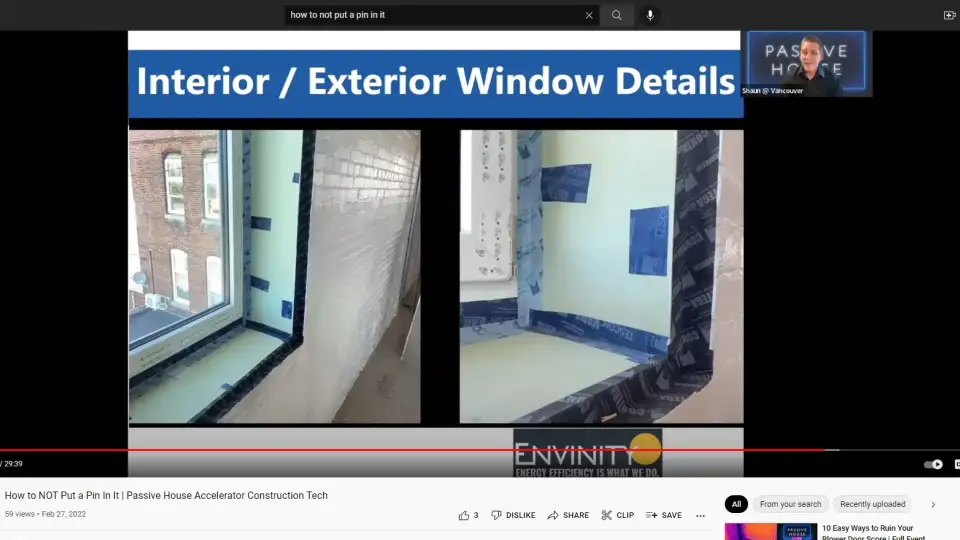
So we've gone through 200 penetrations. We've got air sealed now. We've got 25 windows we've now airtighted. We're getting down to the little ones where we're looking at either the concrete to wood connection, because we've got different materials. And that one's a little bit more difficult compared to wall to ceiling because that's just typically wood to wood or it's the same material. So that's why there's difference in the methodology there with that. I love a good mock up and you can see here again, how they're able to tape up the edges to make sure it's carefully done. And you can see the metal clips, how those are properly taped. And again, good friend Norm, look at this job here in Philly where he's able to do a really nice taping job and making sure that those high performance windows, again difference too, between code-based windows and high performance windows of how they're air sealed but the issue of connecting the window to our air barrier membranes and tapes and sheathings or liquid applied materials needs to be dealt with. And typically you're going to see pinholes in the corner if you're not taking the time to finesse that corner. So yeah, so membranes or whatever material you're using to wrap it, again, as long as you're taping it or making sure those connections are there, it can get done.
Because you can see for the most part, that whole building is covered in membrane. Now you've got the tape seems to need to be taken care of, but for the most part, it is covered. Now one of my favorite photos, look at this nicely gift wrapped home that's going to go to the clients. I don't know about this, but I have literally thought, you know you could put a bow on this and you know, the clients are getting that gift wrapped home.
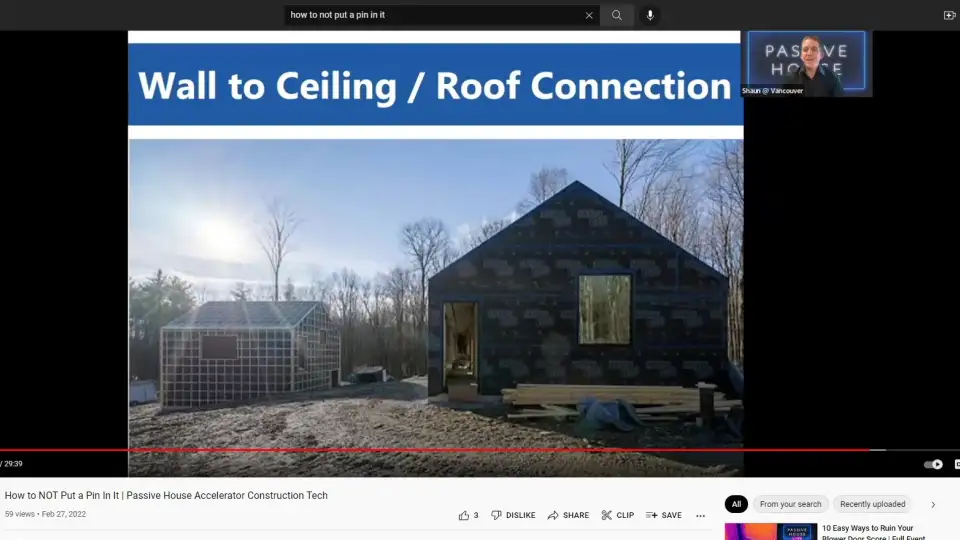
If you had to take away something from today, you can either just give them something where it's nicely wrapped. It might be flapping in the wind or you can wrap it and say clients, I'm giving you a present. A high performance home where I took the cost of the extra stuff and put it in mechanical. I was able to reduce some of the other mechanical needs and the part to it is the air barrier materials are passive. They don't have mechanical parts working. They're going to last and they've been tested to the last 50, 75, a hundred plus years where some of those mechanical pieces only last in 25. You might have to change it out four times. And if we're looking at building homes that are longer than a hundred plus years we're talking 200 plus years on the accelerator. We had one in Portland where they're talking about a 500 year old building and it's wrapped nicely.
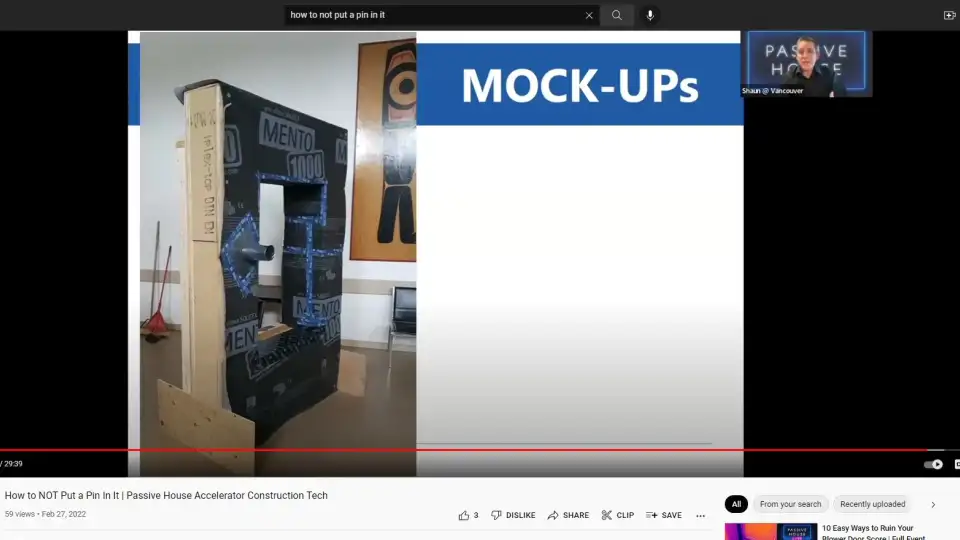
So things, food for thoughts. Now another little connection detail just to inquire because we've seen a lot on the build show is using caulking or sealants to be able to connect from concrete to the bottom of your sills, connecting to the plywood. So again, you've got some air barrier continuity in between that connection point. Now to kind of wrap things up, you know I love a mock up. The mock up is so great. The reason it's so great is here's a mock up for a project, it's one window. On this multifamily project, they got about 80 windows. Copy and paste times 80. Copy and paste 10 times. Do all the details, show everybody, make sure it's there so everyone who enters the site knows this project is acting differently. It's working high performance and this is how you achieve it. And so every time they go through their walls, you're seeing this carried through.
You can even have a complex one. This is one that we did recently at a project when I was with 475, where we had to go through the different details. Mockups are so critical for just reviewing things. And again, if it's messy, it's an opportunity to learn because if you fail, you're giving yourself a chance to learn. So when you do a mock up, fail, fail hard, fail again so that you can learn, you can implement the right strategy and succeed and accelerate.
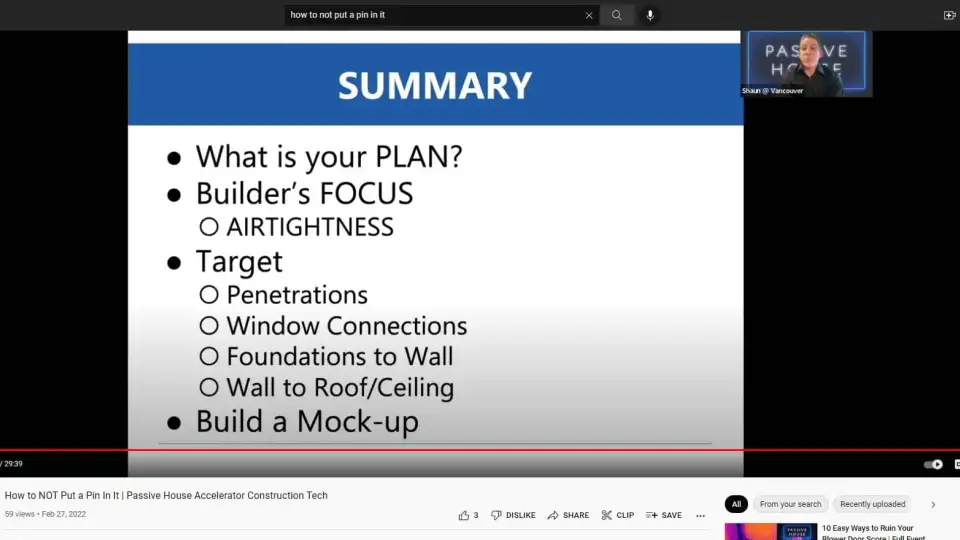
So to wrap things up here, what is your plan? What is your plan? What is your plan? I want you to go to your team tomorrow and start talking about your plan and work towards, hey, we've never done an air barrier or we've never done a draft detection on our project. So you know what? We're going to do one, we might fail.
But if you haven't done it yet, you need to start it somewhere. And I typically say is once you've been able to do once, work towards your passive levels or tightness. If you fail on the way you're making improvements, you're doing better than code. You're doing better than other people. You're giving yourself a competitive advantage in the marketplace. And the more you do it, the more affordable you get, you use less tapes, you'll get more resilient with the performance in the steps. As a builder, your focus is not only providing the client with a home that's on budget and on schedule with all the resources you can but you have a great opportunity to manage air tightness. That is the gift of where passive levels I'm always saying, hey, we'll take care, we'll take the some of the design issues away. We'll model the insulation requirement, we'll model out thermal bridges, we'll model which forms of windows it's required.
But in air tightness, this is where the builder can really succeed in failing or succeeding. When we look at how to achieve it, start looking at the penetrations, eliminate as many as you can, make sure your window connections are dialed in, then make sure your foundation to wall details are correct. And then wall to roof. And lastly, build a mock up. You'll be surprised of how affordable they are and you can move them from job to job. You can show different people at different stages, that you can show your clients so that everyone understands what is your plan. So happy air ceiling everybody. And I am done and looking forward to answering any questions that you may have.